I want to add an interesting article that discusses the Rockport Sirius 3 linear arm.
I have researched but I can’t find anything reference as to which air bushing the Rockport might be employing.
Rockport Technologies System III Sirius turntable and tonearm Page 3 | Stereophile.com
Also very interesting, in reviewing kuzma turntable there is another interesting article about the kuzma airline and makes reference once again to the rockport arm and discuss in small detail the "groove-compensated" air bearing.
They seem to be normalizing the air pressure at the anular gap thus reducing the high frequency ringing caused by the high pressure air turbolenze Of the standard bearing.
Kuzma Stabi XL turntable & Air Line tonearm Page 2 | Analog Planet
It would be interesting to know if anybody has any idea as to which airbearig is being used on the rockport for comparison with the new ne on the kuzma.
I have researched but I can’t find anything reference as to which air bushing the Rockport might be employing.
Rockport Technologies System III Sirius turntable and tonearm Page 3 | Stereophile.com
Also very interesting, in reviewing kuzma turntable there is another interesting article about the kuzma airline and makes reference once again to the rockport arm and discuss in small detail the "groove-compensated" air bearing.
They seem to be normalizing the air pressure at the anular gap thus reducing the high frequency ringing caused by the high pressure air turbolenze Of the standard bearing.
Kuzma Stabi XL turntable & Air Line tonearm Page 2 | Analog Planet
It would be interesting to know if anybody has any idea as to which airbearig is being used on the rockport for comparison with the new ne on the kuzma.
Kuzma uses 65 psi compressed air and Rockport uses 33 psi. As I said before, I am not air bearing expert and not sure what Micheal Fremer was talking about high frequency ringing. In my experience, the different air pressure will make significant difference sonically. Usually, high air pressure makes sound more dynamic and edgy while low pressure makes sound soft and smooth. I have tried different air pressures as low as 15 psi.
Re high frequency ringing
I'm no air bearing expert either but this is my take on what Micheal Fremer was talking about when he mentioned high frequency ringing.
The air in the gap of the bearing acts like a spring. The specifications of most air bearings has the stiffness of the bearing at different air pressures as one of the main points. And stiffness is the most important specification of a spring. Combined with the mass of the arm/carriage (or more accurately the rotational inertia of the carriage about its centre of mass) the stiffness of the air bearing will have a certain resonant frequency. Increasing the pressure will push this resonant frequency to a higher frequency. As the air gap is small the bearing tends to be very stiff even at low pressure. At low pressure the resonance is probably falling in the midrange causing a mild colouration that is heard as a softness. At high pressure the resonance is likely to fall in the treble leading to a false sense of dynamics and edge. Ideally we would like to have this resonance at a frequency where it is inaudible. The ultimate would be to have it above the audio band 20khz+. This would require the carriage to have a low moment of inertia and the bearing to be as stiff as possible. Making the arm light and short is the best way of reducing the moment of inertia. Increasing air pressure will increase the bearing stiffness. Larger diameter air bearings are also stiffer than smaller ones at the same pressure. Even if it is not possible to push the resonance above the audio band it should be possible to move it into the upper treble range where the ear is less sensitive. This would also mean that any harmonics would likely be outside the audio band. The addition of the damping trough should help to keep this resonance in check but will not eliminate it. I am of course only talking about enclosed bearings and not the terminator style open bearings that run at much lower pressure and probably have their resonant frequency in the bass area and harmonics through out the audio range.
Niffy
I'm no air bearing expert either but this is my take on what Micheal Fremer was talking about when he mentioned high frequency ringing.
