I felt that was likely Warren, but was interested from two points of view, firstly about that type of carriage and secondly whether this was or wasn't an interesting application for a material. I like solutions where something available for one purpose is well suited to something useful.
For example, I have a broken golf shaft that might make a good PTA wand, it's tapered stiff and light and might just be ideal, but i don't do PTA's!
M
For example, I have a broken golf shaft that might make a good PTA wand, it's tapered stiff and light and might just be ideal, but i don't do PTA's!
M
Hi Mark,
I agree that Beryllium would be the dream material for tonearm construction.
It has low density and high modulus which will facilitate the building of a carriage with extremely high bending mode frequencies. It also has the highest speed of sound of any material (at normal, non-exotic pressures). As you say, it's a pity that it is so toxic, up there with plutonium.
The closest material for a high rigidity to density ratio is ultra-high modulus carbon fibre. Especially that with nanotubes in the mix.
I did want to build my carriage with UHM carbon fibre but I couldn't find a non-industrial source.
I reckon I could have made my carriage with a first bending mode of around 28khz. Using standard modulus carbon fibre I still managed 20khz.
I agree that Beryllium would be the dream material for tonearm construction.
It has low density and high modulus which will facilitate the building of a carriage with extremely high bending mode frequencies. It also has the highest speed of sound of any material (at normal, non-exotic pressures). As you say, it's a pity that it is so toxic, up there with plutonium.
The closest material for a high rigidity to density ratio is ultra-high modulus carbon fibre. Especially that with nanotubes in the mix.
I did want to build my carriage with UHM carbon fibre but I couldn't find a non-industrial source.
I reckon I could have made my carriage with a first bending mode of around 28khz. Using standard modulus carbon fibre I still managed 20khz.
Hi gents, thanks for the interesting discussion about the sapphire veneer. @niffy this might wet your appetite with regards to the CNTs https://www.ossila.com/collections/carbon-nanotubes
S.
S.
Hey everyone!
I'm designing a turntable for my senior project. I'm interested in designing and building my own linear tracking tonearm for the project, but I'm a beginner in audio electronics and could use some help figuring out what parts I need and how they generally work. Does anyone have any advice with where to start in building one? Thanks!
I'm designing a turntable for my senior project. I'm interested in designing and building my own linear tracking tonearm for the project, but I'm a beginner in audio electronics and could use some help figuring out what parts I need and how they generally work. Does anyone have any advice with where to start in building one? Thanks!
I’d suggest reading this thread front to back before starting anything. There are only 5424 entries. When I was at university 4 decades ago I had 8000 pages of reading a week in one class alone. You can do this!
Hey everyone!
I'm designing a turntable for my senior project. I'm interested in designing and building my own linear tracking tonearm for the project, but I'm a beginner in audio electronics and could use some help figuring out what parts I need and how they generally work. Does anyone have any advice with where to start in building one? Thanks!
It's really easy. Here is one that I made when I was younger. I made half of it out of trash I had lying around and it still performed better than a lot of high end tonearms.
TJ,
I can't tell you how surprised that I was that your setup worked and how good it sounded given the circumstances. It gives a starting point to improve on, and I suspect that the idea can go farther than expected.
First of all, I would have guessed that the bearings were not fine enough to even use, but apparently they worked. Secondly, as you mentioned in the video a set of more flexible wires will undoubtedly also improve the tracking/skipping.
At first, when I considered that this could be a high school level project, it seemed out of reach, but you have proven me wrong. The biggest problem may be in the appreciation for what was accomplished by those who view it. I had the same reaction in high school when I built a set of bass corner horns. "But the speaker is inside the box. You can't hear it." Then, they heard/felt it.
I can't tell you how surprised that I was that your setup worked and how good it sounded given the circumstances. It gives a starting point to improve on, and I suspect that the idea can go farther than expected.
First of all, I would have guessed that the bearings were not fine enough to even use, but apparently they worked. Secondly, as you mentioned in the video a set of more flexible wires will undoubtedly also improve the tracking/skipping.
At first, when I considered that this could be a high school level project, it seemed out of reach, but you have proven me wrong. The biggest problem may be in the appreciation for what was accomplished by those who view it. I had the same reaction in high school when I built a set of bass corner horns. "But the speaker is inside the box. You can't hear it." Then, they heard/felt it.
Thank you for your kind words. I can't tell you how surprised I was either
. It is truly amazing how much you can do in audio with junk you have lying around.
Some additional thoughts.
The bearings I bought from a skateboard shop at the mall. It may be hard to tell, but the corners of the bearings ride on the glass rods. This minimizes friction to such a degree that the hardest part about this build was trying to set the needle down on the record. It was actually pretty trippy because all your little muscle movements that you don't consciously recognize make it very hard to move something exactly where you want it. The quality of these bearings was surprisingly good. I am sure you can improve it further with ceramic bearings from Japan, but I have a very strong feeling you would find that you would run into diminishing returns EXTREMELY quickly.
