Teflon is soft and "tears". See if you can find loaded Nylatron (delrin). Some formulas have graphite or molydisulphide at 10 or 15%. The best is VESPEL, a dupont product. Look on Ebay U.S.A. Just make sure you are sitting down when you see the price !!!! Torlon and PEEK are other very good materials. Depends how serious you are with this bearing design. It would be easier IMHO to bite the bullet and get jeweled bearings and carbide / hardened steel axles / pivots. I used Vespel for my turntable bushing and polished micrograin carbide for the spindle / shaft.
Good luck,
Joe
Good luck,
Joe
Problem is I have been unable to source jewel VEE pivots here in Aus, it might be easy for you folk in NA. I have a machine shop so I can make easier than trying to source OS.
I do not think plastic, be it teflon or delrin will be good for VEE pivots, the material is too soft. Even anodized aluminium I do not think will be good. While the anodizing is extremely hard it is very thin and will still allow the base aluminium to compress.
IMO the only diy alternative is brass or stainless for the VEE's and HSS for the pivot pin.
If using stainless for the VEE it could be machined, polished then hardened. HSS is already hard and can be easily ground. Old drills will work as pivot pins.
I do not think plastic, be it teflon or delrin will be good for VEE pivots, the material is too soft. Even anodized aluminium I do not think will be good. While the anodizing is extremely hard it is very thin and will still allow the base aluminium to compress.
IMO the only diy alternative is brass or stainless for the VEE's and HSS for the pivot pin.
If using stainless for the VEE it could be machined, polished then hardened. HSS is already hard and can be easily ground. Old drills will work as pivot pins.
One of my first attempts at vee bearings used Teflon. Although Teflon has a very low coefficient of friction it is very soft. This resulted in the contact point with the pivot being large. The distance from the centre of rotation to the edge of the contact point is also much larger than for a hard material. This results in a greater frictional torque. Also being soft reduces mechanical grounding.
Sorry Teflon really doesn't work in this application.
Niffy
Sorry Teflon really doesn't work in this application.
Niffy
One of my first attempts at vee bearings used Teflon. Although Teflon has a very low coefficient of friction it is very soft. This resulted in the contact point with the pivot being large. The distance from the centre of rotation to the edge of the contact point is also much larger than for a hard material. This results in a greater frictional torque. Also being soft reduces mechanical grounding.
Sorry Teflon really doesn't work in this application.
Niffy
Thanks
The anodization, especially the hard+teflon one is not a simple embellishment, but a surface treatment, a kind of hardening widely used in industry. On sailboats e.g. there are winches, pulleys, sliders working for decades under heavy loads + sand&salt wear. (from direct experience). Using a spring for contact, our loads would be much more contained.
The problem is anodizing; having my gadgets anodized by a workshop nearby, I can say almost nothing, but a friend used an ebay kit with excellent results. The crucial stage is the final sealing: normally into boiling water, but the heated pivots themselves could be rotated against the vees to obtain a perfect and smooth seat. A few turns with diamond powder for the break-in, could help too.
maybe - carlo
The problem is anodizing; having my gadgets anodized by a workshop nearby, I can say almost nothing, but a friend used an ebay kit with excellent results. The crucial stage is the final sealing: normally into boiling water, but the heated pivots themselves could be rotated against the vees to obtain a perfect and smooth seat. A few turns with diamond powder for the break-in, could help too.
maybe - carlo
Attachments
I have sent a request for 50pc of this to jewel bearing, jewel bearing direct from Jingpeng Machinery & Equipment (Shanghai) Co., Ltd. in CN
Maybe we can split it in smaller portions (group buy?)
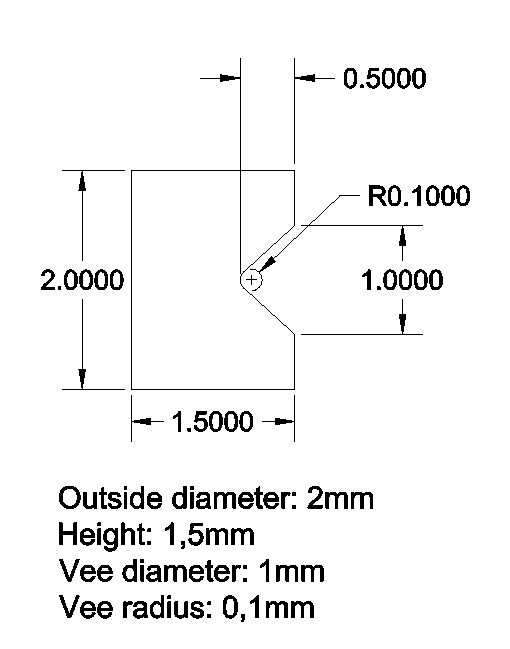
Maybe we can split it in smaller portions (group buy?)
