Christian.
are the speaker measurements you were talking about , the klippel system ?
I believe audio science review forum are now using this method to review and measure speakers.
Steve.
are the speaker measurements you were talking about , the klippel system ?
I believe audio science review forum are now using this method to review and measure speakers.
Steve.
hi eric.Some more details on my cf skinned balsa core panels.
Thickness: 2.1 mm
Elastic Modulus: 27 GPa
Density: 450 kg/m^3
Stiffness (D): 20 Nm
Areal Density (mu): 0.95 kg/m^2
D/mu^3: 23
Fc: 4100 Hz
Size: 584 mm x 406 mm
Of course, to call these panels the holy grail is a huge overstatement. However, they do meet my goal, which was to have a panel with a sound as good and clear as wood but with much higher efficiency. I find they do indeed sound as good as wood, and put out about 6 dB more (if I recall correctly) than plywood at the same volume setting on my amp.
Already, I have an idea for an improvement. I recently learned that my cf fabric supplier has an even thinner (by half) cf fabric than I used, for a reasonable price (normally, very thin cf fabric is very expensive). Using the thinner fabric instead, with the same balsa thickness, I should be able to produce a panel that has even higher efficiency. Or, by using the thinner fabric combined with thinner balsa, I could achieve similar efficiency, but sginificantly lower stiffness, permitting similarperformance at low frequency but with a smaller panel.
Attached pic is of my prototype panel, in a test frame, when I was testing the frequency response at various distances and angles.
Eric
View attachment 1020132
I see you have been having lots of fun.
did you use the tectonic 500 panel size as a template (clone) or was this just coincidence ?
Did you try other materials such as fine glass fibre mesh as in the tech ingredients video I posted ?
I just used the epoxy as my skin for my 5mm xps as I was not sure what grade of mesh to use ?
But they work very well..
My 5mm panels are far too large for this type of panel, thinner smaller more flexible panels tend to not need to be so large.
I halved the size of one of my 5mm panels and the performance was roughly the same.
The small corrugated panel also looses hardly anything when matched with the large 5mm panel, in some respects it is better.
have you posted any frequency plots ?
sorry if I must them.
Steve.
Is it just me or does predictive text change words around just for fun ?
I had a quick play around with the corrugated panel today and managed to change the response a little ,it was resisting my charms to alter it in more subtle ways so had to revert back to very small 2mm blob of blu-tack.
I didn't want to spend too much time in my room as the heating is not on out there and it's freezing.
But it's not bad for a first attempt.
The hf looks a lot better I hope ?
This plot was taken with the microphone at about 30cm as I did not want to move everything around again.
Steve.
I had a quick play around with the corrugated panel today and managed to change the response a little ,it was resisting my charms to alter it in more subtle ways so had to revert back to very small 2mm blob of blu-tack.
I didn't want to spend too much time in my room as the heating is not on out there and it's freezing.
But it's not bad for a first attempt.
The hf looks a lot better I hope ?
This plot was taken with the microphone at about 30cm as I did not want to move everything around again.
Steve.
Attachments
Hello
Hello Eric,
Luckily, the bait didn't taste bad! I would event take another one!
This thread is like a giant jigsaw puzzle... You got a post but don't know how to insert it in the picture, sometime you forgot it, sometime it doesn't fit in the picture, some posts shows much more than others.
Thank you for this introduction to your CF/balsa membrane DIY process. If I remember things I saw around double top guitar it is the process used in composite materials. Much much high tech than what I do currently.
Christian
Christian,
You took the bait, as I hoped you would! Of course I will be happy to share details about my holy grail. I have mentioned it before, I suspect, but perhaps not described it in much detail.
It is a carbon fiber skinned, basla core sandwich composite. The top and bottom cf skins are 190 g/m2 carbon fiber fabric with epoxy resin matrix. These densify to about 0.23 mm each. The core is 1.6 mm thick balsa, with a density of about 160 g/cm^3.
I make these panels myself in my workshop. I will share more details of the process if anyone truly would like to try it themselves. But the basic process goes like this:
1. Lay the first layer of cf fabric on a glass plate, saturate it with epoxy, and apply the balsa on top.
2. Apply "peel ply" and absorbant batting layers, then put it all in a vacuum bag.
3. Apply vacuum, then let the epoxy cure overnight.
4. Remove everything from the vacuum bag, remove the peel ply and batting.
5. Apply the second layer of cf fabric on top of the balsa face, and saturate it with epoxy.
6. Repeat steps 2-4.
7. Carefully peel the composite sandwich from the glass
Hello Eric,
Luckily, the bait didn't taste bad! I would event take another one!
