Looking good Turbon, how is it playing?
Better than I expected. Some resonances but the geometry wasn't right during the test. Will test again tomorrow.
Brgds
hat are you using for the arm wand?
Squiffything: I watched the videos, looked good, although a little "odd". Found a video for a 30 ft tonearm. That is just a little too long...
Gijsch: just remember to do whatever must be done to get the height of the pivot "in the ball park" to allow for an initial VTA setting. So put the base on a block of wood or something (thin shims, etc).
Jay1234: A ridge cut into a long dowel can work, then just use a few O-rings to hold the wire in there (or glue or whatever you wish...rubber cement would work and allow the removal of the wire if you decide to rewire it.
All: With regards to adjusting VTA, I think Gijsch has it about right. On a 9" arm once the initial VTA is set, you should only have to adjust the pivot +0.010", -0.005" to dial the arm in for various record thicknesses. So if wanting a "set it and forget it" option, a gross adjustment should be available. With the 219, with its 307mm effective length, you may need adjustments of +0.015, -0.0065
Turbon: the tubing looks like it is very thick wall. If possible, try for an arrow shaft, they're much thinner wall (therefore much lighter) and very stiff. When playing the bottom edge of the cartridge (and usually the arm) should be near parallel to the surface of the record. The VTA would then be close.Ok, my proof of concept is done. It works.
Next iteration will be a more rigid build.
Brgds
Squiffything: I watched the videos, looked good, although a little "odd". Found a video for a 30 ft tonearm. That is just a little too long...
Gijsch: just remember to do whatever must be done to get the height of the pivot "in the ball park" to allow for an initial VTA setting. So put the base on a block of wood or something (thin shims, etc).
Jay1234: A ridge cut into a long dowel can work, then just use a few O-rings to hold the wire in there (or glue or whatever you wish...rubber cement would work and allow the removal of the wire if you decide to rewire it.
All: With regards to adjusting VTA, I think Gijsch has it about right. On a 9" arm once the initial VTA is set, you should only have to adjust the pivot +0.010", -0.005" to dial the arm in for various record thicknesses. So if wanting a "set it and forget it" option, a gross adjustment should be available. With the 219, with its 307mm effective length, you may need adjustments of +0.015, -0.0065
a few more pictures
a little better look at te base with vta adjustment. Thumbscrew has a 6 mm thread, locknut is needed for a solid construction. I ve got about 10 mm of adjustment range, so way more than needed. Just hope the adjustment will not be too coarse.
headshell.
rather heavy in comparison to the armwand, but wanted to stay with brass.
Effective mass is 15 grammes for this 10" arm, should fit my cartridge quite nice.
Not sure yet if I will try to keep the wires inside the wand, or fix them to the outside with a few O-rings
An externally hosted image should be here but it was not working when we last tested it.
a little better look at te base with vta adjustment. Thumbscrew has a 6 mm thread, locknut is needed for a solid construction. I ve got about 10 mm of adjustment range, so way more than needed. Just hope the adjustment will not be too coarse.
An externally hosted image should be here but it was not working when we last tested it.
headshell.
rather heavy in comparison to the armwand, but wanted to stay with brass.
Effective mass is 15 grammes for this 10" arm, should fit my cartridge quite nice.
Not sure yet if I will try to keep the wires inside the wand, or fix them to the outside with a few O-rings
Sorry to Jump In...But, I Liked Stew's thoughts on a Straight HeadShell...Needle to Pivot...So, I just made One...
Damn...These are Easy to Make...And, it Sounds Great and Balances Naturally.
TT Spindle to Tone Arm Pivot; 10"...Pivot to Needle 10 5/8"...21 Deg Angle..
Damn...These are Easy to Make...And, it Sounds Great and Balances Naturally.
TT Spindle to Tone Arm Pivot; 10"...Pivot to Needle 10 5/8"...21 Deg Angle..
