Calibration tools are a great idea. +/- 0.12mm (or ~0.005") is a pretty standard low side tolerance and should be easy for any machine shop to hit in metal, but is also about twice the width of a human hair. Where were you thinking of getting your parts made?
It is a wonderful feeling to receive machined parts that fit together perfectly. But you're right, it can be pricey. There's a lot of prototype places popping up that can do great work for not a whole lot of money (relatively speaking). The problem with aluminum is it likes to ring. Makes for great chimes or tuning forks. If you make an enclosure with it, that means you'll have a high frequency first mode, but a large amplitude one too.
I did a quick simulation with my old model, as requested, using your 4.124" baffle edge dimension with 0.125" thick aluminum. First mode, as before with the back panels oscillating, is 2.57 KHz. With 0.25" walls it's 4.92 KHz. Maybe if you used some absorption material you could eliminate the modes of that construction.
It is a wonderful feeling to receive machined parts that fit together perfectly. But you're right, it can be pricey. There's a lot of prototype places popping up that can do great work for not a whole lot of money (relatively speaking). The problem with aluminum is it likes to ring. Makes for great chimes or tuning forks. If you make an enclosure with it, that means you'll have a high frequency first mode, but a large amplitude one too.
I did a quick simulation with my old model, as requested, using your 4.124" baffle edge dimension with 0.125" thick aluminum. First mode, as before with the back panels oscillating, is 2.57 KHz. With 0.25" walls it's 4.92 KHz. Maybe if you used some absorption material you could eliminate the modes of that construction.
So why don't make it thicker ? 1/8" is crazy thin
One inch or more should do fine 🙄
Or, I was considering going to magnesium due to the better stiffness to weight ratio...
If you ever wanted to get rid of them you could have one heck of a fire.