The tracking was perfect after some adjustments even with the hard wire. My biggest issue was trying to level the tonearm. I ended up making a base for it that allowed me to level the system with some thumb screws. Didn't do anything to the sound, but it definitely improved reliability. Hard wire was never an issue since and I have been too lazy to replace it. It sounds so good as is, there is really no need.
The big improvement in my case has been swapping out the glass tubes with some precession glass rod. The surface is much more uniform and ended up costing me less than at the art supply store.
Since building this tonearm, there have been many more videos on youtube showing how easy air bearings are to make. There are several videos on using extremely quiet refrigeration pumps to make air compressors. A new video just came out a couple weeks ago showing the process for making an incredibly reliable and easy way of making an air bearing using JB weld, glass and a drill press. I will link the video below. I fully believe that would be a great high school project.
Corner horns are great. I am in the middle of building my home and I have room in my plans just for corner horn listening. Of course I am also working on a 3d printed field coil woofer to go in those horns as well : )

Some additional thoughts.
The bearings I bought from a skateboard shop at the mall. It may be hard to tell, but the corners of the bearings ride on the glass rods. This minimizes friction to such a degree that the hardest part about this build was trying to set the needle down on the record. It was actually pretty trippy because all your little muscle movements that you don't consciously recognize make it very hard to move something exactly where you want it. The quality of these bearings was surprisingly good. I am sure you can improve it further with ceramic bearings from Japan, but I have a very strong feeling you would find that you would run into diminishing returns EXTREMELY quickly.
The tracking was perfect after some adjustments even with the hard wire. My biggest issue was trying to level the tonearm. I ended up making a base for it that allowed me to level the system with some thumb screws. Didn't do anything to the sound, but it definitely improved reliability. Hard wire was never an issue since and I have been too lazy to replace it. It sounds so good as is, there is really no need.
The big improvement in my case has been swapping out the glass tubes with some precession glass rod. The surface is much more uniform and ended up costing me less than at the art supply store.
Since building this tonearm, there have been many more videos on youtube showing how easy air bearings are to make. There are several videos on using extremely quiet refrigeration pumps to make air compressors. A new video just came out a couple weeks ago showing the process for making an incredibly reliable and easy way of making an air bearing using JB weld, glass and a drill press. I will link the video below. I fully believe that would be a great high school project.
Corner horns are great. I am in the middle of building my home and I have room in my plans just for corner horn listening. Of course I am also working on a 3d printed field coil woofer to go in those horns as well : )
TJ,
Stop it man, my head is coming undone! 3D printing of a voice coil (former)? Wait a minute, I just reread the post but still, 3D printing is way beyond me, though fascinating for those with increased imaginations like us. Will you be using the Klipsch corner horn design, like I did in my project? I know there is a mountain of horns out there, and for bass, they are unforgettable when done right.
Yup, the glass tubes look to be of no consequence until you need more accuracy for a bearing to follow. I am still convinced that even replacing a section of the stiffer wire with something more flexible may sound better and yield a friendlier environment for the stylus.
Stop it man, my head is coming undone! 3D printing of a voice coil (former)? Wait a minute, I just reread the post but still, 3D printing is way beyond me, though fascinating for those with increased imaginations like us. Will you be using the Klipsch corner horn design, like I did in my project? I know there is a mountain of horns out there, and for bass, they are unforgettable when done right.
Yup, the glass tubes look to be of no consequence until you need more accuracy for a bearing to follow. I am still convinced that even replacing a section of the stiffer wire with something more flexible may sound better and yield a friendlier environment for the stylus.
Lol. If things go according to plan, it should be doable with hand tools. No 3d printing of a voice coil former or anything extreme like that. I literally just need a plastic piece to hold the center slug. I could probably do it now with super glue and a plastic plate, but meh.
I will probably be doing the math and making my own pattern. Corner horns need to be designed for the room afterall.
I will probably be doing the math and making my own pattern. Corner horns need to be designed for the room afterall.
Don't let the secret get out. Why don't you try and tackle the impossible with infinite DSP? But yes, making the bass horn conform to the actual needs of the room would be dandy. When you get further on this, I would like to see a thread started.
Sure. I mean designing something to fit the room is not all that hard. Some basic rules of thumb will get you pretty far.
The big advantage to field coils is that you can tweak the operating parameters of the driver through the power supply. So you kind of already have a dsp built into the system already if you think about it.
The big advantage to field coils is that you can tweak the operating parameters of the driver through the power supply. So you kind of already have a dsp built into the system already if you think about it.
Hi folks,
There were some majorly exciting builds going on last year. We haven't heard anything in quite a while.
