Hello Nanook,
Please don't get me wrong. I'm fully aware of the neccessity to implement an offset angle to keep tracing error related distorsions as low as possible. That related math is 50years and older. What remains is that any correction mechanism, aka "antiskate" will preload the cantilever in the horizontal plane, on some unipivots a much smaller vertical component exists as well. An excursion in one direction, say right, will require more force than one in the opposite direction. Similar to a speaker/driver with an asymmetrical suspension characteristic(essentially all cone drivers).
There simply is(almost) no way to compensate for the skating force at the stylus tip.
What you describe regarding turning my arm into an "active" device is covered in the patent application. It complicates matters, leads to the old "error before correction" problem or requires some very clever correction algorythm, but, most importantly, sounds no more transparent.
"The key is that whatever the orientation of the headshell/stylus tip at the initial state was, it should remain in that state. " Yes.
"This could be accomplished by allowing only vertical travel of the arm, while the base provides the rotation." No(or maybe I misunderstood).
"A very minute amount of lateral force would be applied to the stylus...". As mentioned before, no more than 5 Milligrams will ever deflect the cantilever(the arm's lateral movement is critically damped), the actual figure in operation(tracing a regular track) is quite a bit lower. The behaviour in this "domain" of any arm/cartridge combination can be checked with a Namiki side force checker or a strain gauge cartridge with appropriate analyzing circuitry.
Greetings from a believer in the KISS principle,
Frank
Please don't get me wrong. I'm fully aware of the neccessity to implement an offset angle to keep tracing error related distorsions as low as possible. That related math is 50years and older. What remains is that any correction mechanism, aka "antiskate" will preload the cantilever in the horizontal plane, on some unipivots a much smaller vertical component exists as well. An excursion in one direction, say right, will require more force than one in the opposite direction. Similar to a speaker/driver with an asymmetrical suspension characteristic(essentially all cone drivers).
There simply is(almost) no way to compensate for the skating force at the stylus tip.
What you describe regarding turning my arm into an "active" device is covered in the patent application. It complicates matters, leads to the old "error before correction" problem or requires some very clever correction algorythm, but, most importantly, sounds no more transparent.
"The key is that whatever the orientation of the headshell/stylus tip at the initial state was, it should remain in that state. " Yes.
"This could be accomplished by allowing only vertical travel of the arm, while the base provides the rotation." No(or maybe I misunderstood).
"A very minute amount of lateral force would be applied to the stylus...". As mentioned before, no more than 5 Milligrams will ever deflect the cantilever(the arm's lateral movement is critically damped), the actual figure in operation(tracing a regular track) is quite a bit lower. The behaviour in this "domain" of any arm/cartridge combination can be checked with a Namiki side force checker or a strain gauge cartridge with appropriate analyzing circuitry.
Greetings from a believer in the KISS principle,
Frank
Oh. talking about why instead of how is not necessary out of topic ?I don't want to take this thread away from the topic,
As i had designed in the 70th a very similar (i presume) prototype of tangential arm (on the principle) to your, i believe we lie on the same planet ?
Well, no angle errors, no parasitic lateral forces on the cartridge is all about.
Purely mechanical or electronically assisted is just a question of price/results/simplicity, industrial facilities, personal preferences, agree ?
After that, resonances (acoustic or mechanical), inertia, quality of the cartridge, all that makes the real sonic difference, you are right...
On my side, about cartridges, i'm more aware about good tracking on high level trebles than response curve linearity. I too appreciated some moving coils, too expensive nowadays (300$ for a 310MC ?) , i stay with my old poor ADC to copy old vinyls to my HDs, with as much pressure in the groove it can afford...
Oh, one thing, one of the most annoying parasitic force on the cantilever is often the one of the signal wires. Linear tracking systems are the best on that matter, as the angle of the pivot does not varies, so no torsion.
Cheers,
Last edited:
The only question that remains is what's the most effective way to accomplish this in a purely passive system? RS Labs uses a headshell that passively pivots.
The RS Labs arm has NOTHING to do with keeping tangency. It is designed to reduce skating force. I don't know how many times this error has been repeated. In fact, the designer of the RS arm never claim that as the intention of the design.
Mr. Schroeder's solution may be very effective, but can a mount that rotates really be any better than a headshell that does the same thing?
rotating headshell or headshell with offset angle has more skating force.
