How many people have an interest in purchasing a SS platter for the MK2?
I could see about another batch of 10 or 20 if there is interest.
Looks like the interest is already around 10?
The Boston mat that is no longer made or the original rubber.
ART [Italy] introduced solid-carbon mats to Europe long before Boston sold a similar mat. I was a very early UK user (on a SP-10 MkII)....I tried many mats that were around 20 plus years ago. Only two stood out, the solid carbon 'ART' and a Spectre mat from France. One was hard, the other extremely soft and floppy, yet they were both exceptionally good. Luigi Basagni at ART (Audio Reference Technology) may still have them.
<http://www.art-hifi.com>
Otherwise it should be possible to have a batch of similar mats made, but remember that they need to be made from the densest fine grain carbon and that 1/4" thickness is the minimum. [I would go for 3/8" to 1/2"]. Unless you have a full dust removal system do NOT attempt to machine this stuff yourself....it is a carcinogen
I still have x2 1" carbon blanks...one is destined for my Lenco, the other I am considering bonding to a SP-10 platter [having reduced the rim to flat.]
Any attempts to replace the platter damping?
I have had around ten SP10 mk II pass through my hands over the last 15 years or so. I'm a big fan and have 3 in my system at the moment and 2 more as spares/parts donors. Now here's the issue. Of the 10 I have played with over the years, 2 have had the damping layer start to lift. One was a serious detachment, but not surprising since it was an ex radio station workhorse with obvious signs of a liquid spill beneath the platter. It looked like coke or coffee. This appeared to soften the glue and hence the lifting. I bought it as a parts donor for little money so no real drama.
Now the latest issue was one of my working SP10's started making a very faint ticking noise once a revolution. You had to be right next to the table to notice. After pulling off the platter, I noticed a very slight unevenness with my finger moving from one half of the damping layer to the other. Sure enough the layer had lifted very slightly. Searching the chassis beneath I found a protruding screw thread from a brass circuit stand-off had a slight polish. It was barely 0.5 mm above the chassis but this was enough to contact the lifting damping layer. I just replaced the platter with a spare and problem solved.
BUT 2/10 is a significant failure rate. Any one else experienced lifting damping?
This got me thinking about replacing the damping by a superior material. Surely there is something better after all this time. I don't know whether it would be audible. The stock material seems to do a good job on the platter. It looks like removing the stock damping leaves partitioned areas in the platter casting that could be filled with a new damping layer such as polyester resin. The platter would probably need rebalancing.
I have had around ten SP10 mk II pass through my hands over the last 15 years or so. I'm a big fan and have 3 in my system at the moment and 2 more as spares/parts donors. Now here's the issue. Of the 10 I have played with over the years, 2 have had the damping layer start to lift. One was a serious detachment, but not surprising since it was an ex radio station workhorse with obvious signs of a liquid spill beneath the platter. It looked like coke or coffee. This appeared to soften the glue and hence the lifting. I bought it as a parts donor for little money so no real drama.
Now the latest issue was one of my working SP10's started making a very faint ticking noise once a revolution. You had to be right next to the table to notice. After pulling off the platter, I noticed a very slight unevenness with my finger moving from one half of the damping layer to the other. Sure enough the layer had lifted very slightly. Searching the chassis beneath I found a protruding screw thread from a brass circuit stand-off had a slight polish. It was barely 0.5 mm above the chassis but this was enough to contact the lifting damping layer. I just replaced the platter with a spare and problem solved.
BUT 2/10 is a significant failure rate. Any one else experienced lifting damping?
This got me thinking about replacing the damping by a superior material. Surely there is something better after all this time. I don't know whether it would be audible. The stock material seems to do a good job on the platter. It looks like removing the stock damping leaves partitioned areas in the platter casting that could be filled with a new damping layer such as polyester resin. The platter would probably need rebalancing.
Platter damping issues
I also had the same problem - one corner of one of the damping sheets had started to come loose, causing a very slight noise each revolution.
I simply pried it up a bit, put in a little superglue, and weighted it down while it dried. Seems to have worked fine.
I would also guess that the platters were balanced at the factory after the damping was applied, and replacing the damping would potentially jeopardize that balancing.
Best regards,
Mike
I also had the same problem - one corner of one of the damping sheets had started to come loose, causing a very slight noise each revolution.