Folks may have forgotten already, but foam core makes a very nice and easy to build hypercube. The geometry is such that it is a very stiff structure despite the panels being so thin and lightweight. It sounds great and measures very well too.
http://www.diyaudio.com/forums/full-range/265053-hypercube-loudspeakers-12.html#post4128571
Here is response with a TC9FD:
It literally can be made in an hour with 1/3rd a sheet of foam core. I even made one for a 5in driver.
I even made a FAST with two hypercubes:
http://www.diyaudio.com/forums/full-range/265915-hyperfast-hypercube-based-2-way.html
You can get creative with how you arrange them:
http://www.diyaudio.com/forums/full-range/265053-hypercube-loudspeakers-12.html#post4128571
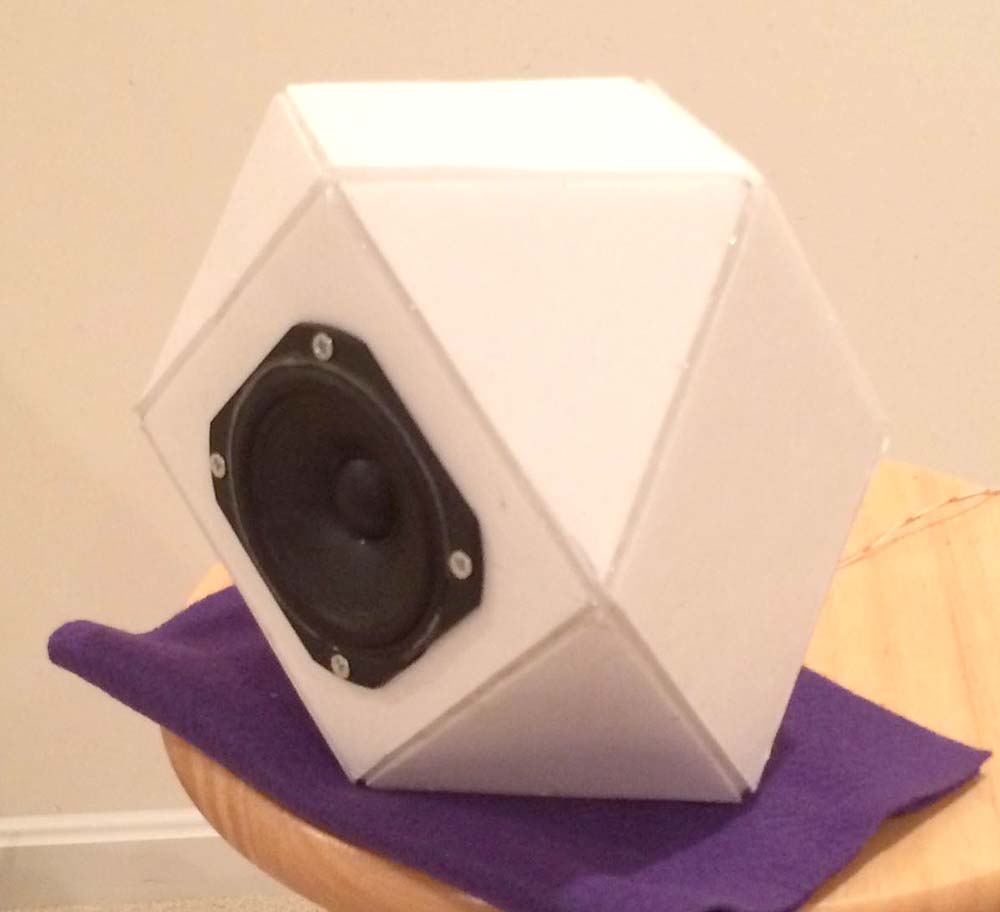
Here is response with a TC9FD:
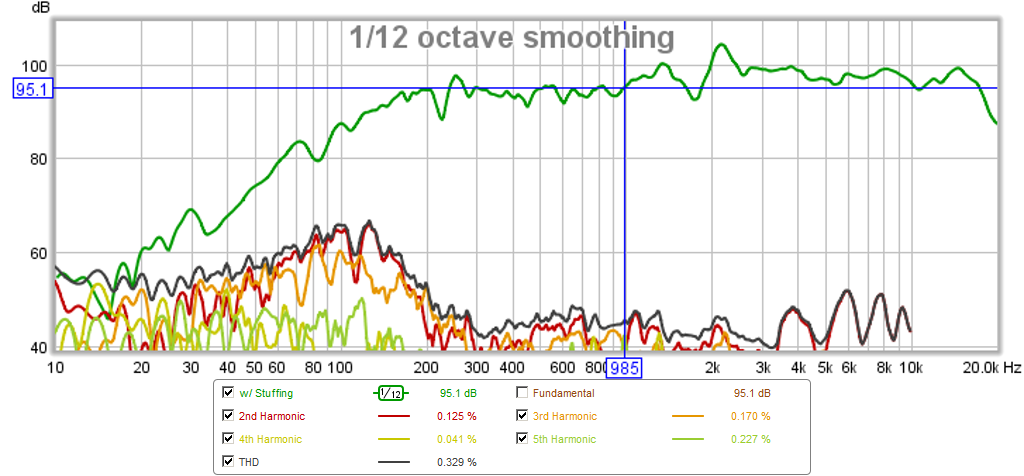
It literally can be made in an hour with 1/3rd a sheet of foam core. I even made one for a 5in driver.
I even made a FAST with two hypercubes:
http://www.diyaudio.com/forums/full-range/265915-hyperfast-hypercube-based-2-way.html
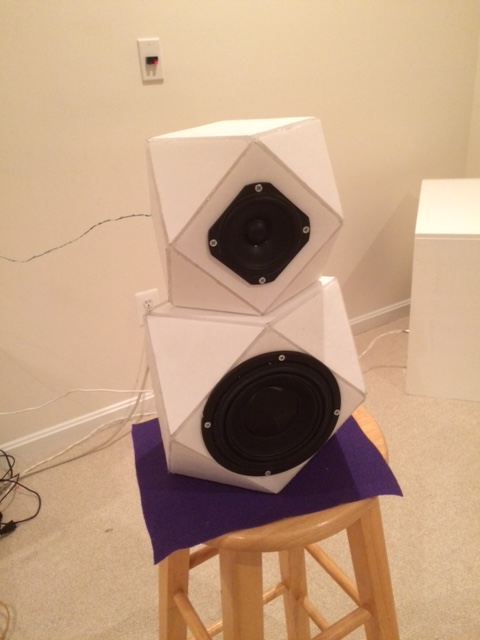
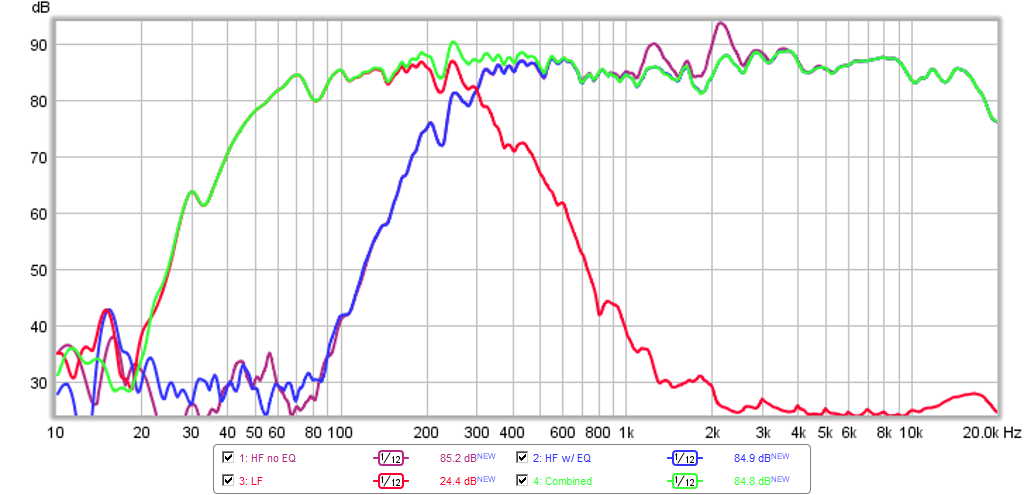
You can get creative with how you arrange them:
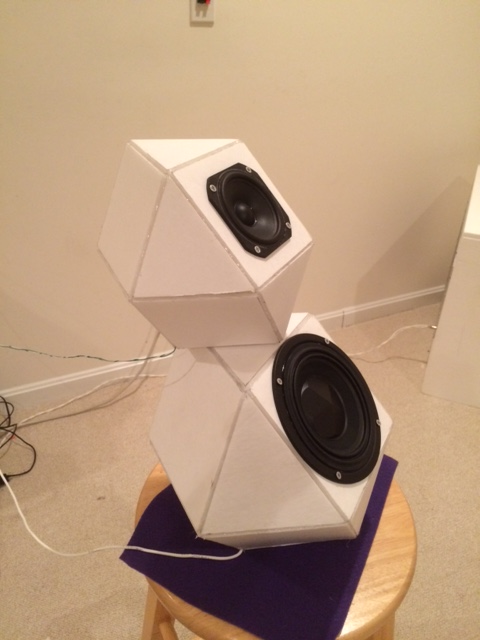
Last edited:
It sounds great and measures very well too.
you should make it your signature
Pico,
Not sure why you would make a snide comment like that - have I done something to get on your grumpy attitude list?
Not sure why you would make a snide comment like that - have I done something to get on your grumpy attitude list?
Calibration tools are a great idea. +/- 0.12mm (or ~0.005") is a pretty standard low side tolerance and should be easy for any machine shop to hit in metal, but is also about twice the width of a human hair. Where were you thinking of getting your parts made?
It is a wonderful feeling to receive machined parts that fit together perfectly. But you're right, it can be pricey. There's a lot of prototype places popping up that can do great work for not a whole lot of money (relatively speaking). The problem with aluminum is it likes to ring. Makes for great chimes or tuning forks. If you make an enclosure with it, that means you'll have a high frequency first mode, but a large amplitude one too.
