McMaster-Carr has an amazing selection of taps.
A tapping block is worth its weight in gold (even at today's gold prices).
Cutting oil is a must.
Tom
A tapping block is a good tool but if you have a drill press or milling machine here is a very good procedure.
Using a hammer and sharp punch make a mark with some depth (about 1 mm) where you want a tapped hole
Put a small center drill in the drill chuck and place the work piece on the drill table. Align the punch mark with the center drill.
Clamp the part to the table and drill a very shallow starter hole with the center drill. Drill only deep enough to make the punched mark a clean conical starter hole. The reason for the center drill is it will not walk like a thin diameter drill usually does.
Put the tap drill in the chuck and drill the hole to what ever depth you want.
You will probably need to lower the table for the next step to accommodate the combined length of the tap handle and tap.
Put the tap in a tap holder that has a center hole in the top. Put a small center, a worn out chamfer tool will work, in the chuck. Put cutting oil in the hole to be tapped. Put the tip of the tap in the hole and lower the spindle to engage the center with the tap handle center hole. Make sure the tap is vertical after lowering the table. If not make any table or work piece adjustments to ensure the tap and handle are vertical.
Begin tapping while applying light pressure with the spindle height adjustment handle. Follow the periodic cleaning described below.
Lubricating and cutting oils are a must. The following is especially important for tapping blind holes. Removing the tap a couple times before reaching final depth is important to allow removal of chips in the hole with a pipe cleaner and cleaning the tap with a tooth brush. Always apply more cutting oil when restarting the tape. For 1/2" depth I will probably repeat the cleaning and re-oiling two times. I even do the cleaning and re-oiling in thru holes. Taps stay sharp and last quite a while. TiN coating is a very good thing.
If you have drilling, sawing or milling equipment different oils are required for the various parts. Spindle oils are not to be used on gears and gear oils are not appropriate for machine ways.
A tapping block is a good tool but if you have a drill press or milling machine here is a very good procedure.
Using a hammer and sharp punch make a mark with some depth (about 1 mm) where you want a tapped hole
Put a small center drill in the drill chuck and place the work piece on the drill table. Align the punch mark with the center drill.
Clamp the part to the table and drill a very shallow starter hole with the center drill. Drill only deep enough to make the punched mark a clean conical starter hole. The reason for the center drill is it will not walk like a thin diameter drill usually does.
Put the tap drill in the chuck and drill the hole to what ever depth you want.
You will probably need to lower the table for the next step to accommodate the combined length of the tap handle and tap.
Put the tap in a tap holder that has a center hole in the top. Put a small center, a worn out chamfer tool will work, in the chuck. Put cutting oil in the hole to be tapped. Put the tip of the tap in the hole and lower the spindle to engage the center with the tap handle center hole. Make sure the tap is vertical after lowering the table. If not make any table or work piece adjustments to ensure the tap and handle are vertical.
Begin tapping while applying light pressure with the spindle height adjustment handle. Follow the periodic cleaning described below.
Lubricating and cutting oils are a must. The following is especially important for tapping blind holes. Removing the tap a couple times before reaching final depth is important to allow removal of chips in the hole with a pipe cleaner and cleaning the tap with a tooth brush. Always apply more cutting oil when restarting the tape. For 1/2" depth I will probably repeat the cleaning and re-oiling two times. I even do the cleaning and re-oiling in thru holes. Taps stay sharp and last quite a while. TiN coating is a very good thing.
If you have drilling, sawing or milling equipment different oils are required for the various parts. Spindle oils are not to be used on gears and gear oils are not appropriate for machine ways.
Not as precise as your method described above, but what I do is, after drilling the hole to depth with the tap drill, insert the tap into the drill press chuck, but not real tight. Lower the tap into the hole (drill press turned OFF) to be tapped and apply light pressure. Make a quick ON/OFF snap of the power switch. Depending on the hole you are tapping (material, thickness, tap size, through-hole or blind) you can use this method to start the tap straight in the hole and finish it off with a hand tap, or tap the complete hole.
