I've also run my vent spacers to the back minus panel thicknes. But, the idea is to screw and glue? In that case i think i have a removable back atm (somewhat removable with some need of violence i guess).
If one wanted to make the back functionally removable on the Fonken prime, an air-tight seal is required around the entire perimeter (otherwise venting performance would be significantly compromised).
The easiest way to achieve this would be to adjust dimension of cut parts and overlay the back, which would result in exposed ply edge grain. The more aesthetically appealing method would be to inset the back panel in rabbets in the sides and top/bottom, which is a bit more fiddly, and of course requires revision of parts dimensions and precision cutting and extra dry-fitting to confirm fit. ( masking tape is your friend)
Question guys, what's the best way to do the chamfers on the front?
Chamfer each piece individually before assembly, or assemble it without chamfers then run a circular saw on a 45 degree angle across it?
Chamfer each piece individually before assembly, or assemble it without chamfers then run a circular saw on a 45 degree angle across it?
Question guys, what's the best way to do the chamfers on the front?
Chamfer each piece individually before assembly, or assemble it without chamfers then run a circular saw on a 45 degree angle across it?
One cut if you have a big table saw. I have a small saw, so I did this in two steps. I cut the boxes and the front baffles separately. It only took a bit of sanding to match the big 45 chamfer after glue-up.
jeff
Definately do it in one pass. Find a friend with a standard table saw; you will be pleased with how easy it is as well as the results.
Doc
Doc
When i did my Mar-Kel70 i put them all together, then i took my circular saw and did the 45-degree cut. Worked very well 😀
Hi,
This might have been asked before but I havent seen it anywhere.
Whats the reason for the brace being offset to one side? Would it be ok to have it in the centre?
Cheers
19
This might have been asked before but I havent seen it anywhere.
Whats the reason for the brace being offset to one side? Would it be ok to have it in the centre?
Cheers
19
Hi,
This might have been asked before but I havent seen it anywhere.
Whats the reason for the brace being offset to one side? Would it be ok to have it in the centre?
Cheers
19
The short answer is to subdivide the panels in question into uneven areas with staggered natural resonant frequencies .
There is a much longer explanation, but it's late, and I'd not do it justice at the best of times.
Ah that explanation is fine, I was just wondering in laymans terms 🙂
What issue does having the brace central have? I've seen a lot designs with it this way still...
What issue does having the brace central have? I've seen a lot designs with it this way still...
Ah that explanation is fine, I was just wondering in laymans terms 🙂
What issue does having the brace central have? I've seen a lot designs with it this way still...
The degree of "issue" , and/or our thinking on why to offset the bracing might well serve as fodder for yet more expert discussion, but as it's the best I can do - in simple terms, unless you can completely eliminate all resonant energy in enclosure panels (and not create other "issues" in the process), with ( any number of) braces subdividing panels into smaller equal unrestrained surface areas, the resonant frequencies of the multiples will be the same, and will tend to beat together when excited by program content.
By offsetting bracing to create unequal subdivisions, each new smaller panel area will have a different resonant frequency - the variances may be very minor when the bracing is only off-center by the material thickness, but it is there none the less. By distributing the resonant energy in to a range of multiple and unequal frequencies, the thinking is that the beating or intermodulation of the panels will be less dissonant with program material.
or something like that
and of course, it could well be that any of a range of system variables could swamp the audibility of this effect on two pairs of otherwise identical speaker enclosures - that's something with which I've never experimented
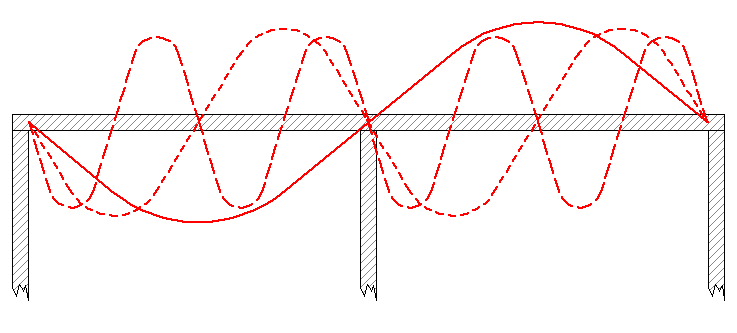
Putting the brace in the middle does not do a good job of killing the 1st resonance mode (and worst, if you ignore ballooning) as the brace is at its zero crossing. ie you are holding the panel in place, at the place where it isn't going to move anyway.
dave
Driver Rebate Method?