This thread is like a giant jigsaw puzzle... You got a post but don't know how to insert it in the picture, sometime you forgot it, sometime it doesn't fit in the picture, some posts shows much more than others.
Thank you for this introduction to your CF/balsa membrane DIY process. If I remember things I saw around double top guitar it is the process used in composite materials. Much much high tech than what I do currently.
Christian
EricSome more details on my cf skinned balsa core panels.
Thickness: 2.1 mm
Elastic Modulus: 27 GPa
Density: 450 kg/m^3
Stiffness (D): 20 Nm
Areal Density (mu): 0.95 kg/m^2
D/mu^3: 23
Fc: 4100 Hz
Size: 584 mm x 406 mm
Of course, to call these panels the holy grail is a huge overstatement. However, they do meet my goal, which was to have a panel with a sound as good and clear as wood but with much higher efficiency. I find they do indeed sound as good as wood, and put out about 6 dB more (if I recall correctly) than plywood at the same volume setting on my amp.
Already, I have an idea for an improvement. I recently learned that my cf fabric supplier has an even thinner (by half) cf fabric than I used, for a reasonable price (normally, very thin cf fabric is very expensive). Using the thinner fabric instead, with the same balsa thickness, I should be able to produce a panel that has even higher efficiency. Or, by using the thinner fabric combined with thinner balsa, I could achieve similar efficiency, but sginificantly lower stiffness, permitting similarperformance at low frequency but with a smaller panel.
Attached pic is of my prototype panel, in a test frame, when I was testing the frequency response at various distances and angles.
Eric
View attachment 1020132
Very clean your test frame. Is the speaker on the right here as a reference?
Thank you for the data. I'll put them in the material graph.
The gain in weight compare to the plywood is important. I understand the gain in efficiency.
The stiffness is what I estimate for a 3mm plywood. Isn't it a bit high for the areal weight you got? Less stiffness will increase the coincidence frequency and lower the first resonance for a same surface.
Christian
Compression "in the thickness" was mentioned a long time ago somewhere (where?) with the commendation if I remember not to be more thick than a quarter wave at the highest frequency... which make sense... and disqualify all the thick membrane. To keep in mind as a potential cause.Christian,
I must admit, I don't have a clear model in my mind for the loss of level in HF. I have seen it in materials with both high and low coincidence frequency (PMMA and PS foam), but perhaps there are different causes in each case. I always had a feeling that it was worse with softer materials, due the the exciter compressing the material under the coil, instead of bending the plate, but possibly there is an effect of fc as well. I'll have to look for it in the future.
Eric
Christian
Steve,Christian.
If you go back to my posts on dml open baffle for pro use you will see on my reply 51 and 52 ,the response of a 6ft hardboard panel.
51, shows the hump in response above 10k and the slow dip up to the 10k point.
52, shows the corrections that I made using simple methods ( no damping methods or mass used)
in post 54 you see my 3ft ply panel ,which has AA batteries stuck to it's front surface.
and as it states ,I used the battery masses to fill in the dips in the 100hz to 300hz region. !
Even with some of my small panels , I could extend the frequency down to 100hz without the dips, but there is always a price to pay,regarding sound quality(in my opinion) but it is a matter of taste.
We must not get confused with the room suck outs and the panel cancellations as these two problems show up in the same area,
Once again looking at this picture from my gallery in NXT RUBBISH, you can see the small dip left after using the batteries, but when moving the microphone back 3m ,the room takes its toll,
https://www.audiocircle.com/index.php?action=gallery;area=browse;image=137096
Steve
Thank you for the adjustement of the "FR reading grid" : different causes candidate for the "100/300Hz hole". The room, the mode efficiency. This remind me how I found instructive to make outdoor measurements. What I thought being obviously room interactions came in fact from the panel itself!
Christian
I don't know if it is mentioned by Klippel. I found it from other sources. I will post later what I have on that. Before those papers on MMM I was on the standard model of measurement with a microphone in one fix position with a stand. When I understood it is possible to have it at hand, moving, it changes completely my view of measurements.Christian.
are the speaker measurements you were talking about , the klippel system ?
