I do.
I have a calibrated 50hz strobe light and strobe disk. I reset the speed every time I change belts. The speed can change quite a bit between belts, especially those of different thicknesses.
I have a calibrated 50hz strobe light and strobe disk. I reset the speed every time I change belts. The speed can change quite a bit between belts, especially those of different thicknesses.
Hi Niffy,
apologies if you have explained it in previous posts, but do you calculate or measure the forces on the belt? If you measure, how do you do it?
Thanks.
P.
apologies if you have explained it in previous posts, but do you calculate or measure the forces on the belt? If you measure, how do you do it?
Thanks.
P.
I revisited the 1mm nitrile and 2mm silicone belts. I was a little over generous with my previous evaluation with both of them. Both of them had strong points, especially imaging with the 1mm nitrile. Both of them lacked bass definition and depth, the 1mm nitrile was a bit thin across the board. The biggest failing was in the way they portrayed the leading edges of notes. They both had soft transients.
I also experimented further with the 2mm nitrile. I noticed that the belt tension that I am using was insufficient to curve this belt in as tight a curve as the diameter of the idler/pulley. This resulted in the belt arching away from the idler and not making full contact.
These photos should illustrate better than my description.
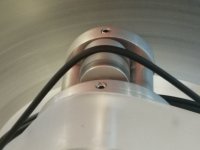
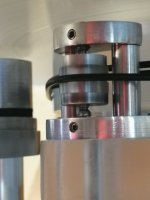
The 2mm nitrile had scored highly on tonality but imaging dynamics and transparency faired less well. I had noted that these belts seemed unstable, like they were only just hanging in there. The way the belt interface with the idlers could well explain this.
I remade these belts, increasing the side force on the motor from 0.75N to 1.25N.
The improvement in sound quality was quite dramatic. Imaging and transparency both improved. Dynamics went from OK to the best of the test group. Unfortunately this came at the expense of midrange tonality. Overall still better than previously, probably just behind the 2mm EPDM.
The 2mm EPDM also suffered from the belt arching away from the idlers but to a lesser extent. I made up a second set of 2mm belts of this material with a side force of 1N. These weren't quite as good as the 0.75N set, loosing a bit of midrange fullness.
I'm currently just leaving the 2mm EPDM on the deck and living with them, getting used to them. Compared to my reference 1.5mm nitrile they seem to be better tonally from top to bottom, image better and be very slightly more transparent. However they do seem to be slightly softer on transients. This might be an illusion as the body of notes and the decay are better so the transients only suffered in comparison.
I'll live with the 2mm EPDM for a bit longer then swap back to the 1.5mm nitrile for a while.
Niffy
I also experimented further with the 2mm nitrile. I noticed that the belt tension that I am using was insufficient to curve this belt in as tight a curve as the diameter of the idler/pulley. This resulted in the belt arching away from the idler and not making full contact.
These photos should illustrate better than my description.
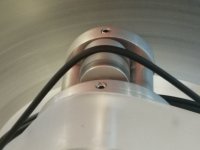
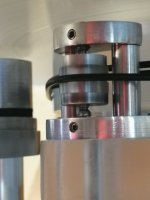
The 2mm nitrile had scored highly on tonality but imaging dynamics and transparency faired less well. I had noted that these belts seemed unstable, like they were only just hanging in there. The way the belt interface with the idlers could well explain this.
I remade these belts, increasing the side force on the motor from 0.75N to 1.25N.
The improvement in sound quality was quite dramatic. Imaging and transparency both improved. Dynamics went from OK to the best of the test group. Unfortunately this came at the expense of midrange tonality. Overall still better than previously, probably just behind the 2mm EPDM.
The 2mm EPDM also suffered from the belt arching away from the idlers but to a lesser extent. I made up a second set of 2mm belts of this material with a side force of 1N. These weren't quite as good as the 0.75N set, loosing a bit of midrange fullness.
I'm currently just leaving the 2mm EPDM on the deck and living with them, getting used to them. Compared to my reference 1.5mm nitrile they seem to be better tonally from top to bottom, image better and be very slightly more transparent. However they do seem to be slightly softer on transients. This might be an illusion as the body of notes and the decay are better so the transients only suffered in comparison.
