Does this work better than simply having soft clipping at some chosen voltage level?The Kii speaker has a clever protection scheme. An analog circuit ahead of the DSP looks at the signal, and if illegal demands are made, DSP-slopes are adjusted. .
B.
Well, it is a small closed box with 4 relatively large woofers, so it will need a bass boost a la Linkwitz to get as low as it does. My educated guess that it is the slope of this bass reinforcement that gets tuned down. So it is not soft clipping but gain reduction.
I have heard it play really loud in two different large rooms ( > 60 persons) without ever noticing anything like protection kicking in.
I have heard it play really loud in two different large rooms ( > 60 persons) without ever noticing anything like protection kicking in.
One of the things I took away from my few years of working at an audio electronics company, was the realization that "really loud" means very different things to different people.I have heard it play really loud
I remember a fellow from marketing plunking away at a prototype electronic keyboard which had studio monitor speakers built in, literally wincing in pain at the ear-shattering volume, and then telling the engineers to go away and make the keyboard even louder.
I remember visitors to a NAMM show subwoofer exhibit, who described a subwoofer in terms of whether or not it could shake the sofa they sat on to audition it. If they could feel the sofa shake, then it was a good subwoofer, otherwise, it wasn't. 😱
I'm guessing that subwoofer protection is designed mainly to cope with these kinds of customers.
-Gnobuddy
My concrete horn under the floor does not play loud at all, but it feels by a body. Loud subwoofer means dirty sound.
Well, your subwoofer is (a) made of concrete, (b) a horn, (c) under the floor, and (d) you are an engineer, and you know exactly what you're doing. 🙂
Put all those together, and I have a feeling that the SPL and frequency capability of your subterranean concrete horn subwoofer is a little more extreme than most! 😀
-Gnobuddy
Put all those together, and I have a feeling that the SPL and frequency capability of your subterranean concrete horn subwoofer is a little more extreme than most! 😀
-Gnobuddy
Well, your subwoofer is (a) made of concrete, (b) a horn, (c) under the floor, and (d) you are an engineer, and you know exactly what you're doing. 🙂
Put all those together, and I have a feeling that the SPL and frequency capability of your subterranean concrete horn subwoofer is a little more extreme than most! 😀
Believe me, SPL is not high; it is adequate to about 75 dB of an overall sound level when we are watching movies. We have no earthquake insurance, but it anyway would not help. 😀
A big thanks to Steph_tsf for encouraging me to learn some LTSpice and for his many helpful suggestions for this project.
Now that I have some hands on experience, I can more fully appreciate the many tips and admonitions of previous posts by Steph_tsf, Gnobuddy and bolserst - thank you.
Per Bolserst suggestion: The 5.6k Ohm SMD resistor (+6dB bass boost @ 40 Hz) has been removed (quite skillfully I might add🙂)
Scope snapshots taken 20, 30, 35, 40, 60 and 90 Hz. Plugged port, without 5.6k Ohm bass boost resistor.
Blue Trace - piezo direct into oscilloscope
Yellow Trace - reading across MFB resistor.
Similar readings taken running piezo output through my buffer + integrator noisy circuit (data not shown).
Concerns:
1. Phase shift seems to go through 180 over short interval in frequency relative to MFB output. Running piezo signal through circuit just seems to shift everything but still goes through seemingly at least a 180 phase swing from 20-60 Hz. I guess I could say - "Gnobuddy" warned me.
2. Piezo output from 20-28 Hz pretty low, although I think this easily fixed by adding a bit of weight similar to what I had a couple weeks ago in my first rendition, or changing mounting mechanics.
As Steph_tsf suggested in earlier post, one may be able to modulate the piezo response mechanically by adding a bit of weight or even a drop or two of glue.
Note the changes in amplitude of piezo vs MFB as function of frequency.
Conclusion thus far:
If I only played say 40-45 Hz tune, I think I could just pop in the piezo and bypass the MFB resistor using existing Sony circuit - Ha.