Attachments
Last edited:
Got geometry set so no more resonances as I had yesterday. It's quite amazing how good it sounds. 🙂. Yes, the walls are quite thick on this carbon tube but that was what I had at hand and this is just a test to learn from. The arrows - how thick are the walls on them?
I found 8mm od / 7.1mm id Al tubing - weight 26.67g/m. Does the arrows have thinner walls? I also found carbon tube 8mm od / 7mm id - weight 22g/m.
I will probably go for the al even if it is heavier.
Nice photos of the base and headshells! Very tidy.
Brgds
I found 8mm od / 7.1mm id Al tubing - weight 26.67g/m. Does the arrows have thinner walls? I also found carbon tube 8mm od / 7mm id - weight 22g/m.
I will probably go for the al even if it is heavier.
Nice photos of the base and headshells! Very tidy.
Brgds
Last edited:
mass of my iteration.
Guys: a 360 mm (14.173") length of the arrow shafts that I am using weighs in at 12.4 g, so a little heavier than what is being suggested, but the OD is 9.35 mm or about .3681" (so 1.35mm larger OD). The wall thickness is .4318 mm or 0.017". The larger diameter allows a thinner wall for a given strength. I think the stiffness to weight ratio is appropriate, and I suspect that the 8mm carbon fibre will be similarly stiff but approximately 50% lighter. The 8mm aluminium tubing will be about 20% lighter, but without a specification of exactly what alloy (eg 7075, 7071) and what temper is used (eg: T6, T7, T9) there is no reason to believe that it will be stronger (the 7075-T9 arrow shafts have an ultimate strength of 96ksi). 7000 series aluminium alloys are typically the highest strength of any aluminium alloy. Unsure of carbon fibre's physical properties, other than it is very light.
sled:
Turbon: Great to hear that all the resonances worked out. Pretty amazing for such a little investment 🙂.
Gijsch: Don't get too worried about a little more mass at the headshell. Actually a slightly heavier headshell does have some benefits: the cartridge will stabilize laterally and be much more difficult to upset.
All: Again I must compliment the builders who have posted their builds , they have way more skill than I do. Keep up the great work guys.
Guys: a 360 mm (14.173") length of the arrow shafts that I am using weighs in at 12.4 g, so a little heavier than what is being suggested, but the OD is 9.35 mm or about .3681" (so 1.35mm larger OD). The wall thickness is .4318 mm or 0.017". The larger diameter allows a thinner wall for a given strength. I think the stiffness to weight ratio is appropriate, and I suspect that the 8mm carbon fibre will be similarly stiff but approximately 50% lighter. The 8mm aluminium tubing will be about 20% lighter, but without a specification of exactly what alloy (eg 7075, 7071) and what temper is used (eg: T6, T7, T9) there is no reason to believe that it will be stronger (the 7075-T9 arrow shafts have an ultimate strength of 96ksi). 7000 series aluminium alloys are typically the highest strength of any aluminium alloy. Unsure of carbon fibre's physical properties, other than it is very light.
sled:
no need for apologies. As I have no wood working machines , nor any skill, I will take your word for it. I might suggest that the inside screw hole be created in an arc to allow for easier alignment. I'll just continue with my hacked together stuff until I complete all the details to my satisfaction. Your headshell looks great by the way.Sorry to Jump In...But, I Liked Stew's thoughts on a Straight HeadShell...Needle to Pivot...So, I just made One...
Damn...These are Easy to Make...And, it Sounds Great and Balances Naturally.
TT Spindle to Tone Arm Pivot; 10"...Pivot to Needle 10 5/8"...21 Deg Angle..
Turbon: Great to hear that all the resonances worked out. Pretty amazing for such a little investment 🙂.
Gijsch: Don't get too worried about a little more mass at the headshell. Actually a slightly heavier headshell does have some benefits: the cartridge will stabilize laterally and be much more difficult to upset.
All: Again I must compliment the builders who have posted their builds , they have way more skill than I do. Keep up the great work guys.
Though to be fair the added weight at that point (directly below the pivot point ) could be of benefit to overall stability.......Any thoughts about this?