The air in the gap of the bearing acts like a spring. The specifications of most air bearings has the stiffness of the bearing at different air pressures as one of the main points. And stiffness is the most important specification of a spring. Combined with the mass of the arm/carriage (or more accurately the rotational inertia of the carriage about its centre of mass) the stiffness of the air bearing will have a certain resonant frequency. Increasing the pressure will push this resonant frequency to a higher frequency. As the air gap is small the bearing tends to be very stiff even at low pressure. At low pressure the resonance is probably falling in the midrange causing a mild colouration that is heard as a softness. At high pressure the resonance is likely to fall in the treble leading to a false sense of dynamics and edge. Ideally we would like to have this resonance at a frequency where it is inaudible. The ultimate would be to have it above the audio band 20khz+. This would require the carriage to have a low moment of inertia and the bearing to be as stiff as possible. Making the arm light and short is the best way of reducing the moment of inertia. Increasing air pressure will increase the bearing stiffness. Larger diameter air bearings are also stiffer than smaller ones at the same pressure. Even if it is not possible to push the resonance above the audio band it should be possible to move it into the upper treble range where the ear is less sensitive. This would also mean that any harmonics would likely be outside the audio band. The addition of the damping trough should help to keep this resonance in check but will not eliminate it. I am of course only talking about enclosed bearings and not the terminator style open bearings that run at much lower pressure and probably have their resonant frequency in the bass area and harmonics through out the audio range.
Niffy
Thanks Niffy.
I think from what I have heard that rockport has a different design of airbrushing that allows it to run at lower pressure but yet to maintain the same high level of stiffness.
I am not an ME nor an airbearing expert so I tried to read some technical documentation around the net to try to get a little better understanding. Unfortunately there are no info on the Rockport design other than what I posted.
Since you have commented on the terminator, I own that tonearm already. It works decently well at very low air pressure. I must say that the lower the pressure the better it sounds but then it starts mistracking as you see the cantilever swaying left and right. So I can say that air pressure affects deeply the quality of the sound. I assume same would go with the kuzma arm.
Would it be safe to state that a kuzma design would perform better than terminator or not?
I think from what I have heard that rockport has a different design of airbrushing that allows it to run at lower pressure but yet to maintain the same high level of stiffness.
I am not an ME nor an airbearing expert so I tried to read some technical documentation around the net to try to get a little better understanding. Unfortunately there are no info on the Rockport design other than what I posted.
Since you have commented on the terminator, I own that tonearm already. It works decently well at very low air pressure. I must say that the lower the pressure the better it sounds but then it starts mistracking as you see the cantilever swaying left and right. So I can say that air pressure affects deeply the quality of the sound. I assume same would go with the kuzma arm.
Would it be safe to state that a kuzma design would perform better than terminator or not?
Last edited:
Hi Stefano,
The open bearing design as used by the terminator kind of works in the opposite way to the enclosed bearing of the kuzma and Rockport. With an open bearing the pressure in the gap is constant regardless of supply pressure. Changing the supply pressure only changes the air gap, a higher supply pressure will result in a greater gap. In theory the terminator should sound at its best with the lowest possible supply pressure as this will result in the smallest stiffest gap. Having a small gap will also make the arm more stable, a thicker layer of air will allow the arm to move around in undesirable directions.
The terminator style of arm does have a couple of points in its favour. They are considerably cheaper than the closed bearing designs. The air supply needs to be lower pressure so should be easier to build. As this is diyaudio, the entire open bearing design can be built at home. Building a closed bearing from scratch is definitely beyond my skills.
Ultimately the Kuzma should outperform the terminator.
Niffy
The open bearing design as used by the terminator kind of works in the opposite way to the enclosed bearing of the kuzma and Rockport. With an open bearing the pressure in the gap is constant regardless of supply pressure. Changing the supply pressure only changes the air gap, a higher supply pressure will result in a greater gap. In theory the terminator should sound at its best with the lowest possible supply pressure as this will result in the smallest stiffest gap. Having a small gap will also make the arm more stable, a thicker layer of air will allow the arm to move around in undesirable directions.
The terminator style of arm does have a couple of points in its favour. They are considerably cheaper than the closed bearing designs. The air supply needs to be lower pressure so should be easier to build. As this is diyaudio, the entire open bearing design can be built at home. Building a closed bearing from scratch is definitely beyond my skills.
Ultimately the Kuzma should outperform the terminator.
Niffy
I think from what I have heard that rockport has a different design of airbrushing that allows it to run at lower pressure but yet to maintain the same high level of stiffness.
Smaller gap between bearing and shaft will maintain high level of stiffness at low air pressure. But custom made shaft with tight tolerance is difficult to get for DIY. Here is an image from New Way air bearing to illustrate the advantage of porous material over air channels.
