I suppose one could try ”The Flex-Seal Family of Products” to fix a shoe. 😀 I’ll bet that stuff comes with the Prop 65 warning all over it. Anybody know if that stuff is any good, or just marketing BS?
I tried every adhesive known to science (except miracle products advertised on TV) to fix a delaminated sole on a cycling shoe. I resorted to screws. It worked. Probably not the best thing for putting weight on the heels, but in th application….
I tried every adhesive known to science (except miracle products advertised on TV) to fix a delaminated sole on a cycling shoe. I resorted to screws. It worked. Probably not the best thing for putting weight on the heels, but in th application….
Some plastics need blowlamp / heat gun pass immediately prior to printing, or sticking.
More expensive option is a corona discharge unit, which are used in film plants for example.
In a repair job, mild abrasion may help in achieving a better bond between the surfaces being bonded.
More expensive option is a corona discharge unit, which are used in film plants for example.
In a repair job, mild abrasion may help in achieving a better bond between the surfaces being bonded.
Maybe; but you can't know by looking at their website. They do not post their MSDS sheets. They make SO many products that when you do find data elsewhere, it may not be the goo you want.”The Flex-Seal Family of Products” to fix a shoe. 😀 I’ll bet that stuff comes with the Prop 65 warning all over it.
http://www.haywood.k12.nc.us/wp-content/uploads/sites/12/2016/08/Flex-Seal-Petrochem-Mfg.pdf
A law-firm solicits for Flex-Seal lawsuits:
https://www.clarkfountain.com/blog/the-dangers-of-flex-seal-toxic-exposure/
I'm not convinced of their chemical authority but I am sure they can argue it as long as there is money.
I had a motor driver controlled by a PIC micro.
Worked ok to start with then I got a motor driver IC failure.
Realised motor driver needs decoupling (rookie mistake) due to motor flyback spikes.
So added a 100uf across motor driver ic power supply and that fixed it.
Sold quite a few pcb's without a problem.
Then I noticed sometimes the PIC would crash with rubbish on the lcd display.
Tried 100nf across motor driver power supply and that fixed it.
So while decoupling with a big cap is sort of ok, using a small cap too kills the fast spikes.
I have always known this but for some reason tried to cut corners.
Worked ok to start with then I got a motor driver IC failure.
Realised motor driver needs decoupling (rookie mistake) due to motor flyback spikes.
So added a 100uf across motor driver ic power supply and that fixed it.
Sold quite a few pcb's without a problem.
Then I noticed sometimes the PIC would crash with rubbish on the lcd display.
Tried 100nf across motor driver power supply and that fixed it.
So while decoupling with a big cap is sort of ok, using a small cap too kills the fast spikes.
I have always known this but for some reason tried to cut corners.
My last repair: brought my (AMD Ryzen 9) PC back to life after the last Windows update crashed it beyond recovery (killed WiFi adapter too). Beyond recovery = safe boot impossible. Only the "worst possible" option - reset with total loss of everything remained followed by restoring files and settings. With 2.8Gb only Zinstall offered that automated possibility as the backup image is using a different SSD format.
Nice Microsoft job as the installed version was "pro" and the reset was to "home" - check the present cost of a pro license. But at least the thing more or less works as normal. BTW the main cause of the crash was the (disabled) Realtek audio chip that continues "service" despite having been disabled.
Nice Microsoft job as the installed version was "pro" and the reset was to "home" - check the present cost of a pro license. But at least the thing more or less works as normal. BTW the main cause of the crash was the (disabled) Realtek audio chip that continues "service" despite having been disabled.
A doorbell.
Working some days, not working some days.
Found terrible connectors, no way they could ever make reliable contacts, way too loose, no way to tighten it.
All I could do, was spraying contact cleaner, and it has been working.
Well, so far working, call it fixed, who knows ?
Working some days, not working some days.
Found terrible connectors, no way they could ever make reliable contacts, way too loose, no way to tighten it.
All I could do, was spraying contact cleaner, and it has been working.
Well, so far working, call it fixed, who knows ?
An acoustic guitar I bought has a 3 "fan" bracing scheme, where the middle one had come loose from its gluing to the bottom side of the top. This brace extends from the bridge, about to the heel of the guitar. I could barely reach in there with my hand to feel it wiggle, still being secured at the bridge end. I figured no way am I going to reach back in there with a blob of glue on the end of my finger feel around and get most of it under the loose brace successfully.