If your drill press/mill has a reverse (mine doesn't 🙁), you can back out the tap when done. Quick and easy!
I've used similar methods on a milling machine that allowed the spindle speed to be reduced to something like 40-50 RPM. That works great for through holes. For blind holes you may be able to start the tap with the machine if you're really careful, but you'll have to finish by hand.
I agree with Henry that centring drills are good things.
Tom
I agree with Henry that centring drills are good things.
Tom
Hi Tom, I'm glad to help.The wonders of spring steel....
I still reckon it's worth a try to fit a small 'pad' of some non ferrous/non magnetic material between the spring clip and the top of the chip.
I have encountered situations where the spring clip is slightly twisted and this exerts uneven pressure across the device, with slightly uneven HS paste spreading....changing the pressure contact point to small and central would cure this possibility.
Raising the ferrous spring further away from the 'chip' may be of benefit also.
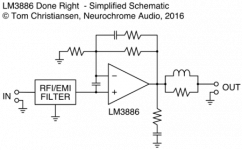
Any possibility of seeing closer detail ?.
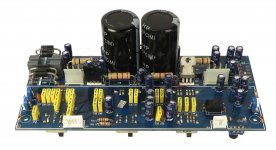
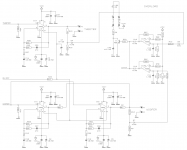
I have two pairs of Behringer B2031A as per the schematic above, and I am interested to modify one pair of amp modules according to your advices.
Notably there are no output networks.
Dan.
I have encountered situations where the spring clip is slightly twisted and this exerts uneven pressure across the device, with slightly uneven HS paste spreading....changing the pressure contact point to small and central would cure this possibility.
If the clip is bent, it would be wise to throw it away and blow $0.20 on another clip. In fact, I bet if you call up Mouser and let them know that you've received bent clips, they'd probably ship you another one for free.
Raising the ferrous spring further away from the 'chip' may be of benefit also.
Should I say anything? 😉
Any possibility of seeing closer detail ?.
No, but reading the LM3886 data sheet thoroughly will get you most of the values. The rest you'll have to find here in various recommendations made both by AndrewT and me.
I have two pairs of Behringer B2031A as per the schematic above, and I am interested to modify one pair of amp modules according to your advices.
Notably there are no output networks.
My boards should drop straight in, assuming there's room in the chassis.
Tom
I promise I won't write anything this long again but it's just my two cents on tapping
I have never used a powered spindle to tap a hole, blind or thru. I was a master tool and die maker for 13 years and never saw that done. In the tool rooms I worked in we all used a procedure similar to what I described or a small tapping press that would rest on a work bench. For large taps like 3/8" or more we would use either, the procedure described with a large tap holding bar (more torque), a larger tapping press or a mechanically driven tapping head on the appropriate machine.
Putting the tap in a chuck and rotating by hand is OK but some spindles have inherent torque due to connection to pulleys in the machine head. Just a little too much torque will quickly snap miniature taps like #2 thru #8. Also aluminum, copper and brass are considered "sticky metals". Cutting fluid is very important. As important is regular reversing of direction before the tap feels like its about to bind. Again, the cleaning/removal of chips is also important.
There are special tapping heads that are very sensitive and auto reversing, but those are usually used with 1/4" or larger taps and primarily when there are a large number of holes to be tapped. Further the taps, used on these machines, have a different design than regular hand taps. All my references are to tool room work. Production lines almost always have special automated tapping machines.
Bottom line...there is a reason a type of a tap is called a "hand tap". It is also the reason for so many different sized tap handles and tapping presses. Fine control of cutting torque on small hand taps is critical.
I have never used a powered spindle to tap a hole, blind or thru. I was a master tool and die maker for 13 years and never saw that done. In the tool rooms I worked in we all used a procedure similar to what I described or a small tapping press that would rest on a work bench. For large taps like 3/8" or more we would use either, the procedure described with a large tap holding bar (more torque), a larger tapping press or a mechanically driven tapping head on the appropriate machine.
