Thank you very much for sharing, this is very interesting to see. Nice work.
Now it will be extremely interesting to see the simulation after you include the dome geometry in the throat (with Ath 4.6) - how good the match will be. So far my experience is that the surround of the diaphragm in the throat is not a good thing but then the measured data you show are pretty good, at least compared to what I have seen in the sims. It is also possible that the real-world situation is actually better than the with the theoretically rigid dome - that's one of the things to be seen.
Thank you.
It will be interesting to try the 4.6 version and see if we can get a better correlation between sim and measured result. Looking forward to this.
I have done some variants with throat ID from 27mm (completely covering the surround) and out to where the groove for the grille is at 41mm. So far I like the 31mm version best.
Nice, I suggest you to use VitiuxCAD tool to convert pir files to the frequency domain (a breeze to use by the way) and then you can see polar maps at your convenience
Thank you for this tips. I have not used this before.
Attachments
I have the prototype, it's just fantastic.In the meantime we are progressing on Tritonia baffles (milled from a solid MDF block) ...
Attachments
So I did another print based on the simulations you showed with a conical expansion from the throat.
I kept the overall outside dimensions the same as in my previous versions, but the depth is reduced to 52mm.
I kept the overall outside dimensions the same as in my previous versions, but the depth is reduced to 52mm.
Code:
; Horn Geometry
; -------------------------------------------------------
Throat.Diameter = 31 ; [mm]
Throat.Angle = 40 ; [deg]
Throat.Profile = cone
Throat.Ext.Length = 0
Length = 52 ; [mm]
GCurve = SE
GCurve.SE.Exp = 2.3
GCurve.Angle = 50
GCurve.VertScale = 0.75
Term.s = 0.7
Term.n = 4.0
Term.q = 0.995
Morph.TargetShape = rect
Morph.FixedPart = 0
Morph.StretchExp = 3
Morph.CornerRadius = 35 ; [mm]
Attachments
Directivity could be better above 10kHz, but it's getting quite good in the important range below 10k I think.
Measured in a 600 x 800mm baffle at about 1 meter.
The Vituixcad plot is normalized to the 10 degree curve.
Arta plots is normalized to 0 deg.
Measured in a 600 x 800mm baffle at about 1 meter.
The Vituixcad plot is normalized to the 10 degree curve.
Arta plots is normalized to 0 deg.
Attachments
I would say it's quite consistent with what I saw in the simulations. This is not bad at all, IMO.
Do you set also ABEC.Source.Velocity = axial?
Do you set also ABEC.Source.Velocity = axial?
I would say it's quite consistent with what I saw in the simulations. This is not bad at all, IMO.
Do you set also ABEC.Source.Velocity = axial?
Yes.
ABEC.Source.Shape = spherical
ABEC.Source.Curv = 1
ABEC.Source.Radius = 21
ABEC.Source.Velocity = axial
Ath 4.6 released: #3088
Now you can try to model the particular tweeter used.
Please note that the syntax of the definition file changed since 4.5 - this was again inevitable as too much has changed internally and some items would lost a good meaning. It's not difficult to transfer the existing definitions however - just go throuth the syntax reference in the User Giude. The basic principles remain about the same.
Now you can try to model the particular tweeter used.
Please note that the syntax of the definition file changed since 4.5 - this was again inevitable as too much has changed internally and some items would lost a good meaning. It's not difficult to transfer the existing definitions however - just go throuth the syntax reference in the User Giude. The basic principles remain about the same.
Super interesting, keep up the good work.New prototype on the printer.
Based on a model with the shape of the dome included.
Will be interesting to see how measurements and simulation correlates.View attachment 875368
I'm quite piqued to see the waveguide being built from side to side instead of front to back.
New prototype on the printer.
Based on a model with the shape of the dome included.
Will be interesting to see how measurements and simulation correlates.View attachment 875368
Looks good!
Which printer are you using?
i've got it )
finally, everything works perfect! Thank you for your development! I used your soft, Sketchup and Fusion360 for machining. Result looks good. Will see how they will sounds when i'll finished them )Roman, you are free to start a new thread where we can discuss your new project - as it is a shallow waveguide for a dome tweeter I guess it might interest a lot of people. I could contribute with the little know-how I have, or even adapt Ath more for dome tweeters a bit along the way. It would be interesting to watch the development.