0.1mm radius is a little small. Maybe see if they can do 0.2mm - 0.25mm.
You can probably get away with 0.1mm if you have a pivot radius of 0.075mm which is a bit larger than the normally recommended 1:2 - 1:3 ratio. A 0.05mm pivot would result in excessively high contact pressure and may limit bearing life expectancy.
Niffy
You can probably get away with 0.1mm if you have a pivot radius of 0.075mm which is a bit larger than the normally recommended 1:2 - 1:3 ratio. A 0.05mm pivot would result in excessively high contact pressure and may limit bearing life expectancy.
Niffy
I'm quoting myself here but...
The top part of the drawing shows such a solution. Why this is I don't know but I suspect that true point knows what they are saying. For a bigger pic see:
http://www.dahlbergaudiodesign.se/images/linear_8.png
Edit: When applying this way of thinking a holed jewel with a hole the same radius as the contact radius of the vee schould function similarly. The smallest holed one from true point was 0,3mm, therefore in the drawing.
From true point:
Notes: When used horizontally, the pivots should not bottom against the radius of the jewel. A degree of looseness is required which is called 'end shake'.
![]()
The top part of the drawing shows such a solution. Why this is I don't know but I suspect that true point knows what they are saying. For a bigger pic see:
http://www.dahlbergaudiodesign.se/images/linear_8.png
Edit: When applying this way of thinking a holed jewel with a hole the same radius as the contact radius of the vee schould function similarly. The smallest holed one from true point was 0,3mm, therefore in the drawing.
Last edited:
Edit: When applying this way of thinking a holed jewel with a hole the same radius as the contact radius of the vee schould function similarly. The smallest holed one from true point was 0,3mm, therefore in the drawing.
With a conical ring jewel + end cap the contact point will be smaller than your 2nd picture. A straight ring jewel will be similar but it has much higher contact surface and therefore friction.
A 0.3mm hole is very difficult to drill in a hard bearing.....
Maybe a 0,1mm brass 3D printer nozzle could work. 
1 Pieces 0.1mm 3D Printer Part Extruder Brass Nozzle Head For 1.75mm V6 Head Hot | eBay
1 Pieces 0.1mm 3D Printer Part Extruder Brass Nozzle Head For 1.75mm V6 Head Hot | eBay
I've been punching some numbers.
If you use sapphire vees with a cup radius of 0.1mm you will not be able to use tungsten carbide pivots with a tip radius of 0.05mm as the contact stress will be too high (a 2:1 ratio with the cup, as generally recommended). If you use steel pivots with a tip radius of 0.05mm the contact pressure will still be a little excessive. If you increase the radius of the tip of the pivot to 0.075mm the maximum contact pressure will be decreased to a just usable amount for carbide and a quite usable level for steel. I am assuming a 50g carriage mass and reasonably careful handling.
Brass would not be suitable for making pivots.
Even the finest tipped ball point pen has a tip that is way to big for this purpose. I used hardened sewing pins to make my first pivots. I used prym brand as these seem to be very high quality. I carefully rounded the tips to a radius of 0.125mm and then polished them. Rounding the tips to 0.075mm shouldn't be much more difficult. Use the shank of a 0.15mm drill bit as a visual reference. A microscope will help.
Finding tungsten carbide pivots in this size will not be easy.
Niffy
If you use sapphire vees with a cup radius of 0.1mm you will not be able to use tungsten carbide pivots with a tip radius of 0.05mm as the contact stress will be too high (a 2:1 ratio with the cup, as generally recommended). If you use steel pivots with a tip radius of 0.05mm the contact pressure will still be a little excessive. If you increase the radius of the tip of the pivot to 0.075mm the maximum contact pressure will be decreased to a just usable amount for carbide and a quite usable level for steel. I am assuming a 50g carriage mass and reasonably careful handling.
Brass would not be suitable for making pivots.
Even the finest tipped ball point pen has a tip that is way to big for this purpose. I used hardened sewing pins to make my first pivots. I used prym brand as these seem to be very high quality. I carefully rounded the tips to a radius of 0.125mm and then polished them. Rounding the tips to 0.075mm shouldn't be much more difficult. Use the shank of a 0.15mm drill bit as a visual reference. A microscope will help.
