Perhaps shape of the baffle helps with stiffness so it can be bit flimsier than expected. Perhaps the allen bolts to back is to make the innards accessible while visually hiding any fasteners. Back panel could have been detachable instead of the front, but I speculate it was likely easier this way. If backpanel was detachable, they would have needed different way to attach the driver for example. The bracing damping is interesting however, damping everywhere, no rigid connections between bracing and panels!
More images from innards here https://www.stereonet.com/forums/topic/98114-kef-ls50-crossover-upgrade/
More images from innards here https://www.stereonet.com/forums/topic/98114-kef-ls50-crossover-upgrade/
Attachments
There was some mention in the white paper of the removable back panel on the BBC speaker. I suspect simplicity and looks were the reasons in the LS50.If backpanel was detachable, they would have needed different way to attach the driver for example.
Did not know earlier that the KEF LS50 baffle is constructed this way and comparatively so light and hollow. Typically the best practices recommend a very strong and dense baffle. I guess the strength will come from the shape and the materials used, and due to the "lossy" nature of the mounting and braces, the driver is still well decoupled from the baffle and rest of the cabinet. The LS50 baffle shape should help with the diffraction signature also, so with the stiffness it would be two birds with one stone.
Agree, the rear mount screws would keep the design clean.
IIRC, the KEF Team found that with using damped bracing and damped mounting of front baffle and driver they could do away with CLD cabinet construction? Or the cabinet has CLD construction too?
Agree, the rear mount screws would keep the design clean.
IIRC, the KEF Team found that with using damped bracing and damped mounting of front baffle and driver they could do away with CLD cabinet construction? Or the cabinet has CLD construction too?
The text hints there is CLD on the walls, but the images and illustrations show it only between brace and wall, and between brace and drive magnet.
More observations: Since the LS50 box is relatively small, and the brace is middle of the panels killing lowest mode, the resulting structure ends up relatively close to Linkwitz rule of thumb for ~4" brace spacing and aligns with notion that it pushes lowest panel modes to low kHz range, which is visible in the KEF paper plots. It's quite shocking how effective the overall construct with damping is in the paper.
I suspect these issues get worse the bigger the enclosure, so perhaps this exact construction method would need to be adapted. If I reflect to what I've been just prototyping first thing that comes to mind is I'm not sure how optimized the damping compound here is for this particular application, or would it work for a box whose resonances are octave lower? I'm using just shore A40 stiffness construction glue, and not sure about what thickness is most effective, also, my CLD parts aren't as long as "full span of a panel" like with KEF, and my bracing is not middle of the panel but two braces about at 1/3 locations and so on, many things are different than with the KEF50 and performance is likely not so good. Likely, because I do not have comparable data so just estimating.
I cannot comment on how easy it is to replicate results in the paper with any other size and shape and construction than LS50, but I suspect it's not straight forward. For example, a typical bookshelf two way speaker doesn't have driver middle of the front panel, so bracing would need to be adapted and so on. Still, such speaker is relatively small and perhaps requires just one more brace to maintain unbraced panel area small. If box is bigger and one would need more than one brace per wall I speculate.
More observations: Since the LS50 box is relatively small, and the brace is middle of the panels killing lowest mode, the resulting structure ends up relatively close to Linkwitz rule of thumb for ~4" brace spacing and aligns with notion that it pushes lowest panel modes to low kHz range, which is visible in the KEF paper plots. It's quite shocking how effective the overall construct with damping is in the paper.
I suspect these issues get worse the bigger the enclosure, so perhaps this exact construction method would need to be adapted. If I reflect to what I've been just prototyping first thing that comes to mind is I'm not sure how optimized the damping compound here is for this particular application, or would it work for a box whose resonances are octave lower? I'm using just shore A40 stiffness construction glue, and not sure about what thickness is most effective, also, my CLD parts aren't as long as "full span of a panel" like with KEF, and my bracing is not middle of the panel but two braces about at 1/3 locations and so on, many things are different than with the KEF50 and performance is likely not so good. Likely, because I do not have comparable data so just estimating.
I cannot comment on how easy it is to replicate results in the paper with any other size and shape and construction than LS50, but I suspect it's not straight forward. For example, a typical bookshelf two way speaker doesn't have driver middle of the front panel, so bracing would need to be adapted and so on. Still, such speaker is relatively small and perhaps requires just one more brace to maintain unbraced panel area small. If box is bigger and one would need more than one brace per wall I speculate.
