Not exactly bookshelf size speakers anymore.........although still excellent work as what may be the smallest Synergy type system to date.
Well I contend that if mine comes in at 17in high it technically qualifies as a bookshelf speaker. I think 19in tall X 12in wide books covers ("folio" size) are the largest accepted "books" in a standard library shelf as defined by the American Library Association.
There is a 12in wide cover limit so that means the depth of the speaker can not exceed 12in. That may present some challenges and require more work on making the rear chamber even thinner.
But I did buy myself 2in of height for reserve now when using the American Library Association max limit for a folio book.
Last edited:
On another note, just found that 1/8" felt lining portions of the interior walls on the TC9/Maltese horn made a very large reduction in HF ripple- from +/-4 dB, to near that of a compression driver, around +/- 1dB, with only about one dB loss of sensitivity. Also made polar response more uniform.
Unfortunately, the "very large reduction in HF ripple" must have been an interpretation error (probably comparing two different measurement angles) after spending this morning trying damping felt in various places in the horns, I could not replicate the "last test of the day" results from yesterday.
The sensitivity loss turned out to be too much for the very minor improvement in polar response in some frequency ranges, and the polar response was worse in others, and overall no smoother.
Although the quad array of narrow dispersion Maltese horns using TC9s will work well for my intended use (center fill for high SPL live sound reinforcement) the polar response is not nearly as good as a single horn of similar dispersion pattern.
The tape and cardboard TC9FD-18-08 45 x 30 conical horn prototype whipped up in about 20 minutes just before last Christmas had really good polars, and a only a few easy to correct "bumps", raw response below.
Note that only about 6 dB of EQ correction would be required to flatten response from 250 to 16kHz.
Though the initial conical horn flare is 45 degrees, actual horizontal coverage is 60 degrees (-6dB 30 degrees off axis) with uniform constant directivity pattern control to 650 Hz.
It would be easy to build from plywood (or foam core), and much easier to mount woofers on than elliptically shaped horns.
Art
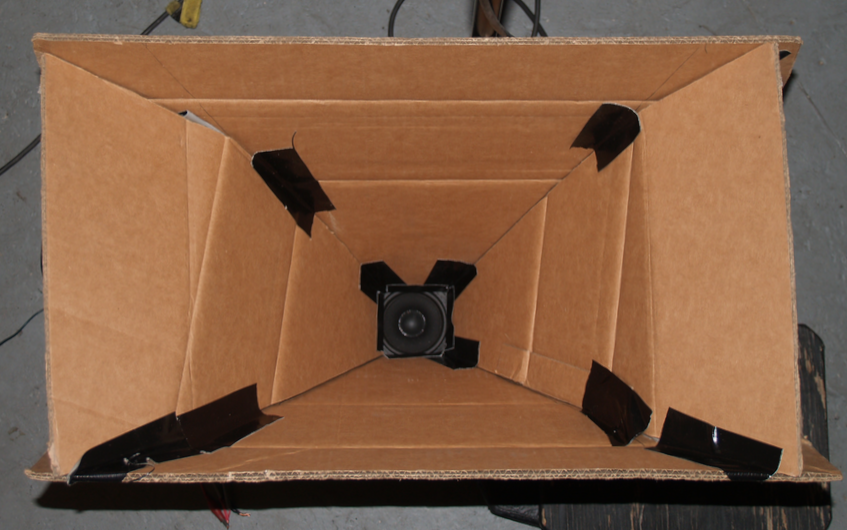
Weltersys,
That's a nice cardboard horn. I actually have tons of the same type of triple wall cardboard from moving company boxes. What size is that TC9 horn and can you share dimensions? Is it as simple as going into Bwaslo's spreadsheet and plugging in 45x30 and 3in throat? Did you have a problem with horn wall vibrations? I noticed with foam core horns is that when not CLD'd and unbraced - they vibrate as a secondary resonator sound board and sometimes give a better looking polar and deeper bass extension than a stiffer material. Once you add a second layer of cardboard glued on with a thick layer of latex caulking, the bass extension goes higher, the polar directivity narrower, and it is peakier. But the HD hoes way down. It may just be broadband noise rather than true HD though.