Nice idea for VTA, can you post a pic of the thumb screw..without arm tube in the way lol
I'd like to incorporate something like that myself providing it can be made quite solid.
Jay
I guess the added mass is so small here that it would not affect the stability at all. Maybe a gramme for the bearing cup?
The VTA thumbscrew is really stable, once the locknut is tightened down. The adjustment might be too coarse, but this was what I had at hand.
Nanook, I guess it's a nice collaboration then. Your ideas, our hands. You made it seem so simple to build this arm that quite a few people took the bait. I Guess that's just one of your qualities 🙂
Thanks a lot for getting me into this fun!
Last edited:
I guess the added mass is so small here that it would not affect the stability at all. Maybe a gramme for the bearing cup?
The VTA thumbscrew is really stable, once the locknut is tightened down. The adjustment might be too coarse, but this was what I had at hand.
Gijsch - it won't be to coarse. An M6 will rise 1mm for each turn so quarter of a turn will elevate the pivot 0,25mm.
Nanook, I guess it's a nice collaboration then. Your ideas, our hands. You made it seem so simple to build this arm that quite a few people took the bait. I Guess that's just one of your qualities 🙂
Thanks a lot for getting me into this fun!
Hear hear 😀
Nanook - Easton Jazz 7075 aluminium - are these good enough?
Brgds
Last edited:
Sorry if a little long. Continuing developments.
folks,
I have been "classified" as an innovator (not a creator) by many that know me as being able to see through clutter and get to the point (so to speak). Some find that in itself abrasive, hence any apologies that have been expressed by myself on this thread.
Turbon: Yes! Easton Jazz arrow shafts are more than adequate. Just remember that the larger the diameter, the stiffer the shaft for a given wall thickness (unless using some sort of super exotic material). The shafts that I use are XX75 "Gamegetter" hunting arrows. They are inexpensive (cannot remember the price when I bought the ones I have, but the archery range suggested they were perhaps the best buy).
Gijsch:
Hope this doesn't become an overly distracting obsession for any. Up until recently, few took the bait. Perhaps under 20 people or so. That includes those that have recently posted and those that have shown interest: Jay, Turbon, Gijsch, sled108, Squiffything, Chris, hajj, a.wayne, Helmuth, laiphroaig, et al. I guess I thought that if I could build a satisfying results using nothing but a Dremel tool, an allen key, a small hand saw, and a pipe cutter, then others could too. A file is handy, but I think that pretty much is the complete list of tools that I used to create the first one.
Once, I had a phone conversation with one of the guys from Sumiko (or was it Spiral Groove?). He suggested that the most difficult thing to do in audio was to find a manufacturer who would build an item to the exact specs, without trying to put their own twist on it (as in change the design, etc). He suggested design was much easier to do. Thus I have decided that DIY and "cottage" manufacturing in my home is most likely the result. Obviously DIY for the folks here, and the "cottage" manufacturing for any commercial version that is to be offered.
One thing that I truly believe in is "but right, sell at a reasonable price". An old boss of mine (thanks Martin) taught me that you make money when you buy, not when you sell. So things like trying to purchase in large enough quantities to gain some sort of discount, or rather than purchasing Parker ball point pen refills, perhaps seek out another similar, yet suitable brands could very well occur, but the base specifications will remain without any changes.
Outside costs are the only thing that I have little or no control over other than that. For example, if I prefer Easton 2317 shafts, but can get 2217s as a "special, guess what. I'll build arms using 2217, and deal with any changes due to that. Now if I can wholesale say 10 dozen 2317s I can completely standardize the tonearms, which would be ( in a manufacturing sense) the goal. Any changes after that would have to consider this.