If a tangential arm with effectively zero error is wanted, then a passive linear tracker may be the only "true" solution (like the Souther and the Rauna Cantus).
The problem is high horizontal mass on those passive linear trackers or arms on rollers.
.
On my new arm, 1,5 milligrams(possibly near zero in the production version) will deflect the arm vertically, 5mg or less horizontally(preloaded bearings, no slack) When properly mounted, there is no skating force to be measured.
Hi Frank. Thanks for chiming in. I look forward to seeing more pictures, particularly the guiding mechanism. 🙂
.
"Oh, one thing, one of the most annoying parasitic force on the cantilever is often the one of the signal wires. Linear tracking systems are the best on that matter, as the angle of the pivot does not varies, so no torsion."
May be it is a bit off topic, however I would agree, and I also unable to understand, why on many modern expensive arms/tables we may see extremely rigid tone arm wires, sticking up (not hanging down)? They should implement said "parasitic" forces, measured in a couple of grams, and far not in just milligrams...What is a sense of applying highly sophisticated arm bearings e.t.c. together with such brutal wires?![]()
Quote:
Originally Posted by Nanook
If a tangential arm with effectively zero error is wanted, then a passive linear tracker may be the only "true" solution (like the Souther and the Rauna Cantus).
Directdriver:
The problem is high horizontal mass on those passive linear trackers or arms on rollers.
.[/QUOTE] Also there is no level fulcrum (on true linear trackers), able of multiplying the torque, applied on pivot. As it does on both pivoting arms and semi-linear arms, helping to deal with high mass of the arm base and counterweight. So there is no gain in force (on linear trackers), and both stylus and cantilever must drag all the arm+base+counterweight masses linear way. Looks a bit scary and not very optimistic for me...
Originally Posted by Nanook
If a tangential arm with effectively zero error is wanted, then a passive linear tracker may be the only "true" solution (like the Souther and the Rauna Cantus).
Directdriver:
The problem is high horizontal mass on those passive linear trackers or arms on rollers.
.[/QUOTE] Also there is no level fulcrum (on true linear trackers), able of multiplying the torque, applied on pivot. As it does on both pivoting arms and semi-linear arms, helping to deal with high mass of the arm base and counterweight. So there is no gain in force (on linear trackers), and both stylus and cantilever must drag all the arm+base+counterweight masses linear way. Looks a bit scary and not very optimistic for me...
Last edited:
I remember the first arm i designed. With a very low masse thin aluminium tube and a Euphonics head (very light too). The wires were repaced by four nickel needles plunging in 4 quater of circle baths of mercury around the axe.
(Mercury, dangerous for the health, can be replaced todays with galium alloys).
I was able to read at 45RPM a fully excentred jukebox record, with a cigarette under one side.
Try to do this with wires and heavy heads ;-)
(Mercury, dangerous for the health, can be replaced todays with galium alloys).
I was able to read at 45RPM a fully excentred jukebox record, with a cigarette under one side.
Try to do this with wires and heavy heads ;-)
Another interesting patented design that features no offset angle at the headshell and pivoting at the base but notice the curious guiding mechanism and then, just for fun, compare the arm to the Schroeder LT arm.
This one is designed by Dwipendra N. Guha, an inventor from Calcutta, India.
Tangential tracking tonearm Patent# 4153256
This one is designed by Dwipendra N. Guha, an inventor from Calcutta, India.
Tangential tracking tonearm Patent# 4153256
An externally hosted image should be here but it was not working when we last tested it.

Last edited:
Hello directdriver
It is my opinion that the arm by Dwipendra Guha skates like crazy. I don't think he ever built a prototype or he would have found that out.
Sincerely,
Ralf
It is my opinion that the arm by Dwipendra Guha skates like crazy. I don't think he ever built a prototype or he would have found that out.
Sincerely,
Ralf
If you applied a torque to the arm 52 acting CCW around pivot 48 and of magnitude sufficient to counteract the stylus reaction force, the arm would no longer skate. Since the torque required varies strongly with arm position, this is not trivial.
You might also need to add a small torque acting CCW around the pivot 32 in order to keep the guide arm 44 in contact with the guide 40.
You might also need to add a small torque acting CCW around the pivot 32 in order to keep the guide arm 44 in contact with the guide 40.