I believe audio science review forum are now using this method to review and measure speakers.
Steve.
Christian
Hello Steve.Is it just me or does predictive text change words around just for fun ?
I had a quick play around with the corrugated panel today and managed to change the response a little ,it was resisting my charms to alter it in more subtle ways so had to revert back to very small 2mm blob of blu-tack.
I didn't want to spend too much time in my room as the heating is not on out there and it's freezing.
But it's not bad for a first attempt.
The hf looks a lot better I hope ?
This plot was taken with the microphone at about 30cm as I did not want to move everything around again.
Steve.
Yes more "quiet". Let us know your listening impression. If I remember, additional mass gives nicer FR but not necessary a much better sound. I have always difficulties with added mass. For me mass is synonym of delay, resonance while working with spring.
Anyway, it proofs again the role of the central area in HF.
Christian
I did finally get a couple good units - Parts Express was very good about it (poor manufacturer packaging). The warping of the panel when I cut it down to 3/8" did present some problems with voice coil location. I haven't built a stretched canvas unit yet - would this be a good candidate for a spiderless driver? I like its sound - better low end extension and estimated 3 db efficiency gain (they look about the same on the graphs, but the Thruster is 4 ohms, while the Tectonics is 8). I haven't built the other one, as improvements are needed. Some isolation between the panel and arms that support the exciter is needed, but my concern with that is sag of the driver, causing voice coil misalignment - so I think a frame around the panel is needed.Bdjohns.
sorry to hear of all those damaged BMR units, hope you managed to get a unit in one piece ?
many years ago over on NXT RUBBISH , I did mention that it would be a good idea to get rid of the spider ,mainly because of the noise it was making.
I could have done this with my rigid ply panels, but the warping of the ply panel prevented this.
My free floating panels need a spider , maybe we need a better designed spider similar to some older designs of the past ?
How does the sound compare to a standard exciter ?
Steve.
Could it be this Yamaha unit? I have been wanting to cut a panel to this shape.I don't know why but I always presumed that bertagni speakers would not use a spider ?
But I've never seen one without the cone.
I'm sure I've seen a polystyrene speaker without a spider , but I can't remember the model ?
Steve.
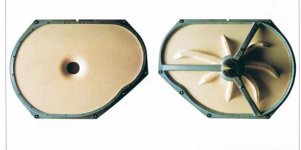
Steve,I see you have been having lots of fun.
did you use the tectonic 500 panel size as a template (clone) or was this just coincidence ?
Did you try other materials such as fine glass fibre mesh as in the tech ingredients video I posted ?
I just used the epoxy as my skin for my 5mm xps as I was not sure what grade of mesh to use ?
have you posted any frequency plots ?
Yes, lot's of fun indeed! I actually really do enjoy making carbon (and fiberglass) stuff.
Yes, the Tectonic panel was my model. It's been my default size for panels for some time, I have quite a collection of panels and frames in that size! Funny thing is that I built the frames for these panels almost a year ago, and finished the panels in April. Then due to the pandemic my daughter and her fiance came to stay with us, and my project lost momentum. So the speakers remain unassembled. Meanwhile, I'm becoming intrigued with panels of higher aspect ratio. So whether or not these speakers will ever come together remains to be seen....
I have, however, made a temporary assembly of a prototype panel, and made a series of measurements. I'll post some soon.
I did try fiberglass skins on balsa too. It works well too, and much cheaper. As fiberglass/epoxy (and CF/epoxy) are kind of heavy, I believe that the optimum construction for panels is usually with very thin composite skins. In that respect, fiberglass is actually better, as it is cheaply available in very thin fabrics. For carbon fiber, on the other hand, you pay a big premium for thin fabric.
Here's one of the fabrics I like:
https://compositeenvisions.com/prod...=2-1oz-71gsm&really_curr_tax=1411-product_cat
Eric
Christian,The gain in weight compare to the plywood is important. I understand the gain in efficiency.
The stiffness is what I estimate for a 3mm plywood. Isn't it a bit high for the areal weight you got?
I'm not sure what you mean by the "gain in weight compared to plywood". The density of wood is typically around 550 kg/m3 (or more), while these panels are 450 kg/m3. On an areal basis they are 0.95 kg/m2, while 3 mm plywood would be about 1.6 kg/m2. So I don't understand what you mean by the gain in weight.