Now for any that have expressed interest in helping out via machining, etc., I will definitely have a look and hope that I could make use of the kind offers. Kickstarter is the place to be for crowd sourced funding and whole reason for that is to allow me to invest in machinery to streamline the manufacturing process and increase consistency in the end product. The last pieces to the puzzle are ergonomic and aesthetic in nature. Of course there might be economies of scale, but the least of the issues for the arms themselves is economic. As I have suggested, buying an arm lift is easily the most expensive part on these arms in terms or purchasing. I am going to devise my own. It may not be operationally smooth, but should do the job. I've posted elsewhere on diyAudio regarding how simple a arm lift can be (similar to what ChrisG had posted). Simple. Mechanically as sophisticated as a hammer, but useable.
Please note that should any ideas from the thread be used (eg: alternate headshells other than the Scheu, my original wooden types, or the offset type with the stylus point inline with the centre of the arm as sled108 had so beautifully built ), permission will be asked for use, and credit will be given.
Once I have the arm where I think I have all of the correct pieces together is when I will offer it on Kickstarter, with rewards of headshells, arm "kits" (an arm tube, the female bearing installed and the pivot), and complete arms. It may be that some who have offered could support me by providing parts as they had suggested, or limited edition headshells (again as some have suggested) or whatever they feel they can contribute. I would consider that as a "donation in kind" to any that chose to do so.
Then just wait a little while.😉
Many may or may not know that I have reviewed audio gear in the past and would like to continue with that. I had outlined what I think constitutes a good turntable design and had written this opinion in Affordable$$Audio. If I can find the issue I'll post it in this thread , and perhaps start a "splinter" thread regarding that. If successful, I'll do the same for a turntable (design is complete). It may require me purchasing parts from some folks that already make them, but (sorry to beat a dead dog here) with my own take on turntable design. The other option would be to modify an existing table with suitable components into something much more than what the parts might suggest (as exemplified by the various Lenco, Rega and Linn rebuilds and custom parts now being offered). Again, this thread would not be an exercise in democracy, but open to comments, discussions and arguments ( as a debate argument, not an attack or anything like that).
Lastly, thus far the new job hasn't started. I think the fellow was just BS'ing me, so I feel I must do something to keep busy. Thus the Kickstarter project and continued refinement of the 219 are to be pushed to the forefront of my pursuits, regardless of any potential employment.
folks,
I have been "classified" as an innovator (not a creator) by many that know me as being able to see through clutter and get to the point (so to speak). Some find that in itself abrasive, hence any apologies that have been expressed by myself on this thread.
Turbon: Yes! Easton Jazz arrow shafts are more than adequate. Just remember that the larger the diameter, the stiffer the shaft for a given wall thickness (unless using some sort of super exotic material). The shafts that I use are XX75 "Gamegetter" hunting arrows. They are inexpensive (cannot remember the price when I bought the ones I have, but the archery range suggested they were perhaps the best buy).
Gijsch:
Nanook, I guess it's a nice collaboration then. Your ideas, our hands. You made it seem so simple to build this arm that quite a few people took the bait. I Guess that's just one of your qualities 🙂
Thanks a lot for getting me into this fun!
Hope this doesn't become an overly distracting obsession for any. Up until recently, few took the bait. Perhaps under 20 people or so. That includes those that have recently posted and those that have shown interest: Jay, Turbon, Gijsch, sled108, Squiffything, Chris, hajj, a.wayne, Helmuth, laiphroaig, et al. I guess I thought that if I could build a satisfying results using nothing but a Dremel tool, an allen key, a small hand saw, and a pipe cutter, then others could too. A file is handy, but I think that pretty much is the complete list of tools that I used to create the first one.
Once, I had a phone conversation with one of the guys from Sumiko (or was it Spiral Groove?). He suggested that the most difficult thing to do in audio was to find a manufacturer who would build an item to the exact specs, without trying to put their own twist on it (as in change the design, etc). He suggested design was much easier to do. Thus I have decided that DIY and "cottage" manufacturing in my home is most likely the result. Obviously DIY for the folks here, and the "cottage" manufacturing for any commercial version that is to be offered.
One thing that I truly believe in is "but right, sell at a reasonable price". An old boss of mine (thanks Martin) taught me that you make money when you buy, not when you sell. So things like trying to purchase in large enough quantities to gain some sort of discount, or rather than purchasing Parker ball point pen refills, perhaps seek out another similar, yet suitable brands could very well occur, but the base specifications will remain without any changes.