I hope everyone is in good health and that the projects are going to plan.
Any updates?
There were some majorly exciting builds going on last year. We haven't heard anything in quite a while.
I hope everyone is in good health and that the projects are going to plan.
Any updates?
For me its been my line array speakers caused a diversion.
See my "another corner array" thread if interested!
Anyone who has no space for speakers in the room might look at this.
Winter will be around soon, so maybe some RTA work then!
But what of Warren and Sether?
See my "another corner array" thread if interested!
Anyone who has no space for speakers in the room might look at this.
Winter will be around soon, so maybe some RTA work then!
But what of Warren and Sether?
That is one heck of a turn table, incredible. The appearence reminds me of a 3D printer, maybe it would be possible to build a platter into a 3D printer. But you need a feedback solution as the cartridge has to move along with all the warps etc. of the record. Food for thought, curious about the end result!
@Horneydude the end result is sensational and has out performed a Goldmund Reference and TechDas AF3 Premium. 3 of these TT's have been built and this photo is of the first one which is mine. The reflex clamp eliminates all but the worst warps, and is as good as vacuum hold down with a lot less things to go wrong. The clamp can be removed and the LP is still stuck to the platter.
A friend of mine who owns the high end TT's loaned me a Kuzma 4point which was installed on this TT and the LTA was significantly better. It was an interesting exercise. The midrange bloom of the pivoting arm was immediately noticeable. The LTA had far more accurate rendering of notes. With the same cartridge on both arms I had to turn down the volume with the Kuzma to have the same perceived level the midrange was noticeably louder.
The carriage and rail design was originally developed by @niffy. This was never intended to be a commercial venture. Cost of making this TT is way too high
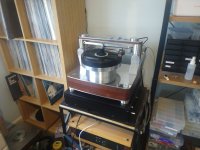
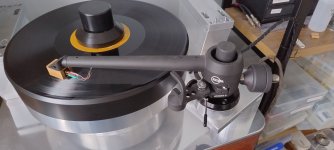
A friend of mine who owns the high end TT's loaned me a Kuzma 4point which was installed on this TT and the LTA was significantly better. It was an interesting exercise. The midrange bloom of the pivoting arm was immediately noticeable. The LTA had far more accurate rendering of notes. With the same cartridge on both arms I had to turn down the volume with the Kuzma to have the same perceived level the midrange was noticeably louder.
The carriage and rail design was originally developed by @niffy. This was never intended to be a commercial venture. Cost of making this TT is way too high
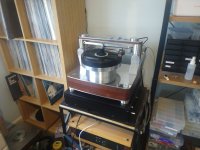
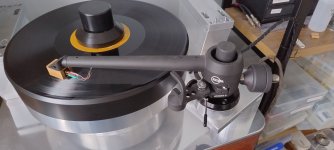
Your TT makes my outdated and unmodified Thorens 165 with an off-the-shelf Grado wood cartridge a very humble machine 😳 and I can only imagine how it would sound; I appreciate your high end effort though! Searching the boundaries of what is possible brings progress 🙂
I am writing via Google Translate.I'm still here. I've been building 2 more Franken SP10s now called the Arcadia. This one is for Kev who has done all the CNC machining. The cuing mechanism in the last pic is a pattern for Kev and the final mech will be much more pleasing visually.
View attachment 1460147View attachment 1460148View attachment 1460149
Greetings from Russia.
I am in awe of your work.
I have a question and would like to ask you to clarify.
How do you solve the problem of dust on the carriage guides? There is always dust in the air.
Hi Andre,
Welcome to the thread.
Warren's arm is based on my design so I feel that I can answer your question. In both of our designs there is a beam that runs above the rail on which the carriage run. The main function of this beam is to make the support structure, that holds the rail, as rigid as possible. It also helps to shield the rail from dust. Every so often I wipe the rail and the wheels of the carriage with a dry cotton bud. I only do this about once a month. I don't recall ever having the stylus skip due to a comtaminant on the rail. I have a dust cover that encloses the entire deck when it is not in use. I don't know what Warren has in the way of a dust cover.
I hope this answers your question.
Niffy
Welcome to the thread.
Warren's arm is based on my design so I feel that I can answer your question. In both of our designs there is a beam that runs above the rail on which the carriage run. The main function of this beam is to make the support structure, that holds the rail, as rigid as possible. It also helps to shield the rail from dust. Every so often I wipe the rail and the wheels of the carriage with a dry cotton bud. I only do this about once a month. I don't recall ever having the stylus skip due to a comtaminant on the rail. I have a dust cover that encloses the entire deck when it is not in use. I don't know what Warren has in the way of a dust cover.
I hope this answers your question.
Niffy
- Home
- Source & Line
- Analogue Source
- DIY linear tonearm