Putting the tap in a chuck and rotating by hand is OK but some spindles have inherent torque due to connection to pulleys in the machine head. Just a little too much torque will quickly snap miniature taps like #2 thru #8. Also aluminum, copper and brass are considered "sticky metals". Cutting fluid is very important. As important is regular reversing of direction before the tap feels like its about to bind. Again, the cleaning/removal of chips is also important.
There are special tapping heads that are very sensitive and auto reversing, but those are usually used with 1/4" or larger taps and primarily when there are a large number of holes to be tapped. Further the taps, used on these machines, have a different design than regular hand taps. All my references are to tool room work. Production lines almost always have special automated tapping machines.
Bottom line...there is a reason a type of a tap is called a "hand tap". It is also the reason for so many different sized tap handles and tapping presses. Fine control of cutting torque on small hand taps is critical.
About 10 years ago I bought a 500 foot roll of OFHC 22awg copper wire. It was cheap and the smallest amount I could buy from a Mil certified supplier. OK I drank the Cool aid/snake oil. Over the years I've used maybe 50 feet and would love to use more. I'm thinking of using it from the LED lead to GND...just wrap one end around the GND screw in the chassis. Is this bad? I will use shrink tube over the joint at the LED lead.
Another thought on using bare wire for GND applications. I don't think skin effect means squat in that application...so let it oxidize. Am I nuts?
Wait a minuet. If skin effect is so important why are 3/8" or 1/2" diameter X 6 foot long grounding rods driven into the ground at almost all homes. Wouldn't oxidation eventually make them malfunction? What am I missing here?
Wait a minuet. If skin effect is so important why are 3/8" or 1/2" diameter X 6 foot long grounding rods driven into the ground at almost all homes. Wouldn't oxidation eventually make them malfunction? What am I missing here?
Last edited:
Tom,
Re: the Mod86
I'm listening to Pat Metheny's UNITY and it sounds amazing. As I mentioned the speakers are decoupled from the floor yet the whole room vibrates. Fantastic and the soundstage is great.
Re: the Mod86
I'm listening to Pat Metheny's UNITY and it sounds amazing. As I mentioned the speakers are decoupled from the floor yet the whole room vibrates. Fantastic and the soundstage is great.
Last edited:
About 10 years ago I bought a 500 foot roll of OFHC 22awg copper wire. It was cheap and the smallest amount I could buy from a Mil certified supplier. OK I drank the Cool aid/snake oil. Over the years I've used maybe 50 feet and would love to use more. I'm thinking of using it from the LED lead to GND...just wrap one end around the GND screw in the chassis. Is this bad? I will use shrink tube over the joint at the LED lead.
The wire is fine. You need to run the LED+resistor from one of the GND terminals on the Power-86 to one of the (-) terminals on the Power-86. As long as the anode end of the circuit connects to the GND terminal and the cathode end to the (-) terminal, you're good. The cathode of the LED is marked with a shorter lead.
The reason the VEE supply is loaded by the LED is that the MUTE signal for the LM3886 is derived from the negative rail, thus, to avoid thumps, the VEE rail needs to collapse before the VCC rail if they don't go away simultaneously. By loading the VEE (negative) rail with the LED, it will see a larger load and discharge faster than the VCC rail.
Another thought on using bare wire for GND applications. I don't think skin effect means squat in that application...so let it oxidize. Am I nuts? [...] What am I missing here?
I think you've misunderstood the concept of skin effect, maybe due to the influence of Kool-Aid 🙂. In a conductor, alternating current in the centre of the conductor will set up eddy currents within the conductor. These eddy currents will reinforce the current density near the edge of the conductor. At very, very low frequency - say DC - the current is distributed evenly in the conductor. As the frequency is increased, the eddy currents form and the current starts crowding near the surface of the conductor. At RF most of the current flows in a conductive "skin" near the surface of the conductor. This is why RF wire is often made from silver clad steel. The vast majority of the current flows in the silver. The insulation plays no role in this. It just sits there. The DC potential of the wire plays no role. It is the AC current flowing in the wire that causes the skin effect.
