I have seen it before, are you referring to the plastic outer baffle?Have you had a look at this design?
Did you have the oppotunity to listen to it?
I saw it some time ago, but could not find any reporting or testing.
It is one of the concepts i am pondering on for the back chamber of tweeter.
When holding a sb26adc in my hand while testing i was surprised how heavy the backchamber was vibrating.
I saw it some time ago, but could not find any reporting or testing.
It is one of the concepts i am pondering on for the back chamber of tweeter.
When holding a sb26adc in my hand while testing i was surprised how heavy the backchamber was vibrating.
Alas no. But I wouldn’t know why this couldn’t be pulled off.Did you have the opportunity to listen to it?
It seems like there is no fibrous stuffing or foam in the cabinet, and all of the acoustic damping is coming from the gyroid matrix. It was not clear to me if the designer actually tested the acoustic absorption of the material ?
The one million dollar question of course being, why do we need acoustic damping?It seems like there is no fibrous stuffing or foam in the cabinet, and all of the acoustic damping is coming from the gyroid matrix. It was not clear to me if the designer actually tested the acoustic absorption of the material ?
Well, if we can be certain that there are no internal acoustic resonances (standing wave resonances), then I suppose we don't need acoustic damping. None of the common geometric shapes have this property. An acoustic resonance can (and will) form along any linear air path, even one which is significantly curved.
I don't know enough about this gyroidal lattice... does is suppress resonances due to its magic shape rather than by the process of absorption?
j.
I don't know enough about this gyroidal lattice... does is suppress resonances due to its magic shape rather than by the process of absorption?
j.
No it's not magic. It is not bad at absorbing sound down to 1000Hz or so in this testing.I don't know enough about this gyroidal lattice... does is suppress resonances due to its magic shape rather than by the process of absorption?
https://shura.shu.ac.uk/34121/1/Final cleaned paper .pdf
Plus the resonances that remain will most certainly be spread over a wide area, because there hardly are dominant pathway lengths.
I found this in another paper this was a baseline impedance test of polyester
It looks a lot like the gyroid lattice results above. In my own testing polyester was nearly useless at supressing resonances so I would still have some skepticism that a gyroid infill for the majority of the speaker is better than using conventional absorbents.
One thing I did find interesting is that most wooden boxes are rectliniear for obvious reasons of construction. There is the suggestion that this makes the walls more likely to flex out and "breathe". I have seen some B&W cabinet simulations in one of their infomercial papers that showed that when the rear cabinet shape was rounded it performed better in that regard. This makes sense in the same way that creases and ribs in flat surfaces makes them stiffer.
The thought being that if the rear cabinet shape is designed with that in mind it could be made thinner without being less stiff than a normal wooden panel.
It looks a lot like the gyroid lattice results above. In my own testing polyester was nearly useless at supressing resonances so I would still have some skepticism that a gyroid infill for the majority of the speaker is better than using conventional absorbents.
One thing I did find interesting is that most wooden boxes are rectliniear for obvious reasons of construction. There is the suggestion that this makes the walls more likely to flex out and "breathe". I have seen some B&W cabinet simulations in one of their infomercial papers that showed that when the rear cabinet shape was rounded it performed better in that regard. This makes sense in the same way that creases and ribs in flat surfaces makes them stiffer.
The thought being that if the rear cabinet shape is designed with that in mind it could be made thinner without being less stiff than a normal wooden panel.
Yeah, I also think the box walls moving is far greater issue than sound inside the box, because it seems to cleanup just with some damping material quite nicely.
Simple observation from looking at driver impedance plot, it cleans nicely with some damping material inside, compared to what it is for an empty box. The little wiggle left on impedance plot are panel and cone resonances. Cone resonances are present on a free air impedance plot so easy to detect, and there isn't much we can do about them other than changing the driver.
Panel / box resonance can be detected by tightening and loosening driver holding screws, which tunes the box like an instrument, and the remaining wiggle on impedance plot move higher or lower in frequency, but don't go away. This is easy to detect by hand as well, use tone generator and find frequency where say a back panel seems to vibrate, now loosen some screws on the driver with your other hand and the vibration seems to be gone, good riddance, adjust the tone generator only to find out the resonance moved lower in frequency.
Getting rid of box resonance is very tough, perhaps impossible, so the good old rules of thumbo applies very well: stiffen to tune the box resonances high, above passoband for a bass woofer. Use relatively unstiff box for a mid to get the resonance below passband. Introduce damping.
