2wice: Are you saying Reed 3D printed the $10K Reed 5?
Only the prototype
I continue to try to improve both arms.
For 5A ( please note it is not Reed 5A, it is the 5th version and a variant of the 5th version), I redeigned all the parameters. Its tracking errors are so small and they are not factors at all since tolerance during making may be larger than theoretical tracking errors.
For 6B, I changed the guiding mechanism. It was inspired by Schroder LT tonearm. Schroder LT has the guiding mechanism under the base tower. It is a very clever implementation. I can't do that because it may get too complicated to use the arm on my existing table. I also found that if I design the guiding mechanism too far from the front of the arm, tracking errors may be getting larger. So, a non-circle guiding rail may be desirable.
I am not going to use magnetic counterweights for both arms since I have no experience with magnetic counterweights and don't have confidence in magnetic counterweights. The arm wands will be 3D printed in carbon with 60% or 70% infill. The light blue color indicates aluminum. The dark charcoal color is carbon 3D printing. The brass color is steel or brass. The light grey color is nylon 3D printing.
I like both arms so much and don't know which I should make now. If I have to choose, my favorite leans slightly towards 6B.
For 5A ( please note it is not Reed 5A, it is the 5th version and a variant of the 5th version), I redeigned all the parameters. Its tracking errors are so small and they are not factors at all since tolerance during making may be larger than theoretical tracking errors.
For 6B, I changed the guiding mechanism. It was inspired by Schroder LT tonearm. Schroder LT has the guiding mechanism under the base tower. It is a very clever implementation. I can't do that because it may get too complicated to use the arm on my existing table. I also found that if I design the guiding mechanism too far from the front of the arm, tracking errors may be getting larger. So, a non-circle guiding rail may be desirable.
I am not going to use magnetic counterweights for both arms since I have no experience with magnetic counterweights and don't have confidence in magnetic counterweights. The arm wands will be 3D printed in carbon with 60% or 70% infill. The light blue color indicates aluminum. The dark charcoal color is carbon 3D printing. The brass color is steel or brass. The light grey color is nylon 3D printing.
I like both arms so much and don't know which I should make now. If I have to choose, my favorite leans slightly towards 6B.
Attachments
Last edited:
I prefer 6B. I like having only ONE primary bearing so the majority of the mass is on one pivot. And the secondary bearing should be relegated for the guiding mechanism. I don't like the Thales Simplicity tonearm approach of dual pivots/armwands. Said to have resonance cancelling effect but I don't buy it. I would put the guiding arm at the top instead of the bottom so it's easier to implement a cueing device.
DD,
I have been thinking about a cueing device for a while, but it seems very difficult. The reason for that is my thought about TP arms. Most TP arm designers treat a TP arm as a regular pivot arm, i.e., a 9" pivot arm. They constrain all the links and guiding mechanisms around the base tower while I push the links and guiding as far away from the base tower as possible. That is the difference.
I do this because I believe following two factors.
1, A short arm is better than a long arm. In fact, I have one version of the TP arm with a 90 mm arm wand. The 6B arm has a 185 mm arm wand. It is shorter than other PT arms. From the image I posted here, you can see the arm wand is the shortest I can do without further complicating the mechanism.
2, Pushing all links and mechanisms toward the front of the arm can reduce tracking errors and can avoid non-circle guiding with minimum tracking errors.
But such a design brings difficulty to implement a cueing device. For now, I am thinking to add a fixed armrest on the turntable and a tall lifting handle on the headshell.
Jim
I have been thinking about a cueing device for a while, but it seems very difficult. The reason for that is my thought about TP arms. Most TP arm designers treat a TP arm as a regular pivot arm, i.e., a 9" pivot arm. They constrain all the links and guiding mechanisms around the base tower while I push the links and guiding as far away from the base tower as possible. That is the difference.
I do this because I believe following two factors.
1, A short arm is better than a long arm. In fact, I have one version of the TP arm with a 90 mm arm wand. The 6B arm has a 185 mm arm wand. It is shorter than other PT arms. From the image I posted here, you can see the arm wand is the shortest I can do without further complicating the mechanism.
