Hi Remlab, the sony cabinet is done the right way. A constrain layer usually is a combination of a thin viscouselastic layer sandwich between 2 dissimilar thickness material.If the layer is thick then u won,t have good shearing between layer.
vibration causing flexing motion is damped by shearing force between the 2 different thickness material. Only problems is the adhesive efficiency is highly temperature dependent . Another problem is its expensive and not widely available.
I am waiting for some viscoelastic glue from China . It is actually very cheap so not sur if its good or not but no harm giving it a try.
To reiterate, the midbass sits on a 3.2mm panel of aluminum, followed a3.2mm sorbothane layer, followed by a 6.4mm panel of aluminum followed by a 3.2mm layer of sorbothane followed by another 6.4mm layer of aluminum. the key here is in the first three layers. as far as the thickness of the viscoelastic layers? I made sure they complied to the specifics of the patent..
"In the preferred embodiment, the layer of damping material has a thickness in the range of 3.2 mm to 6.4 mm. The first and second substrates are bonded to the layer of damping material using a two-part adhesive suitable for bonding PVC films to porous fiberboard. The first and second substrates each comprises a pair of panels of medium density fiberboard bonded together with a layer of adhesive. A gasket is sandwiched between a mounting frame of the transducer and the baffle board for providing an airtight seal between the transducer and the baffle board. An extensional damping material may be bonded to the first substrate on an interior side of the baffle board."
Last edited:
I do have to say though, that in retrospect, the thin layer of aluminum should have been the central layer, not the top one(That way, each thicker piece of aluminum would be adjacent to a thiner piece). If I could have only gone back and done it over. The top thin(3.2mm) piece also flexes a little while torquing down the four corner mounting bolts. The 6.4mm aluminum plate on top would not have done this. It would have applied a perfectly even pressure over the entire inner surface of the baffle's sorbothane layers.
Last edited:
Hi remlab, If the vicoelastic layer is thick it will act like a damper ( effectiveness depend on thickness) . it won't be like a CLD. The sandwich board then will act like a mass damper (MLV) . However Mass damper is most effective if its very dense or have a low resonce frequency to begin with. If this is what u intend to do . Isolate the driver with rubber bushing on baffle panel. Its way more effective. Usually the most efficient way to isolated vibration is nearest to source. Its like a cage of chickens. Catching them at the entrance is easier then catching then once they are 10 feet out of the cage.
The idea of mounting directly onto an aluminium panel ( wood is inherently better damped than aluminium ) is not good but in your case the sorbthane help offset the negative.
I am not trying to belittle your effort, going out of the way to try something new is very good as a learning experience.
The idea of mounting directly onto an aluminium panel ( wood is inherently better damped than aluminium ) is not good but in your case the sorbthane help offset the negative.
I am not trying to belittle your effort, going out of the way to try something new is very good as a learning experience.
I need you to post some studies to back up your opinion, and they don’t even need to be peer reviewed.🙂
Just go and google CLD or constrained damping, extensional damping , mass loaded vinyl or MLV, viscouselastic properties related to temperature and effective damping frequencies of the aboves. There is a good handbook online on sound proofing but I cannot recall the site. Sorry. In fact if you have the time check out how they soundproof planes and helicopter to give you a general idea of huge sound and vibration problem and solutions.
BnW is very good at this look at their top end speakers.You can't go wrong following their ideas. Millions hv been invested in RnD
BnW is very good at this look at their top end speakers.You can't go wrong following their ideas. Millions hv been invested in RnD
if you hv the means to fabricate , getting rid of all flat surface panel will be a great start. Curved surfaces is much stiffer. Use some butyl rubber to totally lined the interior to damp the vibrations. As thick as possible is the word. Paste onto the butyl a thin layer of MLV or whatever that is heavy. DECOUPLE with a 1 inch or more layer of foam or fibres before adding another layer of MLV. This next layer of MLV must be DECOUPLED from the cabinet by the foam and almost totally cover the interior . The side joining MLV and cabinet can be a soft pcs of butyl rubber. You got a damped cabinet. Next problem how to decouple the speaker from the cabinet... Rubber bushing behind speaker holding bolts or decoupled damped baffle panel from cabinet by isolated bolting and vicoselastic joins.
