But a DD motor that rotates at 33 1/3 revolutions does not generate as much vibration as a 2500 RPM motor in a belt system, that is the eternal discussion, the belt together with a high mass of the plate, absorbs that vibration in its entirety ? Exceeds DD?
The 1st law of thermodynamics is the conservation of energy, whereas energy in a system remains constant, or to simplify energy can neither be created or destroyed.
So energy can not be absorbed, it can only be transformed.
In a belt drive system the belt will vibrate as a function of its unrestrained length in addition to the vibration of the motor, the platter must be capable of damping this vibration energy. Vibration energy increases by the square of the rotational speed so a belt drive motor spinning at 330rpm will have 100 times more vibration to deal with than a DD motor spinning at 33rpm.
Early Neumann used the Lyrec motor later versions used the Technics SP02, and ALL cutting lathes are Direct Drive.
The spindle on the Neumman is 16mm OD and runs in a sleeve bearing, the motor is mounted very low down in the base of the lathe.
The spindle on the Neumman is 16mm OD and runs in a sleeve bearing, the motor is mounted very low down in the base of the lathe.
But a DD motor that rotates at 33 1/3 revolutions does not generate as much vibration as a 2500 RPM motor in a belt system, that is the eternal discussion, the belt together with a high mass of the plate, absorbs that vibration in its entirety ? Exceeds DD?
HI,
My brushless motor runs at 360 Rpm and has good torque to drive an over 5 Kg platter.
Rgds
Adelmo
dreamth's point is true: we can not improve upon whatever is already etched within the grooves by the lathes. That said, the turntable bearing can be additive to the baseline noise created by the lathe. So, one of the turntable's design goal must be to minimize the additive noise caused by the bearing, motor, vibration, etc.
The spindle on the Neumman is 16mm OD and runs in a sleeve bearing, the motor is mounted very low down in the base of the lathe.
The Lyrec is mounted in a cradle that sits on the floor.
the guy on lathe troll site sais its vms 70 is a regular bearing, whatever "regular" might mean...Do you have any photo or evidence of it being a sleeve bearing?A heavy platter also needs some sort of thrust bearing for support...The spindle on the Neumman is 16mm OD and runs in a sleeve bearing, the motor is mounted very low down in the base of the lathe.
Early Neumann used the Lyrec motor later versions used the Technics SP02, and ALL cutting lathes are Direct Drive.
The Scully motor uses a complicated belt drive system.

Two Scully lathes are used in Bernie Grundman's mastering studio but he eliminated the belt drive systems and replaced them each with an entire Technics SP-10Mk3 direct drive turntable which includes the SP-02 motor. So every record you own that was mastered at his place is the sound of the SP-10Mk3.
Also a video at 4:46 mark of Bernie explaining the reconfiguration. Previous motor was a Lyrec motor.

Last edited:
The Lyrec is mounted in a cradle that sits on the floor.
Here's an example of a Lyrec direct drive motor underneath a Scully lathe.

