Now my idea is to introduce a couple of rubber wheels on the upper and lower side of the two corrugator rods and that this will make feeding of the foil into the corrugator more evenly. The other idea I have is to make a type of steering mechanism to the input of the corrugator preventing the foil from misaligning. This tells me that the pressure between the two corrugating rods have to be adjusted to be loose enough to allow correct feeding of the foil. A picture of your corrugator would be informative to those of us (NERDS) that have a special interest in these type of DIY speakers.
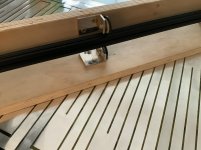
Yes I used a couple of ball bearing wheels off a drawer slide and machined a little groove for the O rings. Soft skate board wheels will work also.
You have to cut your starting edge perfectly parallel to the first trace and as you come up to the trace looking down, use the wood edge to view if its parallel and adjust before it it gets there.
I too use Krell clones both 150 monos and 100 monos
Regards
David
They seems to have a number of polyimide films, like 0.25 mil (6.35 µm).
is erveryone here talking bass panels or tweeters ?
i dont think there is need for really thin foil, the amount aluminium on there will dwarf having 6 or 12 or 20 micron film.
anyone knows the original foil and thickness ?
Last edited:
Post #91 I show widths of a Diva 1989 stock bass panel. I do not know the dims.
of other models and sure they vary across the range.
The rods you can get at DRP performance (off road) supplies. Anodized aluminum
They do sell an 1.125” diameter rod BUT it has same 9 peak profile as the 1/2” shown here and would be spread out even more and why I didn’t use the bigger version.
You will notice that the peaks and valleys do not follow a perfect 1 to 1 ratio as you would in say , straight cut gears in a racing transmission for instance, but anything in this length is difficult to find and while not what I would want ultimately, it is what it is..
A decorative light pole or floor mat pressed together�� might work hehe
Regards
David
of other models and sure they vary across the range.
The rods you can get at DRP performance (off road) supplies. Anodized aluminum
They do sell an 1.125” diameter rod BUT it has same 9 peak profile as the 1/2” shown here and would be spread out even more and why I didn’t use the bigger version.
You will notice that the peaks and valleys do not follow a perfect 1 to 1 ratio as you would in say , straight cut gears in a racing transmission for instance, but anything in this length is difficult to find and while not what I would want ultimately, it is what it is..
A decorative light pole or floor mat pressed together�� might work hehe
Regards
David
Last edited:
Post #91 I show widths of a Diva 1989 stock bass panel. I do not know the dims.
of other models and sure they vary across the range.
The rods you can get at DRP performance (off road) supplies. Anodized aluminum
They do sell an 1.125” diameter rod BUT it has same 9 peak profile as the 1/2” shown here and would be spread out even more and why I didn’t use the bigger version.
You will notice that the peaks and valleys do not follow a perfect 1 to 1 ratio as you would in say , straight cut gears in a racing transmission for instance, but anything in this length is difficult to find and while not what I would want ultimately, it is what it is..
A decorative light pole or floor mat pressed together�� might work hehe
Regards
David
Hmm i was hunting for crimp rods to
when i think of it Coolblock in bar/rod should fit the bill to. often they are extruded , just like my crimper from the hobby shop. gone do some searching again, else i just machine some out of mdf or something im afraid and stack them
extruded heatsink round - Google Search
what also could work, is buy serveral of those hobby paper crimp machines. (for me the best plan i gues) put them on a rodd , line them up and bolt them together they come often in 8inch long. so 4 of those lined up and some bearings should make a machine. in the worst cant you should have a idler wheel (riding the corugration wheel)in the middle keeping the rods from bending to much.
what also could work, is buy serveral of those hobby paper crimp machines. (for me the best plan i gues) put them on a rodd , line them up and bolt them together they come often in 8inch long. so 4 of those lined up and some bearings should make a machine. in the worst cant you should have a idler wheel (riding the corugration wheel)in the middle keeping the rods from bending to much.
Last edited:
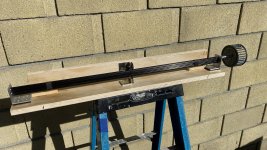
From “L” bracket to L it is 30” long with a 20” cutout area
I did place some cutoff inner tube bands for a little more pressure on the rods
With a little spray lube to rotate easier
Less than 50$
I did think about a spring pressure upper rod with slidable greased plates on the outside L brackets
and might go this route since I would like to try the bigger diameter rods on another set
of wave cut foils
Last edited:
View attachment 795716
From “L” bracket to L it is 30” long with a 20” cutout area
I did place some cutoff inner tube bands for a little more pressure on the rods
With a little spray lube to rotate easier
Less than 50$
I did think about a spring pressure upper rod with slidable greased plates on the outside L brackets
and might go this route since I would like to try the bigger diameter rods on another set
of wave cut foils
Ha nice, i did not read you already addressed the bending ! great minds think alike
Post #118 is a comparison to a stock foil vs my version and 119 is the
complete panel
The peak of the corrugation does touch the valley depth but it doesn’t follow it perfectly
because the valley width is wider than the peaks profile
Not perfect , but close enough for a bass panel
Drp performance has all widths and OD diameters and made of 6061-T6 anodized aluminum
Regards
David
complete panel
The peak of the corrugation does touch the valley depth but it doesn’t follow it perfectly
because the valley width is wider than the peaks profile
Not perfect , but close enough for a bass panel
Drp performance has all widths and OD diameters and made of 6061-T6 anodized aluminum
Regards
David
Last edited:
Another way to corrugate would be a ribbed floor mat.
One could take a plywood strip 4” wide by 20”. 2 pcs and cut 2 sections of the mat and spray glue
To each side of each block the rubber mat and these would be used to compress across
each foil panel.
You just keep going line by line. It might be an issue on each start next to a finished line but worth a try on a test piece.
You might have to provide a depth stop on 1 board and the Kapton back soaped down as the width will draw the foil in due to corrugation shrinkage
You could get fairly accurate lines and not damage either side of the lamination.
I have not tried this, but seems doable and cheap
Regards
David
One could take a plywood strip 4” wide by 20”. 2 pcs and cut 2 sections of the mat and spray glue
To each side of each block the rubber mat and these would be used to compress across
each foil panel.
You just keep going line by line. It might be an issue on each start next to a finished line but worth a try on a test piece.
You might have to provide a depth stop on 1 board and the Kapton back soaped down as the width will draw the foil in due to corrugation shrinkage
You could get fairly accurate lines and not damage either side of the lamination.
I have not tried this, but seems doable and cheap
Regards
David
- Home
- Loudspeakers
- Planars & Exotics
- Anyone making Apogee bass panels?