Last edited:
Hi guys,
Ralf and Mark hit the nail on the head. The pictured patent would be a nightmare in operation. A small preload on the guide bar 44 against the guide rail 42(I guess the number 40 relates to the actual surface aka eff. radius) is a MUST, otherwise a "perfect" skating force compensation(impossible anyway due to varying stylus drag) as suggested by Mark would have the entire arm assembly bouncing around(44 against 42). Once there is physical contact between 44 and 42, a skating force is present, which, admittedly, could be kept very small.
Now if the arm's subassembly(48,52,54,56...)was driven cw around 50 by a small motor everytime 44 lost contact with 42, the whole thing would work. But, ough, what happens if the record is eccentric... the poor cantilever would be forced towards the outer rim of the record periodically.
Easy to modify the design to avoid that...
In its stock form, such an arm would have a rather high lateral eff. mass. The counterweight 56 has to counterbalance the entire arm/bearing assembly!
I shall read the patent later again. For now, I'll commence the preparation for my birthday party tomorrow 🙂 🙂 🙂
Merry x-mas everyone!
Frank
Ralf and Mark hit the nail on the head. The pictured patent would be a nightmare in operation. A small preload on the guide bar 44 against the guide rail 42(I guess the number 40 relates to the actual surface aka eff. radius) is a MUST, otherwise a "perfect" skating force compensation(impossible anyway due to varying stylus drag) as suggested by Mark would have the entire arm assembly bouncing around(44 against 42). Once there is physical contact between 44 and 42, a skating force is present, which, admittedly, could be kept very small.
Now if the arm's subassembly(48,52,54,56...)was driven cw around 50 by a small motor everytime 44 lost contact with 42, the whole thing would work. But, ough, what happens if the record is eccentric... the poor cantilever would be forced towards the outer rim of the record periodically.
Easy to modify the design to avoid that...
In its stock form, such an arm would have a rather high lateral eff. mass. The counterweight 56 has to counterbalance the entire arm/bearing assembly!
I shall read the patent later again. For now, I'll commence the preparation for my birthday party tomorrow 🙂 🙂 🙂
Merry x-mas everyone!
Frank
Happy to see three talented designers, Ralf, Mark, and Frank, on here to discuss a weird arm. 🙂
I have a question. If I draw a line along arm "24" and extends all the way to the back will every position converge to a point that is similar to Point "B" in the Birch arm? (Reference back to post# 195 & 236)
I see the Guha arm as a variation of the Birch design with a curious guiding mechanism. Any comment?
Happy holidays to everyone!
Happy birthday to Frank!! Enjoy the party and don't let these patents get in the way of fun! :-D
I have a question. If I draw a line along arm "24" and extends all the way to the back will every position converge to a point that is similar to Point "B" in the Birch arm? (Reference back to post# 195 & 236)
I see the Guha arm as a variation of the Birch design with a curious guiding mechanism. Any comment?
Happy holidays to everyone!
Happy birthday to Frank!! Enjoy the party and don't let these patents get in the way of fun! :-D

Last edited:
Basic answer: Yes.
For the lengths shown the convergence will be fairly loose since the curve decribed by point 26 is likely to be a segment of an ellipse rather than an arc.
For the lengths shown the convergence will be fairly loose since the curve decribed by point 26 is likely to be a segment of an ellipse rather than an arc.
Last edited:
A glimpse of the guiding mechanism from the back of the arm. Check out that black looking piece underneath the gray plate and it is in line or parallel with the arm and would pivot along with the arm as well.
Happy New Year!
DIY Lives in 2012!

An externally hosted image should be here but it was not working when we last tested it.
Happy New Year!
DIY Lives in 2012!
Last edited:
Here's something different, at least compare to the kind of tonearm we discussed on this thread. It's a motorized servo tonearm using ultra precise linear motion bearings and tracks. The below website and write up are from the company that makes the linear tracks, not the turntable company. The whole assembly looks like some military weapon!
Original German website
Website translated to English
Original German website
Website translated to English
Rainer Horstmann has a dream: In times of CD and MP3 he wants to build the best record player in the world. Finally, audio experts, and vinyl enthusiasts agree: The good old record is unmatched in its rendering quality and richness. The plate is annually doubling turnover confirms this. Horstmann is the founder and CEO of AVDesignHaus, an agency for professional sound reinforcement, film production and media management. His motto for the development of the turntable is very simple: No Kompromisse.Konsequent installed it in the reference machine Phono, the VPM Dereneville 2010-1, only the best and latest technology.
