Nope, before I started building my own accelerometers Piet Gouw (former philips hifi sales & mkt team lead) provided me with a copy of their 1968 tech research doc outlining their choice for accelerometer based feedback over fixed position measurements. Had to do with difficulties, both technical & costwise, of obtaining a steady reference point with optical, capacitive and inductive based feedback systems.Have you looked at laser feedback?
Correct, visited Pirol Hifi in Köln - Germany last year where I witnessed the inner workings of a Backes & Muller system. Their magneto dynamic pickup is definitely a work of art with a corresponding price tag.My guess is that nothing of this type would be fast, accurate or inexpensive enough for use as a loudspeaker voice coil position sensor.
Agree, maybe one day we learn how to mod a cd laser to do just that but until then piezo remains the cheapest way to build loops. Lejonkungen, haven't got around writing you that mail yet as my soldering tool broke down & have been busy replaceing it with new weller toys 🙂It would be an ideal solution for a feedback as it does not interfere whith the object and the challenge I assume is how to get a robust signal.
Last edited:
...maybe one day we learn how to mod a cd laser to do just that but until then piezo remains the cheapest way to build loops....
Wheatstone Bridge, current feedback, or custom coils are excellent sensors and greatly simplify the system compared to accelerometers, home-brew or purchased. I can't recall seeing the methods tested for comparison.
BTW, the "optical" approach Philips long ago was considering was a bulb, photocell, and a little metal tapered mask moving with the cone. No way to make it work as well as off the shelf accelerometers or even the 10-cent piezo that Philips implemented.
Last edited:
Built one Saturday...Wheatstone Bridge, current feedback, or custom coils are excellent sensors and greatly simplify the system compared to accelerometers, home-brew or purchased. I can't recall seeing the methods tested for comparison.
BTW, the "optical" approach Philips long ago was considering was a bulb, photocell, and a little metal tapered mask moving with the cone. No way to make it work as well as off the shelf accelerometers or even the 10-cent piezo that Philips implemented.
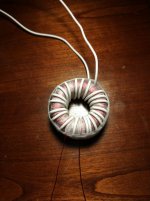
Built one Saturday...
What's that?
(In post #162, the "custom coil" referred to drivers with a extra high-turns coil added just to produce a feedback signal. Sony made a driver with such a coil discussed on this forum somewhere. Seems a good concept to me. I don't know of anyone succeeding in producing feedback using an ordinary DVC driver because the voltage generated is too low. I've tried too.)
B.
Feedback coil for Mr. Erath's circuit.
Justia Patents Loudspeaker FeedbackUS Patent for Feedback system for a sub-woofer loudspeaker Patent (Patent # 5,086,473
Patents Assigned to Louis W. Erath - Justia Patents Search
Same as used in this:View attachment 839764
Justia Patents Loudspeaker FeedbackUS Patent for Feedback system for a sub-woofer loudspeaker Patent (Patent # 5,086,473
Patents Assigned to Louis W. Erath - Justia Patents Search
Same as used in this:View attachment 839764
Last edited:
Feedback coil for Mr. Erath's circuit.
Given the mysteriousness and vintageness of the LWE speakers, as best as I can guess*, that coil is the leg of the Wheatstone Bridge meant to simulate (that is, to balance against) the driver.... a circuit well-known in audio circles at the time (mid-70's?) and that others (and me) had been experimenting with for some years (see JASA, Werner, 1954).
What Erath marketed what a little passive panel containing the bridge and some odds and ends and the speaker. The buyer had a choice of purchasing the LWE amp all connected or doing surgery on their own amp to connect the feedback signal. It would be perilous to try this on a modern high-feedback factor solid-state amp today.
By all accounts I've seen, the modest (and kind of tacky) LWE box greatly impressed reviewers. Which is true of nearly every account of MFB I've ever read, including this thread.
Erath was an audio amateur whose day-job was geophysical engineering. All adherents refer to him as a gesture of the highest esteem and genius as "Mr. Erath".
B.
*Sure would be nice if troystg could provide a schematic or link to the circuit.
Last edited:
I have several working units that I bought from him directly. Not the earlier LWE speakers with clip kits but purpose built stand alone units. In all actuality I probably have the last units he made before he passed excluding his Trout powered speakers.
Problem is the unit is a single stereo box and I am making 3 channel amps to sit next to the speakers.
So I am trying to copy the stereo unit into mono units. Off and on for 10 years now. I am finally in a position where I have time and resources to finish this project.
The amps have room in the enclosures to add Mr.Erath’s units when I finish them. All wiring in the amps, other than power and switch, is temporary and too long. Will be cleaned up once complete.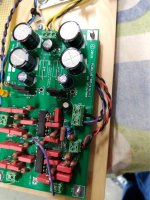
View attachment 1
View attachment 1
View attachment 1
Problem is the unit is a single stereo box and I am making 3 channel amps to sit next to the speakers.
