Is there an intent to eventually design a 3d printed model where the drivers bolt right up? It could be sliced into sections in the software so that it could be printed in small desktop printers and then bolted together. Ive never used a 3d printer, or designed for one so I'm not aware of the limitations but that would be so damn cool! You might even achieve a good WAF that way.
I'm surprised there isn't more badass audio related 3d printery going on. Glad to see some of that happening here.
Yes this is very possible I think.
I will try pursue this.
Baffle board completed
I hate cutting plywood. 3/4in ply is used for the baffle board 11.125 wide x 18.25 high. I just could not make the the 17in high goal however below 19in still qualifies as a "book". 🙂
I hate cutting plywood. 3/4in ply is used for the baffle board 11.125 wide x 18.25 high. I just could not make the the 17in high goal however below 19in still qualifies as a "book". 🙂
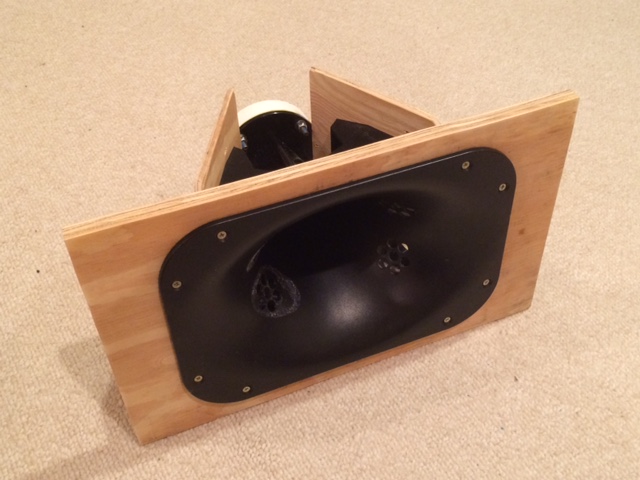
Attachments
Last edited:
I'm a professional woodworker (full time job) as a result, its not much fun as a hobby anymore. If I ever change careers then its game on for hobby creations. However, I've learned a thing for two that can help you guys.
If you can do cad drawings, there are lots of woodshops that use CNC machines. They might charge you $100 an hour plus material to run that machine, but it works out to be pretty cheep. The shop where I work doesn't have one so we sub out to another shop for CNC. We buy material from our supplier and have it shipped to them for cutting. The wholesale material destributers can probably point you in the right direction as far as suggesting a shop that might be willing to work with you.
You don't even need a CAD drawings really, if you can just sketch the parts on paper with all the necessary dimensions, they can input that into their software pretty easily. It will just cost a little extra for their time. Too much information is better than not enough, fabricators are fast and efficient as long as we know what you want. Think in terms of parts, don't go on telling the shop about when you are building, they don't care just draw the parts and talk about the parts themselves.
As far as cutting plywood, I hate it too unless it's at work with proper dust collection, MDF is even worse. I'm sure everyone here already knows about the Jasper circle jig for doing recessed driver mounting, they sell it at parts express. That's a must have tool.
If you can afford it, the festool track saw makes cutting plywood pretty painless and almost dust free, I use it for modifications on site when I'm installing. Make sure you get the clamps the attach to the under side of the track, its necessary for cutting smaller parts. That's about a $1500 investment for the whole rig so you might as well just pay a shop to make your parts.
If you can do cad drawings, there are lots of woodshops that use CNC machines. They might charge you $100 an hour plus material to run that machine, but it works out to be pretty cheep. The shop where I work doesn't have one so we sub out to another shop for CNC. We buy material from our supplier and have it shipped to them for cutting. The wholesale material destributers can probably point you in the right direction as far as suggesting a shop that might be willing to work with you.
You don't even need a CAD drawings really, if you can just sketch the parts on paper with all the necessary dimensions, they can input that into their software pretty easily. It will just cost a little extra for their time. Too much information is better than not enough, fabricators are fast and efficient as long as we know what you want. Think in terms of parts, don't go on telling the shop about when you are building, they don't care just draw the parts and talk about the parts themselves.
As far as cutting plywood, I hate it too unless it's at work with proper dust collection, MDF is even worse. I'm sure everyone here already knows about the Jasper circle jig for doing recessed driver mounting, they sell it at parts express. That's a must have tool.
If you can afford it, the festool track saw makes cutting plywood pretty painless and almost dust free, I use it for modifications on site when I'm installing. Make sure you get the clamps the attach to the under side of the track, its necessary for cutting smaller parts. That's about a $1500 investment for the whole rig so you might as well just pay a shop to make your parts.
I use a hand held jig saw and have no proper work room - it's done in a carpeted room in the basement. I work on the floor as no work benches are available. Plywood dust gets on everything. That's the main reason I work with foam core - no shop is needed as a razor, ruler, hot melt glue gun, and carpeted floor are all that is needed.
Thanks for the tip on CNC - I would do that except for the need to do this experimentally as I am developing the physical fit and layout of the design as I go in real time. If I slow down and think up of the design all on paper first and CAD it all up first - I could send it out. I do use CAD for much of the things I do as I print in 3d where possible. That may be the case for all future wood builds as I just can't have the mess this creates anymore.