I have tested different air pressures on my arms. The best air pressure is probably 40-50 psi. I have tried 70 psi but don't see the reason to run air pressure this high.
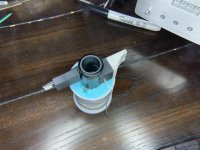
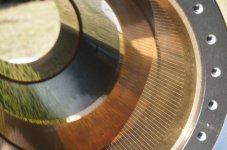
My Versa Dynamics and a big commercial air bearing of the same air distribution design principal.
A fingerprint on the shaft will give you an idea of how tight the tolerance is since it will stick in its presence.
The New Ways are an excellent alternative since no one has a centerless grinder
In their garage To do the O.D. let alone internal I.D. machining to match
Regards
David
Smaller gap between bearing and shaft will maintain high level of stiffness at low air pressure. But custom made shaft with tight tolerance is difficult to get for DIY. Here is an image from New Way air bearing to illustrate the advantage of porous material over air channels.
I have tested different air pressures on my arms. The best air pressure is probably 40-50 psi. I have tried 70 psi but don't see the reason to run air pressure this high.
I am inclined to try something a little different. I would like to do moving shaft similar to the Chinese implementation with two bearings but balancing the counterweight similar to the back diamond turntable.
My question is where can I inquire a custom ultra precision shaft? I know it could be expensive but I want at least know how expensive it could be.
Since it’s movimg shaft I assume the shaft cannot be solid stainless steel as the moving mass would be incredibly heavy.
But wouldn’t an hollow long shaft ring like a bell?
Now I am exploring different possibility and the most that catches is my interesting is to have a custom shaft very tight with extremely low tolerance so pressure can kept to let’s say 20-30psi. Moving shaft so there is no interference from the air tube.
Also how do you know what is the correct air pressure for your system? What do you measure?
Hi David,View attachment 757712
View attachment 757713
My Versa Dynamics and a big commercial air bearing of the same air distribution design principal.
A fingerprint on the shaft will give you an idea of how tight the tolerance is since it will stick in its presence.
The New Ways are an excellent alternative since no one has a centerless grinder
In their garage To do the O.D. let alone internal I.D. machining to match
Regards
David
Thanks for these very interesting photos! So, I think the air pressure will be high on both opening areas of the bearing. That makes sense. I don't know the construction of New Way air bearing. I would assume there is an air chamber behind the layer of porous material.
Jim
I am inclined to try something a little different. I would like to do moving shaft similar to the Chinese implementation with two bearings but balancing the counterweight similar to the back diamond turntable.
Which Chinese implementation are you talking about? I would like to see it if possible.
My question is where can I inquire a custom ultra precision shaft? I know it could be expensive but I want at least know how expensive it could be.
Since it’s movimg shaft I assume the shaft cannot be solid stainless steel as the moving mass would be incredibly heavy.
But wouldn’t an hollow long shaft ring like a bell?
I guess you need to buy some kind hollow metal tube and find a shop which can do precision grinding to grind down to the size you need.
What I did for a hollow shaft was to lay the wire through the shaft first. Then, I sealed one end, head shell side, of hollow shaft. I used Gorilla glue to fill in the hole from other end of hollow shaft. Be careful not to pour too much because Gorilla glue will expend like foam.
Also how do you know what is the correct air pressure for your system? What do you measure?
I can’t measure. All I did was to listen to meet my liking.
Jim
The Chinese execution with two bearings is at post #81
https://www.diyaudio.com/forums/analogue-source/268614-diy-air-bearing-linear-arm-9.html#post4231877
I want to do something similar using two bearings but one next to the other and counterweight arrangement similar to the black diamond.
Having one next to the other makes the moving shaft shorter than having the bearing spaced out with the armwand places in between like at post #81.
What specialty company are able to produce an ultra precision hollow shaft?
What tolerances am I likely looking at? So I know what to inquire.
In the case of custom precision hollow shaft, would I achieve a more precison result with lower pressure by using a film type bearing instead of porous or would I still be using same new ways bearings?