Wikipedia has more detail: https://en.wikipedia.org/wiki/Skin_effect
Tom
Last edited:
Thanks Tom,
I think I understand where the LED leads go. I was just trying to describe what I thought was an unimportant aspect of skin effect in some applications... specifically a bare ground wire that oxidizes over time.
I thought it would act as a conductor until it oxidizes to the point where it is essentially a broken or cut wire. Am I missing something? Wouldn't surprise me.
I think I understand where the LED leads go. I was just trying to describe what I thought was an unimportant aspect of skin effect in some applications... specifically a bare ground wire that oxidizes over time.
I thought it would act as a conductor until it oxidizes to the point where it is essentially a broken or cut wire. Am I missing something? Wouldn't surprise me.
Considering that you still find knob-and-tube wiring in old houses, intact and working well 100 years after it was installed, I wouldn't worry about the oxidation of the wire. In theory you're right, though. If the conductive layer turns to oxide it won't conduct very well if at all.
Tom
Tom
The 116 year old knob and tube in my house looks good and tests well. I think a 22awg ground wire in a stereo amp will be conductive after I'm in the ground.
Spring steel bending often is not precision.If the clip is bent, it would be wise to throw it away and blow $0.20 on another clip......
In my experience they are never bent exactly straight/parallel.....I have fixed thermal failure faulty gear because of this.
There are divided 'finger' springs and single contact point versions that are better.
A 'modification' single correctly placed contact pressure point would eliminate any doubt.
What's to lose ?.Should I say anything? 😉
Henry, you have keen ears and you have some titanium sheet, cut a little 5mm square, and find 5 seconds to slot it into place.
Try a bunch of metallic and non metallic materials same size, try varying the size....
Ok thanks.No, but reading the LM3886 data sheet thoroughly will get you most of the values. The rest you'll have to find here in various recommendations made both by AndrewT and me.
I don't want to derail your thread, and respect/nice work in coming out with nicely engineered, high performance, reliable and sensible range of psu/amp modular solutions for the enthusiast/DIYer.
Lol, there are enough photos available for me to reverse engineer your schematic, but not quite your layout effort.....missing the underside of your board, bugger.
This is my invitation for you to say your stuff about audio high current/earthing layout considerations and explain your design decisions regarding this current layout and further explain your component types/values choices.
This would be nicely educational for all, and would likely increase buyer interest. 😎
My boards should drop straight in, assuming there's room in the chassis.
Tom
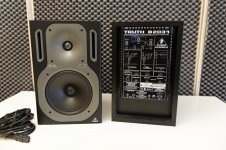
Ha, no not a chance.
For now, I have tweaked (ie totally changed) the internal acoustic damping arrangement and driver connection wires, but have very deliberately totally refrained from touching the electronics for the purpose of keeping the electronics in stock/factory condition.
The stock PCB layout/components is from hell.....BUT with a bunch of tricks (240V screened iso transformers, balanced audio feed, isolated USB Dac running on car battery power, my interesting filters, etc....) the sound of this system is seriously way cool.
These speakers have gone mostly as far as they can easily on the 'passive' side, and now is time to finesse the electronics.
So, this thread and your input inspires me to quite easily component add/swap out shift one pair of modules up a gear, win win, all good, thanks.
Dan.
Last edited:
To be honest if you have to ask with high performance composites you probably won't get it working as well. Took me about a nanosecond to realise I couldn't get within 10dB of the performance Tom has with the mod, let alone measure it. Made the boards a no-brainer to me. YMMV.I don't want to derail your thread, and respect/nice work in coming out with nicely engineered, high performance, reliable and sensible range of psu/amp modular solutions for the enthusiast/DIYer.
Lol, there are enough photos available for me to reverse engineer your schematic, but not quite your layout effort.....missing the underside of your board, bugger.
