DNic,
I have also used Corian as the top plate of my Lenco L78 restoration. The bottom part is birch ply. Corian is a great material, easy to machine with very nice acoustic properties.
I have a Mylar tape roll, so I do not have to buy ready-made belts. I can prepare Mylar belts of the appropriate length. The same with polyester thread belts.
Cheers,
Panos
I have also used Corian as the top plate of my Lenco L78 restoration. The bottom part is birch ply. Corian is a great material, easy to machine with very nice acoustic properties.
I have a Mylar tape roll, so I do not have to buy ready-made belts. I can prepare Mylar belts of the appropriate length. The same with polyester thread belts.
Cheers,
Panos
Attachments
My best stretchiness of belt experimentation has hit a couple of snags.
The glues that I have are all completely incapable of gluing silicone rubber, even the one that says it is. The best looking glue option is going to cost around $35+postage which is more than I want to spend on this experiment. The only cheap option seems to be a glue designed for repairing silicone rubber sex dolls. A, I doubt it will be effective and B, I shudder to think what type of spam I will get in my inbox if I ordered it.
The polyurethane belt is nice and easy to join, just melt the ends together. It is however very stiff and I doubt that it will run smoothly around the pulley and idlers. I'll have a go at making some belts anyway just to check but I don't hold out much hope. Unfortunately the size I have seems to be the smaller diameter available so I can't get around the flexibility problem by using a thinner belt.
Niffy
The glues that I have are all completely incapable of gluing silicone rubber, even the one that says it is. The best looking glue option is going to cost around $35+postage which is more than I want to spend on this experiment. The only cheap option seems to be a glue designed for repairing silicone rubber sex dolls. A, I doubt it will be effective and B, I shudder to think what type of spam I will get in my inbox if I ordered it.
The polyurethane belt is nice and easy to join, just melt the ends together. It is however very stiff and I doubt that it will run smoothly around the pulley and idlers. I'll have a go at making some belts anyway just to check but I don't hold out much hope. Unfortunately the size I have seems to be the smaller diameter available so I can't get around the flexibility problem by using a thinner belt.
Niffy
Hello Niffy,
taking into account the bonding (gluing, melting, etc.) of the two ends of the belt, which are all very reasonable (i.e. expected), I would highly recommend that you tried the polyester thread as belt material. The knot is very easy to make (see the video) and it has absolutely no effect in the running of the belt, due to the fact that it's so small (hardly visible with the naked eye).
I have personally tried it with success, creating 4-5 belts of varying length. The result is excellent and it's very flexible to make as many polyester belts as one wants.
How To Make Well Tempered Labs Turntable Belts - YouTubeYouTubehttps://www.youtube.com › watch
Cheers,
Panos
taking into account the bonding (gluing, melting, etc.) of the two ends of the belt, which are all very reasonable (i.e. expected), I would highly recommend that you tried the polyester thread as belt material. The knot is very easy to make (see the video) and it has absolutely no effect in the running of the belt, due to the fact that it's so small (hardly visible with the naked eye).
I have personally tried it with success, creating 4-5 belts of varying length. The result is excellent and it's very flexible to make as many polyester belts as one wants.
How To Make Well Tempered Labs Turntable Belts - YouTubeYouTubehttps://www.youtube.com › watch
Cheers,
Panos
With this type of belt, It pays to make a belt it pays to make the belt 3 or 4 layers hooped together. Takes a bit of practice, but gives a better driving force & helps to bury the knot.
Cheers
Cheers
DNic,
according to my experience, the knot is so small, that it does not have any effect on the movement of the belt and consequently has no audible effect either. On the other hand, gluing / melting belt ends made of other materials has a much more audible effect (even visible effect when looking at how the belt turns) .
My two cents...
according to my experience, the knot is so small, that it does not have any effect on the movement of the belt and consequently has no audible effect either. On the other hand, gluing / melting belt ends made of other materials has a much more audible effect (even visible effect when looking at how the belt turns) .
My two cents...
However one strand does not have enough surface contact area. When I tried one strand I could see my stand alone pulley move as the knot pasted over it. Than must disrupt the performance. That is why I went for Mylar.
Cheers
Cheers
Hi DNic,
although the polyester thread seems to be extremely thin, its grip is surprising, even without too much belt tension.