Outside costs are the only thing that I have little or no control over other than that. For example, if I prefer Easton 2317 shafts, but can get 2217s as a "special, guess what. I'll build arms using 2217, and deal with any changes due to that. Now if I can wholesale say 10 dozen 2317s I can completely standardize the tonearms, which would be ( in a manufacturing sense) the goal. Any changes after that would have to consider this.
Now for any that have expressed interest in helping out via machining, etc., I will definitely have a look and hope that I could make use of the kind offers. Kickstarter is the place to be for crowd sourced funding and whole reason for that is to allow me to invest in machinery to streamline the manufacturing process and increase consistency in the end product. The last pieces to the puzzle are ergonomic and aesthetic in nature. Of course there might be economies of scale, but the least of the issues for the arms themselves is economic. As I have suggested, buying an arm lift is easily the most expensive part on these arms in terms or purchasing. I am going to devise my own. It may not be operationally smooth, but should do the job. I've posted elsewhere on diyAudio regarding how simple a arm lift can be (similar to what ChrisG had posted). Simple. Mechanically as sophisticated as a hammer, but useable.
Please note that should any ideas from the thread be used (eg: alternate headshells other than the Scheu, my original wooden types, or the offset type with the stylus point inline with the centre of the arm as sled108 had so beautifully built ), permission will be asked for use, and credit will be given.
Once I have the arm where I think I have all of the correct pieces together is when I will offer it on Kickstarter, with rewards of headshells, arm "kits" (an arm tube, the female bearing installed and the pivot), and complete arms. It may be that some who have offered could support me by providing parts as they had suggested, or limited edition headshells (again as some have suggested) or whatever they feel they can contribute. I would consider that as a "donation in kind" to any that chose to do so.
Then just wait a little while.😉
Many may or may not know that I have reviewed audio gear in the past and would like to continue with that. I had outlined what I think constitutes a good turntable design and had written this opinion in Affordable$$Audio. If I can find the issue I'll post it in this thread , and perhaps start a "splinter" thread regarding that. If successful, I'll do the same for a turntable (design is complete). It may require me purchasing parts from some folks that already make them, but (sorry to beat a dead dog here) with my own take on turntable design. The other option would be to modify an existing table with suitable components into something much more than what the parts might suggest (as exemplified by the various Lenco, Rega and Linn rebuilds and custom parts now being offered). Again, this thread would not be an exercise in democracy, but open to comments, discussions and arguments ( as a debate argument, not an attack or anything like that).
Lastly, thus far the new job hasn't started. I think the fellow was just BS'ing me, so I feel I must do something to keep busy. Thus the Kickstarter project and continued refinement of the 219 are to be pushed to the forefront of my pursuits, regardless of any potential employment.
sled's headshell
sled:
Was the "Damn...These are Easy to Make" reference to the headshell, the arm, or both? In any possible Kickstarter offering I was thinking that a 10.5" arm would be a nice compromise between length (and therefore superior tracking error) and convenience regarding the retro-fit to existing turntables. Anybody have any thoughts on this?
sled:
Sorry to Jump In...But, I Liked Stew's thoughts on a Straight HeadShell...Needle to Pivot...So, I just made One...
Damn...These are Easy to Make...And, it Sounds Great and Balances Naturally.
TT Spindle to Tone Arm Pivot; 10"...Pivot to Needle 10 5/8"...21 Deg Angle..
Was the "Damn...These are Easy to Make" reference to the headshell, the arm, or both? In any possible Kickstarter offering I was thinking that a 10.5" arm would be a nice compromise between length (and therefore superior tracking error) and convenience regarding the retro-fit to existing turntables. Anybody have any thoughts on this?
"I'll do the same for a turntable (design is complete)."