I'll live with the 2mm EPDM for a bit longer then swap back to the 1.5mm nitrile for a while.
Niffy
Hi Panos,Hi Niffy,
apologies if you have explained it in previous posts, but do you calculate or measure the forces on the belt? If you measure, how do you do it?
Thanks.
P.
I measure the materials before I make up belts so I'm just measuring a single length.
I gradually add weights to the material and measure how much it stretches I then gradually remove the weights and measure the length as it contracts. I repeat the loading and unloading cycle 3 times and take the average of the 3.
As my target belt tension is ~0.5N (to give ~0.75N force on motor) I load from 0N to 1N. This puts my target in the middle. I use 0.125N weights so have 9 steps, 54 measurements per belt material.
The extension of the belt will be different during loading and unloading. This forms a loop. The area of this loop is used to determine the Hysteresis (internal damping) of the belt centred around my target tension.
The average of the extension of the belt between loading and unloading at the target tension is used to calculate the compliance of the belt material. This compliance is then used to calculate the lengths the belts needs to be to give the correct tension.
Niffy
This chart shows all of the belt materials that I have tested so far.
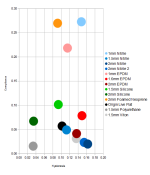
Compliance is shown on the x axis with stretchier towards the top and less stretchy towards the bottom.
Hysteresis is shown on the y axis. Hysteresis is the internal damping inherent within the material. Higher hysteresis means greater damping.
Please ignore the scales on this chart, they are calculated around my target belt tension. The important thing is that the difference between the different materials is clearly visible.
Of the materials shown I have not made belts from the polyurethane. It feels too inflexible and low friction, it would probably need excessive tension.
I was unable to listen to the 1.6mm viton as it slipped on the drive pulley.
I have made belts from the 1mm EPDM but have not listened to them as yet.
2mm nitrile has two entries because I wanted to double check that my measurements are consistent. The two sets of measurements are very close. The second set were taken on a much warmer day which would explain the slightly higher compliance and lower hysteresis.
In general it would seem that belts with lower compliance and higher hysteresis sound better. That is the belts located at the bottom right of the chart. This by itself would suggest that the 2mm nitrile should be the best sounding. It very nearly is with high belt tension. What the chart does not show is the flexibility of the belts. It would appear that being more flexible is beneficial. The 2mm nitrile is much stiffer than most of the other belts, too stiff. The 2mm EPDM is probably about on the edge of being too stiff. The very flexible belts seem to have a smoothness and openness.
I've made an attempt to estimate the relative flexibility of the different belts. I used the 1.5mm nitrile as a basis, hence it having a relative flexibility of 1. Higher numbers are more flexible.
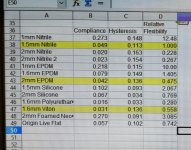
The calculated flexibilities line up pretty well with how the materials feel with the exception of the polyurethane which feels stiffer than the chart would imply.
A thinner belt made of the same material will be more flexible but will also have greater compliance. The trick seems to be to find a belt that is low compliance, has high damping and is flexible.
The 1.6mm viton looks ideal being stiffer than the 2mm EPDM, having the same damping and being more flexible. Unfortunately this belt slipped. I have remade these belts to have 50% more tension. Hopefully this will stop it slipping without introducing additional problems.
I'm more interested than ever to get the polyester monofilament thread. It will hopefully be very low compliance with high hysteresis. Being very thin it should be very flexible.
I'm still going to keep the 2mm EPDM on the deck for a while before I compare back to the 1.5mm nitrile. Then bring in the new materials.
Niffy
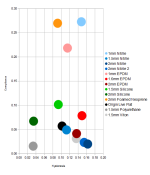
Compliance is shown on the x axis with stretchier towards the top and less stretchy towards the bottom.
Hysteresis is shown on the y axis. Hysteresis is the internal damping inherent within the material. Higher hysteresis means greater damping.
Please ignore the scales on this chart, they are calculated around my target belt tension. The important thing is that the difference between the different materials is clearly visible.
Of the materials shown I have not made belts from the polyurethane. It feels too inflexible and low friction, it would probably need excessive tension.