For example, on a big two way woofer box I'm prototyping no matter how I tried to dampen driver / box interface, adjusted bracing, turned bracing into simple CLD, all the box resonances did just moved around in frequency with very little change on apparent magnitude. I would have to move the resonance more than an octave up to get the resonances above passband, ain't gonna happen unless I use some extreme methods to stiffen the box. Can you tune a guitar string for octave higher without snapping it? Only option left for retrofit solution would be to further examine how to dampen the resonances, perhaps CLD outside the box which doubles cost and weight without guarantee of help without great effort to optimize it, perhaps it just moves the resonances even lower in frequency. Or just don't care about it, perhaps it's already fine enough given the room would further affect sound on the bandwidth, so be sure to somehow quantify how severe / mild it is to get peace of mind 🙂 I think very stiff panels + CLD bracing for bass is logical next step to try for me.
From the get go one could: make it a three way and make the structure of bass enclosure very very stiff like with round shape, to really help push box resonances high up in frequency. Perhaps consider dual opposing drivers for bass to actually reduce resonances. Use any kind of lossy connections at any point that would help dampen the resonances, kill them faster. Perhaps this is not an issue for a small speaker.
Simple observation from looking at driver impedance plot, it cleans nicely with some damping material inside, compared to what it is for an empty box. The little wiggle left on impedance plot are panel and cone resonances. Cone resonances are present on a free air impedance plot so easy to detect, and there isn't much we can do about them other than changing the driver.
Panel / box resonance can be detected by tightening and loosening driver holding screws, which tunes the box like an instrument, and the remaining wiggle on impedance plot move higher or lower in frequency, but don't go away. This is easy to detect by hand as well, use tone generator and find frequency where say a back panel seems to vibrate, now loosen some screws on the driver with your other hand and the vibration seems to be gone, good riddance, adjust the tone generator only to find out the resonance moved lower in frequency.
Getting rid of box resonance is very tough, perhaps impossible, so the good old rules of thumbo applies very well: stiffen to tune the box resonances high, above passoband for a bass woofer. Use relatively unstiff box for a mid to get the resonance below passband. Introduce damping.
For example, on a big two way woofer box I'm prototyping no matter how I tried to dampen driver / box interface, adjusted bracing, turned bracing into simple CLD, all the box resonances did just moved around in frequency with very little change on apparent magnitude. I would have to move the resonance more than an octave up to get the resonances above passband, ain't gonna happen unless I use some extreme methods to stiffen the box. Can you tune a guitar string for octave higher without snapping it? Only option left for retrofit solution would be to further examine how to dampen the resonances, perhaps CLD outside the box which doubles cost and weight without guarantee of help without great effort to optimize it, perhaps it just moves the resonances even lower in frequency. Or just don't care about it, perhaps it's already fine enough given the room would further affect sound on the bandwidth, so be sure to somehow quantify how severe / mild it is to get peace of mind 🙂 I think very stiff panels + CLD bracing for bass is logical next step to try for me.
From the get go one could: make it a three way and make the structure of bass enclosure very very stiff like with round shape, to really help push box resonances high up in frequency. Perhaps consider dual opposing drivers for bass to actually reduce resonances. Use any kind of lossy connections at any point that would help dampen the resonances, kill them faster. Perhaps this is not an issue for a small speaker.
Last edited:
So to summarize: In a combination of mass size flexibity and alternating energy there are always resonances. So either no energy , which is not the objective, or absorption of resonance energy and/or push way outside of needed bandwidth .
With the bandwidth of audio pushing outside of bandwidth is in my view very difficult, so damping is the more feasible direction.
Energy propagates, so follow the path(s) and think it through. Same for materials, MDF(the version with a softer core) f.i. has an increase in damping with frequency, but its stiffness i.c. applied size makes it prone for first modes in the 200 to 600 hz. So stiffening to reduce the resonating size pushes frequency up and also in the increased damping of the material. And so on.
With the bandwidth of audio pushing outside of bandwidth is in my view very difficult, so damping is the more feasible direction.
Energy propagates, so follow the path(s) and think it through. Same for materials, MDF(the version with a softer core) f.i. has an increase in damping with frequency, but its stiffness i.c. applied size makes it prone for first modes in the 200 to 600 hz. So stiffening to reduce the resonating size pushes frequency up and also in the increased damping of the material. And so on.
Like tmuikku proposed, the approach should be fitting the application. Bass drivers: push panel resonances outside pass band. Mid drivers: use damping and decoupling techniques and small enclosures (reduce radiating surface). High frequency drivers are of no concern in this respect. This all is very old knowledge, look at B&W801 or KEF105.