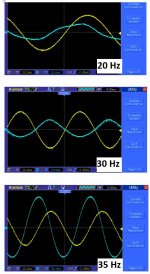
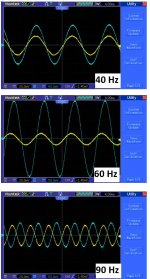
Now that I have some hands on experience, I can more fully appreciate the many tips and admonitions of previous posts by Steph_tsf, Gnobuddy and bolserst - thank you.
I agree, you should be able to work a piezo into the Sony circuit with a few changes to the compensation scheme. Of course when it comes to producing a stable feedback network around a mechanical device...the devil is in the details.
4) Had you looked at removing the 40Hz boost of +6dB and extending the LF response of the Sony pre-amp as mentioned in second paragraph of Post#432 ?
Per Bolserst suggestion: The 5.6k Ohm SMD resistor (+6dB bass boost @ 40 Hz) has been removed (quite skillfully I might add🙂)
Scope snapshots taken 20, 30, 35, 40, 60 and 90 Hz. Plugged port, without 5.6k Ohm bass boost resistor.
Blue Trace - piezo direct into oscilloscope
Yellow Trace - reading across MFB resistor.
Similar readings taken running piezo output through my buffer + integrator noisy circuit (data not shown).
Concerns:
1. Phase shift seems to go through 180 over short interval in frequency relative to MFB output. Running piezo signal through circuit just seems to shift everything but still goes through seemingly at least a 180 phase swing from 20-60 Hz. I guess I could say - "Gnobuddy" warned me.
2. Piezo output from 20-28 Hz pretty low, although I think this easily fixed by adding a bit of weight similar to what I had a couple weeks ago in my first rendition, or changing mounting mechanics.
As Steph_tsf suggested in earlier post, one may be able to modulate the piezo response mechanically by adding a bit of weight or even a drop or two of glue.
Note the changes in amplitude of piezo vs MFB as function of frequency.
Conclusion thus far:
If I only played say 40-45 Hz tune, I think I could just pop in the piezo and bypass the MFB resistor using existing Sony circuit - Ha.
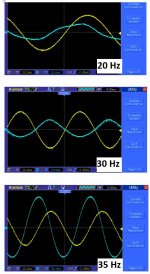
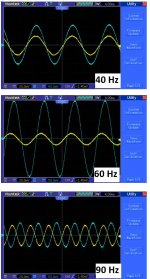
Now that I have some hands on experience, I can more fully appreciate the many tips and admonitions of previous posts by Steph_tsf, Gnobuddy and bolserst - thank you.
You obviously are not ready to understand my advices,
1. Don't forget about a rumble filter,
2. Consider a positive feedback by current as an alternative,
3. Consider a microphone inside as a pressure sensor.
You are welcome!
I am wondering if someone would be kind enough to explain why I am seeing the phase shift of the piezo output vs. the MFB output as a function of frequency, particularly in the range of about 25-45 Hz - woofer in box with plugged port or woofer out of box - still seems like at least a 180 phase shift - I do not understand. I would think only the amplitude would vary...is the MFB resistor output not really measuring woofer movement? Is the MFB resistor just acting like a voltage divider and sending a small part of the output signal back to the pre amp mixer?
I understand that the woofer has a natural roll off, but I do not understand the phase shift of the piezo vs MFB outputs. Any thoughts / insight appreciated.
I understand that the woofer has a natural roll off, but I do not understand the phase shift of the piezo vs MFB outputs. Any thoughts / insight appreciated.
In April 2010, I started a http://www.diyaudio.com/forums/solid-state/166061-philips-motional-feedback-mfb-4.html subject on diyAudio. You may find a couple of answers over there. Have a look to the LTspice simulations starting from post #33.I understand that the woofer has a natural roll off, but I do not understand the phase shift of the piezo vs MFB outputs. Any thoughts / insight appreciated.