I was unable to listen to the 1.6mm viton as it slipped on the drive pulley.
I have made belts from the 1mm EPDM but have not listened to them as yet.
2mm nitrile has two entries because I wanted to double check that my measurements are consistent. The two sets of measurements are very close. The second set were taken on a much warmer day which would explain the slightly higher compliance and lower hysteresis.
In general it would seem that belts with lower compliance and higher hysteresis sound better. That is the belts located at the bottom right of the chart. This by itself would suggest that the 2mm nitrile should be the best sounding. It very nearly is with high belt tension. What the chart does not show is the flexibility of the belts. It would appear that being more flexible is beneficial. The 2mm nitrile is much stiffer than most of the other belts, too stiff. The 2mm EPDM is probably about on the edge of being too stiff. The very flexible belts seem to have a smoothness and openness.
I've made an attempt to estimate the relative flexibility of the different belts. I used the 1.5mm nitrile as a basis, hence it having a relative flexibility of 1. Higher numbers are more flexible.
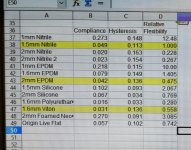
The calculated flexibilities line up pretty well with how the materials feel with the exception of the polyurethane which feels stiffer than the chart would imply.
A thinner belt made of the same material will be more flexible but will also have greater compliance. The trick seems to be to find a belt that is low compliance, has high damping and is flexible.
The 1.6mm viton looks ideal being stiffer than the 2mm EPDM, having the same damping and being more flexible. Unfortunately this belt slipped. I have remade these belts to have 50% more tension. Hopefully this will stop it slipping without introducing additional problems.
I'm more interested than ever to get the polyester monofilament thread. It will hopefully be very low compliance with high hysteresis. Being very thin it should be very flexible.
I'm still going to keep the 2mm EPDM on the deck for a while before I compare back to the 1.5mm nitrile. Then bring in the new materials.
Niffy
Last edited:
Niffy,Hi Panos,
I measure the materials before I make up belts so I'm just measuring a single length.
I gradually add weights to the material and measure how much it stretches I then gradually remove the weights and measure the length as it contracts. I repeat the loading and unloading cycle 3 times and take the average of the 3.
As my target belt tension is ~0.5N (to give ~0.75N force on motor) I load from 0N to 1N. This puts my target in the middle. I use 0.125N weights so have 9 steps, 54 measurements per belt material.
The extension of the belt will be different during loading and unloading. This forms a loop. The area of this loop is used to determine the Hysteresis (internal damping) of the belt centred around my target tension.
The average of the extension of the belt between loading and unloading at the target tension is used to calculate the compliance of the belt material. This compliance is then used to calculate the lengths the belts needs to be to give the correct tension.
Niffy
you have clearly thought your measurement process.
Now, the challenge is to correlate your listening results with the appropriate material qualities (characteristics).
I see where you are coming from with respect to the hysteresis concept. Do you think that the time scale may affect hysteresis, i.e. if the stretching/contracting happens in say 1 sec or in 0.1 sec (or less). Would that make a difference in the measured hysteresis? Just a thought.
Keep up the good work. It's extremely interesting and thank you for sharing.
Let's see how the polyester thread fares against the other materials. And even more importantly what your listening impressions are.
Cheers,
P.
Last edited:
Hi Panos, excellent question.
The time scale will indeed affect hysteresis. The measured hysteresis of a material will vary depending on the magnitude of the load and rate at which the load is applied. This is one of the characteristics of viscoelastic materials. I have tried to keep the rate at which I add and remove the weights consistent. The time taken to fully load and unload is much longer than I would ideally like due to doing it manually, minutes rather than milliseconds. A material that shows higher hysteresis at low frequencies is almost certainly going to also show higher hysteresis at higher frequencies. This is why I said to ignore the scale on the chart in my previous post. The chart shows the relative difference in hysteresis rather than a meaningful absolute value.
As I purchased the Sulky polyester monofilament from New York in the US it's expected arrival isn't until the 3rd of July. Hopefully this is a pessimistic estimate to prevent premature chasing and it will arrive before then.
Is should give me plenty of time to finish testing the other materials by then.