2, Pushing all links and mechanisms toward the front of the arm can reduce tracking errors and can avoid non-circle guiding with minimum tracking errors.
But such a design brings difficulty to implement a cueing device. For now, I am thinking to add a fixed armrest on the turntable and a tall lifting handle on the headshell.
Jim
Attachments
Jim,
I agree with 2wice and DD - 5A is an attractive arm, but 6B would be my choice for its relative simplicity and inherent stability. And it's a pretty good looking arm. Nice designs and excellent drawings. There is one possible hitch I think I see in 6B - there's a possibility the guide arm will foul the pivot arm when the arm reaches the final grooves. If that's true, a slight curve or offset will cure it.
You may find a bubble level is not only useful, but sort of necessary. PLTs need to be able to set a slight degree of off level in a specific direction as an anti skating measure.
I don't believe there are any hard and fast rules about relative wand, pivot arm, or guide arm lengths. There are multiple reasons, good ones, for choosing between alternatives, including, for instance, resonances and bearing stresses. Commercial designers will have to consider overcoming conventional preference for 9" - 12" pivot arms. That said, I hope your choices are successful.
5A reminded me of something because of the way it sits - the Van Epps and Burne-jones arms. If those designers had shortened the arms, moved the outer bearings inward and added a wand, they might have invented the twin arm PLT a long time ago.
Rayk: When I was looking up those two arms, I came across a conversation you and I had about them ten years ago on VE. Ten years ago.
I agree with 2wice and DD - 5A is an attractive arm, but 6B would be my choice for its relative simplicity and inherent stability. And it's a pretty good looking arm. Nice designs and excellent drawings. There is one possible hitch I think I see in 6B - there's a possibility the guide arm will foul the pivot arm when the arm reaches the final grooves. If that's true, a slight curve or offset will cure it.
You may find a bubble level is not only useful, but sort of necessary. PLTs need to be able to set a slight degree of off level in a specific direction as an anti skating measure.
I don't believe there are any hard and fast rules about relative wand, pivot arm, or guide arm lengths. There are multiple reasons, good ones, for choosing between alternatives, including, for instance, resonances and bearing stresses. Commercial designers will have to consider overcoming conventional preference for 9" - 12" pivot arms. That said, I hope your choices are successful.
5A reminded me of something because of the way it sits - the Van Epps and Burne-jones arms. If those designers had shortened the arms, moved the outer bearings inward and added a wand, they might have invented the twin arm PLT a long time ago.
Rayk: When I was looking up those two arms, I came across a conversation you and I had about them ten years ago on VE. Ten years ago.
Attachments
Last edited:
cueing difficulty
I understand. It reminds me of the Dynavector arm with short vertical arm and long horizontal arm.
Understandable. You can either attach a thin light rod extending out of that area to be in contact with a cueing lift but any extra attachment can create resonance. Or you might have to install the cueing on the counterweight area to push DOWN in order to lift arm UP. Just spitballing here...
They constrain all the links and guiding mechanisms around the base tower while I push the links and guiding as far away from the base tower as possible.
I understand. It reminds me of the Dynavector arm with short vertical arm and long horizontal arm.
But such a design brings difficulty to implement a cueing device.
Understandable. You can either attach a thin light rod extending out of that area to be in contact with a cueing lift but any extra attachment can create resonance. Or you might have to install the cueing on the counterweight area to push DOWN in order to lift arm UP. Just spitballing here...
Doug,
I checked the guide arm after reading your post. The clearance between the guide arm and counterweight is about 2 mm in the vertical plane. It may be problematic. The counterweight is a spare part I left from building the air-bearing arm. I may have to make a new counterweight. Thanks for your advice!
From the photos you posted, they do look to have the same geometry as my 5A arm. However, it is hard to say without knowing the details. It also seems to me that they resemble Thales tonearm more.
Jim
I checked the guide arm after reading your post. The clearance between the guide arm and counterweight is about 2 mm in the vertical plane. It may be problematic. The counterweight is a spare part I left from building the air-bearing arm. I may have to make a new counterweight. Thanks for your advice!