So I had previously bought this ear wax examination camera, tethered to a USB interface. Looking in there with it, I could see the offending...situation. But still no way to simultaneously hold the camera and get a fingertip blob of glue under the brace. So I went to the local Tractor supply store, got a syringe and an 18 gauge animal needle set. Took one and ground off the sharp tip;
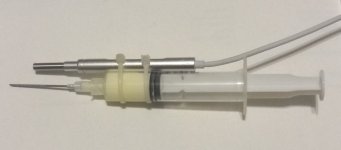
Adjusting the camera back along the syringe axis allows me to see the tip in the corner of the PC displayed image;
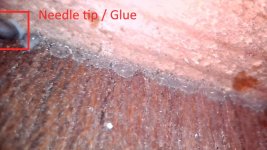
I was able to - because of the extension provided by the syringe / needle, get to the spot needing to be re-glued. The camera's embedded light allowed me to see what I was doing in an otherwise blind area, making the otherwise not possible job, possible;
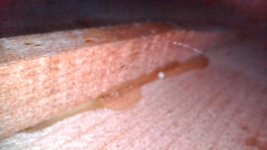
I did make a little spinning jack thing out of one of those metal things you pound into a sheetrock wall, to mount something to the wall with a threaded screw - this put at least some pressure on the brace to hold it up against the top's bottom while the glue set.
Well, the thread title is what did you last repair and this is one of the most recent things, albeit not electrical or audio.
So I had previously bought this ear wax examination camera, tethered to a USB interface. Looking in there with it, I could see the offending...situation. But still no way to simultaneously hold the camera and get a fingertip blob of glue under the brace. So I went to the local Tractor supply store, got a syringe and an 18 gauge animal needle set. Took one and ground off the sharp tip;
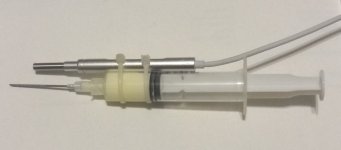
Adjusting the camera back along the syringe axis allows me to see the tip in the corner of the PC displayed image;
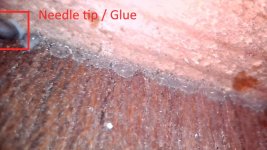
I was able to - because of the extension provided by the syringe / needle, get to the spot needing to be re-glued. The camera's embedded light allowed me to see what I was doing in an otherwise blind area, making the otherwise not possible job, possible;
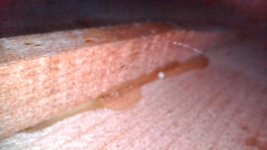
I did make a little spinning jack thing out of one of those metal things you pound into a sheetrock wall, to mount something to the wall with a threaded screw - this put at least some pressure on the brace to hold it up against the top's bottom while the glue set.
Well, the thread title is what did you last repair and this is one of the most recent things, albeit not electrical or audio.
Musical instruments are the SOURCE of audio😉Very much 'audio'.
I swapped output boards in an amp to change tubes... Not really a repair though I guess.
Then I decided I liked listening to the music I was hearing, but I wanted to hear the Raptors game, too. So I used the fact I use make before break switches to my advantage and am now listening to both inputs 1 and 2 LMAO There are no resistors, the two inputs are simply shorted together. Surprising the sound is as good as it is really.
Then I decided I liked listening to the music I was hearing, but I wanted to hear the Raptors game, too. So I used the fact I use make before break switches to my advantage and am now listening to both inputs 1 and 2 LMAO There are no resistors, the two inputs are simply shorted together. Surprising the sound is as good as it is really.
i like jjasniew's guitar repair. clever and very well done. as others have said, its a musical piece so yes its audio 😀
parasound p3 preamp.
'direct 1' input was out on left channel for the rca, and the right channel on the xlr (direct 1 can be switched between either rca or xlr inputs).
very simple section comprising a switch to select rca/xlr, feeding an opamp, feeding a relay, feeding into the rest of the input circuit.
dirty switch contacts.
pulled the switch apart, gentle scrub with a fibreglass pen, clean with flux remover, reassembled with some caig progold, works like a bought one..
marantz sa11s1 cd player.
display would die after a few minutes.
replaced three small electrolytics on the display board, and all good again.
parasound p3 preamp.
'direct 1' input was out on left channel for the rca, and the right channel on the xlr (direct 1 can be switched between either rca or xlr inputs).
very simple section comprising a switch to select rca/xlr, feeding an opamp, feeding a relay, feeding into the rest of the input circuit.
dirty switch contacts.
pulled the switch apart, gentle scrub with a fibreglass pen, clean with flux remover, reassembled with some caig progold, works like a bought one..
marantz sa11s1 cd player.
display would die after a few minutes.
replaced three small electrolytics on the display board, and all good again.
My AKSA/Lender + MoFo would occasionally develop a ground loop in the right channel.
I thought it was the preamp because I recently housed it in a proper case. Moved it around a bit, poked & prodded. No sign of the problem.
Turns out in the MoFo the right channel screw-and-clamp terminal for the input wires in the Mofo wasn't secured. One wire appeared to be inserted, but was actually floating. 🤦♂️
Thanks to everyone who has helped me along the way!
Kind regards,
Drew
I thought it was the preamp because I recently housed it in a proper case. Moved it around a bit, poked & prodded. No sign of the problem.
Turns out in the MoFo the right channel screw-and-clamp terminal for the input wires in the Mofo wasn't secured. One wire appeared to be inserted, but was actually floating. 🤦♂️
Thanks to everyone who has helped me along the way!