Perhaps you may have to give an initial spin to the platter to avoid slipping in the beginning, but once up to speed, the rotation is remarkable. Very stable and extremely quiet.
That's my experience, and I have been amazed, too, by the polyester thread, to be honest.
Cheers,
Panos
although the polyester thread seems to be extremely thin, its grip is surprising, even without too much belt tension.
Perhaps you may have to give an initial spin to the platter to avoid slipping in the beginning, but once up to speed, the rotation is remarkable. Very stable and extremely quiet.
That's my experience, and I have been amazed, too, by the polyester thread, to be honest.
Cheers,
Panos
Hey Panos,
I'm very sorry for your troubles.
Had your new DC motor been from LINN, ORIGIN LIVE, MICHELL or another manufacturer, I suspect you would have sent it back long ago.
Given that it is a premium MAXON motor - with a premium price tag - I think you have every right to return it with questions around its performance.
Let's hope they can sort it out for you - quick smart!
I'm very sorry for your troubles.
Had your new DC motor been from LINN, ORIGIN LIVE, MICHELL or another manufacturer, I suspect you would have sent it back long ago.
Given that it is a premium MAXON motor - with a premium price tag - I think you have every right to return it with questions around its performance.
Let's hope they can sort it out for you - quick smart!
Hi, Just though I would share my 12 VDC motor & controller results, to show you what can be achieved. Running a Mylar bely around the platter perimeter.
Donor deck was a Lenco 78 & these results are better than when that desk was new. Slight overspeed is to allow for stylus load slow down when running.
Cheers
Cheers
Donor deck was a Lenco 78 & these results are better than when that desk was new. Slight overspeed is to allow for stylus load slow down when running.
Cheers
Cheers
Attachments
Hi Panos,
Good luck with getting your motor sorted. As you've already experienced the Maxon Re-Max motors have huge potential. Hopefully you can unleash even more of this potential.
My experiments with drive belts is continuing slowly.
Unfortunately I'm going to have to give up on silicone as an option. The only product that I've found that can bond the ends satisfactorily seems to only be available in the US. The cheapest I've found it with shipping to the UK is about $80. For an experiment this is a bit steep.
I have taken another set very accurate measurements of all the dimensions of my deck and set up a little spreadsheet to calculate the required belt lengths to completely balance the side forces acting on the main bearing. Luckily it turns out that the belt lengths I have been using were pretty much spot on. This spreadsheet will be very useful when I get to trying different belt materials.
I've also set up a test gig to measure the stretch of different materials under varying loads. Previously I had only measured the stretch at the target belt tension. I've now measured from 0 to 1.5N both when loading and unloading the belt. Being polymers the belts will stretch and relax at different rates. When plotted on a graph the loading and unloading cycle forms a loop that shows the hysteresis of the belt. Hysteresis is very similar to damping.
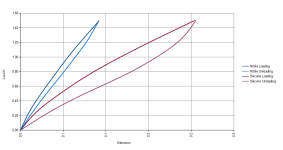
This is a quick comparison I made between 1.5mm nitrile rubber and 1.5mm silicone. The Silicone is much stretchier (more compliant) as shown by the shallower slope. It also has greater hysteresis as shown by the width of the loop. Unfortunately I am unable to determine how this relates to sound quality at the moment.
I have ordered some additional belt materials to further this investigation. I have some monofilament polyester thread on order, thanks for the heads up Panos. Unfortunately my deck isn't suitable for mylar tape. 😢. I'll keep looking for an affordable way to bond silicone but my hopes are not high.
Niffy
Good luck with getting your motor sorted. As you've already experienced the Maxon Re-Max motors have huge potential. Hopefully you can unleash even more of this potential.
My experiments with drive belts is continuing slowly.
Unfortunately I'm going to have to give up on silicone as an option. The only product that I've found that can bond the ends satisfactorily seems to only be available in the US. The cheapest I've found it with shipping to the UK is about $80. For an experiment this is a bit steep.
I have taken another set very accurate measurements of all the dimensions of my deck and set up a little spreadsheet to calculate the required belt lengths to completely balance the side forces acting on the main bearing. Luckily it turns out that the belt lengths I have been using were pretty much spot on. This spreadsheet will be very useful when I get to trying different belt materials.