Last edited:
At the low level of SPL of the testing, horn wall vibrations were not a problem, though I would not use cardboard for anything but a prototype.![]()
Weltersys,
That's a nice cardboard horn. I actually have tons of the same type of triple wall cardboard from moving company boxes. What size is that TC9 horn and can you share dimensions? Is it as simple as going into Bwaslo's spreadsheet and plugging in 45x30 and 3in throat? Did you have a problem with horn wall vibrations?
The dispersion pattern was chosen because toed in it is adequate to completely cover my couch at 12', and because the TC9 native dispersion pattern is only about 45 degrees at 12.5kHz, a wider angle horn would not have wider HF dispersion. 30 x 45 also loads to a lower frequency than a wider horn, while the "beaming" response of the 3.5" driver (partially) compensates for the HF drop inherent in a constant directivity horn. Low mid gain is 6-10 dB compared to the response of the driver, tapering off to the same HF sensitivity.
The throat is probably close to 2 5/8" x 2 5/8", with a 3" 3/16" deep ring around to keep the surround from hitting the throat.
Mouth width was approximately 32". Bwaslo's calculator would be an easy way to duplicate the horn, though this prototype did not use a secondary section on the top and bottom sections, they are single walls. The size could be scaled down to "bookshelf size", polars response would remain the roughly the same, but pattern control would be lost at a higher frequency.
Art
"Starfish" rear chamber for SB65 with natural organic curves:
![]()
So what are the plans for the rest of the enclosure, an Octopus? 😀
"Starfish" rear chamber for SB65 with natural organic curves:
![]()
Dear lord.....
So what are the plans for the rest of the enclosure, an Octopus? 😀
Close, a chambered Nautilus. 🙂
"Starfish" rear chamber for SB65 with natural organic curves:
![]()
Wooow !!!!
X that startfish is a awesome work.
You are a real 3D artist.
I leave my hat for you master.
Enviado desde mi MX4 Pro mediante Tapatalk
I can't take credit for starfish as that was a 3d scan of a real animal that is freely available on 3d print libraries online.
Well I figured it looked mighty real... that explains it. How does it look when viewed from the other side (the inside where the driver mounts)?
There are two versions one with realistic underside and one with flattened underside (still has some curves and deep channels). I am using the flattened one.
https://www.youmagine.com/designs/starfish-360-degree-model
https://www.youmagine.com/designs/starfish-360-degree-model
Last edited:
Do you open it all up towards the driver? The picture looks like a tunnel into the Starfish. I assume you open up the driver entrance as soon as possible into the star shape? You know, the usual chamfer on the baffle thing 😉.
Have not got that far yet - I may put a reverse cone deflector at the top but one thing I may try is to print it as a solid filled with 3D printed "stuffing" as the support structure for the printing. The manually remove the printed atuffing around the driver with pliers.
All 4 Band Pass Holes Polars
To my surprise, adding the second set of band pass injection holes for the second woofer actually improved the response relative to having only 2 holes. Each "hole" being the seven smaller hole arrays. Here you can see that compared to the earlier case with only two, the response (magenta curve) improved by 3.5dB at 9kHz, and smoothed out a little more over a range. It is even more sensitive at 9kHz than the taped over (pristine case) - which is puzzling. Overall, the pristine horn is smoother though.
Here are the polars with all holes out to 45 deg:
So it appears that the strategy to go with the array of 7 smaller holes worked out well as it minimally affects the polar response. I can now go back and re-EQ the response for flat at either 10deg or as some have proposed, at 30deg.
To my surprise, adding the second set of band pass injection holes for the second woofer actually improved the response relative to having only 2 holes. Each "hole" being the seven smaller hole arrays. Here you can see that compared to the earlier case with only two, the response (magenta curve) improved by 3.5dB at 9kHz, and smoothed out a little more over a range. It is even more sensitive at 9kHz than the taped over (pristine case) - which is puzzling. Overall, the pristine horn is smoother though.
