Even more interesting than the M106-beater with like parts, I also would like to do a MW16 Textreme + Bliesma T25B. Imagine the performance of that for a price still less than the M106!
Oh trust me, the M106-beater is already in the plan! Just need to nail down construction techniques from my other research thread. I'll be using ceramic versions of the SB17 and SB26. I'm also considering the possibility of using the Rohacell SB17 as a variant since I'm curious about it and never heard any reviews. I'm also interested in a "M108" using the 8" ceramic SB woofer and my 8.5" waveguide.
Construction technique ? Do you have more to share ? I'm looking for pragmatic enclosures designs
Construction technique ? Do you have more to share ? I'm looking for pragmatic enclosures designs
Box Construction Methods | somasonus
Whoouou 🙂 thx you
(Are you working full time on theses topics ?)
I am at the moment, but not sure how long that will last.
Augerpro,
Given the eliptical shape of the waveguide, would it possible to offer an opposing primiter template, which one can then print and used it with a top bearing flush trim bit to make the waveguide recess?
Thanks
I posted one a while ago, but that might have been over at HTGuide.
If one wants to do something extraordinary, the shape has to mitigate diffraction. This probably leaves out the typical, nice looking, box.
//
//
If one wants to do something extraordinary, the shape has to mitigate diffraction. This probably leaves out the typical, nice looking, box.
//
The nice thing about a waveguide is it illuminates the baffle less. But yes, I wonder if a curved baffle could be 3D printed, perhaps filled with cement, polyurethane, etc. What would be the shape? Simply large radius curves?
From the "ATh4" thread, it seems like a roll-over makes a substantial difference to the better. Anything organic looking with smooth curves is probably not bad. There is a lot of simulation going on en every corner it but I don't know if there is a package that can estimate the FR in different directions from a "box" with different round-over / 3D shape... But it's seems like that one should try to avoid diffraction in any way possible really. A "rounder" shape is foreseen 🙂 Olsen knew...
//
//
Printing a baffle is no problem at all, i did several of them, with your WG design integrated in them. (WG and baffle in one piece), they turned out to be very solid with just PLA and look really nice 🙂
Tomorrow i can post some pictures and STL files if you like.
Tomorrow i can post some pictures and STL files if you like.
Working on spherical integration... Radius of 28cm.
Ikea Blanda Matt bowls, with sb17 nbac as a mid way.
This draft here is with wg 6.5" version, just to evaluate visual look. A round shaped wg would be ideal and avoid any adapter [emoji6]
I already printed the 4" version (too fast)...
Wondering if 5" or 6.5" would give better performance for this application...
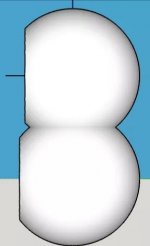
Ikea Blanda Matt bowls, with sb17 nbac as a mid way.
This draft here is with wg 6.5" version, just to evaluate visual look. A round shaped wg would be ideal and avoid any adapter [emoji6]
I already printed the 4" version (too fast)...
Wondering if 5" or 6.5" would give better performance for this application...

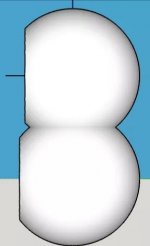
Last edited:
Here are some pictures of my 3D printed baffles and speakers.
Units in this case are Satori MR13 (with edge coating) and 25mm titanium dome tweeters (from Neumann KH120 studio monitors)
Units in this case are Satori MR13 (with edge coating) and 25mm titanium dome tweeters (from Neumann KH120 studio monitors)
Attachments
-
20201022_141937_resized.jpg760.4 KB · Views: 342
-
20201022_142042_resized.jpg666.8 KB · Views: 327
-
20201022_141843_resized.jpg684.1 KB · Views: 377
-
20201022_141838_resized.jpg751.1 KB · Views: 370
-
20201022_141815_resized.jpg596.6 KB · Views: 387
-
20201022_141731_resized.jpg656.1 KB · Views: 641
-
20201022_141713_resized.jpg737.1 KB · Views: 642
-
20200620_212340_resized.jpg802.9 KB · Views: 641
-
20200620_212155_resized.jpg950.4 KB · Views: 659
-
20200620_212118_resized.jpg380.1 KB · Views: 656
Those are purdy!! How do you plan on finishing them cosmetically? A few coats of automotive high-build primer would likely take care of the printing layer lines
Some of these baffles have Augerpro's SB26 5" waveguide integrated, the others waveguides are my own design (for the KH120 tweeter)
I found the KH120 tweeter better than the SB26 so i used these in the final speakers.
I found the KH120 tweeter better than the SB26 so i used these in the final speakers.
Attachments
-
20201022_142531_resized.jpg354.1 KB · Views: 368
-
20201022_142443_resized.jpg594 KB · Views: 346
-
20201022_142440_resized.jpg552.5 KB · Views: 358
-
20201022_142425_resized.jpg644.9 KB · Views: 314
-
20200704_002050_resized.jpg770.1 KB · Views: 331
-
20200621_102021_resized.jpg811.4 KB · Views: 373
-
20201022_142654_resized.jpg674.3 KB · Views: 358
No CNC because i just wanted to try my new 3D printer (Ender 3 Pro)
But believe me, these baffles are very strong/stiff (a lot stronger than MDF), weight is about 0.8 to 1 KG.
Printed with 0.6mm nozzle, 90% infill and 5 inner+outer wall layers
It took about 52 hours to print 1 baffle.
Maybe i will paint them in the future, but for now i like the printed look 😀
I mounted the MR13 from the back, so that the waveguide could overlap the MR13 flange, this way the center to center distance is about 1.5cm less.
But believe me, these baffles are very strong/stiff (a lot stronger than MDF), weight is about 0.8 to 1 KG.
Printed with 0.6mm nozzle, 90% infill and 5 inner+outer wall layers
It took about 52 hours to print 1 baffle.
Maybe i will paint them in the future, but for now i like the printed look 😀
I mounted the MR13 from the back, so that the waveguide could overlap the MR13 flange, this way the center to center distance is about 1.5cm less.
Holy, 90% infill.
Did you consider to create a honeycomb grid open from the back, that you could fill in with epoxy composite (granite dust & grit is a common mix) and/or or construction adhesive?
Epoxy granite stiffness - follow-up - YouTube
Did you consider to create a honeycomb grid open from the back, that you could fill in with epoxy composite (granite dust & grit is a common mix) and/or or construction adhesive?
Epoxy granite stiffness - follow-up - YouTube
Last edited:
Some of these baffles have Augerpro's SB26 5" waveguide integrated, the others waveguides are my own design (for the KH120 tweeter)
I found the KH120 tweeter better than the SB26 so i used these in the final speakers.
Beautiful. What software are you using to set these up?
Some of these baffles have Augerpro's SB26 5" waveguide integrated, the others waveguides are my own design (for the KH120 tweeter)
I found the KH120 tweeter better than the SB26 so i used these in the final speakers.
That looks awesome 🙂 How do you attach the baffle to the box?
- Home
- Loudspeakers
- Multi-Way
- Open source Waveguides for CNC & 3D printing!