Thank you.
https://www.diyaudio.com/forums/analogue-source/268614-diy-air-bearing-linear-arm-9.html#post4231877
I want to do something similar using two bearings but one next to the other and counterweight arrangement similar to the black diamond.
Having one next to the other makes the moving shaft shorter than having the bearing spaced out with the armwand places in between like at post #81.
What specialty company are able to produce an ultra precision hollow shaft?
What tolerances am I likely looking at? So I know what to inquire.
In the case of custom precision hollow shaft, would I achieve a more precison result with lower pressure by using a film type bearing instead of porous or would I still be using same new ways bearings?
Thank you.
Hi,
arrow shafts are typically produced to tight tolerances.
In my TheKiller arm project I used a hunting arrow carbon shaft with 9.8mm OD.
hunting arrow shafts are larger in diameter than target arrow shafts.
Placing 3 small foam slices -cut from a ear damping pad- at the ends and the middle of the tube a high degree of damping was achieved without increasing mass considerably -the carbon tube itself exhibits a quite well damped behaviour already.
jauu
Calvin
arrow shafts are typically produced to tight tolerances.
In my TheKiller arm project I used a hunting arrow carbon shaft with 9.8mm OD.
hunting arrow shafts are larger in diameter than target arrow shafts.
Placing 3 small foam slices -cut from a ear damping pad- at the ends and the middle of the tube a high degree of damping was achieved without increasing mass considerably -the carbon tube itself exhibits a quite well damped behaviour already.
jauu
Calvin
The Chinese execution with two bearings is at post #81
What specialty company are able to produce an ultra precision hollow shaft?
What tolerances am I likely looking at? So I know what to inquire.
In the case of custom precision hollow shaft, would I achieve a more precison result with lower pressure by using a film type bearing instead of porous or would I still be using same new ways bearings?
Thank you.
This kind of construction has its pros and cons.
Pros:
It has more stable straight movements. The moving shaft is less impacted by vibrations.
Cons:
The shaft will be longer. In other words, the mass will be heavy. The structure to maintain perfect line-up of two bushes will get complicated.
Bushing Inside Diameter (ID) 0.5008 in +.0002/-.0000
Recommended Shaft Outside Diameter (OD) 0.5000 in
Recommended Shaft Tolerance -.0002/-.0007 in
These are the recommended value for New Way air bushing. I assume you are going to use 1/2” air bushings. I personally won’t recommend to change the shaft tolerance. But if you want, you may reduce the gap between air bushing and shaft. So,
Bushing Inside Diameter (ID) 0.5008 in +.0002/-.0000
Shaft Outside Diameter (OD) 0.5004 in
Shaft Tolerance -.0002/-.0007 in
Therefore, you reduce the air gap by half of New Way’s default.
I have never used different kinds of air bearings so I am not able to advise which kind of air bearing you should chose. However, my general feeling is other factors are much more important than construction of bearings. Once you reduce the air gap, you increase effectively stiffness with same or lower air pressure.
Jim
Hi,
arrow shafts are typically produced to tight tolerances.
In my TheKiller arm project I used a hunting arrow carbon shaft with 9.8mm OD.
hunting arrow shafts are larger in diameter than target arrow shafts.
Placing 3 small foam slices -cut from a ear damping pad- at the ends and the middle of the tube a high degree of damping was achieved without increasing mass considerably -the carbon tube itself exhibits a quite well damped behaviour already.
jauu
Calvin
If Stefanoo decides to make arm with long wand, it is not bad to use arrow carbon shaft. Titanium tube is nice too. I was used to cut plastic foam cheap wine corks in small pieces and trim it into round shape. Then, I coated these small pieces of wine corks with Gorilla glue or epoxy and used a stick to push these small pieces of corks into carbon fiber tube piece by piece. It worked very well. This was for my mechanical linear arms and counter weight part of one of my air bearing arm.
Last edited:
Thank you very much guys for your response. Please keep in mind I am completely newbie in this field without your help I won't be able to build anything that decently functions. I will rely on your precious advice to pull through this project.
With that said, yes I am going to build a long wand version. I have already acquired the magnesium wand from EMT and I will send pictures with details once I receive it.