From the photos you posted, they do look to have the same geometry as my 5A arm. However, it is hard to say without knowing the details. It also seems to me that they resemble Thales tonearm more.
Jim
Last edited:
I am posting the geometry for my 5A arm and for other variable geometry for my 5B arm here. It seems to me that both tonearms in the photos posted by Doug have the same length of arm wand. If a tonearm is based on double Birch geometry, the two arm wands can't be the same length. My arms may look similar to these arms, but the underlying principle is different. Especially for the geometry of my 5B as I posted here, their geometries look very similar. In fact, they are different in their geometry.
Attachments
I finalized my designs and came up with two versions of the same arm.
I am going to make V1. For V1, I am going to print the headshell in stainless steel sandwiched with a 2 mm carbon fiber plate. I also took Doug's suggestion to install a bubble level on the top of the base. All the orders for 3D printed parts had been placed.
For V2, the arm wand is 3D printed in aluminum or, better yet, titanium. Titanium is not cheap but acceptable for this particular piece. The headshell and arm wand is a uni-body design. The headshell gets sandwiched with carbon fiber, too. From the experience of making air-bearing arms, I realized how important a headshell is.
I am going to make V1. For V1, I am going to print the headshell in stainless steel sandwiched with a 2 mm carbon fiber plate. I also took Doug's suggestion to install a bubble level on the top of the base. All the orders for 3D printed parts had been placed.
For V2, the arm wand is 3D printed in aluminum or, better yet, titanium. Titanium is not cheap but acceptable for this particular piece. The headshell and arm wand is a uni-body design. The headshell gets sandwiched with carbon fiber, too. From the experience of making air-bearing arms, I realized how important a headshell is.
Attachments
Jim,
I hope you're seeing progress on the parts for your arm because I really want to see photos of the completed project and to read your report about the results.
I hope you're seeing progress on the parts for your arm because I really want to see photos of the completed project and to read your report about the results.
Doug,
I have placed the orders for the parts except the honeycomb arm wand. The honeycomb arm wand is going to be printed in aluminum with a brass plate in between the head shell and the cartridge. But the first part I ordered was a waste of money. It was the head shell that printed in stainless steel. I didn't check the magnetic properties for 316 stainless steel until I got the part. The 316 stainless steel is magnetic. The stainless steel head shell was printed in France. I use this web site for my 3D printing.
Craftcloud(R) by All3DP | Your 3D Printing Service Marketplace
They send their orders all over the world. So, it may take a while to get all the parts printed.
Jim
I have placed the orders for the parts except the honeycomb arm wand. The honeycomb arm wand is going to be printed in aluminum with a brass plate in between the head shell and the cartridge. But the first part I ordered was a waste of money. It was the head shell that printed in stainless steel. I didn't check the magnetic properties for 316 stainless steel until I got the part. The 316 stainless steel is magnetic. The stainless steel head shell was printed in France. I use this web site for my 3D printing.
Craftcloud(R) by All3DP | Your 3D Printing Service Marketplace
They send their orders all over the world. So, it may take a while to get all the parts printed.
Jim
SLM = Selective Laser Melting
Speaking of honeycomb style tonearm, the latest tonearm in the OMA K3 turntable, designed by Frank Schröder, certainly raised some eyebrows.
Speaking of honeycomb style tonearm, the latest tonearm in the OMA K3 turntable, designed by Frank Schröder, certainly raised some eyebrows.
"The K3 tonearm is the creation of world renowned tonearm designer/maker Frank Schroder of Berlin. Frank created the K3 arm to be consistent with the project's innovative and technically revolutionary spirit as much as with its bold appearance. The arm is the first to be made using the 3D metal printing process known as SLM (Selective Laser Melting), whereby an aerospace aluminum alloy powder is fused by a laser into a form impossible to fabricate any other way. The ratio of bending/torsional stiffness to weight is extremely high, the tonearm's low mass counterweight is decoupled by its own thread suspension/bearing assembly system which effectively decouples it from the main arm wand and prevents any energy storage in the counterweight section, an often overlooked detriment to sonic purity . The integrated Azimuth- and VTF-finetuning contributes to the ease of set up and use, same for the neutral balance mass distribution of the arm, which accounts for near zero change in tracking force for any change in VTA or record thickness. The Schroder K3 arm is only available as part of the K3 turntable package."