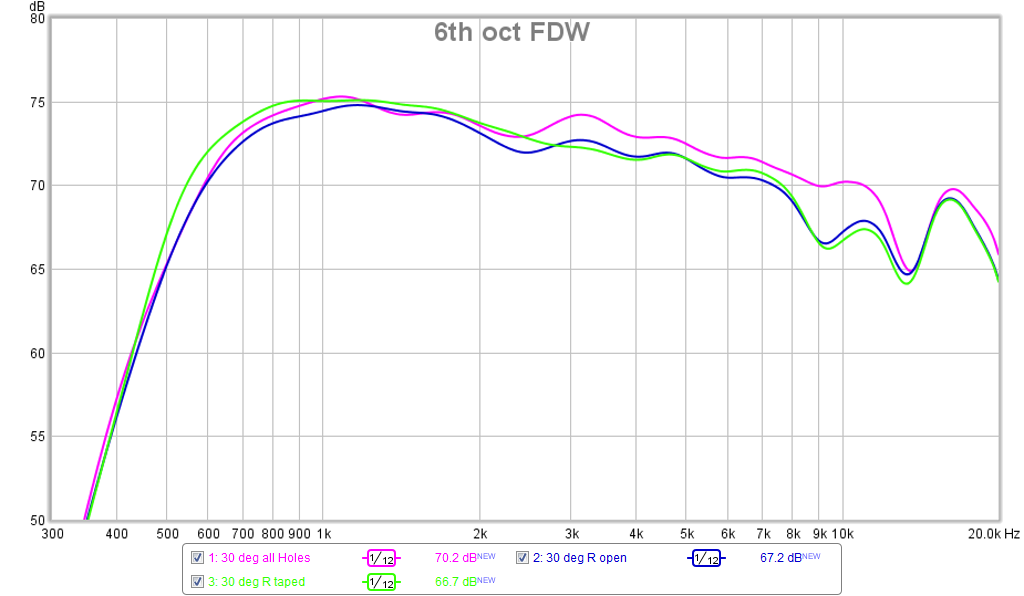
Here are the polars with all holes out to 45 deg:
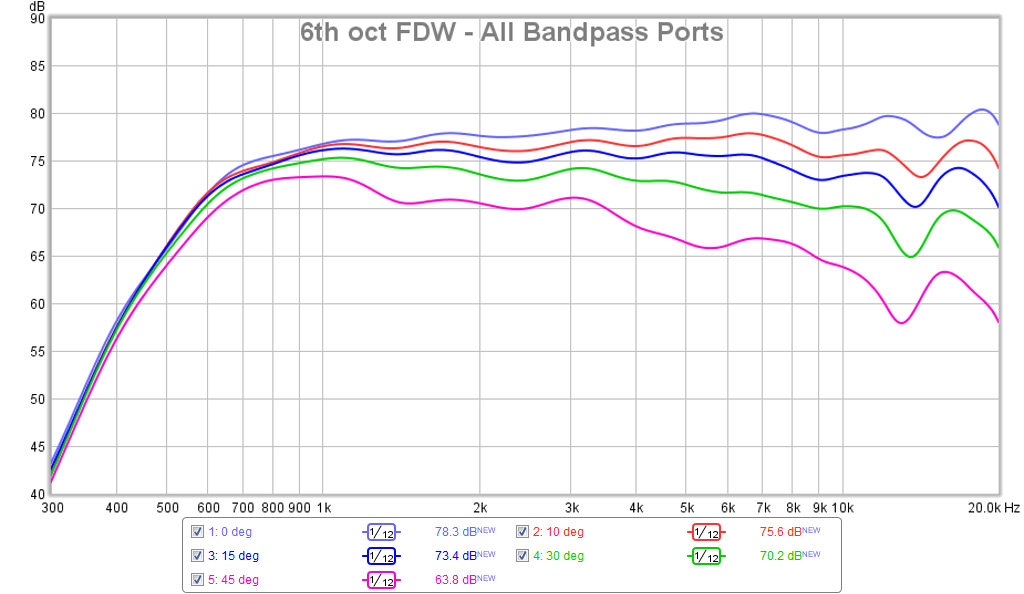
So it appears that the strategy to go with the array of 7 smaller holes worked out well as it minimally affects the polar response. I can now go back and re-EQ the response for flat at either 10deg or as some have proposed, at 30deg.