I will also have to make the connection joint to the want in order to adjust overhang and azimuth (the headshell has two holes instead of two slots).
As far as air bushings are concerned, I am going for a two bushing approach; is it advisable to go with two bushing spaced apart like the Chinese build or go like the black diamond with two bushings side by side (which from picture it looks like it has two bushings one next to the other as it has two air fittings coming out from the golden manifold) ?
The main difference I can catch from these two approaches is:
1) spaced out bushing has more straight trajectory but a longer shaft which adds more moving mass
2) back diamond's approach i.e. one bushing next to the other has less guidance for straight trajectory but uses a shorter shaft thus less moving mass.
Regarding air bushing, would I still go for the new ways porous bushing or a film version would be more precise with the precision shaft?
Diameter of the bushing/shaft: it was mentioned 1/2" which also makes the shaft smaller and lighter but larger bushing/shaft seem to bring more stability thus better sound.
Should I aim for a 3/4" or even 1" design or go for a smaller 1/2"?
Regarding the shaft, where can I inquire a carbon or a titanium shaft? Which company can I inquire to have quote me something to get a grasp of the total price and even if such a precision part can be obtained for a DIY project?
Thank you everyone.
With that said, yes I am going to build a long wand version. I have already acquired the magnesium wand from EMT and I will send pictures with details once I receive it.
I will also have to make the connection joint to the want in order to adjust overhang and azimuth (the headshell has two holes instead of two slots).
As far as air bushings are concerned, I am going for a two bushing approach; is it advisable to go with two bushing spaced apart like the Chinese build or go like the black diamond with two bushings side by side (which from picture it looks like it has two bushings one next to the other as it has two air fittings coming out from the golden manifold) ?
The main difference I can catch from these two approaches is:
1) spaced out bushing has more straight trajectory but a longer shaft which adds more moving mass
2) back diamond's approach i.e. one bushing next to the other has less guidance for straight trajectory but uses a shorter shaft thus less moving mass.
Regarding air bushing, would I still go for the new ways porous bushing or a film version would be more precise with the precision shaft?
Diameter of the bushing/shaft: it was mentioned 1/2" which also makes the shaft smaller and lighter but larger bushing/shaft seem to bring more stability thus better sound.
Should I aim for a 3/4" or even 1" design or go for a smaller 1/2"?
Regarding the shaft, where can I inquire a carbon or a titanium shaft? Which company can I inquire to have quote me something to get a grasp of the total price and even if such a precision part can be obtained for a DIY project?
Thank you everyone.
Hi Stefano,
If you want to build one as in the photo, I would suggest to use two 1/2” air bushings since you can control the total mass in a reasonable range. I did a rough calculation. This kind of arm needs a 15” or longer shaft. Assume the shaft is a hollow aluminum one with 1/16” wall, so the total mass for shaft will be 60 grams which is close to the mass of 1” air bushing. However, it will be difficult to achieve total mass 80 gram. Also you need to think about the possibility of grinding a shaft with 1/16” wall. It won’t be easy. You have to find a shop to see if the shop can do it.
Using two 1” air bushings is out of question due to the mass of shaft. For same kind of shaft as above but 1” OD, it will be 122 gams.
3/4” will be 90 grams. Let’s assume to use 3/4” air bushings. As long as you can control the total mass not over 150 grams, you will be ok although it is too heavy for your Goldfinger. Even though, it will play and sounds wonderful. However, you may have trouble to track some of high dynamic passage of music. The arm will track but sound may have distortion for some music passages, such broken sound. I can’t estimate cartridge/arm resonance frequency either since it is a long arm wand. You need to do some calacutions to foresee the resonance frequency.
In addition to what I said above, you need to know the total mass of EMT magnesium wand.
I don’t think carbon fiber can be used as shaft for air bushing. The arrow carbon fiber shaft I was talking about was for arm wand only.
Jim
If you want to build one as in the photo, I would suggest to use two 1/2” air bushings since you can control the total mass in a reasonable range. I did a rough calculation. This kind of arm needs a 15” or longer shaft. Assume the shaft is a hollow aluminum one with 1/16” wall, so the total mass for shaft will be 60 grams which is close to the mass of 1” air bushing. However, it will be difficult to achieve total mass 80 gram. Also you need to think about the possibility of grinding a shaft with 1/16” wall. It won’t be easy. You have to find a shop to see if the shop can do it.