I've also set up a test gig to measure the stretch of different materials under varying loads. Previously I had only measured the stretch at the target belt tension. I've now measured from 0 to 1.5N both when loading and unloading the belt. Being polymers the belts will stretch and relax at different rates. When plotted on a graph the loading and unloading cycle forms a loop that shows the hysteresis of the belt. Hysteresis is very similar to damping.
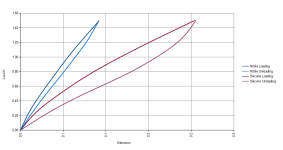
This is a quick comparison I made between 1.5mm nitrile rubber and 1.5mm silicone. The Silicone is much stretchier (more compliant) as shown by the shallower slope. It also has greater hysteresis as shown by the width of the loop. Unfortunately I am unable to determine how this relates to sound quality at the moment.
I have ordered some additional belt materials to further this investigation. I have some monofilament polyester thread on order, thanks for the heads up Panos. Unfortunately my deck isn't suitable for mylar tape. 😢. I'll keep looking for an affordable way to bond silicone but my hopes are not high.
Niffy
My analysis of the difference between the hysteresis of the two belts was incorrect.
To compare I should stretch the belts to the same extension not the same load and the degree of damping is the area between the lines. If I had done so the area of the loop for the silicone would actually be slightly smaller than for the nitrile showing that the nitrile is actually better damped.
I did also measure some 2mm diameter silicone. This had almost exactly the same compliance as the 1.5mm nitrile but the hysteresis was only about half.
Niffy
To compare I should stretch the belts to the same extension not the same load and the degree of damping is the area between the lines. If I had done so the area of the loop for the silicone would actually be slightly smaller than for the nitrile showing that the nitrile is actually better damped.
I did also measure some 2mm diameter silicone. This had almost exactly the same compliance as the 1.5mm nitrile but the hysteresis was only about half.
Niffy
Last edited:
@niffy
Interesting intel.
In the interests of getting a silicone belt at a useful length, have you explored this outfit?
dindiki.com
Interesting intel.
In the interests of getting a silicone belt at a useful length, have you explored this outfit?
dindiki.com
Hi Sondeknz,
Thanks for the link.
Unfortunately I can only use round belts as my drive system is somewhat unusual comprising 3 separate belts and a couple of idler wheels.
After a lot of searching yesterday I think that I have found a suitable method of bonding silicone. It's still quite expensive but not anywhere near the price of what I had previously found. It's from an industrial adhesive supplier so is hopefully of good quality.
I now have 7 different belt materials to play with. 1mm, 1.5mm and 2mm nitrile rubber, 1.5mm and 2mm silicone, 1.5mm Viton rubber and monofilament polyester.
Should keep me busy for a while.
Niffy
Thanks for the link.
Unfortunately I can only use round belts as my drive system is somewhat unusual comprising 3 separate belts and a couple of idler wheels.
After a lot of searching yesterday I think that I have found a suitable method of bonding silicone. It's still quite expensive but not anywhere near the price of what I had previously found. It's from an industrial adhesive supplier so is hopefully of good quality.
I now have 7 different belt materials to play with. 1mm, 1.5mm and 2mm nitrile rubber, 1.5mm and 2mm silicone, 1.5mm Viton rubber and monofilament polyester.
Should keep me busy for a while.
Niffy
Niffy,
That’s great stuff. Looking forward to the results of your experiments with great interest.
Panos
That’s great stuff. Looking forward to the results of your experiments with great interest.
Panos
Hi Sondeknz,
Thanks for the kind offer.
Unfortunately I won't know the required dimensions until I've measured the compliance of the belt.
When I originally designed my deck I used a single belt that ran around the subplatter, motor and idlers in the same way that Arthur Khoubesserian did with his vector drive. I'm very proud to say that I came up with the idea completely independently, the guy's a frickin' genius. The layout was set so the motor and idlers were 120° apart centered around the main bearing with the belt making 90° turns at each.
Since then I have further refined the design and now have 3 separate belts. As the belts each run at slightly different heights on the subplatter (and the motor pulley has slightly increased in diameter) the 3 belts now need to be slightly different in length so that the forces acting on the main bearing completely cancel out.
With my current 1.5mm nitrile rubber belts the difference between the longest and shortest is only about 4mm, about a 1% difference. The deck runs fine with 3 belts of the same length but sounds more refined with the lengths fine tuned. The required lengths of the belts and the difference between them will be different with each belt material so has to be calculated afresh for each.