Attachments
Great work X - I love that starfish! So much more glamorous than an old Tupperware bowl!!!!
Can't wait to see how yours turn out. I am just finishing up the stereo pair. Also I am thinking about how I can make them more aesthetically pleasing - obviously the red spray job is just a temporary fix.
Ultimately, I think I may build them into a full front wall unit - with TV, storage, books etc. Will depend on how they sound in stereo.
Can't wait to see how yours turn out. I am just finishing up the stereo pair. Also I am thinking about how I can make them more aesthetically pleasing - obviously the red spray job is just a temporary fix.
Ultimately, I think I may build them into a full front wall unit - with TV, storage, books etc. Will depend on how they sound in stereo.
bushmeister, I'd still make them into floor standers if it were up to me.
I'd use an array of woofers down to floor level below the horn to give them more oomph and headroom down low. The extension down to the floor for obvious reasons...
But it has to fit the room too I guess. I liked the ideas of Onni, you can give them a classic look with modern internals that way. The round and/or curved shapes can be made with translam construction. Not that hard to make something pretty i.m.h.o.
I'd use an array of woofers down to floor level below the horn to give them more oomph and headroom down low. The extension down to the floor for obvious reasons...
But it has to fit the room too I guess. I liked the ideas of Onni, you can give them a classic look with modern internals that way. The round and/or curved shapes can be made with translam construction. Not that hard to make something pretty i.m.h.o.
Is there an intent to eventually design a 3d printed model where the drivers bolt right up? It could be sliced into sections in the software so that it could be printed in small desktop printers and then bolted together. Ive never used a 3d printer, or designed for one so I'm not aware of the limitations but that would be so damn cool! You might even achieve a good WAF that way.
I'm surprised there isn't more badass audio related 3d printery going on. Glad to see some of that happening here.
I'm surprised there isn't more badass audio related 3d printery going on. Glad to see some of that happening here.
Thanks Bushmeister. The starfish was a bit of whimsy and only reason I thought of making it was that for a 3d printer, it doesn't matter how complex the part is - it prints almost as easily and I really needed a way to get the profile thinner to get the whole "bookshelf" aesthetic of the thread title. I haven't given up yet. Plywood cabinet building is not my strength so here is where it gets hard and slows down. I have thought about making the whole thing as a sectioned 3d print and either bolting together or better yet - glue it together. Hot melt glue is actually an excellent way to bond smaller pieces together as it partially melts the PLA plastic on the process of bonding it for and solid connection. It would be pretty expensive material wise to print the main waveguide that I am still think using a COTS one and adapting it is still the way to go. Also, as more builds in this thread progress with other waveguides, we will see which ones work well. However, my suspicion is that they will all work and that it's not that sensitive to the waveguide as long as you use a driver that is well matched and allows smooth operation. The drilling of the band pass injection holes won't affect the polar response too much of done judiciously and around the corners for the rectangular WG's. Can't wait to see others start connecting their 3.5in drivers to the larger 2in throat horns.
There were a couple of other 3d printing audio threads. One was a synergy by cookiemonster and I think he was printing the main CD throat and band pass injection part and then planning to couple to a traditional wooden conical horn. I don't know if that ever made it past small prototypes of the core print.
Onni also had a tweeter waveguide 3d printing thread too.
I think 3d printing will revolutionize how we DIY waveguides. Especially small shallow dome tweeter ones that can be made in a few hours. We can add a lot of interesting concepts like acoustic lending etc like Patrick Bateman is doing a la SAW / B&O.
There were a couple of other 3d printing audio threads. One was a synergy by cookiemonster and I think he was printing the main CD throat and band pass injection part and then planning to couple to a traditional wooden conical horn. I don't know if that ever made it past small prototypes of the core print.
Onni also had a tweeter waveguide 3d printing thread too.
I think 3d printing will revolutionize how we DIY waveguides. Especially small shallow dome tweeter ones that can be made in a few hours. We can add a lot of interesting concepts like acoustic lending etc like Patrick Bateman is doing a la SAW / B&O.
Last edited:
- Home
- Loudspeakers
- Multi-Way
- A Bookshelf Multi-Way Point-Source Horn