So I am trying to copy the stereo unit into mono units. Off and on for 10 years now. I am finally in a position where I have time and resources to finish this project.
The amps have room in the enclosures to add Mr.Erath’s units when I finish them. All wiring in the amps, other than power and switch, is temporary and too long. Will be cleaned up once complete.
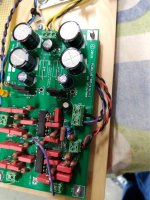
View attachment 1
View attachment 1
View attachment 1
Thanks for update. Good luck with your project.
Based on painful experience with the risks of feedback turning into howl back, use an amp with output lower than what your driver can handle without burning out and be cautious.
Got a problem when I selected your attachments, I get this ominous warning from the DIYaudio web server: "Invalid Attachment specified. If you followed a valid link, please notify the administrator"
B.
Based on painful experience with the risks of feedback turning into howl back, use an amp with output lower than what your driver can handle without burning out and be cautious.
Got a problem when I selected your attachments, I get this ominous warning from the DIYaudio web server: "Invalid Attachment specified. If you followed a valid link, please notify the administrator"
B.
...use an amp with output lower than what your driver can handle....
Or a fuse. 🙂
At the risk of seeming humourless or restating what is already obvious, I thought no ordinary fuse is big enough for normal service but will melt fast enough to protect a driver from a real big momentary pulse. (But many readers will be happy to learn if there is one.)
Last edited:
The line arrays were built by a close friend of Mr. Erath. 8 x Scan Speak Revelator mids and Fountek neo 2 ribbons. The woofers in the picture are 2 x 10" PartsExpress Reference Aluminum woofers but they are for one of his other servo units. His best servo uses a 15" woofer in a 1.25cu. ft. sealed enclosure. I hope to eventually have 2 x 15's on each side and then dynamics will never be a concern. Even though all new music is compressed to hell.
The line arrays were built by a close friend of Mr. Erath. 8 x Scan Speak Revelator mids and Fountek neo 2 ribbons. The woofers in the picture are 2 x 10" PartsExpress Reference Aluminum woofers but they are for one of his other servo units. His best servo uses a 15" woofer in a 1.25cu. ft. sealed enclosure.
Ummm, quite an accomplishment just getting a 15-inch driver into a 1.25cf box.
The servo function has nothing to do with the nice looking tall speakers, only the subs.
If you don't ever plan on providing information on the LWE MFB circuitry of 1970, there's no value in this thread with pretty pictures of boxes. You've popped up in various threads over the years with adulation for "Mr. Erath" but I have yet to learn anything of interest about the design from you.
... which is a pity since the Wheatstone Bridge is a good MFB DIY contender. Links?
B.
Last edited:
The purpose of this forum is not to educate you..
It is to share the love of building your OWN DIY gear.
You ask for help when needed and other good people help you out.
If you are looking for schematics and cloning then my work is not for you.
It is to share the love of building your OWN DIY gear.
You ask for help when needed and other good people help you out.
If you are looking for schematics and cloning then my work is not for you.
At the risk of seeming humourless or restating what is already obvious, I thought no ordinary fuse is big enough for normal service but will melt fast enough to protect a driver from a real big momentary pulse. (But many readers will be happy to learn if there is one.)
I use fast blo fuses. They open pretty quick. 1.5A rating on the old Philips MFB drivers. 2.0A rating on the larger MFB for ACI SV12 Drivers...
Thanks, hope you're right.I use fast blo fuses. They open pretty quick. 1.5A rating on the old Philips MFB drivers. 2.0A rating on the larger MFB for ACI SV12 Drivers...
But even without thinking about the bass boost that MFB introduces automatically and the muscular transient corrections from MFB, and recognizing the exaggerated notions of power demand common on this website, 10-20 watts seems low for a sustained organ pedal note.
A sudden pulse caused by feedback design goof takes place in audio time, not melting fuse-wire time. It's an old topic here and I recall it often ends with morose posters.
B.
Thanks, hope you're right.
But even without thinking about the bass boost that MFB introduces automatically and the muscular transient corrections from MFB, and recognizing the exaggerated notions of power demand common on this website, 10-20 watts seems low for a sustained organ pedal note.
A sudden pulse caused by feedback design goof takes place in audio time, not melting fuse-wire time. It's an old topic here and I recall it often ends with morose posters.
B.
Use smaller fuses during development. These blow before things get too exciting this eases stress tremendously. I think I started with 0.25A or so. Buy fuses in 10-packs... 🙂
Lejonkungen, haven't got around writing you that mail yet as my soldering tool broke down & have been busy replaceing it with new weller toys 🙂
Chris I'm stuck in the house ( as many others around the globe..) and have a hot soldering tool melting for action 😀
- Home
- Loudspeakers
- Subwoofers
- Motional Feedback Speaker Project - Circa 1981