Hi Matthias,
I'm curious on the answers to your question as well.
To my understanding, the hum breaking network (R5||D1||D2 in the HB's v2.4 design) prevents from hum that could be induced into the loop area formed by the two cables running from your preamplifier to the power amp. So, if you strictly separate each channel and their PSUs(the yet mentioned Dual Monoblock design), tying them loosely only by ground breaking networks elsewhere, e.g. next to the ground star of the filter caps (where impedance is lowest), to my understanding these three components on the boards could be omitted, i.e. replaced by a wire jumper.
Edit, after reading jwilhelms last answer: That would mean that we connect the RCA input by a shielded cable (or by a twisted pair) to the PCBs input terminals, and that any other connection from either end of that cable to ground would be contraproductive?
Best regards!
For ground loop prevention the lifted ground on the input has no advantage in a fully isolated dual monoblock design. Direct chassis/earth ground of an input is usually not a good thing. The input hum breaker will keep the amplifier supplies disconnected from earth ground through the input in the event of an earth grounded source which may be beneficial.
HBRR and HBRL as described by D.Joffe does not remove or eliminate the hum from a commoned remote signal return.
The loop still exists. The two added resistances reduces (not eliminates) the interference current.
The Safety connection that is intended to couple any exposed conductive parts (to the protected Chassis) is a quite separate requirement that has nothing to do with the commoned remote signal return.
If your multi-channel amplifier has two, or more, isolated PSUs, then all of them need their own Safety connection to Chassis, not to PE.
This is a reiteration of what I stated earlier
The loop still exists. The two added resistances reduces (not eliminates) the interference current.
The Safety connection that is intended to couple any exposed conductive parts (to the protected Chassis) is a quite separate requirement that has nothing to do with the commoned remote signal return.
If your multi-channel amplifier has two, or more, isolated PSUs, then all of them need their own Safety connection to Chassis, not to PE.
This is a reiteration of what I stated earlier
Each isolated PSU needs it's own MAG to Chassis Safety connection.
If one has 4 secondaries (from two dual secondary transformers, or a quad secondary transformer), then there can be two MAGs, one dedicated to each amplifier.
Both these MAGs need separate safety connections to the Chassis.
Last edited:
Hi,
related to this thread http://www.diyaudio.com/forums/solid-state/294664-diyab-amp-honey-badger-line-grid-board.html I have the problem of an increasing bias when the temperature of the heat sink is getting higher, means the bias is under-compensated. I am using a MJE340 for Q13.
After some reading about bias servo, my plan is now to change R28 from 2.2k to 3.3k (or even higher) to increase the VBE amplification until bias is stable.
Is that a good idea or will I introduce other issues by that?
related to this thread http://www.diyaudio.com/forums/solid-state/294664-diyab-amp-honey-badger-line-grid-board.html I have the problem of an increasing bias when the temperature of the heat sink is getting higher, means the bias is under-compensated. I am using a MJE340 for Q13.
After some reading about bias servo, my plan is now to change R28 from 2.2k to 3.3k (or even higher) to increase the VBE amplification until bias is stable.
Is that a good idea or will I introduce other issues by that?
Last edited:
As you increase the resistor from one side of the transistor's base, you'd also have to increase the other one by the same ratio, in order to achieve the correct Vce for biasing the cold output devices. Thus the Vbe multiplying factor will remain constant. Perhaps a second transistor, wired as a diode and also mounted on the heatsink, in the emitter lead of the first one would solve your problem?
This is where I found the hint with the resistor values Elliott Sound Products - Audio Power Amplifier Design Guidelines. I must admit that I haven't really understood how the VBE amplification can be adjusted by that. And another thing that I am wondering about is that the temperature co-efficient of BJTs is not specified in the data sheets I have checked. Only information I could find was roughly 2mV/K. Why is this information not part of a data sheet?
Another idea I had without changes in the schematic was to try around with different types for Q13 like 2SC3503.
Another idea I had without changes in the schematic was to try around with different types for Q13 like 2SC3503.
Hi Folks,
I am building a Honey Badger and just now starting on the power supply and soft start. There are issues, in my mind at least, with Jojo's design in the diyAStore in that there are electronic components always in the AC power circuit with associated dissipation and subsequent uncertainty of outcome should there be a failure.
My solution has been to use a 240Vac relay with a spare contact pole to permanently latch the relay ON after the timing circuit delay. For my Badger with 2 transformers I have an LY4 with 2 sets of contacts controlling the transformer softstart resistors and a 3rd contact to short the timing circuit to keep the relay powered by shorting the timing circuit.
Hope this is useful.