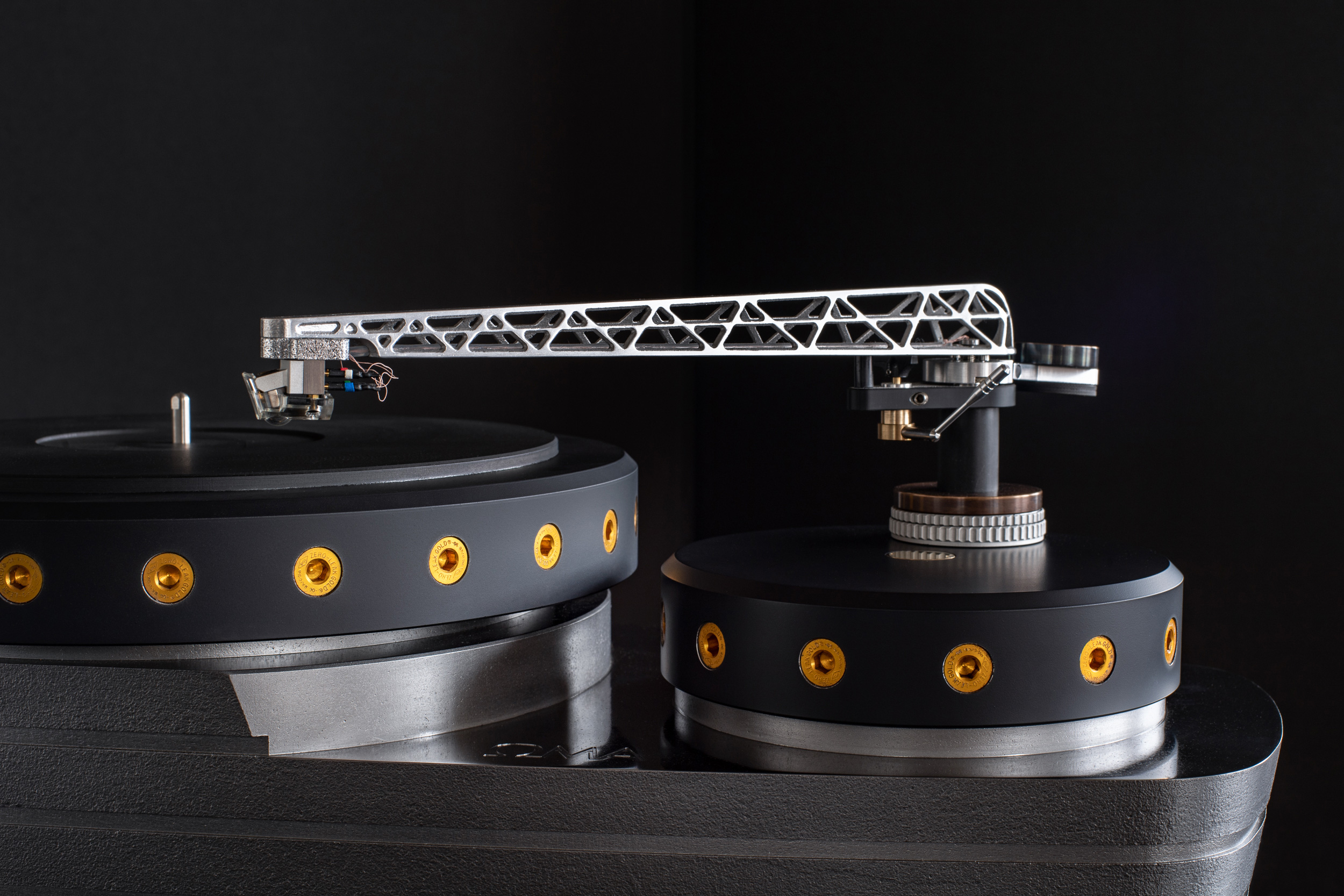

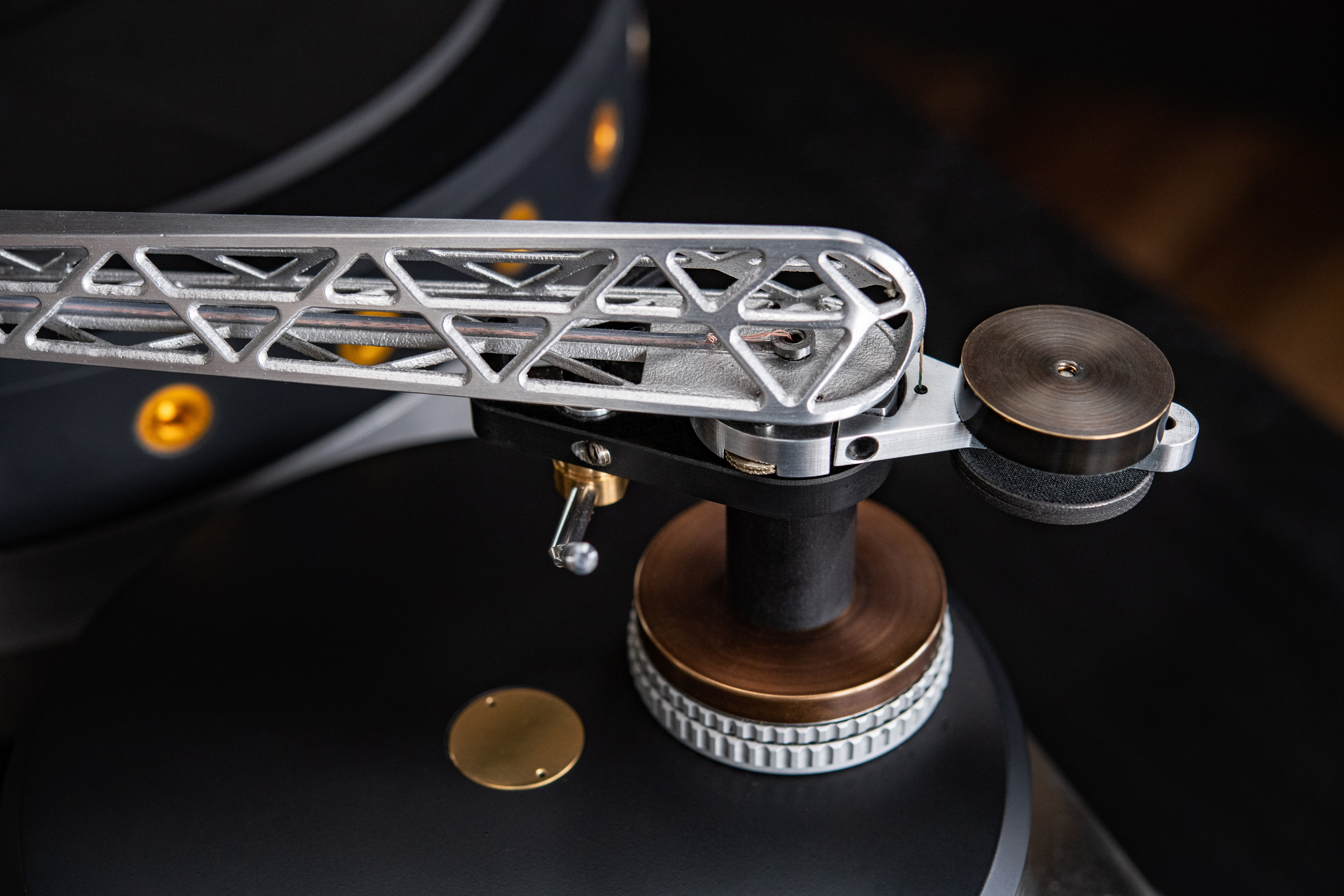
Last edited:
I received the 2nd part, a carbon fiber 3D printed wand, today. The wand is beautifully printed. If I can do it 2nd time, I may try to reduce the weight of the wand by using less infill. I used 80% infill. I think 60% should be better. The stainless steel headshell is on the bottom of the photo. The headshell is nice, too, but I can't use it because 316 stainless is magnetic.