I simply pried it up a bit, put in a little superglue, and weighted it down while it dried. Seems to have worked fine.
I would also guess that the platters were balanced at the factory after the damping was applied, and replacing the damping would potentially jeopardize that balancing.
Best regards,
Mike
It is time to start this incredible intellectual machinery again. I've been stuck with designing and creating a plinth for the table.
What do you think would be a good alternative to highly rated panzerholz plinth?
I would not ming get a sheet/two of it, but it seems very difficult to obtain, extremely difficult to route at home and as I can imagine extremely expensive
.
As an alternative I was thinking of something like bamboo ply wood or a composite laminate made of 1/4" HDF, MDF glued by epoxy. Can even route some cavities and feel with some sort of resin and sand in it.
Any suggestions opinions please?
What do you think would be a good alternative to highly rated panzerholz plinth?
I would not ming get a sheet/two of it, but it seems very difficult to obtain, extremely difficult to route at home and as I can imagine extremely expensive
As an alternative I was thinking of something like bamboo ply wood or a composite laminate made of 1/4" HDF, MDF glued by epoxy. Can even route some cavities and feel with some sort of resin and sand in it.
Any suggestions opinions please?
Yes, Panzer is incredibly expensive. in excess of $1000/sheet if I recall correctly, it's been a while since I've looked.
This is baltic birch with cavities drilled out and filled with lead shot, thence epoxied in.
I think the idea of Bamboo is really interesting. Perhaps with a HDF bottom layer. The consensus on MDF is to just stay away from it.
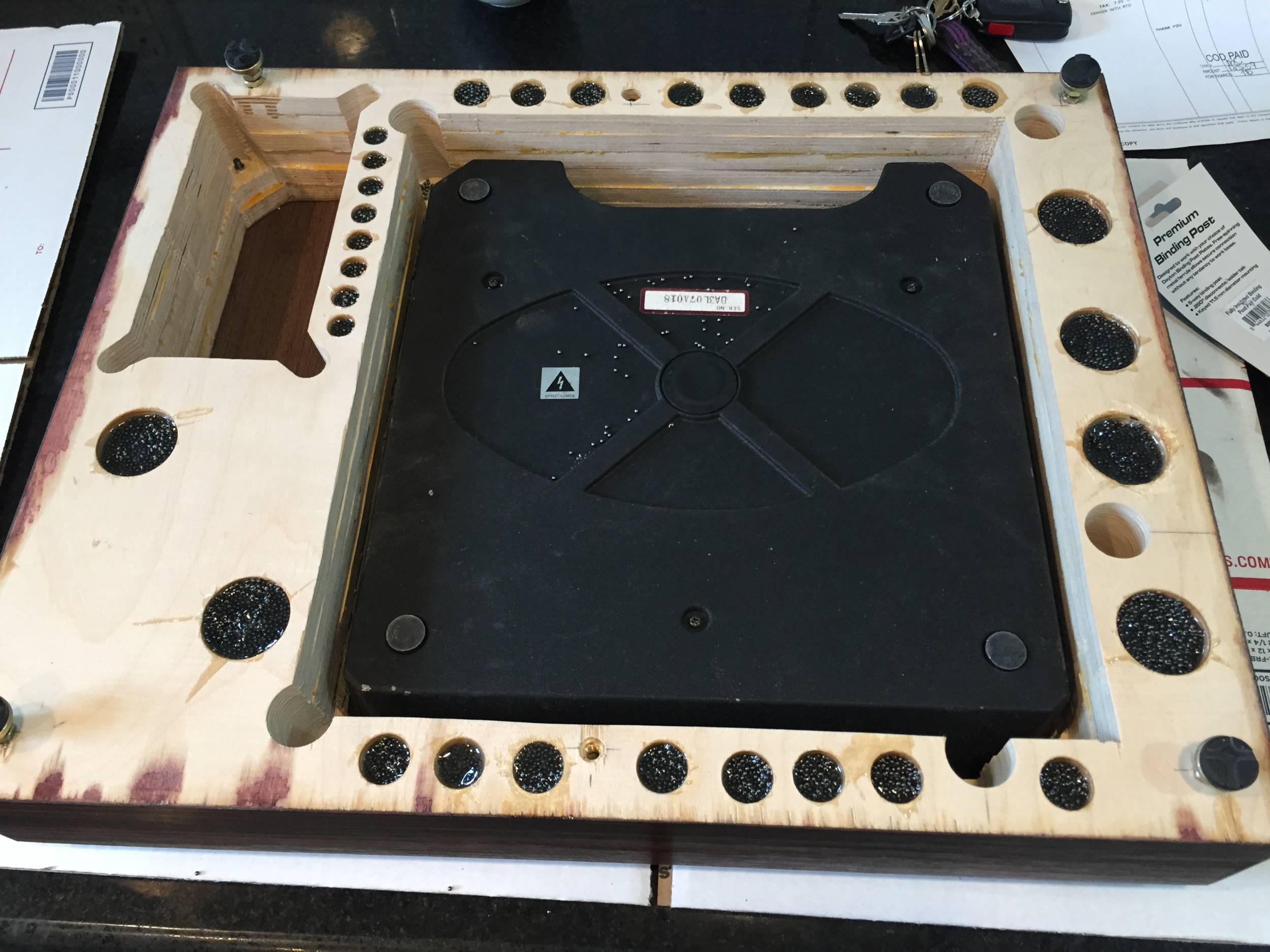
This is baltic birch with cavities drilled out and filled with lead shot, thence epoxied in.
I think the idea of Bamboo is really interesting. Perhaps with a HDF bottom layer. The consensus on MDF is to just stay away from it.
It is time to start this incredible intellectual machinery again. I've been stuck with designing and creating a plinth for the table.
What do you think would be a good alternative to highly rated panzerholz plinth?
I would not ming get a sheet/two of it, but it seems very difficult to obtain, extremely difficult to route at home and as I can imagine extremely expensive.
As an alternative I was thinking of something like bamboo ply wood or a composite laminate made of 1/4" HDF, MDF glued by epoxy. Can even route some cavities and feel with some sort of resin and sand in it.