I did a quick simulation with my old model, as requested, using your 4.124" baffle edge dimension with 0.125" thick aluminum. First mode, as before with the back panels oscillating, is 2.57 KHz. With 0.25" walls it's 4.92 KHz. Maybe if you used some absorption material you could eliminate the modes of that construction.
I had my acrylic pieces done through eMachineShop. Their prices seem ok and I actually like using the software that they provide. I drew the pieces by specifying the angles 70.53 and 109.47 deg. This method is not as accurate as my current method* (drawing a 1 : 1.41421 rectangle and inscribing a rhombus by drawing lines connecting the midpoints of adjacent sides). Despite this and despite not being able to request tight tolerances with acrylic, the pieces went together quite well but a couple of edges were very slightly off (a flat file worked pretty well here).
Wow, thanks for the sim. Amazing - first mode at ~5khz 🙂. So the question is, does a mode that is pushed higher in both amplitude and freq present any more of a problem. I found with my hypercubes that putting even a small piece of cloth or foam inside killed the ringing completely. I've actually been using them this way for a while although I listened to them mostly without any stuffing for a few months right after I made them. I was pretty certain at the time however that they lost a little bit of their "omni" character when stuffed but I also remember thinking the difference wasn't nearly as noticeable when listening from a typical distance (as opposed to holding them in your hands).
*it's been a while since I did this so I mentioned a slightly different method in my earlier post
Well, high frequencies tend to cause less movement, so that would probably help. Also, it would be easy to get absorption material that absorbs almost 100% that high. So I think it would make it easier to stop any ringing.
Pico,
Not sure why you would make a snide comment like that - have I done something to get on your grumpy attitude list?