The stiffness is indeed high for the areal density. That's what CF skins do!
Eric
Bdjohns.
when you mentioned a spiderless canvas panel , I suddenly thought ,why didn't I think of that !
But then thinking about it , looking at your coil former ,I started to think, what if there was some canvas wobble going on .
There is nothing keeping the coil centrally in the grooves, you could get some rubbing and buzzing ?
I'm not saying it isn't possible but it's something to think about.
or make a minimalist spider that makes very little noise.
Steve.
when you mentioned a spiderless canvas panel , I suddenly thought ,why didn't I think of that !
But then thinking about it , looking at your coil former ,I started to think, what if there was some canvas wobble going on .
There is nothing keeping the coil centrally in the grooves, you could get some rubbing and buzzing ?
I'm not saying it isn't possible but it's something to think about.
or make a minimalist spider that makes very little noise.
Steve.
Steve,have you posted any frequency plots ?
Here's the response of the cf/balsa, at 1 meter on axis. This is in a frame with with foam around most of the perimeter (not the corners) and a Dayton DAEX25FHE-4 exciter at about the .45/.45 location. Frankly it's pretty similar in overall character to my plywood panel of the same dimensions, but 6 dB louder.
Eric
Attachments
Eric,Steve,
Yes, lot's of fun indeed! I actually really do enjoy making carbon (and fiberglass) stuff.
Yes, the Tectonic panel was my model. It's been my default size for panels for some time, I have quite a collection of panels and frames in that size! Funny thing is that I built the frames for these panels almost a year ago, and finished the panels in April. Then due to the pandemic my daughter and her fiance came to stay with us, and my project lost momentum. So the speakers remain unassembled. Meanwhile, I'm becoming intrigued with panels of higher aspect ratio. So whether or not these speakers will ever come together remains to be seen....
I have, however, made a temporary assembly of a prototype panel, and made a series of measurements. I'll post some soon.
I did try fiberglass skins on balsa too. It works well too, and much cheaper. As fiberglass/epoxy (and CF/epoxy) are kind of heavy, I believe that the optimum construction for panels is usually with very thin composite skins. In that respect, fiberglass is actually better, as it is cheaply available in very thin fabrics. For carbon fiber, on the other hand, you pay a big premium for thin fabric.
Here's one of the fabrics I like:
https://compositeenvisions.com/prod...=2-1oz-71gsm&really_curr_tax=1411-product_cat
Eric
2 questions (or at least open points in my mind... answers might be difficult...) :
- About the panel ratio : designs derivated from NXT's work seem have a ratio of 1:1.something (a "short rectangle, here your panel ration is 1:1.438); the DIY panels like the tall blondes are 1:4. Is there here a discrepancy? An other possibility is that a professional design think the balance performance/cost in another looking for solutions with a minimum of material...
- About the choice of the material in a composite design like yours, is there a possibility to predict the final ending stiffness? In other words : we have ideas of the target for the bending stiffness and the areal mass; there are many choices possible in material (CF, glass mat, EPS core, balsa core...) their thickness. Is there a possibility to limit the trial and error process
Eric,Christian,
I'm not sure what you mean by the "gain in weight compared to plywood". The density of wood is typically around 550 kg/m3 (or more), while these panels are 450 kg/m3. On an areal basis they are 0.95 kg/m2, while 3 mm plywood would be about 1.6 kg/m2. So I don't understand what you mean by the gain in weight.
The stiffness is indeed high for the areal density. That's what CF skins do!
Eric
Sorry not being clear enough (not adapted vocabulary?). I wanted to highlight exactly what you mention : there is a huge decrease in density in your panel compare to plywood.
Christian
Only emphasis on the frequency response?
A lot of work is being done on this for TV speakers. Some of the newer OLED sets are not bad at all. Not high fidelity by any means, but useable as a TV. More work is being done with DSP to use multiple drivers and synthesize a wider stereo image. A recent paper was about ultra thin back loading to improve bass response.
A lot of work is being done on this for TV speakers. Some of the newer OLED sets are not bad at all. Not high fidelity by any means, but useable as a TV. More work is being done with DSP to use multiple drivers and synthesize a wider stereo image. A recent paper was about ultra thin back loading to improve bass response.
- Home
- Loudspeakers
- Full Range
- A Study of DMLs as a Full Range Speaker