Niffy
The time scale will indeed affect hysteresis. The measured hysteresis of a material will vary depending on the magnitude of the load and rate at which the load is applied. This is one of the characteristics of viscoelastic materials. I have tried to keep the rate at which I add and remove the weights consistent. The time taken to fully load and unload is much longer than I would ideally like due to doing it manually, minutes rather than milliseconds. A material that shows higher hysteresis at low frequencies is almost certainly going to also show higher hysteresis at higher frequencies. This is why I said to ignore the scale on the chart in my previous post. The chart shows the relative difference in hysteresis rather than a meaningful absolute value.
As I purchased the Sulky polyester monofilament from New York in the US it's expected arrival isn't until the 3rd of July. Hopefully this is a pessimistic estimate to prevent premature chasing and it will arrive before then.
Is should give me plenty of time to finish testing the other materials by then.
Niffy
Hi Niffy,
my comment was that the time scale of how you measure the belt characteristics (i.e. the time you take to load and unload the belt) is different from the time scale the belt is actually loaded/unloaded in real operation, due to stylus drag. Without being able to quantify it accurately, I would expect that the real phenomenon may be one or even two orders of magnitude smaller than your belt measurements. If we assume that the stylus drag may change every 1mm of record movement (rotation), I've done some quick calculations and at say 15cm from the record center, that 1mm can be covered in 0.0019s. So, I would assume that theoretically in that (very, very small) timeframe, the belt tension could change, due to stylus drag.
I would not be surprised if the belt material showed different behavior in 0.0019s vs. say 1s or more.
My two cents...
Cheers,
Panos
my comment was that the time scale of how you measure the belt characteristics (i.e. the time you take to load and unload the belt) is different from the time scale the belt is actually loaded/unloaded in real operation, due to stylus drag. Without being able to quantify it accurately, I would expect that the real phenomenon may be one or even two orders of magnitude smaller than your belt measurements. If we assume that the stylus drag may change every 1mm of record movement (rotation), I've done some quick calculations and at say 15cm from the record center, that 1mm can be covered in 0.0019s. So, I would assume that theoretically in that (very, very small) timeframe, the belt tension could change, due to stylus drag.
I would not be surprised if the belt material showed different behavior in 0.0019s vs. say 1s or more.
My two cents...
Cheers,
Panos
Last edited:
Absolutely.
Most viscoelastic materials are more compliant at low frequencies and less compliant at higher frequencies. Likewise the hysteresis will change with frequency. Generally a material that shows higher hysteresis at low frequencies compared to another will also show higher hysteresis at higher frequencies.
It would be nice if I could measure over a wide frequency range but this would require equipment of much greater sophistication than I can cobble together from what I possess.
The important things are not the absolute values of compliance, flexibility and hysteresis but the relative differences between these factors with the different materials.
Most viscoelastic materials are more compliant at low frequencies and less compliant at higher frequencies. Likewise the hysteresis will change with frequency. Generally a material that shows higher hysteresis at low frequencies compared to another will also show higher hysteresis at higher frequencies.
It would be nice if I could measure over a wide frequency range but this would require equipment of much greater sophistication than I can cobble together from what I possess.
The important things are not the absolute values of compliance, flexibility and hysteresis but the relative differences between these factors with the different materials.
Niffy,
yes, I think that the frequency that the decompression/compression takes place may be so high, that the belt material may not be able to even 'sense' it. Do not misunderstand me, your measurements are absolutely fine to measure the material properties under 'static' conditions. But in reality the phenomenon is fully 'transient' and the material may have a completely different reaction than the what you've measured, i.e. transient and static behavior may be completely irrelevant.
Again, please do not misinterpret my comments as criticism. I wonder how it might be possible to measure the transient phenomenon.
Cheers,
P.
yes, I think that the frequency that the decompression/compression takes place may be so high, that the belt material may not be able to even 'sense' it. Do not misunderstand me, your measurements are absolutely fine to measure the material properties under 'static' conditions. But in reality the phenomenon is fully 'transient' and the material may have a completely different reaction than the what you've measured, i.e. transient and static behavior may be completely irrelevant.
Again, please do not misinterpret my comments as criticism. I wonder how it might be possible to measure the transient phenomenon.
Cheers,
P.