Using two 1” air bushings is out of question due to the mass of shaft. For same kind of shaft as above but 1” OD, it will be 122 gams.
3/4” will be 90 grams. Let’s assume to use 3/4” air bushings. As long as you can control the total mass not over 150 grams, you will be ok although it is too heavy for your Goldfinger. Even though, it will play and sounds wonderful. However, you may have trouble to track some of high dynamic passage of music. The arm will track but sound may have distortion for some music passages, such broken sound. I can’t estimate cartridge/arm resonance frequency either since it is a long arm wand. You need to do some calacutions to foresee the resonance frequency.
In addition to what I said above, you need to know the total mass of EMT magnesium wand.
I don’t think carbon fiber can be used as shaft for air bushing. The arrow carbon fiber shaft I was talking about was for arm wand only.
Jim
Hi Jim,
Thanks for your preliminary calculations. Yes accordingly to general calculations, the moving mass should be a max of 80gr.
I don’t know how that’s achiveable. If the shaft can be at least 60-70gr plus I assume the magnisium armwand to be not less than 50gr.
On top of that we have to consider the housing that joins the wand with the shaft that is a solid piece with the shaft for the counterweight maybe another 10-15g, plus counterweight itself can be another 10g or more?!
How can it all that be 80gr or less? If I add up not including any foam for dampening that can be around 200gr for the full moving mass.
Do you think I am missing something?
If this is the case 200gr will definitely be too heavy for most cartridges.
Maybe a titanium shaft would help?! If I gogle titanium hollow shafts just Chinese suppliers pop up and I rather go different route for this high precision shaft.
Does anybody have any suggestion as to which shop I can contact that produces precision hollow shafts maybe in titanium?
Moreover it was estimated a length for the shard of 15” but if we go for one bushing next to the other, similar to the proscenium tonearm that has the counterweight on the extreme left side of the shaft, this arrangement requires a shorter shaft than having the two bushing spaced apart and the wand in between them.
Now my question is which arrangement is technically preferable, the one used on
The proscenium tonearm or the one used by the Chinese guy at post #81?
This is definitely a very challenging implementation for me but I want to try to pull through and make it. Like super has mention it is important that the total weight puts the resonance on the right spot to allow the cartriddge to track in hard dynamic passage withyou compressing or distorting. At the moment I struggle to see how this could be achievable.
Thanks for your preliminary calculations. Yes accordingly to general calculations, the moving mass should be a max of 80gr.
I don’t know how that’s achiveable. If the shaft can be at least 60-70gr plus I assume the magnisium armwand to be not less than 50gr.
On top of that we have to consider the housing that joins the wand with the shaft that is a solid piece with the shaft for the counterweight maybe another 10-15g, plus counterweight itself can be another 10g or more?!
How can it all that be 80gr or less? If I add up not including any foam for dampening that can be around 200gr for the full moving mass.
Do you think I am missing something?
If this is the case 200gr will definitely be too heavy for most cartridges.
Maybe a titanium shaft would help?! If I gogle titanium hollow shafts just Chinese suppliers pop up and I rather go different route for this high precision shaft.
Does anybody have any suggestion as to which shop I can contact that produces precision hollow shafts maybe in titanium?
Moreover it was estimated a length for the shard of 15” but if we go for one bushing next to the other, similar to the proscenium tonearm that has the counterweight on the extreme left side of the shaft, this arrangement requires a shorter shaft than having the two bushing spaced apart and the wand in between them.
Now my question is which arrangement is technically preferable, the one used on
The proscenium tonearm or the one used by the Chinese guy at post #81?
This is definitely a very challenging implementation for me but I want to try to pull through and make it. Like super has mention it is important that the total weight puts the resonance on the right spot to allow the cartriddge to track in hard dynamic passage withyou compressing or distorting. At the moment I struggle to see how this could be achievable.
- Home
- Source & Line
- Analogue Source
- DIY Air Bearing Linear Arm