Indeed nothing new in that discussion and still valid information, except this project is not a 3 way and the bass and midrange are handled by the same driver. In that sense the approach taken in the KEF LS50 of strategic bracing and decoupling or the old BBC approach of lighter weight panels and damping might be worth trying.
If possible try shape / bracing optimization with FEA or some other suitable simulation, but the result is likely something like this quote from Linkwitz:
https://www.linkwitzlab.com/frontiers_2.htm#N
”There are several ways to reduce modal panel vibrations. Because the vibration energy from the driver decreases rapidly with increasing frequency it is advantageous to push the panel vibration modes up in frequency where the excitation energy is small. This is best accomplished by increasing the panel stiffness, but often goes together with increasing the mechanical Q of resonance. Dampening the panel by using a constrained layer that dissipates energy will reduce Q. Panel stiffness is also obtained by extensive bracing. As my rule of thumb, no un-braced box panel area should be larger than 4 inch squared for 3/4 inch thick wood panels. That is a lot of bracing, but it pushes modes into the low kHz range. ”
https://www.linkwitzlab.com/frontiers_2.htm#N
”There are several ways to reduce modal panel vibrations. Because the vibration energy from the driver decreases rapidly with increasing frequency it is advantageous to push the panel vibration modes up in frequency where the excitation energy is small. This is best accomplished by increasing the panel stiffness, but often goes together with increasing the mechanical Q of resonance. Dampening the panel by using a constrained layer that dissipates energy will reduce Q. Panel stiffness is also obtained by extensive bracing. As my rule of thumb, no un-braced box panel area should be larger than 4 inch squared for 3/4 inch thick wood panels. That is a lot of bracing, but it pushes modes into the low kHz range. ”
I think this is a more practical perspective than the Linkwitz quote. For a subwoofer stiffness is the way to go but for wideband boxes not so much.I would have to move the resonance more than an octave up to get the resonances above passband, ain't gonna happen unless I use some extreme methods to stiffen the box.
These are KEF's FEA sims for no bracing and adding a cross brace. Stiffness went along with the frequency but it did nothing for magnitude or Q.
Then the sim for CLD damping between the brace and walls, looks good to me.
Thanks, that's from LS50 paper isn't it? There is some extra nugget of info in the text that damping was added also to walls and to decouple the driver, as I understand it. It's bit of confusing with the captions on the images.
"It was found that adding material with high mechanical resistance and low stiffness between the walls, baffle, driver and brace results in extremely effective suppression of the resonances. This arrangement proved highly effective at damping the wall resonances as can be seen from the modelled result shown in Figure 10. A"
edit. end of the paper is cutout image showing how the bracing and damping is implemented:
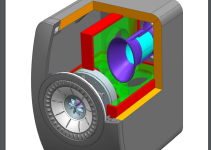
But yeah the main piece is that damping is needed to reduce the resonances. In my case I haven't been able to come up with as effective solution what KEF demonstrates here, and all of it is middle of pass band making it quite an issue. I'm afraid it will cost time and money to figure out what to do with it. Which was to be expected, something that seems to always happen when trying to pull it through with hopium 😀 Always prototype, and read KEF papers.
ps. the paper mentions that acoustic transmission through box is quite much less compared to what mechanical vibration from driver makes. Not sure what the actual conditions are here but it suggests that mechanical vibration of the box parts is the issue, while what happens inside the box less so.
"It was found that adding material with high mechanical resistance and low stiffness between the walls, baffle, driver and brace results in extremely effective suppression of the resonances. This arrangement proved highly effective at damping the wall resonances as can be seen from the modelled result shown in Figure 10. A"
edit. end of the paper is cutout image showing how the bracing and damping is implemented:
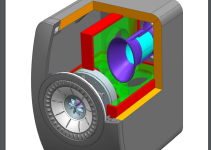
But yeah the main piece is that damping is needed to reduce the resonances. In my case I haven't been able to come up with as effective solution what KEF demonstrates here, and all of it is middle of pass band making it quite an issue. I'm afraid it will cost time and money to figure out what to do with it. Which was to be expected, something that seems to always happen when trying to pull it through with hopium 😀 Always prototype, and read KEF papers.
ps. the paper mentions that acoustic transmission through box is quite much less compared to what mechanical vibration from driver makes. Not sure what the actual conditions are here but it suggests that mechanical vibration of the box parts is the issue, while what happens inside the box less so.
Attachments
Last edited:
- Home
- Loudspeakers
- Multi-Way
- Wide Directivity 2 way compact Speaker T34A Waveguide and Purifi 6.5 Aluminium