Last edited:
That is actually pretty well known. The only air that gets heavy panels resonating and thus emitting sound at the outside is resonating air. And if you have much resonating air inside an enclosure, something went wrong earlier.but it suggests that mechanical vibration of the box parts is the issue, while what happens inside the box less so.
Put otherwise, non-resonant sound transmission through enclosure walls only has a very limited effect on system response, some hard to measure and even harder to hear linear distortion, that is it.
I've been inside both the OG LS50 and Meta and they made some changes between the two. With the OG the baffle was a plastic moulding that was screwed in from the rear via long bolts as @fluid shows. With the meta, as far as I can tell, the front baffle was moulded from a much bulkier denser material and rigidly glued to the carcass, the rear panel was then glued in. In both cases the horizontal and vertical braces were separated from the enclosure with a putty like compliant tape, also placed between the driver magnet and the brace. There is nothing on the enclosure walls.
Basic stuff aside, I think its very hard to predict exactly what an enclosure will do in terms of panel resonances. The devil really is in the detail. Materials, joint types, adhesive, bracing, mounting, damping all contribute. Its great that KEF share as much as they do.
Remember that the driver membrane is thin and also coupled to the air mass inside the enclosure. I think someone (!) at the BBC (during LS3/5a development?) showed that transmission of box resonance through the cone is also significant. Martin Colloms documented this in High Performance Loudspeakers.
Basic stuff aside, I think its very hard to predict exactly what an enclosure will do in terms of panel resonances. The devil really is in the detail. Materials, joint types, adhesive, bracing, mounting, damping all contribute. Its great that KEF share as much as they do.
Remember that the driver membrane is thin and also coupled to the air mass inside the enclosure. I think someone (!) at the BBC (during LS3/5a development?) showed that transmission of box resonance through the cone is also significant. Martin Colloms documented this in High Performance Loudspeakers.
Last edited:
Hmm, of topic but in the context, quick question: my proto box lowest resonance in impedance plot is about at ~400Hz, which changes how tight the driver screws are (got some damping between driver and panel, also between screws and the driver), so could this be just the whole box assembly moving uniformly, and not any panel resonance as such?
This low issues are problematic to measure, semianechoic frequency response measurements, even outside on a few meter pole, do not give enough resolution to see resonances at 400Hz.
This low issues are problematic to measure, semianechoic frequency response measurements, even outside on a few meter pole, do not give enough resolution to see resonances at 400Hz.
Depends on what you want to measure.
Perhaps a new thread where we , you and i, can explore the matter?
Perhaps a new thread where we , you and i, can explore the matter?
Hi, thanks JanRSmith. I started to collect data to make a post but noticed I need to take some more to make a case 🙂
Thanks for the input in the posts above.
The BBC paper linked below from Harwood is interesting in a few ways. The measurements they made of the Q of different materials. At the time stiff GRP materials were too expensive, in the current age birch ply might well top the cost list. The level that they found by listening experiments that corresponded to detectable and non detectable resonances in a handy chart and how they measured using a cardioid microphone in the nearfield.
https://downloads.bbc.co.uk/rd/pubs/reports/1977-03.pdf
I found this post and this thread in general helpful in sorting out some ideas
https://www.diyaudio.com/community/...-damping-with-mdf-and-ply.153419/post-6083896
For now my plan is to make a dual walled construction with a flexible sealant used betwen the outer and inner walls for damping.
The inner shell will be bigger/thicker and may be filled with something, sand plaster, resin, bog or some combination. The inner shell will use the wall shape for stiffness and have no bracing. The inner baffle part will mount the woofer and waveguide and aim to be stiff and solid. The waveguide will have some form of damped gasket. The outer visible skin will be stiff thin and light this will be the constraining layer. Depending on the shape I decide on for the cabinet the outer will either be in two parts or one part with a gap.
I might make a control that is just 3D printed for comparison or I might not depending on time and my own interest later on.
The BBC paper linked below from Harwood is interesting in a few ways. The measurements they made of the Q of different materials. At the time stiff GRP materials were too expensive, in the current age birch ply might well top the cost list. The level that they found by listening experiments that corresponded to detectable and non detectable resonances in a handy chart and how they measured using a cardioid microphone in the nearfield.
https://downloads.bbc.co.uk/rd/pubs/reports/1977-03.pdf
I found this post and this thread in general helpful in sorting out some ideas
https://www.diyaudio.com/community/...-damping-with-mdf-and-ply.153419/post-6083896
For now my plan is to make a dual walled construction with a flexible sealant used betwen the outer and inner walls for damping.