You can check out how high end car like lexus, merc chassis and suspension for ideas.Many hv 2 layers of isolation using rubber bushing and some even hv fluid damped rubber to work effectively at lower frequencies.
CLD without proper testing is not very effective. Its very temperature , material and thickness dependent. Sorbathane. I found out the hard way when soundproofing my car. Its very effective but that makes the low frequency whcih cannot be damped properly very dominant. Our hearing is very sensitive to narrow band noise vs wide which we tend to refer to background noise and is neutral. It is for this reason a lot of aluminium, titanium or mg speakers get bad reviews. All of them hv a pronounce resonace peak that need to be addressed effectively. A speaker box made of lead or tin will ideal so is a teardrop shape enclosure.
You can check out how high end car like lexus, merc chassis and suspension for ideas.Many hv 2 layers of isolation using rubber bushing and some even hv fluid damped rubber to work effectively at lower frequencies.
CLD without proper testing is not very effective. Its very temperature , material and thickness dependent. Sorbathane. I found out the hard way when soundproofing my car. Its very effective but that makes the low frequency whcih cannot be damped properly very dominant. Our hearing is very sensitive to narrow band noise vs wide which we tend to refer to background noise and is neutral. It is for this reason a lot of aluminium, titanium or mg speakers get bad reviews. All of them hv a pronounce resonace peak that need to be addressed effectively. A speaker box made of lead or tin will ideal so is a teardrop shape enclosure.
An old way to test for high grade alloy was to tap it and see ( well, hear ) if it rings, low grade ( and I presume pure " soft " ) alloy should be dead, not as dead as a porous casting though. The only way I can see on improving the "Remlab " baffle is to use steel, soft iron, or lead - but the extreme difficulties in machining and cutting them effectively rule them out. I wish I could hear them.
Bargain priced is aluminum self-adhesive pipe of duct wrap insulation. Comes various widths up to 8 inches. About an eight-inch thick gooey layer and heavy aluminum foil. Wonderfully effective making dishwashers quiet. Not sure it differs much in any important way from costly acoustic materials.
Canadian stores are full of re-purposable insulation stuff like that.
Not sure if this has the sticky stuff, but looks like this:
https://www.homedepot.ca/product/reflectix-duct-wrap-12-x25-/1000167782
Canadian stores are full of re-purposable insulation stuff like that.
Not sure if this has the sticky stuff, but looks like this:
https://www.homedepot.ca/product/reflectix-duct-wrap-12-x25-/1000167782
Last edited:
This one seems interesting🙂
https://www.ijert.org/research/damp...-layer-damping-treatments-IJERTV7IS070111.pdf
https://www.ijert.org/research/damp...-layer-damping-treatments-IJERTV7IS070111.pdf
Question:
Odd to my ears to hear people talk about resilient mounting of drivers. The cone of a driver is designed to move according to the signal relative to the driver frame. But when the frame is also moving relative to the cab, floor, and listener due to being resiliently mounted, doesn't that change the sound that reaches the listener?
So, is soft mounting a really bad notion?
B.
Odd to my ears to hear people talk about resilient mounting of drivers. The cone of a driver is designed to move according to the signal relative to the driver frame. But when the frame is also moving relative to the cab, floor, and listener due to being resiliently mounted, doesn't that change the sound that reaches the listener?
So, is soft mounting a really bad notion?
B.
It's a case of decoupling rather than coupling. Coupling is fine so long as everything the chassis is attached to is immobile.
Wikipedia explains the concept of constrained layer damping in a very simple way. There seems to be only one hard and fast rule...