For the honeycomb wand, I don't know how to arrange the wire yet. I may just glue the wire on the bottom inside the honeycomb.
From the photos, Frank's 3D-printed arm seems very light because its counterweight is small.
The arm looks very nice!
For the honeycomb wand, I don't know how to arrange the wire yet. I may just glue the wire on the bottom inside the honeycomb.
From the photos, Frank's 3D-printed arm seems very light because its counterweight is small.
The arm looks very nice!
Attachments
Last edited:
additive vs subtractive
Very nice armwand. I particularly like the repurposing of the Audio-Technica headshell as it will make future cartridge swap easier. Can't wait to see the rest of the parts arrive.
3D printing is a form of additive machining and traditional machining is a form of subtractive machining. I believe SLM belongs to the latter. Each method can arrive similar results of course.
Very nice armwand. I particularly like the repurposing of the Audio-Technica headshell as it will make future cartridge swap easier. Can't wait to see the rest of the parts arrive.
From the photos, Frank's 3D-printed arm seems very light because its counterweight is small.
The arm looks very nice!
3D printing is a form of additive machining and traditional machining is a form of subtractive machining. I believe SLM belongs to the latter. Each method can arrive similar results of course.
After looking at Frank's arm carefully, I have two questions.
There seems a separate metal piece directly over the cartridge. Isn't it better to print it together with the arm wand?
Judging from the photo, the piece of metal over the cartridge has a different texture from the arm ward. Is it printed in a different metal? If so, what kind of metal it is?
There seems a separate metal piece directly over the cartridge. Isn't it better to print it together with the arm wand?
Judging from the photo, the piece of metal over the cartridge has a different texture from the arm ward. Is it printed in a different metal? If so, what kind of metal it is?
aluminum
According to the Stereophile review, that "the cartridge is first affixed to a porous, "foamed" aluminum plate, which secures to the arm with a single bolt - an oft-copied Schröder innovation."
Judging from the photo, the piece of metal over the cartridge has a different texture from the arm ward. Is it printed in a different metal? If so, what kind of metal it is?
According to the Stereophile review, that "the cartridge is first affixed to a porous, "foamed" aluminum plate, which secures to the arm with a single bolt - an oft-copied Schröder innovation."
Thanks, DD!
Foamed aluminum, very interesting.
My personal preference for the area that directly touches the cartridge is brass or brass with carbon fiber. I was inspired by Benz LPs cartridge to use brass. However, brass is heavy. Audio Technica's Technihard headshell is another favorite of mine. My belief is that the best headshell is a block of metal.
My honeycomb arm wand was directly inspired by Cobra tonearm. They used composite material to form a shell and I use structure to form a shell. My honeycomb arm wand is in a half-moon shape as well from the front view. It also has a curved profile. Frank's arm may be the first commercial arm with 3d printed structured arm wand.
Foamed aluminum, very interesting.
My personal preference for the area that directly touches the cartridge is brass or brass with carbon fiber. I was inspired by Benz LPs cartridge to use brass. However, brass is heavy. Audio Technica's Technihard headshell is another favorite of mine. My belief is that the best headshell is a block of metal.
My honeycomb arm wand was directly inspired by Cobra tonearm. They used composite material to form a shell and I use structure to form a shell. My honeycomb arm wand is in a half-moon shape as well from the front view. It also has a curved profile. Frank's arm may be the first commercial arm with 3d printed structured arm wand.
Attachments
first commercial 3D printed tonearm
VPI did it in 2013.
Correction to my earlier comment that SLM(selective laser melting) is indeed a form of additive machining process.
Frank's arm may be the first commercial arm with 3d printed structured arm wand.
VPI did it in 2013.
Correction to my earlier comment that SLM(selective laser melting) is indeed a form of additive machining process.
certainly raised some eyebrows.
Much neater than gluing together balsa strips. 🙂
DIY Balsa Wood Tonearm | D a r k L a n t e r n
- Home
- Source & Line
- Analogue Source
- Building a Tuthill/Reed 5A Tangential Tracking Pivot Tonearm