The inner shell will be bigger/thicker and may be filled with something, sand plaster, resin, bog or some combination. The inner shell will use the wall shape for stiffness and have no bracing. The inner baffle part will mount the woofer and waveguide and aim to be stiff and solid. The waveguide will have some form of damped gasket. The outer visible skin will be stiff thin and light this will be the constraining layer. Depending on the shape I decide on for the cabinet the outer will either be in two parts or one part with a gap.
I might make a control that is just 3D printed for comparison or I might not depending on time and my own interest later on.
fluid,
Like your inner box / outer shell construction approach. A few questions:
- The inner baffle will be connected/fixed to the inner box with a rigid glue? What about the rear panel?
- For the viscous layer between the inner box and the outer shell, have you considered Decidamp products? Are they available in Australia?
- Some CLD bracing ala Geddes style (slats that are connected to each other with glue with some viscous properties) should be easy to do for you - will further help with dissipating the energy/resonances with the inner box?
Like your inner box / outer shell construction approach. A few questions:
- The inner baffle will be connected/fixed to the inner box with a rigid glue? What about the rear panel?
- For the viscous layer between the inner box and the outer shell, have you considered Decidamp products? Are they available in Australia?
- Some CLD bracing ala Geddes style (slats that are connected to each other with glue with some viscous properties) should be easy to do for you - will further help with dissipating the energy/resonances with the inner box?
Last edited:
Box may have been a bad word to use out of habit, the shape won't be boxy but curved. So no rear panel as such.A few questions:
- The inner baffle will be connected/fixed to the inner box with a rigid glue? What about the rear panel?
The baffle will either be printed as part of the inner in a complete cross section or if that doesn't work for print orientation the baffle will be a separate piece and rigidly glued with something strong like epoxy.
I have and as far as I can tell they are, Pyrotek has an office relatively close that allegedly sells their products but I have no idea if they are reasonably priced or not. There is also Megasorber but price and availability I don't know. I am more interested to see if a commodity item works first.- For the viscous layer between the inner box and the outer shell, have you considered Decidamp products? Are they available in Australia?
I already have some leftover tubes of flexible sealant that I might use or I have found a local supplier that has tubes of a Polyurethane sealant that seems much like Sika 291 from the specs (but half the price), or an MS Polymer variant. Both are supposedly good at bonding with low surface energy products and plastics, where the tubes I already have are less optimistic about the chance of adhering to plastic.
In this case the cabinet is quite small comparatively speaking and the entire structure will be CLD. I don't see any value in complicating the whole thing trying to fit in a CLD brace. If the CLD in the main panel was ineffective or limited by design then more damping from CLD braces would make sense.- Some CLD bracing ala Geddes style (slats that are connected to each other with glue with some viscous properties) should be easy to do for you - will further help with dissipating the energy/resonances with the inner box?
What I will try and include is a structure to support the magnet to 'ground it' to the enclosure and prevent it from becoming a big mass spring. The magnet is pretty heavy and if I make this version sealed and EQ'd it might get some excursion on.
Flexibele sealants are generally not viscosious but only elastic, so a spring and not much damping.
Geddes @gedlee did mix such elastic 2 component matter with microballoons which turned out to be quite energy absorbing aka damping when used in cld (damping through shear) . If the damping material is to be applied in between it needs to be self curing aka 2 components .
Kef with its ls50 f.e. applied a softish matter between the brace and panel, it acts in fact as a soft spring with lots of damping, like a car suspension, so compress-decompress.
Both compress and shear are good principles to absorp energy, springs isolate above the resonance, and are in above examples needed to keep things in shape.
Wrt to the magnet support, i aplied that for the midrange, but still want make a testbed to get more info about uts effectiveness. Mind you the purifi driver magnet-basket mounting is based on a spring-damping principle if i correctly understand how it is constructed.
Geddes @gedlee did mix such elastic 2 component matter with microballoons which turned out to be quite energy absorbing aka damping when used in cld (damping through shear) . If the damping material is to be applied in between it needs to be self curing aka 2 components .
Kef with its ls50 f.e. applied a softish matter between the brace and panel, it acts in fact as a soft spring with lots of damping, like a car suspension, so compress-decompress.
Both compress and shear are good principles to absorp energy, springs isolate above the resonance, and are in above examples needed to keep things in shape.
Wrt to the magnet support, i aplied that for the midrange, but still want make a testbed to get more info about uts effectiveness. Mind you the purifi driver magnet-basket mounting is based on a spring-damping principle if i correctly understand how it is constructed.