All materials will "react" to some extent to an applied force regardless of its frequency or amplitude. The amount of reaction may be very small but so is the difference in the amount the stylus moves between good reproduction and exceptional reproduction.
But yes, more information gained over a wider frequency range would be great.
But yes, more information gained over a wider frequency range would be great.
Another aspect worthy of consideration is whether a round or flat belt is preferable.
It's interesting that almost all the higher end BD turntables use a flat belt; what are the differences?
It's interesting that almost all the higher end BD turntables use a flat belt; what are the differences?
Hi Ralph,
My deck is somewhat unusual in design.
I initially designed the drive system to use a single flat belt that went around the motor pulley, the subplatter and a pair of idler wheels. This was done so that all side forces acting on the main bearing cancelled each other resulting in zero force. The main bearing is inverted with the bearing point just below the surface of the platter. This configuration balanced the platter to such an extent that there would be no side forces acting on the bearing sleeve. As there would be no side forces acting on the sleeve the sleeve is not required. In normal turntable bearings the sleeve is responsible for the vast majority of friction, 95-98%. By removing the sleeve friction is massively reduced. I have a true single point bearing. There are other advantage to removing sleeve beyond this.
This design would sometimes have a slight issue with badly out of balance records. Runout could become a little excessive.
I further developed this design by using 3 separate belts, one for the motor and one each for the 2 idlers. This improved the balance of the forces further eliminating the runout problem. This also had the advantage of markedly improving sound quality on all records.
Running three belts in the space that the single flat belt had run in required that I move to round belts.
With most designs a flat belt is probably going to be a better solution. A flat belt with the same cross sectional area as a round belt will have the same compliance but will be more flexible.
This would seem to agree with the conclusions of my recent experiments in that low compliance with high flexibility are preferable.
Niffy
My deck is somewhat unusual in design.
I initially designed the drive system to use a single flat belt that went around the motor pulley, the subplatter and a pair of idler wheels. This was done so that all side forces acting on the main bearing cancelled each other resulting in zero force. The main bearing is inverted with the bearing point just below the surface of the platter. This configuration balanced the platter to such an extent that there would be no side forces acting on the bearing sleeve. As there would be no side forces acting on the sleeve the sleeve is not required. In normal turntable bearings the sleeve is responsible for the vast majority of friction, 95-98%. By removing the sleeve friction is massively reduced. I have a true single point bearing. There are other advantage to removing sleeve beyond this.
This design would sometimes have a slight issue with badly out of balance records. Runout could become a little excessive.
I further developed this design by using 3 separate belts, one for the motor and one each for the 2 idlers. This improved the balance of the forces further eliminating the runout problem. This also had the advantage of markedly improving sound quality on all records.
Running three belts in the space that the single flat belt had run in required that I move to round belts.
With most designs a flat belt is probably going to be a better solution. A flat belt with the same cross sectional area as a round belt will have the same compliance but will be more flexible.
This would seem to agree with the conclusions of my recent experiments in that low compliance with high flexibility are preferable.
Niffy
Hi Panos,
Any update on the status of your Maxon motor?
Do you know if the motor you had was defective and have you received a replacement?
Niffy
Any update on the status of your Maxon motor?
Do you know if the motor you had was defective and have you received a replacement?
Niffy
Hi Niffy,
Maxon has replied that they have not been able to test my motor unit until now and they will try to do that next week. As soon as I have their feedback, I will post it. Thanks for asking.
Meanwhile, I am also expecting you to receive the Sulky polyester thread and compare it head to head with the other belts. Very curious about your impressions.
Panos
Maxon has replied that they have not been able to test my motor unit until now and they will try to do that next week. As soon as I have their feedback, I will post it. Thanks for asking.
Meanwhile, I am also expecting you to receive the Sulky polyester thread and compare it head to head with the other belts. Very curious about your impressions.
Panos
Good to hear that Maxon are on the case, even if it is at a very slow pace.
Talking of slow pace, the Sulky thread isn't due for another couple of weeks.
Talking of slow pace, the Sulky thread isn't due for another couple of weeks.
- Home
- Source & Line
- Analogue Source
- 12VDC motor for the turntable. Power, torque, PCB questions