Kind regards,
Drew
That's remarkably lame. There are options for buying a license key on ePay for not much money. I'm guessing they're OEM licenses or something.Nice Microsoft job as the installed version was "pro" and the reset was to "home" - check the present cost of a pro license.
Tom
Hickok Cardomatic Tube Tester.
Bit of a minefield especially taking into account it was bought on Ebay with existing Mercury Battery Calibration Cell of which none work anymore.
Trolled the web for ages to find schematic of revised Zener Cal Cell. Lots of fun... 🙂
PS This is a full Military Spec unit and the quality of workmanship is something to behold.
Bit of a minefield especially taking into account it was bought on Ebay with existing Mercury Battery Calibration Cell of which none work anymore.
Trolled the web for ages to find schematic of revised Zener Cal Cell. Lots of fun... 🙂
PS This is a full Military Spec unit and the quality of workmanship is something to behold.
Attachments
For Win 10, no more. The certified one I had bought now was deemed invalid by Microsoft. So I updated to Win 11 and was rather surprised that at first look, the GUI was the same as I had figured out with Open-Shell on Win 10. Sure enough it was Win 11 and that accepts my rejection of Realtek Audio with associated (distortion of) Dolby, that even was running when Realtek Audio is disabled.That's remarkably lame. There are options for buying a license key on ePay for not much money. I'm guessing they're OEM licenses or something.
Tom
Yamaha PF15 electronic piano with the sustain stuck on, which turned out to be a broken solder connection on the board-mounted 1/4 inch jack for the sustain pedal. It took longer to get in the unit than to do the fix.
Before that I replaced an HD-800 cable with Sommer Cicada for the wire, along with a full-size 4 pin XLR matching my headphone amp.
Around that time I also replaced an inordinately noisy fan on an Apogee CRQ-12 parametric equaliser (lovely unit, rarer than hen's teeth) with a Noctua computer fan (Noctuas are quiiiiiet). A bit of fiddling was needed to drop the 24 volt fan supply to the 12 volts the new unit preferred.
Before that I replaced an HD-800 cable with Sommer Cicada for the wire, along with a full-size 4 pin XLR matching my headphone amp.
Around that time I also replaced an inordinately noisy fan on an Apogee CRQ-12 parametric equaliser (lovely unit, rarer than hen's teeth) with a Noctua computer fan (Noctuas are quiiiiiet). A bit of fiddling was needed to drop the 24 volt fan supply to the 12 volts the new unit preferred.
Some people I know use a 7812 to control the fan voltage from the main supply to a fiber optic light guide using a halogen lamp, used for surgery.
The halogens were 150W / 15V, some were 24V, higher watts.
Spotlight type lamps, focus to one end of a fiber optic cable, the other end usually head mounted, or on a long guide (as in endoscopy).
I use oil to lube the sleeve bearings on fans, easy (usually rubber bush under sticker, add with a syringe), a little grease as well, keeps them quiet.
24V is a common DC fan voltage, maybe you could have got that instead of a 12V unit?
Don't take it personally, I prefer to install mains operated fans, they are without the DC to AC converter in DC fans, and are much more reliable than DC fans.
Oddly enough, the ones with sleeve bearings are quieter than the ones with ball bearings from the same maker!
The halogens were 150W / 15V, some were 24V, higher watts.
Spotlight type lamps, focus to one end of a fiber optic cable, the other end usually head mounted, or on a long guide (as in endoscopy).
I use oil to lube the sleeve bearings on fans, easy (usually rubber bush under sticker, add with a syringe), a little grease as well, keeps them quiet.
24V is a common DC fan voltage, maybe you could have got that instead of a 12V unit?
Don't take it personally, I prefer to install mains operated fans, they are without the DC to AC converter in DC fans, and are much more reliable than DC fans.
Oddly enough, the ones with sleeve bearings are quieter than the ones with ball bearings from the same maker!
Last edited:
Automatic LED light, lead acid batteries died, put Lithium with Zener, and it would drain the 18650 cell.
Removed the Zener, seems fine now, it was 3V9 + 22E resistor to hold to 4.3V.
Removed the Zener, seems fine now, it was 3V9 + 22E resistor to hold to 4.3V.
An old Philips radio / cassette tape set for a friend, stuck in Fast Forward, radio dull.
Cleaned the thing, sprayed the mechanism and switches with a nozzle, it was difficult to open, and he does not need cassette. Used contact cleaner spray through gaps, or removed knobs.
Used epoxy putty to fix the antenna (his sets always have a loose antenna, eye roll).
Managed to get the Fast Forward button up, so no motor noise.
Works, no noisy pots and switches.
Cleaned the thing, sprayed the mechanism and switches with a nozzle, it was difficult to open, and he does not need cassette. Used contact cleaner spray through gaps, or removed knobs.
Used epoxy putty to fix the antenna (his sets always have a loose antenna, eye roll).
Managed to get the Fast Forward button up, so no motor noise.
Works, no noisy pots and switches.
- Home
- Member Areas
- The Lounge
- What did you last repair?