Will follow this with the greatest interest and if I know myself - try to make my own 🙂
Brgds
Will follow this with the greatest interest and if I know myself - try to make my own 🙂
Brgds
Uni-pivot arm number two is coming along nicely. Still to do the wiring and decide how I'm going to connect the headshell but the design for the body is pretty much sorted.
Two foot of Carbon fibre arm wand will have it sitting on the coffee table thereby saving me the hassle of getting up when the record ends 🙂
OK two foot is just too damn long and this will be shortened I just wanted to see how it would work. It's like one of those situations where you just know it shouldn't be done but you have just gotta do it, just to see, just so that you can say 'yup I did it'
The ingredients for this recipe are as follows:
2 x draw handles for the main body pieces.
1 x draw handle for the counter weight. I think this is going to be too heavy if I go for a shorter arm but there is a smaller version, although not in stock when I purchased.
1 x very small diameter 2 foot+ long arrow shaft.
1 x computer mouse cord. I may change this out for earbud style speaker cable if I go for the shorter arm.
1 x ball point pen blank.
various bits and bobs from down the shed to make up the rest of the body.
The pivot is different on this one in that it is cut into the top section of the body very near to the top and above the tube of the arm. The wiring will come out before the body section then thread into and through the lower body thereby tidying it all up.
The design is to compliment the Saturn and to be fixed ultimately as a second arm. This is the first time I have worked with metal on one of my designs and without a lathe or proper tooling it's damned hard to get things right. Just drilling a hole through the body section had my metal drill bits glowing red hot!!! Stew it's alot easier working with simple materials when you only have the basic tools to play with 🙂
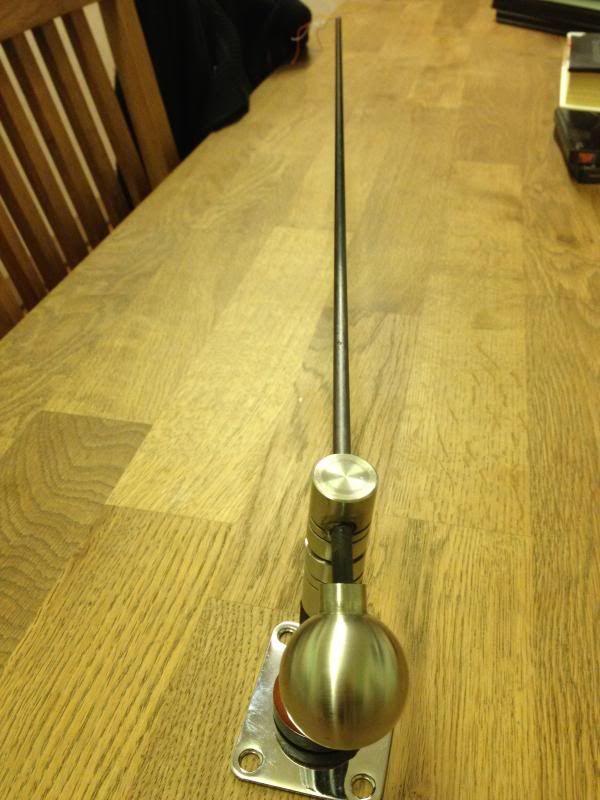