Thanks for the tip on CNC - I would do that except for the need to do this experimentally as I am developing the physical fit and layout of the design as I go in real time. If I slow down and think up of the design all on paper first and CAD it all up first - I could send it out. I do use CAD for much of the things I do as I print in 3d where possible. That may be the case for all future wood builds as I just can't have the mess this creates anymore.
Last edited:
Get some cheap saw horses from Home Depot and go outside. It's been a very mild winter. I'm building a boat pilot house outside.
Mild here until the snow storm of the century came a few weeks ago here in the DC area. We had 4 ft tall snow drifts that just finally started to melt off. I also only am able to work late at night and sawing outside with power tools when people are sleeping is a no no.
Last edited:
More progress, baffle painted and binding posts installed. Once paint dries, install baffle to box, horn reinstall, add fiberglass, work on bracing driver boards to box. Lot's of little steps still need to be done so may be a while still before complete.
I think Byrtt's idea to go for the ATC aesthetic looks good!
I think Byrtt's idea to go for the ATC aesthetic looks good!
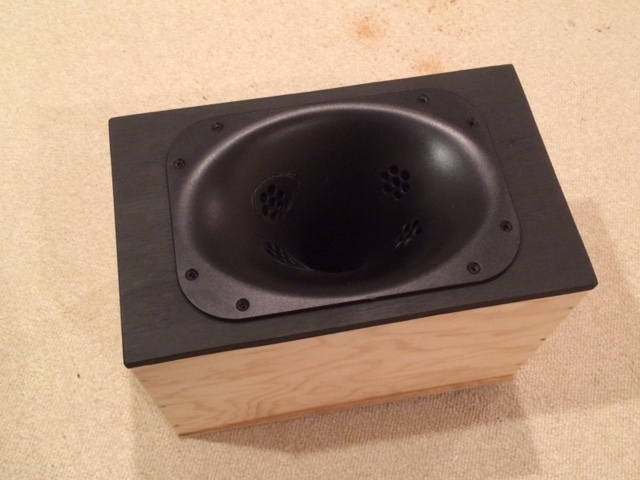
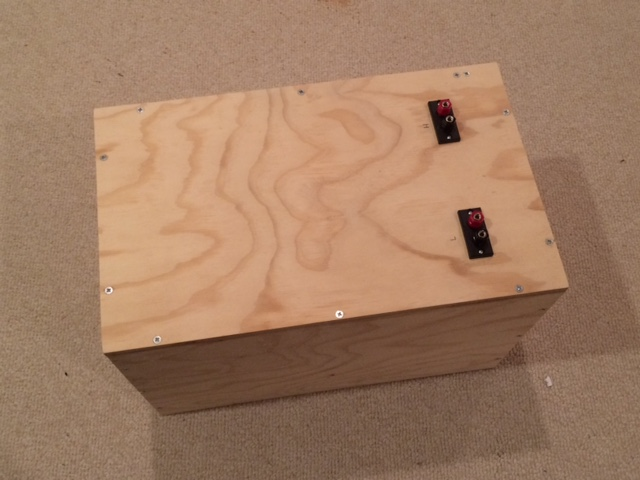
Attachments
Like it very much too and if it ends perform as headphones in a room as Patrick Bateman explained about experience with SH50 it has a good look.
Fingers crossed starfish also will like its new nice home.
Fingers crossed starfish also will like its new nice home.
I had a setback with the starfish. It turns out the real 3d scan is so complex that I could not convert to a solid body to manipulate. You can print it as is but not manipulate. So I have to make my own starfish from scratch.
The box volume is about 30 liters and I wonder how the bass response is going to be. In any event, the bass extension and Q an always be modified with a LT.
I don't have sorbothane and fear some cabinet vibrations are going to get the better of me on this build.
I am not sure if I will ever get the headphone effect as I don't have it in me to make a stereo pair. Just too much work to make the box.
The box volume is about 30 liters and I wonder how the bass response is going to be. In any event, the bass extension and Q an always be modified with a LT.
I don't have sorbothane and fear some cabinet vibrations are going to get the better of me on this build.
I am not sure if I will ever get the headphone effect as I don't have it in me to make a stereo pair. Just too much work to make the box.
i guess i missed it. what is the "starfish" all about?
4 foot snow banks that's a mild winter where i'm from.
4 foot snow banks that's a mild winter where i'm from.
I am not sure if I will ever get the headphone effect as I don't have it in me to make a stereo pair. Just too much work to make the box.
Wait and judge the finished speaker. You've done it once now and will know if it's worth it to do it once more! 😉
Sorry to hear about the starfish, nothing a few lofts and splines can't cure when you make your own...
i guess i missed it. what is the "starfish" all about?
4 foot snow banks that's a mild winter where i'm from.
That's the rear chamber for the SB65 - I was going to make it based on the shape of a starfish to get 5 sealed tapered TL's to absorb the back wave radially vs straight back to keep the profile very flat.
Fit check before final install
I think it looks very good - a serious "monitor" look about it.
18.25in high x 11.0625in wide x 13.125in deep
I think it looks very good - a serious "monitor" look about it.
18.25in high x 11.0625in wide x 13.125in deep

Attachments
Last edited:
- Home
- Loudspeakers
- Multi-Way
- A Bookshelf Multi-Way Point-Source Horn