1) Are you sure about the phase of your piezo signal? What if you reverse its polarity?
2) Please describe the preamplifier that's loading your piezo disc.
3) In case you exploit the piezo disc voltage, does this happen through a high impedance context (several meg ohm) for preserving the very low frequencies?
4) Are you aware that the Sony MFB signal elaborated by the Voight bridge, is supposed to be cone velocity, while the Philips MFB signal elaborated by the piezo disc is supposed to be cone acceleration?
5) For comparing apples with apples, do you know how to convert an acceleration signal into a speed signal? Are you aware of the practical limitations imposed on real-world time integrators?
6) In case the Sony Voight Bridge is incorrectly DC balanced, having its "voltage branch" not perfectly compensating its "current branch", the Sony Voight bridge output will incorrectly reflect the cone speed below 50 Hz. Can we say that the Sony Voight Bridge is correctly DC balanced?
Avoid comparing rotten pears (some incorrectly DC balanced Voight bridge) with good apples (some piezo disc loaded by a very high impedance, properly time-integrated with a low frequency accuracy range extending down 3 Hz or so - well beyond the audio frequency band).
Remember that inside the Sony SA-W2500, the MFB effect is very light, in the order of 3 dB, not significantly changing the frequency response curve and distortion.
Say I hook the piezo disc on a capacimeter able to measure 10 pF to 10 nF. Will the capacimeter display the piezo disc capacitance?
Or will the capacimeter (that's actually injecting some AC current into the piezo disc) get fooled by the piezo-electric effect, generating a voltage that's proportional to the piezo disc deformation?
What if the measuring AC current is 100 kHz or so, a high frequency where the inertia forces tend preventing the piezo disc to contract or expand?
I'm asking the question because I don't know the capacitance of the piezo disc.
Look to the sizes of the various piezo sensors that went exploited as acceleration sensors.
The one that's shown in the Velodyne patent, buried into the coil former thickness, is less than 1 mm. I guess this is a small capacitance, say 100 pF or so.
The one that's inside the Philips RH541, RH544, RH545, RH567 etc. is approx 3 mm. I guess this is a medium capacitance, say 300 pF or so.
The one that's inside the Philips F9638 is approx 15 mm. I guess this is a quite big capacitance of 1500 pF or so.
Now look the sensitivities. It depends the weight (the mass) that you put on the piezo sensor. In case you put no extra-mass, it is the mass of the piezo sensor that will act as sole and only inertia forces generator. Add some mass on the piezo sensor, and there will be more inertia forces being applied on the piezo sensor, increasing the sensitivity. The piezo sensor develops some output voltage proportional to the inertia forces applied to it. Unfortunately, all piezo sensor exhibit some flexibility, determining a mechanical resonant system, exhibiting some resonance frequency. Such feature gets exploited by the 3-terminal piezo discs to be used as oscillators (beepers). They oscillate at their natural mechanical resonant frequency.
In a MFB application, the best you can do, is to design the piezo system and environment, so it exhibits a natural mechanical resonance frequency, an order of magnitude higher than the frequency you want the MFB effect to fade in the loudspeaker. In our closed loop cases, we can see that the MFB effect nearly vanishes past 1 kHz. It is thus recommended to design the piezo sensor mechanical resonance, so it sits well above 3 kHz. Fortunately, a 15 mm diameter piezo disc exhibits a resonant frequency well above 3 kHz. You can taste this, by listening to the sound the piezo disc is making, when you let it fall on a metallic surface (use a mike and a spectrum analyzer). One can try covering the piezo disc by Pattex glue, or by epoxy glue, that may act as damper (lowering the Q factor), and as extra mass (decreasing the resonance frequency, and increasing the sensitivity).