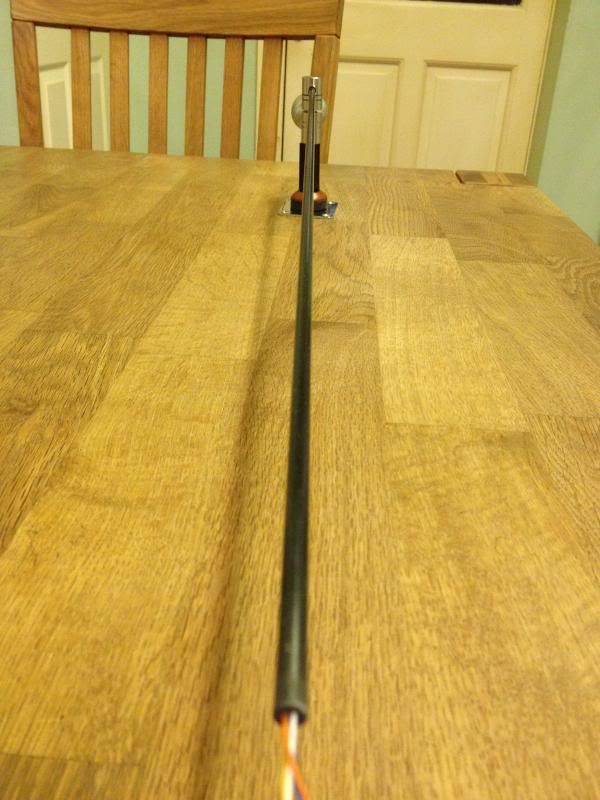
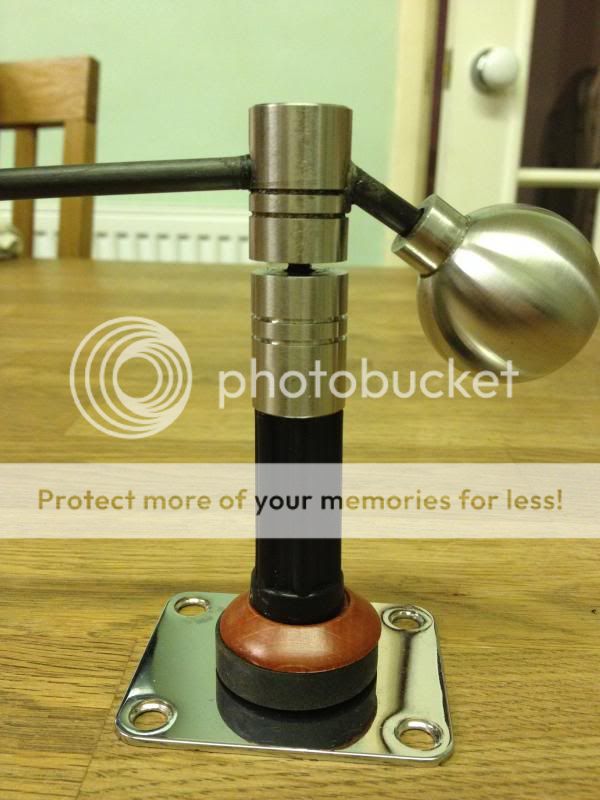
Two foot of Carbon fibre arm wand will have it sitting on the coffee table thereby saving me the hassle of getting up when the record ends 🙂
OK two foot is just too damn long and this will be shortened I just wanted to see how it would work. It's like one of those situations where you just know it shouldn't be done but you have just gotta do it, just to see, just so that you can say 'yup I did it'
The ingredients for this recipe are as follows:
2 x draw handles for the main body pieces.
1 x draw handle for the counter weight. I think this is going to be too heavy if I go for a shorter arm but there is a smaller version, although not in stock when I purchased.
1 x very small diameter 2 foot+ long arrow shaft.
1 x computer mouse cord. I may change this out for earbud style speaker cable if I go for the shorter arm.
1 x ball point pen blank.
various bits and bobs from down the shed to make up the rest of the body.
The pivot is different on this one in that it is cut into the top section of the body very near to the top and above the tube of the arm. The wiring will come out before the body section then thread into and through the lower body thereby tidying it all up.
The design is to compliment the Saturn and to be fixed ultimately as a second arm. This is the first time I have worked with metal on one of my designs and without a lathe or proper tooling it's damned hard to get things right. Just drilling a hole through the body section had my metal drill bits glowing red hot!!! Stew it's alot easier working with simple materials when you only have the basic tools to play with 🙂
sled:
Was the "Damn...These are Easy to Make" reference to the headshell, the arm, or both? In any possible Kickstarter offering I was thinking that a 10.5" arm would be a nice compromise between length (and therefore superior tracking error) and convenience regarding the retro-fit to existing turntables. Anybody have any thoughts on this?