What makes the Dereneville is extremely precise and accurate Tangentiallaufwerk. "It feels exactly the record groove from the way it was cut by the cutter into the vinyl," said Horstmann. In this way minimizes its machine Phono the maximum tracking error of only 0.02 ° and thus achieved a unique sound quality. By comparison, the conventional displacement angle is up to 2°. "And you can hear high notes very well as a distortion, or as a stereo channel offset", says the AV specialist. The core of the drive is a linear unit, the gimbal tonearm leads steadily with the way the groove towards the middle of the plate. A laser system - again adjusted by two linear guides - continuously checks the 90 ° tangential to the groove of the arm and the values are also continuously to the electronic controller. These controls with 256 micro steps per step advancing the linear unit. The drive unit is designed for 800 steps per revolution. The smallest possible movement stroke of the linear unit is thus theoretically 0.000024 millimeter.
An externally hosted image should be here but it was not working when we last tested it.

An externally hosted image should be here but it was not working when we last tested it.
Most Expensive Turntable and Tonearm in the World!
From the turntable company.
Original German website
Website translated to English
.
From the turntable company.
Original German website
Website translated to English
An externally hosted image should be here but it was not working when we last tested it.
An externally hosted image should be here but it was not working when we last tested it.
An externally hosted image should be here but it was not working when we last tested it.
An externally hosted image should be here but it was not working when we last tested it.
An externally hosted image should be here but it was not working when we last tested it.
An externally hosted image should be here but it was not working when we last tested it.
.
Gosh. I don't think my low class records would be allowed anywhere near that installation. Whoop! Whoop! Security! We have unauthorised personnel attempting to enjoy themselves!
"The most expensive record deck in the world"
Here's an English site with better translation:
"The most expensive record deck in the world" ...........and it will cost you 500,000 Euros! Talk about all out assault.
Here's an English site with better translation:
"The most expensive record deck in the world" ...........and it will cost you 500,000 Euros! Talk about all out assault.
Rainer Horstmann has a dream: in this era dominated by CDs and MP3s he wants to build the best record deck the world has ever seen. When all is said and done, audio experts and fans of vinyl all agree on this one point: the good old record is head and shoulders above the rest in terms of reproduction quality and fullness of tone. This is confirmed by record sales, which are now doubling year on year. Horstmann is the founder and managing director of AVDesignHaus, a professional sound engineering, film production and media management agency. His mantra for developing his record deck is simplicity itself: No Compromise. In his flagship phono unit, the Dereneville VPM 2010-1, he uses only the highest-quality, state-of-the-art components.
Tangential linear unit with stepper motor
What sets the Dereneville apart from other decks is its tangential drive, which operates with the utmost precision. "It senses the record groove in exactly the same way as it was cut into the vinyl by the groove cutting machine", explains Horstmann. This enables his phono machine to reduce the maximum tracking angle error to as little as 0.02°, thereby achieving unparalleled sound quality. In conventional record decks, for the purpose of comparison, the angle error will be up to 2°. "What's more", continues our audio-visual expert, "this can be heard very clearly as distortion in the trebles or as stereo channel offset".
The heart of the deck is formed by a linear unit that constantly guides the gimbal-bearing tonearm towards the centre of the record. A laser system, which is likewise adjusted by two linear controllers, continuously checks that the arm maintains a tangential angle of 90° to the groove and also continuously sends its measured values on to the electronic control unit. This unit works in steps that are subdivided into 256 micro steps to control the forward movement of the linear unit. The unit's drive is configured for 800 steps for each revolution. In theory, therefore , the smallest possible movement of the linear unit equates to 0.000024 millimetres.
Linear technology produced in Minden
These ultra-precision linear controllers are manufactured and supplied by the Minden-based company Rose+Krieger (RK). This company supplies a comprehensive range of linear components and profile, joining- and modular technology. Rose+Krieger develops and produces components and system solutions for virtually every sector of industry, but first and foremost for mechanical engineering. "For our linear controllers to be used in record decks is nonetheless a first for us" observes Bernd Klöpper, the marketing manager at RK.