Luckily I find researching, building test rigs and experimenting to fine tune a design highly enjoyable.
Niffy
Thanks for the kind offer.
Unfortunately I won't know the required dimensions until I've measured the compliance of the belt.
When I originally designed my deck I used a single belt that ran around the subplatter, motor and idlers in the same way that Arthur Khoubesserian did with his vector drive. I'm very proud to say that I came up with the idea completely independently, the guy's a frickin' genius. The layout was set so the motor and idlers were 120° apart centered around the main bearing with the belt making 90° turns at each.
Since then I have further refined the design and now have 3 separate belts. As the belts each run at slightly different heights on the subplatter (and the motor pulley has slightly increased in diameter) the 3 belts now need to be slightly different in length so that the forces acting on the main bearing completely cancel out.
With my current 1.5mm nitrile rubber belts the difference between the longest and shortest is only about 4mm, about a 1% difference. The deck runs fine with 3 belts of the same length but sounds more refined with the lengths fine tuned. The required lengths of the belts and the difference between them will be different with each belt material so has to be calculated afresh for each.
Luckily I find researching, building test rigs and experimenting to fine tune a design highly enjoyable.
Niffy
I had an interesting time visiting my friend who has the Pink Triangle Anniversary turntable yesterday. We were experimenting with his prototype open baffle speakers. During the listening tests we kept finding that the speed would be nice and stable then start to drift all over the place. I eventually found the cause of the speed fluctuations.
He had recently purchased an Origin Live belt. The belt appears to have been made slightly to long resulting in it being too loose and slipping on the drive pulley. Putting the original neoprene belt back on cured the speed problem. The interesting part was how much the sound varied between the two. The neoprene belt sounded hard, shouty and congested in comparison. The Origin Live was vastly better. He will be contacting Mark at OL today to arrange a replacement.
Also of interest is the difference between the two belts. The OL is much stretchier, more compliant, and returns to shape after being stretched much more slowly. This would indicate that it has much higher hysteresis. I had been expecting that higher hysteresis would sound better but had also anticipated that lower compliance would also sound better.
Definitely a useful data point in my quest for the best belt material. Pity that OL don't have the same material in a round section.
Niffy
He had recently purchased an Origin Live belt. The belt appears to have been made slightly to long resulting in it being too loose and slipping on the drive pulley. Putting the original neoprene belt back on cured the speed problem. The interesting part was how much the sound varied between the two. The neoprene belt sounded hard, shouty and congested in comparison. The Origin Live was vastly better. He will be contacting Mark at OL today to arrange a replacement.
Also of interest is the difference between the two belts. The OL is much stretchier, more compliant, and returns to shape after being stretched much more slowly. This would indicate that it has much higher hysteresis. I had been expecting that higher hysteresis would sound better but had also anticipated that lower compliance would also sound better.
Definitely a useful data point in my quest for the best belt material. Pity that OL don't have the same material in a round section.
Niffy
Great intel!
I'm just shocked that the PT deck didn't offer any motor adjustment. Or perhaps it does - but the new OL belt was so much bigger that any motor adjustment had already been consumed.
Belt material sure does make a massive difference...
LOVING our ultra-stretchy, ultra-grippy, super-loose BLUE SILICONE BELT.
I'm just shocked that the PT deck didn't offer any motor adjustment. Or perhaps it does - but the new OL belt was so much bigger that any motor adjustment had already been consumed.
Belt material sure does make a massive difference...
LOVING our ultra-stretchy, ultra-grippy, super-loose BLUE SILICONE BELT.
Niffy, Sondeknz,
my take on belt effect on sound is more dependent on belt tension than anything else. The same belt sounds different, depending on the tension. The less tension, the better (without slipping). Of course, tension can be a function of belt material (i.e. friction coefficient) and shape (i.e. coupling area on the pulley).
I am curious about Niffy's results, which I am expecting with great interest.
my take on belt effect on sound is more dependent on belt tension than anything else. The same belt sounds different, depending on the tension. The less tension, the better (without slipping). Of course, tension can be a function of belt material (i.e. friction coefficient) and shape (i.e. coupling area on the pulley).
I am curious about Niffy's results, which I am expecting with great interest.
- Home
- Source & Line
- Analogue Source
- 12VDC motor for the turntable. Power, torque, PCB questions