Any suggestions opinions please?
there are lots of different avenues to take. However when it comes to designing a plinth for the SP10 mkII it is impossible to ignore the rather large foot print needed. And then there is that planar shape that requires a unique approach. And then there is the platter diameter, which is larger than most. And that the thing was designed originally around a 10 inch tonearm. All of these things dictate an approach that is not like other projects.
I think there is a tendency toward brute force, high mass constrained layer damping. Although we have seen some take the path of casting unique resins.
But given the above. And a rather limited budget I chose to take a path somewhat different from the current convention. And Panzerholz is not really in my budget. So I chose Baltic Birch Multi-ply and did this:

I chose to go lowest possible mass while meeting the needs for ridgidity and, hopefully, quick vibration energy dispersal.
The end result turned out better than I had planned. The sonic traits in this plinth are for fast transients. Excellent detail in crisp articulation.
That was almost 5 yrs back and I'm still happy with the result.
-Steve
Thanks Steve! As I understands there is nothing in between those layers? Very interesting, need to consider something lie that maybe. Not mentioning it looks very nice and stands out among traditional plinth.
Yes. Nothing but air. although a quick study will find additional bracing in areas where support is needed. Example, each of the 5 bolt holes have a solid build up of layers to allow for the compression of the bolt tightening. The armboard area has more mass than it might appear. Stuff like that.
-Steve
That said, plain ol Russian or Finnish ply sounded better.
Cyclotronguy.
Thank you, got it! Need to find suppliers here
Last edited:
Most cabinet shops have the various incarnations we call baltic ply. Finnish, Russian and etc.
Ditto for Boat and aircraft constructors, ie Aircraft Spruce
Even my model of customer service "McMaster Carr".
NOT HOME DEPOT / LOWES. What they call Baltic Birch is a far cry from the premium stuff. Hint: The good stuff all seems to come in 2m x 2m sheets not 4' x 8'
Cyclotronguy
Ditto for Boat and aircraft constructors, ie Aircraft Spruce
Even my model of customer service "McMaster Carr".
NOT HOME DEPOT / LOWES. What they call Baltic Birch is a far cry from the premium stuff. Hint: The good stuff all seems to come in 2m x 2m sheets not 4' x 8'
Cyclotronguy
- Home
- Source & Line
- Analogue Source
- The Incredible Technics SP-10 Thread