Sorry if I'm a little late to the party but I've been wanting to build a set of fonkens for a while and it's finally starting to happen. I'm up to the baffle as shown in the picture (hard to see but I have a decent chamfer routed into the back of the driver cutout), and I have a question: to rebate or not to rebate? I did some searching and it seems like it will make a audible difference, so if that's indeed the case, what's the best way for someone without a CNC router? I was thinking about cutting through the veneer with a razor along my driver tracing, and then using the router by hand with a straight bit and leaving maybe a 1/16" or so and chisel out the last little bit up to the razor cut. I'm worried about having an ugly cutout - I guess there's always wood putty to fill in if I make a mistake?
thanks!
wm
Sorry if I'm a little late to the party but I've been wanting to build a set of fonkens for a while and it's finally starting to happen. I'm up to the baffle as shown in the picture (hard to see but I have a decent chamfer routed into the back of the driver cutout), and I have a question: to rebate or not to rebate? I did some searching and it seems like it will make a audible difference, so if that's indeed the case, what's the best way for someone without a CNC router? I was thinking about cutting through the veneer with a razor along my driver tracing, and then using the router by hand with a straight bit and leaving maybe a 1/16" or so and chisel out the last little bit up to the razor cut. I'm worried about having an ugly cutout - I guess there's always wood putty to fill in if I make a mistake?
thanks!
wm
Attachments
Back when i was allowed to build boxes, i was rebating a lot of KEFs. Similar shaped bezels as the FE127. My router was/is a little tiny rockwell. With a small straight bit i got pretty good freehanding, never quite mistake free. Slow steady take just a little bit at a time till i hit the pencil line. Leaving a bit so you can go in with a dremel or chisel will work.
dave
dave
in the case of any of the Fostex stamped basket drivers ( i.e. FE & FF series), I'd be inclined to seal the driver in sandwich bag and mount face down when using this method, as the flange is quite thin and radiused on the face
the small ridged diffraction ring outside of the surround should raise the flange enough to provide a more secure surface against which to register the router base, and the plastic bag would keep nasty wood chips out of delicate places
of course I have the luxury of CNC programs for these patterns, so have never needed to test the above theory, but I have free-handed a few myself - always gratifying to know you can if needed
The above method, (w/driver-in a-bag!) is all we poor cnc-less northerners have to use!!
gotta love those MarkAudio drivers with round baskets!
best, don
gotta love those MarkAudio drivers with round baskets!
best, don
Thanks for all the replies! I think I could probably get there free hand, but I really like the template method you described and feel a lot safer going that way. Of course, just my luck, I have a Dewalt DW621 router which has a rectangular base.. I guess I'm off to buy a round replacement base, gives me an excuse to buy another tool - I'm sure it will come in handy on all kinds of other projects too (that's what I keep telling myself each time I have to buy something else I don't have).
wm
wm
Thanks for all the replies! I think I could probably get there free hand, but I really like the template method you described and feel a lot safer going that way. Of course, just my luck, I have a Dewalt DW621 router which has a rectangular base.. I guess I'm off to buy a round replacement base, gives me an excuse to buy another tool - I'm sure it will come in handy on all kinds of other projects too (that's what I keep telling myself each time I have to buy something else I don't have).
wm
like clamps - you can't have too many routers
hello guys,
just want to ask if this kind of enclosure will work well with merrill dca 4 drivers?
thanks
just want to ask if this kind of enclosure will work well with merrill dca 4 drivers?
thanks
If your pair are anything like the pairs i've measured, not really. Should be best in an aperiodic enclosure as large as you can live with.
dave
dave
- Home
- Loudspeakers
- Full Range
- New Fonken pair is born.