To start with I have measured impedance and phase of 10 bass drivers tangband w3-1876 with the purpose to find 4 candidates for the MBF project. ... The question is if its a good driver for MFB and second is there a sensor that will fit and weigh only 2g or less?
Very interesting project idea. And what a coincidence! I was thinking of using this same driver in a little transmission line subwoofer.
I don't have this driver to inspect. It doesn't have a dust cap to remove to access the voice coil area. This is the best place to add an accelerometer.
This is a bit of a sidebar and may sound like blasphemy to MFB purists, but hear me out...
I think it was back in the very early 80s that Paul Barton (PSB Speakers) developed and sold the Beta II. This speaker used the 8" Philips MFB driver in a ported enclosure. He would have done this to increase LF output. A little driver like this will generate so little SPL at low frequencies it can use all the help it can get. How this would be combined with MFB control would be a very interesting but advanced project!
Very interesting project idea. And what a coincidence! I was thinking of using this same driver in a little transmission line subwoofer.
I don't have this driver to inspect. It doesn't have a dust cap to remove to access the voice coil area. This is the best place to add an accelerometer.
I'll say (coincidence)sqr! I use this driver in a MLTL and I'm very satisfied with it. Not only good transients but also deep bass. If I can reduce the 8 litre to 0.5 litre with the same SPL using two drivers, less THD, dynamicly balanced mass-acceleration etc then I will be very happy.
You are right about the dustcap. However the inverted cone is very hard and the joint to vc very solid. A holder with sensor will work very well if I compare to the Philips design which is my only experience sofar.
Analogy sidebar;
I am today changing to

I'll say (coincidence)sqr! I use this driver in a MLTL and I'm very satisfied with it...
(Coincidence)^3. I was thinking I might try a mass loaded design! I'll send you a PM on this to avoid straying more off topic...
It's the latter, especially with modern bass rich music the woofers cone excursion easily stretches available tinsel length. Remember these drivers were designed late 70ties, early eigthies with mainly analog sources in mind.
The beautiful Philips experience has opened my ears for new adventures 🙂.
I hope you can help me chose the right sensor for my MFB project in post #137. I have looked at the Piratelogic homepage and find ClingOn especially interesting. I plan to use a 3D-printed holder that integrate very well with the hard cone. It will be like an extension of the vc.
I assume we use the private message for how to order etc.
Br
The beautiful Philips experience has opened my ears for new adventures 🙂.
I hope you can help me chose the right sensor for my MFB project in post #137. I have looked at the Piratelogic homepage and find ClingOn especially interesting. I plan to use a 3D-printed holder that integrate very well with the hard cone. It will be like an extension of the vc.
I assume we use the private message for how to order etc.
Br
If you are designing an accelerometer mount of your own, ensure it has a low mass and high section modulus in the motion axis.
TadaaLooking at the w3-1876 driver I wonder if it allows the magnet to be dismounted from the basket using the screws indicated red

A sensor d 19mm fits inside voice coil. However risk for rumble from compressed air.
Attachments
Thats great newsTadaayes it will! The first time might cost the driver but next one will be quite simple.