Now look the Philips F9368 MFB speaker in post #13 on http://www.diyaudio.com/forums/solid-state/166061-philips-motional-feedback-mfb-2.html. This is their latest MFB generation. They relied on a approx 15 mm piezo disc. At first glance, it looks like a naive implementation. Look again the piezo disc used as acceleration sensor. Could it be that being so big, deployed this way, it exploits the ambient air as Q damper? And the two wires, so distant from the center, do they act as extra-mass, forcing the piezo disc to bend when subjected to their inertia forces?
Compare this with the previous Philips implementation relying on a miniaturized piezo element 3 mm x 3 mm square shaped, inserted into a silicon rubber carrier forming a mechanical lowpass filter. See post #12 on http://www.diyaudio.com/forums/solid-state/166061-philips-motional-feedback-mfb-2.html. This is what you have inside the Philips RH541, RH544, RH545, RH567, etc speakers. The solder drop on top of the piezo element seems to act as extra-mass, for increasing the sensitivity. As soon as there is some mechanical play developing between the piezo element and the silicon rubber carrier, you should consider the MFB pickup as kaput. Due to temperature variations (speakers having played loud), time (40 years) and wear (silicon rubber progressively hardening and shrinking), one can expect that many MFB speakers, currently suffer from mechanical play inside their MFB pickup assembly. A way to detect this, is to measure the frequency response curve and distortion curve at low listening levels, where the mechanical play has the same order of magnitude, as the cone travel.
In April 2010, I started a http://www.diyaudio.com/forums/solid-state/166061-philips-motional-feedback-mfb-4.html subject on diyAudio. You may find a couple of answers over there. Have a look to the LTspice simulations starting from post #33.
Thank you for all the details and questions helping me to understand. Some responses below:
1) Are you sure about the phase of your piezo signal? What if you reverse its polarity?
If I switch the phase it just shifts the frequencies at which the piezo and MFB are in phase and 180 out of phase. Important to note that above about 90 Hz, piezo and MFB output are in good phase agreement up to about 200Hz - beyond signal is weak.
2) Please describe the preamplifier that's loading your piezo disc.
No preamp is used - piezo is going directly into oscilloscope. MFB resistor also going straight into oscilloscope.
3) In case you exploit the piezo disc voltage, does this happen through a high impedance context (several meg ohm) for preserving the very low frequencies?
I think so...I think the input impedance of the oscilloscope is 20M ?; also, I do get a nice sine wave output from the piezo down to about 25 Hz.
4) Are you aware that the Sony MFB signal elaborated by the Voight bridge, is supposed to be cone velocity, while the Philips MFB signal elaborated by the piezo disc is supposed to be cone acceleration?
I read that, but do not know if I fully understand it at this point.
5) For comparing apples with apples, do you know how to convert an acceleration signal into a speed signal? Are you aware of the practical limitations imposed on real-world time integrators?
I would integrate the acceleration to get velocity; one could solve the integral using the initial cone velocity for the constant of integration.
6) In case the Sony Voight Bridge is incorrectly DC balanced, having its "voltage branch" not perfectly compensating its "current branch", the Sony Voight bridge output will incorrectly reflect the cone speed below 50 Hz. Can we say that the Sony Voight Bridge is correctly DC balanced?
Maybe this is why I am seeing the 180 phase shift down in this frequency - from about 28-44Hz piezo output seems to invert relative to MFB
Say I hook the piezo disc on a capacimeter able to measure 10 pF to 10 nF. Will the capacimeter display the piezo disc capacitance?
Or will the capacimeter (that's actually injecting some AC current into the piezo disc) get fooled by the piezo-electric effect, generating a voltage that's proportional to the piezo disc deformation?
...
I'm asking the question because I don't know the capacitance of the piezo disc.
Just measured capacitance of piezo disc - looks like about 18nF and as you predicted, voltage across piezo during measuring capacitance produced about a 3800Hz sound. Piezo (dimension of ceramic coating) about 15mm diameter.