Circuit attached....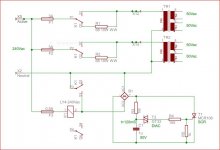
I am building a Honey Badger and just now starting on the power supply and soft start. There are issues, in my mind at least, with Jojo's design in the diyAStore in that there are electronic components always in the AC power circuit with associated dissipation and subsequent uncertainty of outcome should there be a failure.
My solution has been to use a 240Vac relay with a spare contact pole to permanently latch the relay ON after the timing circuit delay. For my Badger with 2 transformers I have an LY4 with 2 sets of contacts controlling the transformer softstart resistors and a 3rd contact to short the timing circuit to keep the relay powered by shorting the timing circuit.
Hope this is useful.
Circuit attached....
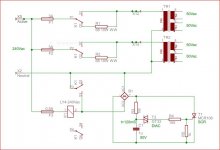
What voltage does the Diac fire at?
How long does the Diac plus Triac take to short across the bridge rectifier?
How high does the voltage across the 1uF 50V capacitor rise before the Triac shorts the supply?
Does this proposal fit within the Forum's Rule about direct to mains circuit discussion?
How long does the Diac plus Triac take to short across the bridge rectifier?
How high does the voltage across the 1uF 50V capacitor rise before the Triac shorts the supply?
Does this proposal fit within the Forum's Rule about direct to mains circuit discussion?
Last edited:
Does this proposal fit within the Forum's Rule about direct to mains circuit discussion?
Surely not. But if we do apply this rule too stringently, the Power Supply section of this board has to be closed as well.
Best regards!
I have written to the Moderatiors specifically asking that the existing rule be reviewed to allow some form of discussion without breaking the Rule.
I have reported a few posts that attempt direct to mains discussion.
So far the Forum have kept the existing ban on discussion of direct to mains circuitry.
Despite the Forum selling PCB that requires direct to mains circuitry that sometimes require discussion.
I have reported a few posts that attempt direct to mains discussion.
So far the Forum have kept the existing ban on discussion of direct to mains circuitry.
Despite the Forum selling PCB that requires direct to mains circuitry that sometimes require discussion.
So, as far as we're not moderators yet, we'd better not cause any excitations, do we?
Best regards!
Best regards!
If the existing rule stays and we correspond on the topic, the Moderators could take action against any Member that cares to make any comment following the first infringement.
It is years since I first raised this as a problem.
It is years since I first raised this as a problem.
Here's a good example of why I prefer doing softstart timing with a microcontroller. Just through hole relays and a radial lead NTC resistor. There is no parts with exposed unisolated mains voltage waiting for someone to touch.
And similar safe working can be assured by using a small isolating transformer to power any of our auxiliary controls.Here's a good example of why I prefer doing softstart timing with a microcontroller. Just through hole relays and a radial lead NTC resistor. There is no parts with exposed unisolated mains voltage waiting for someone to touch.
And similar safe working can be assured by using a small isolating transformer to power any of our auxiliary controls.
Yes this is also a great idea, but seldom done.
What voltage does the Diac fire at?
How long does the Diac plus Triac take to short across the bridge rectifier?
How high does the voltage across the 1uF 50V capacitor rise before the Triac shorts the supply?
Does this proposal fit within the Forum's Rule about direct to mains circuit discussion?
Diacs are imprecise, nominal trigger voltage is 28V, +/- 4V.
From Trigger to SCR fully on < 5uS
Capacitor voltage = Vdiac-trigger + Vscr-gate = (28+0.7) nominal
Yes, this is about the Forum's own direct to mains softstart circuit.
John
small isolating transformer
will always cost more than a 1ufd capacitor,
but i will choose a small traffo over the cap anytime....
Yes this is also a great idea, but seldom done.
you think so? i have used this option for the longest time since 1980,
i only started using the cap option when i saw the design here
a couple of years ago...
you think so? u have used this option for the longest time sin 1980,
i only started using the cap option when i saw the design here
a vouple of years ago...
If you look at pictures of most amps here, there is no isolation transformers on the control circuits unless they are controlling with low voltage.
Do you wind your own control transformers, or just your supply transformers?
If you look at pictures of most amps here, there is no isolation transformers on the control circuits unless they are controlling with low voltage.
Do you wind your own control transformers, or just your supply transformers?
i do wind my own big power traffos with a small secondary winding for for 12 volts or so to use for this function....
small transformers are more economical to buy off shelf than if i wind them,
of course i can wind them if needed...
And similar safe working can be assured by using a small isolating transformer to power any of our auxiliary controls.
yes, but you still have to connect the primaries to mains, and that is working with the mains isn't it?😱
- Home
- Amplifiers
- Solid State
- diyAB Amp The "Honey Badger" build thread