This is my invitation for you to say your stuff about audio high current/earthing layout considerations and explain your design decisions regarding this current layout and further explain your component types/values choices.
This would be nicely educational for all, and would likely increase buyer interest. 😎
There are all the 'taming the LM3886' pages on Tom's site and all the posts in the chipamp forum. Plenty there for the DIY'er.
I would be very pleased to buy Toms boards, but I already have two sets of typical 'prosumer' 3886 based monitors with inbuilt line level crossovers/protection.To be honest if you have to ask with high performance composites you probably won't get it working as well. Took me about a nanosecond to realise I couldn't get within 10dB of the performance Tom has with the mod, let alone measure it. Made the boards a no-brainer to me. YMMV.
I don't expect to gain all that Tom has achieved, just a review of what the Behringer guys left out and optimal circuit values.
Yes, much reading of others experiences with 3886.There are all the 'taming the LM3886' pages on Tom's site and all the posts in the chipamp forum. Plenty there for the DIY'er.
For now I am keen to further optimise what I have....ie tweak one pair of modules and leave one pair in factory state and then do the comparisons with factory cabinets and tweaked cabinets.
How important is the Thiele series output network when running 10" speaker wires and standard dynamic speaker drivers ?.
Dan.
I would be very pleased to buy Toms boards, but I already have two sets of typical 'prosumer' 3886 based monitors with inbuilt line level crossovers/protection.
I don't expect to gain all that Tom has achieved, just a review of what the Behringer guys left out and optimal circuit values.
Just to be clear as this could be misread. You are not asking Tom to read the app notes for you and check that Behringer built it with recommended values to get spec sheet performance? I assume you have done that already?
In the mod86 Rev 1 is r14 the only resistor that needs changing to modify gain? I seem to have lost my build guide perhaps when changing jobs/email addresses.
Right now I am using no preamp. I have a phono section plugged straight into the amp. I believe that the dcb1 buffer I built using a tkd pot is robbing transparency. Without it, it's a bit loud....75 dB or so.
Would a gold point or khozmo be better or just lower gain?
Right now I am using no preamp. I have a phono section plugged straight into the amp. I believe that the dcb1 buffer I built using a tkd pot is robbing transparency. Without it, it's a bit loud....75 dB or so.
Would a gold point or khozmo be better or just lower gain?
Spring steel bending often is not precision.
In my experience they are never bent exactly straight/parallel.....I have fixed thermal failure faulty gear because of this.
I don't have production data on this, but at least in my N = 2 sample, the clip I recommended worked as intended.
What's to lose ?.
A bunch of time chasing a ghost. Time is my most valuable resource right now.
This is my invitation for you to say your stuff about audio high current/earthing layout considerations and explain your design decisions regarding this current layout and further explain your component types/values choices.
This would be nicely educational for all, and would likely increase buyer interest.
Thank you for the invitation. I am planning to put all that information on my Taming the LM3886 pages. It will have to wait as I have other irons in the fire right now, though.
As for the Thiele network: It is required if you're driving a capacitive load much beyond a few nF. For driving 20 cm of wire in an internal wiring harness to a dynamic driver, I wouldn't worry much about it. In an amp designed to drive whatever the customer connects at the speaker terminals, I think it's irresponsible to go without the Thiele network or some other solution to deal with capacitive loads.
Tom
In the mod86 Rev 1 is r14 the only resistor that needs changing to modify gain? I seem to have lost my build guide perhaps when changing jobs/email addresses.
Toss me an email and I'll get the doc to you. Please include your paypal email address and rough time you bought the boards so I can find you.
In Rev. 1.0, I recommended changing R14 to change the gain. You may get slightly lower noise if you change R13 instead.
R13 = 1k15 -> 26 dB gain
Gain(lin) = (1+R14/R13).
In Rev. 2.x, I recommend changing R12 to change the gain.
R12 = 1k05 -> 26 dB gain
Gain(lin) = (1+R13/R12).
Tom
- Home
- Amplifiers
- Chip Amps
- Modulus-86 build thread