Horstmann himself describes the RK linear units as most attractively designed, but the main reason behind his decision to use them is their outstanding precision. A circular ball-bearing guideway and a ball-screw spindle with zero play ensure the degree of precision that he is striving for in the Dereneville. Furthermore, in order to control the tonearm he needed a special length with a travel of just 160 millimetres and a short overall length of 368 millimetres. Rainer Horstmann found it extremely difficult to find a supplier in the market who could produce a unit to such specifications. The Minden-based specialists supplied Horstmann with a custom-built unit based on the RK DuoLine 50. The most significant difference between this unit and the standard model is its unusually small spindle pitch of 12 x 5 mm (standard pitch is 12 x 10 mm). "This was the only way in which we could produce the drive that Herr Horstmann wanted, which would run extremely slowly and with total precision", explains RK's project manager Olaf Durstewitz.
Special commissions are nothing out of the ordinary
For the linear technology professionals at RK Rose+Krieger this kind of custom commission is an everyday situation. "We specialise in small-batch manufacturing to the customer's specifications and to tight deadlines", says Bernd Klöpper. "Customer- and application-specific jobs are our bread and butter." Rose+Krieger accordingly got to grips with Horstmann's problem rapidly, and within four weeks they were able to deliver the required product.
In addition to the custom-built unit, Rainer Horstmann has also integrated two other RK linear controllers in his Dereneville: these are two RK Compact 30/89s with a travel of 30 millimetres, and are used for fine adjustment of the tonearm, thus enabling the VTA (vertical tracking angle) to be adjusted and also enabling tonearms of differing lengths to be used. These "stock items" were in the hands of the customer just a few days after the order was received.
Expensive hobby