A sensor d 19mm fits inside voice coil.
The obvious choice would be a StarBass 25 accelerometer modded to fit the 19mm VC:
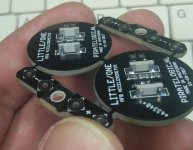
Assuming it gets tightly glued against the back of the cone that shouldn't be a problem as the Murata elements themselves are airtight.However risk for rumble from compressed air.
Last edited:
The obvious choice would be a StarBass 25 accelerometer modded to fit the 19mm VC:.
Let's get on with it! GIve me instructions..😀
By the way what is the roughly weight of a modded starbass 25?
Last edited:
A standard StarBass 25 is around 3 grams and expect a 19 mod to sit around 2. I'll send you more details later this week via mail.Let's get on with it! GIve me instructions..😀
By the way what is the roughly weight of a modded starbass 25?
chriscam
Have you looked at laser feedback? Or anyone else of course..
I built several systems with piezo tweeters as accellerometer and it worked fine But i also tried laser with quite good result, the resolution was too bad so the distortion reduction was only 10db but with this one i believe it could be better!
Smart laser triangulation displacement sensor
Have you looked at laser feedback? Or anyone else of course..
I built several systems with piezo tweeters as accellerometer and it worked fine But i also tried laser with quite good result, the resolution was too bad so the distortion reduction was only 10db but with this one i believe it could be better!
Smart laser triangulation displacement sensor
chriscam
Have you looked at laser feedback? Or anyone else of course..
I built several systems with piezo tweeters as accellerometer and it worked fine But i also tried laser with quite good result, the resolution was too bad so the distortion reduction was only 10db but with this one i believe it could be better!
Smart laser triangulation displacement sensor
Good so see you are making some progress, Nils!
With regard to laser sensors, we used a variant of these for height control on bevel plasma cutting systems. My guess is that nothing of this type would be fast, accurate or inexpensive enough for use as a loudspeaker voice coil position sensor.
Attachments
I use the laser on the photo for linear and un-linear parameter identification (TS and LS parameters) among other precision measurements.
Its good enough up to 700Hz with a resulotion of 1u in a controlled climate. However high quality measuring of a bending, wobbling or angular shifting of the cone demands more than one laser point.
It would be an ideal solution for a feedback as it does not interfere whith the object and the challenge I assume is how to get a robust signal.
Its good enough up to 700Hz with a resulotion of 1u in a controlled climate. However high quality measuring of a bending, wobbling or angular shifting of the cone demands more than one laser point.
It would be an ideal solution for a feedback as it does not interfere whith the object and the challenge I assume is how to get a robust signal.
Attachments
The Klippel measurement system at my workplace also uses laser. And i Guess that 4kHz sampling would be good enough for a subwoofer. 40 times oversampling @ 100Hz.
The resoultion in distance is a question.
"Measuring ranges (mm):
2 | 5 | 10 | 20 | 50 | 100 | 200 | 300
Linearity max. 0.4µm
Resolution max. 0.03µm"
Who will try?
The resoultion in distance is a question.
"Measuring ranges (mm):
2 | 5 | 10 | 20 | 50 | 100 | 200 | 300
Linearity max. 0.4µm
Resolution max. 0.03µm"
Who will try?
The Klippel measurement system at my workplace also uses laser. And i Guess that 4kHz sampling would be good enough for a subwoofer. 40 times oversampling @ 100Hz.
Who will try?
Is it optoNCDT 1420 Klippel are using today? The one I use is what Klippel used some years ago. Max sampling 1kHz but the rest the same for both in spec.
It's not always I manage to measure up to 1kHz because of noise. At cone diameter less than 170mm the pistonic movment is decreasing and gradually distorted by bending at the periferi. Depending on stiffnes of cone, elasticity/density ratio, internal damping etc influence also I assume.
To get a good result it's important that the laser triangulation is made perpendicular to the surface and to have a consistent surface reflection. Also the choice of location for the laser i find essential. There is not one spot on the cone that moves completely pistonic is my experience and manifest in noise.
To clarify previous, the cone breakup start at the vicinity of 1kHz for a 170 mm cone.
In addition to design and material inconsistencies, glue beads, tinsels, anisotrop properties, surround and cone partial resonance modes etc contribute to the challange to use the laser for good results.
In addition to design and material inconsistencies, glue beads, tinsels, anisotrop properties, surround and cone partial resonance modes etc contribute to the challange to use the laser for good results.
Since Lejonkungen showed (above) that you get dramatic benefits even the crude sensors Philips cobbled together, the sensor can't be much of a limiting factor. The familiar off-the-shelf accelerometers have astonishing accuracy and integrated amplification.
While feedback defines performance, even imperfect feedback with imperfect sensors is a whole lot better than the non-feedback subs used by everybody else on this forum.
The core problem is choosing or making or re-making a driver that is suitable for MFB. It may be that some of the physical parameters so cherished by non-MFB builders are of less importance when you have feedback (stability of materials, cone profile?).
And vice versa for the parameters mentioned above related to piston-like cones, reference-point for mounting the sensor (or sensors?), and maybe even power (and Xmax) handling (for very low frequency boosting watts).
B.
While feedback defines performance, even imperfect feedback with imperfect sensors is a whole lot better than the non-feedback subs used by everybody else on this forum.
The core problem is choosing or making or re-making a driver that is suitable for MFB. It may be that some of the physical parameters so cherished by non-MFB builders are of less importance when you have feedback (stability of materials, cone profile?).
And vice versa for the parameters mentioned above related to piston-like cones, reference-point for mounting the sensor (or sensors?), and maybe even power (and Xmax) handling (for very low frequency boosting watts).
B.
Last edited:
Laser is maybe one of the most remarkable inventions the last century. When invented few understood what to use it for. The first ones weight tons and needed kW and water cooling and today they fit into a led and we have them all over in homes, hospitals, space... and yet the development is ongoing.The Klippel measurement system at my workplace also uses laser. And i Guess that 4kHz sampling would be good enough for a subwoofer.
Laser mems for scanning already exist on a tiny chip, we might already be able to integrate the laser scanner in the voice coil? Use it in reverse so to say.🙄
Reverse so the laser spot is on the pole piece inside the coil... or vice versa to avoid the tinsels. 

- Home
- Loudspeakers
- Subwoofers
- Motional Feedback Speaker Project - Circa 1981