Finding tungsten carbide pivots in this size will not be easy.
Niffy
The problem is souring the VEE jewel. I have not been successful. True Point could offer S222 with radius of 0.08-0.1 which I thought I was too small they did not have S24 jewel with 0.5 radius. I emailed Swiss Jewel and never heard back.
Been thinking about to make VEE's, brass (the easily obtainable) I do not think is going to be hard enough. So thoughts went to O1 tool steel it's machinable and can be quenched hardened. Drill ends, the bit that goes in the chuck is not hardened and could possibly be used for the VEE, then hardened. Carbide inserts have the tip radius specified in the part number I have inserts with tip radius of 0.4mm to machine the VEE.
If all else fails back to ceramic ball race bearings.....
.
Been thinking about to make VEE's, brass (the easily obtainable) I do not think is going to be hard enough. So thoughts went to O1 tool steel it's machinable and can be quenched hardened. Drill ends, the bit that goes in the chuck is not hardened and could possibly be used for the VEE, then hardened. Carbide inserts have the tip radius specified in the part number I have inserts with tip radius of 0.4mm to machine the VEE.
If all else fails back to ceramic ball race bearings.....
.
Ok, first reply about the vee's.

Response:
Very nice to hear from you, I wasn't expecting such a quick response. I will have to get back to you
about the specifications but it will not change that much. It's the vee radius that might have to be a
bit bigger, somewhere around 0,2-0,3mm schould be close to the final order. All other as in the drawing.
If you could give me quotes for both 50, and as an alternative 100pc.
Best regards. Bengt Dahlberg
hello,
pleased to receive your inquiry, we can produce your drawing bearings.
How many pcs you need this time?
Welcome tell us sample quantity you like.
Thanks®ards
Linda
Response:
Very nice to hear from you, I wasn't expecting such a quick response. I will have to get back to you
about the specifications but it will not change that much. It's the vee radius that might have to be a
bit bigger, somewhere around 0,2-0,3mm schould be close to the final order. All other as in the drawing.
If you could give me quotes for both 50, and as an alternative 100pc.
Best regards. Bengt Dahlberg
Last edited:
....The no radius pivot is also easy to manage....
Does it mean doing? in which way? For such dimensions and tolerances watchmakers have to use a Jacot tool, and to know well how to. Just to burnish what previously made on their high precision lathes.
In our studio I drew along forty years with Rapidograph 0.1 mm, wondering how the hell they built them (a 0,1 tube with far smaller rod inside), and gaining an almost mystical respect for those capable of such tolerances. (dozens broken just to clean them). A < 0.1 mm smooth conical tip is far beyond my skill/tools: all my compliments, guys.
my 2 cents
Brass is not bronze, and bronze is for lubricated sliding bushings, too soft even for ball races. A 0,1 vee bearing will get a result similar to teflon (indent due load); but what would be increased friction on teflon (resilient), will be some play on brass. Hss on Hss - one of the principle of a sliding bearing is that one part has to be different, a bit softer than the other, with a smoothing, not gripping behavior. To make a jewel bearing seems to be needed a jewel
carlo
From web it seems that nobody has Vee jewel bigger than 2 mm. while rings and cups go up >> 5 mm . Strange, since vees are used for devices far bigger than watches
Does it mean doing? in which way? For such dimensions and tolerances watchmakers have to use a Jacot tool, and to know well how to. Just to burnish what previously made on their high precision lathes.
In our studio I drew along forty years with Rapidograph 0.1 mm, wondering how the hell they built them (a 0,1 tube with far smaller rod inside), and gaining an almost mystical respect for those capable of such tolerances. (dozens broken just to clean them). A < 0.1 mm smooth conical tip is far beyond my skill/tools: all my compliments, guys.
my 2 cents
Brass is not bronze, and bronze is for lubricated sliding bushings, too soft even for ball races. A 0,1 vee bearing will get a result similar to teflon (indent due load); but what would be increased friction on teflon (resilient), will be some play on brass. Hss on Hss - one of the principle of a sliding bearing is that one part has to be different, a bit softer than the other, with a smoothing, not gripping behavior. To make a jewel bearing seems to be needed a jewel
carlo
From web it seems that nobody has Vee jewel bigger than 2 mm. while rings and cups go up >> 5 mm . Strange, since vees are used for devices far bigger than watches
- Home
- Source & Line
- Analogue Source
- DIY linear tonearm