Cannot be. Glass is the worst material in the universe for sound. With the exception of rega-glass 🙂
Aren't this toys using a glass platter too?
Nakamichi Dragon-CT turntable demo - YouTube
Nakamichi TX-1000.MTS - YouTube
The cutter may very well use a heavy glass using lead oxides ...unlike nakamichi players that i believe are making use of a a very light glass unless an organic one...perhaps showing much less vibration patterns, cause at 12 inch diameter a 7mm glass platter can't weight only 0.5 kg .
Nakamichi Dragon-CT turntable demo - YouTube
Nakamichi TX-1000.MTS - YouTube
The cutter may very well use a heavy glass using lead oxides ...unlike nakamichi players that i believe are making use of a a very light glass unless an organic one...perhaps showing much less vibration patterns, cause at 12 inch diameter a 7mm glass platter can't weight only 0.5 kg .
Last edited:
I did try a disc of glass mounted on a polymer substrate. It was the worse sounding of all the materials.
is that a glass platter?
It's pretty obvious to me that does not look like glass at all. Most likely frosted textured acrylic, which is quite common in many turntable such as Basis and at one point VPI, etc...
I like Acrylic thick platter..........
Not the absolute best but on the average the best.
Rgds
Adelmo
Not the absolute best but on the average the best.
Rgds
Adelmo
lathe motor
Lyrec did make a turntable, model AG-40-2, using their lathe motor that is found in Neumann or Lyrec lathes.
Here is a video of it. Another video. Another video.
In case people want to look at the original stock motor and drive system of the Scully lathe, here's a post of a restoration.
Looks overly complicated. No wonder many studios decided to replace them with direct drive motors!
Lyrec did make a turntable, model AG-40-2, using their lathe motor that is found in Neumann or Lyrec lathes.
Here is a video of it. Another video. Another video.
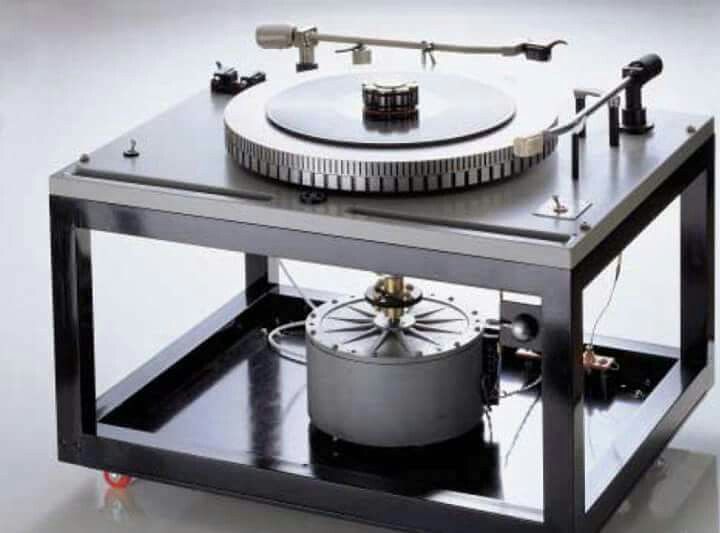
In case people want to look at the original stock motor and drive system of the Scully lathe, here's a post of a restoration.
Looks overly complicated. No wonder many studios decided to replace them with direct drive motors!


Last edited:
Looks overly complicated. No wonder many studios decided to replace them with direct drive motors!
I agree, too complex, too many chances that something will fail !
The Helix uses a magnet between the platter and bearing to reduce load on the ball/thrust pad.
Same as the "Tranquility" add-on developed in the UK for the LP12's "Cirkus" bearing, Warren. 🙂 (I'm using one - you listened to it.)
But a DD motor that rotates at 33 1/3 revolutions does not generate as much vibration as a 2500 RPM motor in a belt system, that is the eternal discussion, the belt together with a high mass of the plate, absorbs that vibration in its entirety ? Exceeds DD?
2500rpm? I think you added a '0'? 🙂
My Premotecs rotate at 250rpm.
Andy
Last edited:
Lyrec lathe
Lyrec made their own lathe using, of course, their own direct drive motor. Noticed in the picture of a lathe in the restoration process, the connecting shaft is decoupled twice between platter and motor with compliant rubber materials. What a beast!
Lyrec made their own lathe using, of course, their own direct drive motor. Noticed in the picture of a lathe in the restoration process, the connecting shaft is decoupled twice between platter and motor with compliant rubber materials. What a beast!
An externally hosted image should be here but it was not working when we last tested it.
An externally hosted image should be here but it was not working when we last tested it.
An externally hosted image should be here but it was not working when we last tested it.
An externally hosted image should be here but it was not working when we last tested it.
the guy on lathe troll site sais its vms 70 is a regular bearing, whatever "regular" might mean...Do you have any photo or evidence of it being a sleeve bearing?A heavy platter also needs some sort of thrust bearing for support...
A regular bearing for a turntable/LP lathe is a sleeve bearing, this is because they run far quieter than ball race bearings. Ball race bearings even ABEC 11 make noise that is audible with a stethoscope and have clearance between the balls and cage. The bearing in my TT is inaudible with a stethoscope.
I have been experimenting with bearings because one of my SP10 motors has a bad sleeve. Ball race was ruled out because it was too noisy. Best I have made so far is PTFE but this will wear quicker than bronze.
- Home
- Source & Line
- Analogue Source
- Ultimate turntable design: modern technology to remediate root cause issues