Hey Xrk, do you know where I could get a template for the foam core hyper cube build? I've been lazy to assemble a cabinet to put my Ff85wk and SS 10F's into. This seems like a great, fast & unique first build.
Just ordered a DTA3116 amp to amp them with! Too lazy to finish my gainclone atm lol.😱
Last edited:
Hey Xrk, do you know where I could get a template for the foam core hyper cube build? I've been lazy to assemble a cabinet to put my Ff85wk and SS 10F's into. This seems like a great, fast & unique first build.
Just ordered a DTA3116 amp to amp them with! Too lazy to finish my gainclone atm lol.😱
Xrk, do you think the score and fold method would work for the hypercube? If so, I could try making plans for it.
Pic 1 is of a corner of my basement which was until recently taken up by a semi-abandoned oil tank. Sports cars are probably the more usual choice for midlife crises but I already have one of those 😉. Pic 2 is of 1/2" MDF pieces I just cut for a pair of FR135EX hypercubes. After I rout out the driver hole/recess, I will install brass threaded inserts for socket cap machine screws. Pic 3 is showing verification of the accuracy of the miter cuts using a printout of a drawing of the required angles.
Attachments
🙂 🙂 🙂....
Would love to have one of those...
🙂 Well, considering the prices machine shops charge, I felt it was justified.
Other than 'because we can' what's the actual benefit of building this very complex enclosure, instead of a well executed 'standard' cuboid design? 😕
Other than 'because we can' what's the actual benefit of building this very complex enclosure, instead of a well executed 'standard' cuboid design? 😕
I only became part of the "because we can" club recently. My first (and currently used) pair was assembled from professionally machined pieces. I was intrigued by the shape and the claims made about the performance, and wanted to decide for myself if there was something to it. Off the top of my head, here are some reasons that these are a worthwhile build for me:
- They seem to have good dispersion characteristics; they "disappear" even when listened to from fairly close range. They also sound good from the sides and rear, although that is probably partly due to what I mention next...
- Although there is a mild structural resonance (determined by the stiffness of the panels), the enclosure tends to resonate fairly evenly over a fairly broad range, and in some ways, they sound and measure better when no stuffing is used.
- Compared to a sealed and stuffed box of identical volume and twice the panel thickness, I have measured a reduction of both harmonic distortion and non-harmonic "noise" (appearing almost as "sidebands" surrounding the fundamental).
- They look really cool 😎
Without a doubt, these are more difficult and time consuming to build than standard boxes. Whether or not the extra effort (or cost) is worthwhile is of course up to each individual.
🙂 I haven't tried foamcore myself but here's how I might make the 13 pieces needed for each enclosure:
-choose an edge length (x) for the square baffle plate and cut one of these
-cut 10 rectangles with dimensions (x) X 1.414(x)**
-inscribe a rhombus in each rectangle by drawing lines connecting the midpoints of adjacent sides and cut these out
-cut two of the rhombi in half to create the four triangles
X, perhaps you have a better method. I think the possibility has been mentioned of creating a "net" and using a special v-shaped scoring tool. I guess once the RD is made we could just truncate one of the pyramids...
**alternately, and with less wasted material, you can cut a few rhombi from a strip with a width of .8165(x) by making parallel 70.53 degree cuts spaced apart by .866(x) (the edges of the strip become the edges of the rhombi).
-choose an edge length (x) for the square baffle plate and cut one of these
-cut 10 rectangles with dimensions (x) X 1.414(x)**
-inscribe a rhombus in each rectangle by drawing lines connecting the midpoints of adjacent sides and cut these out
-cut two of the rhombi in half to create the four triangles
X, perhaps you have a better method. I think the possibility has been mentioned of creating a "net" and using a special v-shaped scoring tool. I guess once the RD is made we could just truncate one of the pyramids...
**alternately, and with less wasted material, you can cut a few rhombi from a strip with a width of .8165(x) by making parallel 70.53 degree cuts spaced apart by .866(x) (the edges of the strip become the edges of the rhombi).
I use similar to latter technique of long strips cut by parallel lines but don't go by angles. Instead edge lengths defined by distances. It was real simple like 1 and 1.41 or something like that.
Right on. We don't need no stinking protractors. Starting from a corner, make marks along one of the edges of the strip spaced apart by .866(x) (the edge length of the rhombus). Do the same thing along the other edge except offset by .289(x). Connecting the dots should make the proper angle.
- Status
- Not open for further replies.
- Home
- Loudspeakers
- Full Range
- Hypercube Loudspeakers