I was referring to the HeadShell...I use the same Tool Kit as You...That one was made with Hand Saws, an Electric Drill and Sand Paper, on the Kitchen Table with a Wooden Clamp and a Dust Pan and Broom...
It looks very good Squiffything!
I see nothing wrong with keeping things as cheap as possible but neither do I refuse to pay where needed. Go and buy yourself some decent cabling.
I have an urge to get a lathe... Not only for this arm but for many reasons. This might be the reason to make it happen. Maybe I should have bought that 20K$ unipivot wand to keep it cheap ;-)
Brgds
I see nothing wrong with keeping things as cheap as possible but neither do I refuse to pay where needed. Go and buy yourself some decent cabling.
I have an urge to get a lathe... Not only for this arm but for many reasons. This might be the reason to make it happen. Maybe I should have bought that 20K$ unipivot wand to keep it cheap ;-)
Brgds
It looks very good Squiffything!
I see nothing wrong with keeping things as cheap as possible but neither do I refuse to pay where needed. Go and buy yourself some decent cabling.
I have an urge to get a lathe... Not only for this arm but for many reasons. This might be the reason to make it happen. Maybe I should have bought that 20K$ unipivot wand to keep it cheap ;-)
Brgds
I'm happy to make my projects with things that I have, my hobby has to be self funding as there is never spare cash from the household budget. I have just had a birthday so the drawer handles were purchased 🙂 it's amazing just what can get the design juices flowing when you have a wander around the local hardware store. I saw in a local furniture shop the other day a small coffee table with a metal horn shaped base. If it hadn't been for the £50 plus price tag it would have come home with me to chop up to form a mold for some paper mache horns 🙂
A lathe is something that would definately fit in the shed but as I know nothing about using one its usage would be limited so I cannot justify the purchase.
"as I know nothing about using one its usage would be limited" 🙂
+1
Oh and yes - there is a cost as well... I would probably need a better reason for spending on it than making stuff for an TT arm :-(
Brgds
+1
Oh and yes - there is a cost as well... I would probably need a better reason for spending on it than making stuff for an TT arm :-(
Brgds
Last edited:
I made another test. Our wedding trip went to Wienna in -91 where we bought this as a souvenir...
A red Mozart Jubileum 2 LP set. The second one is very warped - they obiously had a rush creating these. The sound is OK on the first LP but the second one was no idea of playing. The cart jumped all over it due to the warps... Now - not a single miss - the cart just rides the waves. Amazing.
I'll give you a picture of the album and a youtube video when I have figured out how to get it there...
Brgds
A red Mozart Jubileum 2 LP set. The second one is very warped - they obiously had a rush creating these. The sound is OK on the first LP but the second one was no idea of playing. The cart jumped all over it due to the warps... Now - not a single miss - the cart just rides the waves. Amazing.
I'll give you a picture of the album and a youtube video when I have figured out how to get it there...
Brgds
Youtube as I have it in the cache: http://youtu.be/Xb0_8HJQ8z4
Pic of the album :
I have to add that I haven't percieved any issues with SQ dealing with the warps.
Brgds
Pic of the album :
An externally hosted image should be here but it was not working when we last tested it.
I have to add that I haven't percieved any issues with SQ dealing with the warps.
Brgds
Last edited:
@squiffything, drilling in stainless steel should be done on a surprisingly low speed. For example a 6 mm hole should be drilled at 500 rpm, and plenty of oil. But what a neat arm it is!
How do you plan to adjust the tracking weight?
With regards to the luxury of a lathe in the shed, the nice thing about it is that you will find more use for it than just a tonearm. And a small one does not really need to be very expensive and still be usefull.
How do you plan to adjust the tracking weight?
With regards to the luxury of a lathe in the shed, the nice thing about it is that you will find more use for it than just a tonearm. And a small one does not really need to be very expensive and still be usefull.
- Status
- Not open for further replies.
- Home
- Source & Line
- Analogue Source
- my latest iteration of "Nanook's 219 tonearm"..