"Typically a viscoelastic or other damping material, is sandwiched between two sheets of stiff materials that lack sufficient damping by themselves. The ending result is, any vibration made on either side of the constraining materials (the two stiffer materials on the sides) are trapped and evidently dissipated in the viscoelastic or middle layer."
In light of this fact, unverified esoteric claims are useless at best(Trolling at worst). Posting actual facts to back up those claims? That is very useful and highly encouraged.
"Typically a viscoelastic or other damping material, is sandwiched between two sheets of stiff materials that lack sufficient damping by themselves. The ending result is, any vibration made on either side of the constraining materials (the two stiffer materials on the sides) are trapped and evidently dissipated in the viscoelastic or middle layer."
In light of this fact, unverified esoteric claims are useless at best(Trolling at worst). Posting actual facts to back up those claims? That is very useful and highly encouraged.
Last edited:
This is an interesting video related to constrained layer damping. The music playing demonstration at the end is silly for obvious reasons.
Constrained layer damping | Audio Science Review (ASR) Forum
Constrained layer damping | Audio Science Review (ASR) Forum
It's a case of decoupling rather than coupling. Coupling is fine so long as everything the chassis is attached to is immobile.
Seems to me, the cab face panel - even if there is some microscopic vibration present - is less mobile relative to my chair than a driver chassis resiliently fixed to the face panel and the vibration motion of the driver chassis is additional to whatever the panel is doing.
Doesn't securely securing the cab to the floor* and the driver to the cab makes sense?
B.
*Now the Klipschorn bass is not exactly anorexic, but I sat a large foundation cinderblock on top (later, a wine rack, looked better I suppose).
If the floor is solid/immobile then coupling all the way makes sense, if it's not, wouldn't decoupling at the first opportunity be best?
here's a couple of tracks by Steve Clarke which may be fun for you. He has an album called "Solo Drums" with two cuts - each around 18 minutes
Steve Clarke - Applying Rudiments to Improvisation [Opening Solo] - YouTube
this tribute to "Lemmy" sounds pretty good on my cheap but cheerful One Odio headphones
Lemmy Tribute by Steve Clarke 2016 - YouTube
That was crazy!! I was mesmerized the entire time and I kept turning it up louder and louder. That was probably the loudest I've ever played my system. The speakers kept their composure the entire time. That's the thing I'm noticing most about this speaker with the new baffle(And high density felt), is that it sounds very different from other speakers I've heard when played loud. Utter transparency even at the highest levels. Weird experience. Very counterintuitive. The tweeter being mechanically isolated from the mid-woofer and the baffle being mechanically isolated from the cabinet(And itself) probably has a lot to do with what's going on. Obviously the quality of the drivers have something to do with it too, but I've heard them before and they never sounded like this. I'm also pretty sure that the high density felt is killing much of the internal acoustic noise too, so that's not reflecting back and messing up the mids
Last edited:
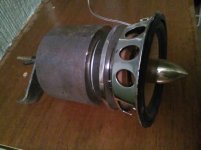
(Question:
Odd to my ears to hear people talk about resilient mounting of drivers. The cone of a driver is designed to move according to the signal relative to the driver frame. But when the frame is also moving relative to the cab, floor, and listener due to being resiliently mounted, doesn't that change the sound that reaches the listener?
So, is soft mounting a really bad notion?
B.
Ideally the magnet should be bolted to a weight ( a lump of cast iron in the above image ) and then the whole assembly suspended by tension springs, with something like a foam ring betwixt driver and enclosure. I think if the chassis were to be bolted to a very ridged and heavy front baffle it ( the chassis ) would act like a spring between the magnet and baffle causing a resonance; I did notice a resonance on a pressed steel chassis that was audibly reduced by adding red babybel cheese wax to the gap between magnet and suspension.
- Home
- Loudspeakers
- Multi-Way
- Midrange experiment with Auto sound panel deadener and high density acoustic felt..