Maybe, but I did put some time into finding the ones that are and do offer damping properties. Polyurethane and MS Polymer types being more likely to have viscoelastic and damping properties. There are of course specialist products but they come with a specialist price normally. Like if the word 'Acoustic' is included in a products title it is automatically twice as expensive as the product it really is.Flexibele sealants are generally not viscosious but only elastic, so a spring and not much damping.
I want to know if something worthwhile can be done with a commodity item. Augerpro did testing with adhesive/sealants and found some that worked so I intend to follow that path.
I agree to look for commodities instead of 'audio' . The damping needs are universal. For CLD i studied solutions in boat / shipbuilding where the need is to 'silence' stiff and heavy plates ( hull, bulkheads, etc) . Especially around machine rooms as there the problems are in the low frequencies, which is the most difficult frequency range. One of the guidelines is the stiffer the plate to damp the stiffer the energy absorber has te be. I work with fenolic resin/paper or cotton fabric based plates (Wislon Audio has a very similar approach) , which are heavy, quite stiff. Found a regular material, used in polyester/glassfiber shipbuilding as an intermediate layer to dampen de engine vibrations. N.B.: Wilson Audio has interesing reading for basic construction principles, such as joining plates ridgidly with glue, the glue needs to be of the saame Youngs modulus (or close) as the plates, els it will form a reflector of vibrational energy.
For much less heavy material like used in 3D prints less stiff damping matter is needed of course. Although on my list, not yet to addresss.
Any way i follow your proceedings with interest.
For much less heavy material like used in 3D prints less stiff damping matter is needed of course. Although on my list, not yet to addresss.
Any way i follow your proceedings with interest.
In the @augerpro thread, he found noticeable differences between various soft cure adhesive sealants (caulk-like materials) in terms of damping.
I am looking forward to seeing what you come up with @fluid. I have read the 1977 BBC paper many times, and to this day I still do not know how to reconcile their findings with some of the other (limited) research and (vast) anecdotal evidence.
I am looking forward to seeing what you come up with @fluid. I have read the 1977 BBC paper many times, and to this day I still do not know how to reconcile their findings with some of the other (limited) research and (vast) anecdotal evidence.
Still have a few tubes. Used it to help reduce noise transmission from laundry room. Worked. Never got around to try on speaker boxes. (No need, anyway -- stopped building conventional boxes by then.)remember the famous green glue?).
Last edited:
Not too thick layers with stuff like Vibradamp A-90-P if it is about damping panel resonances. Isomat is more an isolation of noise if am not mistaken.The typical stuff used in automotive does the job on thinner panels. I think here in Europe stuff like Isomat comes to mind. For CLD though, thin layers are preferred (remember the famous green glue?).
The Swedac layer i used for my enclosures is no longer available.
I sent a pair of waveguides to @Mainframe in the hope that he would find time to test before I did and it worked as there is now some data to look at.
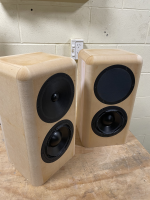
There isn't much of a surprise to me that measured reality is close to the prediction, but it really does hold directivity lower and more evenly than I thought it would. Normally this would be a benefit but in this configuration with a 6.5" woofer it makes mating the two together to not be a paint by numbers exercise. There is a 25mm roundover on these which is less than the 36mm originally simulated.
When the response is equalised for a flat on axis response with a 1.5K LR4 it looks like this
Interestingly the response is smoothest at 40 degrees off axis and if that is used as the reference axis you get a glossy brochure worthy normalized polar plot. I don't consider this to be totally representative of a real life scenario but it is interesting none the less.
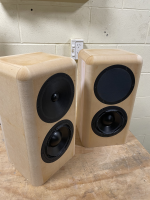
There isn't much of a surprise to me that measured reality is close to the prediction, but it really does hold directivity lower and more evenly than I thought it would. Normally this would be a benefit but in this configuration with a 6.5" woofer it makes mating the two together to not be a paint by numbers exercise. There is a 25mm roundover on these which is less than the 36mm originally simulated.
When the response is equalised for a flat on axis response with a 1.5K LR4 it looks like this
Interestingly the response is smoothest at 40 degrees off axis and if that is used as the reference axis you get a glossy brochure worthy normalized polar plot. I don't consider this to be totally representative of a real life scenario but it is interesting none the less.
- Home
- Loudspeakers
- Multi-Way
- Wide Directivity 2 way compact Speaker T34A Waveguide and Purifi 6.5 Aluminium