This is their latest MFB generation. They relied on a approx 15 mm piezo disc. At first glance, it looks like a naive implementation. Look again the piezo disc used as acceleration sensor. Could it be that being so big, deployed this way, it exploits the ambient air as Q damper? And the two wires, so distant from the center, do they act as extra-mass, forcing the piezo disc to bend when subjected to their inertia forces?
Very good points and this is what I am noticing too - I think one could get a broad range of response / behavior just based on mounting of the piezo and wires and potentially could parlay the mechanical mounting to move the phase shift up or down. I would like to know if the feedback from the MFB resistor or piezo is an accurate indication of the motion of the cone vs input signal.
Thank you for the ideas!
Look to the sizes of the various piezo sensors that went exploited as acceleration sensors.
The one that's shown in the Velodyne patent, buried into the coil former thickness, is less than 1 mm. I guess this is a small capacitance, say 100 pF or so.
The one that's inside the Philips RH541, RH544, RH545, RH567 etc. is approx 3 mm. I guess this is a medium capacitance, say 300 pF or so.
The one that's inside the Philips F9638 is approx 15 mm. I guess this is a quite big capacitance of 1500 pF or so.
I must compliment you on your guesses - your estimate of the 15 mm piezo was in excellent agreement with what I just measured (18 nF) - impressive!
The Voight bridge is made of two branches : 1) the "voltage" branch that's connecting to the power amplifier output, and 2) the "current" branch that's connecting to the shunt resistor. The cone speed signal gets elaborated by the difference amplifier, subtracting the "current" signal from the "voltage" signal. Let me insist : the only valid signal to be analyzed is the Voight bridge difference amplifier output, supposed to reflect the instantaneous cone speed. Call it the VoightSpeed signal.I just did a quick measurement of the output from across the MFB resistor as a function of frequency over narrow range with the woofer in OEM box but with R125 bass boost resistor removed and port plugged. Does this make any sense?
Analyzing the "current" signal alone makes no sense in such context. By the way it is plain normal that the "current" signal exhibits a dip at a certain frequency that's the closed box + speaker resonance. In the context of a flat frequency response curve, a speaker mounted in a closed box requires less current at the resonance frequency.
As you wrote, let's go back to the roots. Grab a + 12 volt and - 12 volt power supply. Hook a high impedance buffer on the piezo sensor (first half of a TL072 opamp), and hook an integrator (second half of a TL072 opamp) for converting such "acceleration" signal into a "speed" signal. Call it the PiezoSpeed signal. Try listening to the PiezoSpeed signal for determining if it gets corrupt by hum or semiconductor noise.
You can compare such PiezoSpeed signal with the VoigthSpeed signal. Both should be identical. This is only true, in case the Sony Voight bridge got nicely balanced by Sony. You may determine this by sending a 30 Hz signal into the Sony subwoofer, leaving the cone free for a while, then trying to immobilize it with your fingers for a while. In case the Sony Voight bridge got nicely balanced, the VoigthSpeed signal should significantly decrease as soon as the cone gets blocked by your fingers, the same way the PiezoSpeed signal decreases.
Once you succeed realizing this, MFB speakers won't have secrets for you.
The more you extend the deep bass response, the more you need an instantaneous cone displacement prediction circuit, governing a variable frequency 2nd-order highpass filter. Such instantaneous cone displacement prediction circuit is a time integrator hooked on the PiezoSpeed signal.
As you wrote, let's go back to the roots. Grab a + 12 volt and - 12 volt power supply. Hook a high impedance buffer on the piezo sensor (first half of a TL072 opamp), and hook an integrator (second half of a TL072 opamp) for converting such "acceleration" signal into a "speed" signal. Call it the PiezoSpeed signal. Try listening to the PiezoSpeed signal for determining if it gets corrupt by hum or semiconductor noise.
You can compare such PiezoSpeed signal with the VoigthSpeed signal. Both should be identical.