The target group for a Horstmann record deck consists exclusively of extremely well-heeled individuals with a penchant for vinyl, and for whom nothing but the best will do. This remarkable piece of kit is not exactly a snip. Hi-fi fans will need deep pockets to pay for this unique sound quality and precision - the Dereneville VPM 2010-1 has a price tag of around 500,000 euros. It is manufactured purely to order. And some prospective buyers have already come forward. "A customer from southern Germany wants to visit us and talk to us with a view to purchasing, we've received a second serious enquiry from Dubai and another one from Japan", says Rainer Horstmann. A well-known dealer from the United States would like to exhibit the Dereneville at the forthcoming CES trade fair in Las Vegas and has invited Horstmann to join him there. Visitors to that fair will then have the opportunity to be won over by the unique quality of the Dereneville. The precision linear units produced by Rose+Krieger in Minden play their part in this top-quality product.
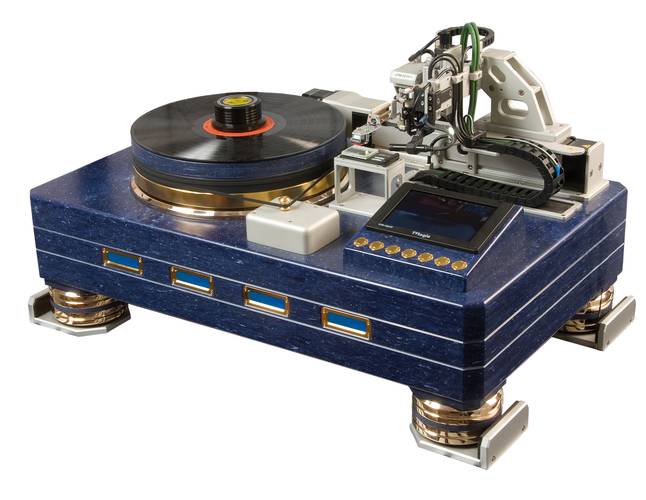
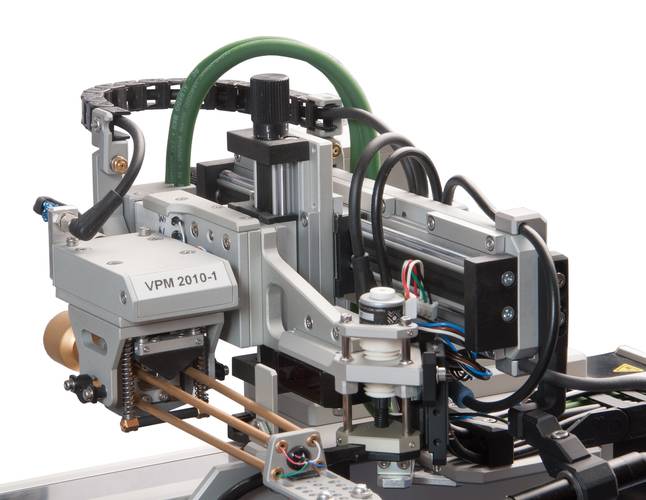
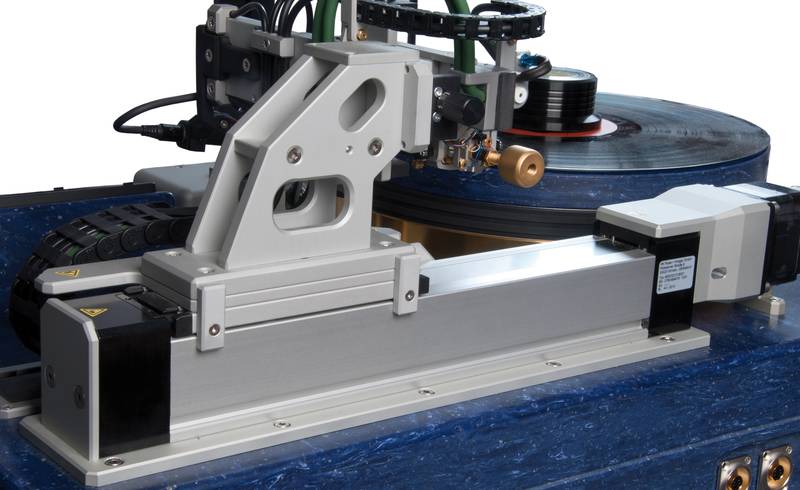
An externally hosted image should be here but it was not working when we last tested it.
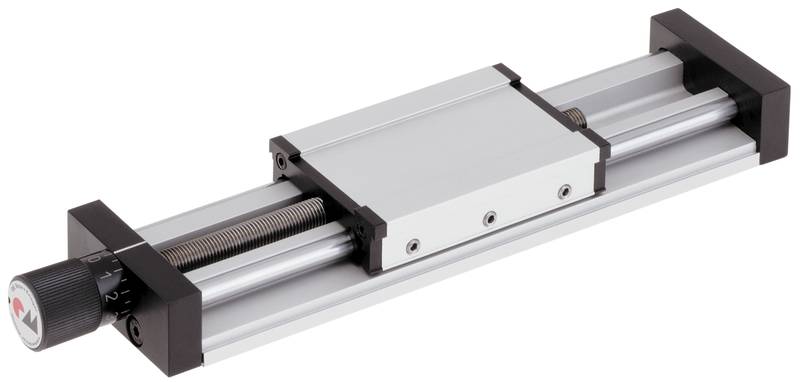
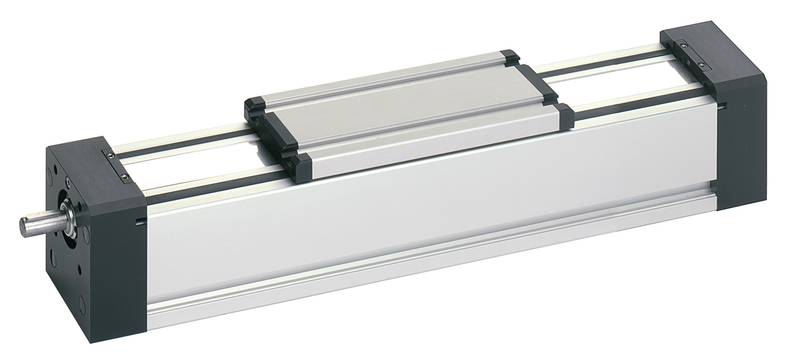
You would think for that kind of money, the designer would address the issue of eccentric records and make some kind of mechanism to center the record a la Nakamichi, consider it has so many laser systems all over the place. Wouldn't that be cheaper to address that first so the laser doesn't have to work so hard to correct the arm just to track the eccentricity of a record, consider so much money is spend on laser detecting system and linear motion tracks, etc... A little too Rube Goldberg for my taste.
The arm is intimidatingly complex but the turntable itself, based on the pictures and description, looks more conventional that's belt-driven with dual motors and hall sensors and heavy platter on magnetic bearing.
The arm is intimidatingly complex but the turntable itself, based on the pictures and description, looks more conventional that's belt-driven with dual motors and hall sensors and heavy platter on magnetic bearing.
- Home
- Source & Line
- Analogue Source
- Angling for 90° - tangential pivot tonearms