I think this is what I tried back in this post http://www.diyaudio.com/forums/subw...ack-woofer-available-sort-54.html#post4899688
The problem was the phase shift of piezo vs MFB resistor as a function of frequency- my goal was, and I still think it possible, to substitute the piezo output for the MFB resistor output using the in situ Sony MFB circuit (maybe with some slight modification) to extend bass to ~ 20Hz. I think it should be possible and that is just based on my naive intuition and seeming similarities in Sony and other piezo based servo circuits.
Thank you for your valuable input!
Hi everyone
Just a short comment to hombre: In one of your photoes it seems as if you're using a piezodisc from a computer beeper (the piezo attached to a circular piece of thin metal). I tried that approach some time ago and found that it does not work - and that may account for some to the unwanted "artefacts" that your oscillogram showed. What you need is a piezo crystal whose front and back sides are the same! I found some in cheap piezo treble loudspeakers. They were glued to a paper cone and were quite easy to cut free of the cone.
You might also be interested in my old article from Speaker Builder. Andre Cuffioli (of audiodesignguide.com has nicked it, scanned it and put it on his webpage
( Andrea Ciuffoli - Documentation page - the item called: An Acceleration Feedback System from Speaker Builder page 1 page 2 page 3 page 4 page 5 page 6 page 7 page 8 page 9).
Good luck with your research!
Just a short comment to hombre: In one of your photoes it seems as if you're using a piezodisc from a computer beeper (the piezo attached to a circular piece of thin metal). I tried that approach some time ago and found that it does not work - and that may account for some to the unwanted "artefacts" that your oscillogram showed. What you need is a piezo crystal whose front and back sides are the same! I found some in cheap piezo treble loudspeakers. They were glued to a paper cone and were quite easy to cut free of the cone.
You might also be interested in my old article from Speaker Builder. Andre Cuffioli (of audiodesignguide.com has nicked it, scanned it and put it on his webpage
( Andrea Ciuffoli - Documentation page - the item called: An Acceleration Feedback System from Speaker Builder page 1 page 2 page 3 page 4 page 5 page 6 page 7 page 8 page 9).
Good luck with your research!
Keep in mind that the piezo output is proportional to cone acceleration. The coil current is (crudely) proportional to cone velocity....I do not understand the phase shift of the piezo vs MFB outputs. Any thoughts / insight appreciated.
Velocity and acceleration are two fundamentally different things. They cannot possibly match over any significant range of frequency - they inherently have quite different phase and frequency responses.
I am pressed for time and can't go into any more detail here. But the only way I know of, to deeply understand this stuff, is to learn complex number arithmetic, and how to describe transfer functions in terms of complex number polynomials. Without that, all we've got is words, and words don't do very well at accurately describing complicated technical concepts.
-Gnobuddy
During some time, french manufacturer Cabasse made servoed loudspeakers with a combinaison of feedbacks from a velocity bridge and from a piezo acceleration sensor.Velocity and acceleration are two fundamentally different things. They cannot possibly match over any significant range of frequency - they inherently have quite different phase and frequency responses.
Last edited:
Hi everyone
What you need is a piezo crystal whose front and back sides are the same!
Thanks for your suggestions and also the link to your interesting article, Hans.
I originally thought about affixing two piezo discs together so I would have a +, ground, and - output but found the simple piezo disc when mounted in bending mode worked quite well and put out what I thought were very nice sine waves as a function of frequency in the domain I was interested in 25-200 Hz. I initially tried much more expensive piezos in compression mode but was not impressed with their weight and output, so back to the el cheapos.
Right now, I do not think my obstacle is the piezo but rather the noise from my crude breadboard circuit with difference/buffer op amp and integrator / low pass filter.
The big problem I have is reconciling the phase shift of piezo vs MFB resistor outputs.
Thanks for your thoughts!
- Home
- Loudspeakers
- Subwoofers
- Commercial motional feedback woofer available sort of