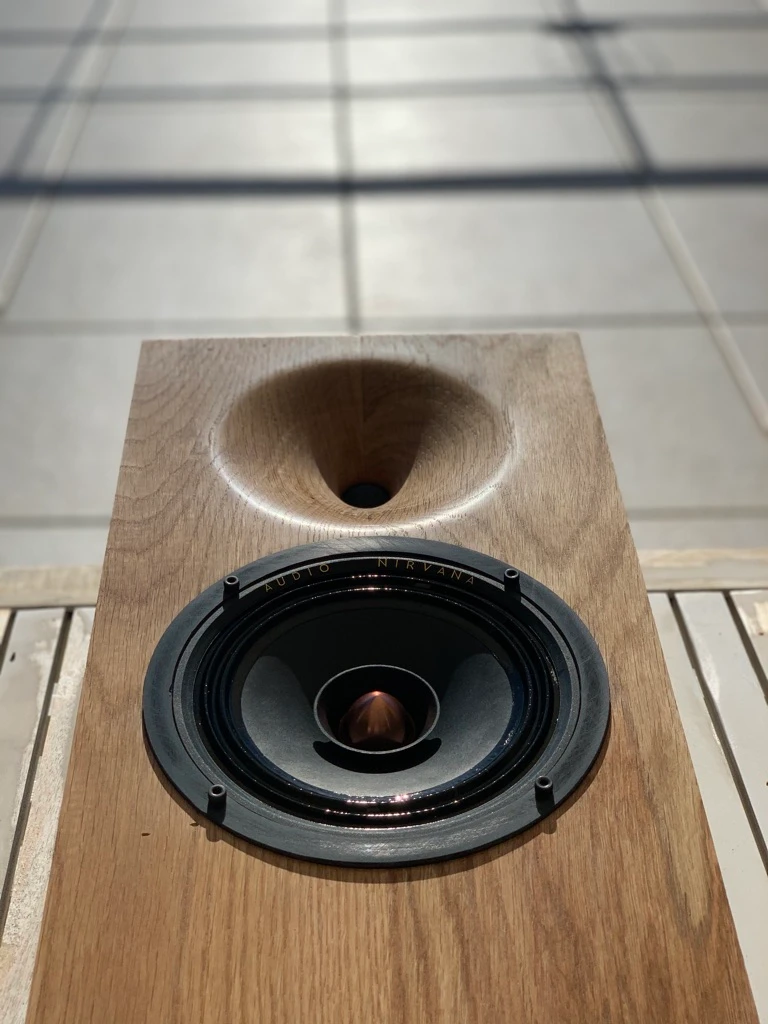
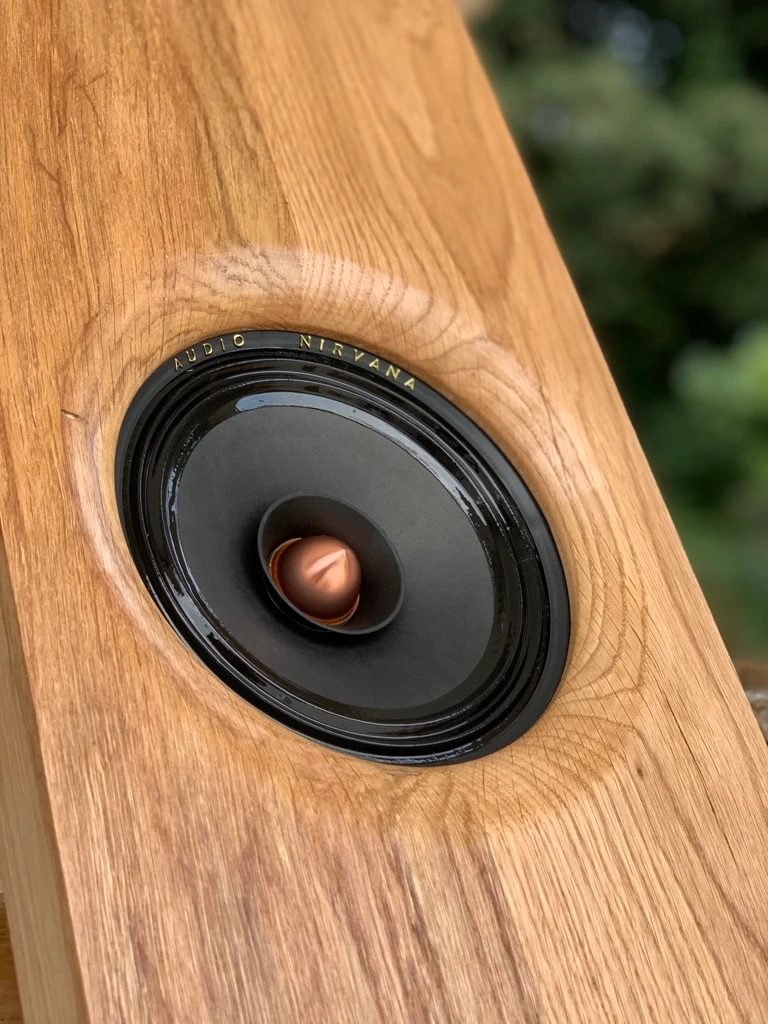
Congrats! So what's the tweeter and did you try to simulate it with the new source modeling capabilities in Ath 4.6?
Dome tweeter waveguide
Hi! Thanks ) the tweeter is Audax TW025A26 dome. I didn't try to make any sim with your new ATH 4.6 I just saw and read about it today. Probably later. Anyway, I'd like to finish this project and make a measurements in real environment.
Hi! Thanks ) the tweeter is Audax TW025A26 dome. I didn't try to make any sim with your new ATH 4.6 I just saw and read about it today. Probably later. Anyway, I'd like to finish this project and make a measurements in real environment.
my TQWT project with waveguides done
New TQWT speaker by inception
Once again, thank you Marcel for your ATH soft! Unfortunately 4.6 don't work on my laptop, I don't know/understand why... But with a previous version and Fusion 360 you can see the results:Congrats! So what's the tweeter and did you try to simulate it with the new source modeling capabilities in Ath 4.6?
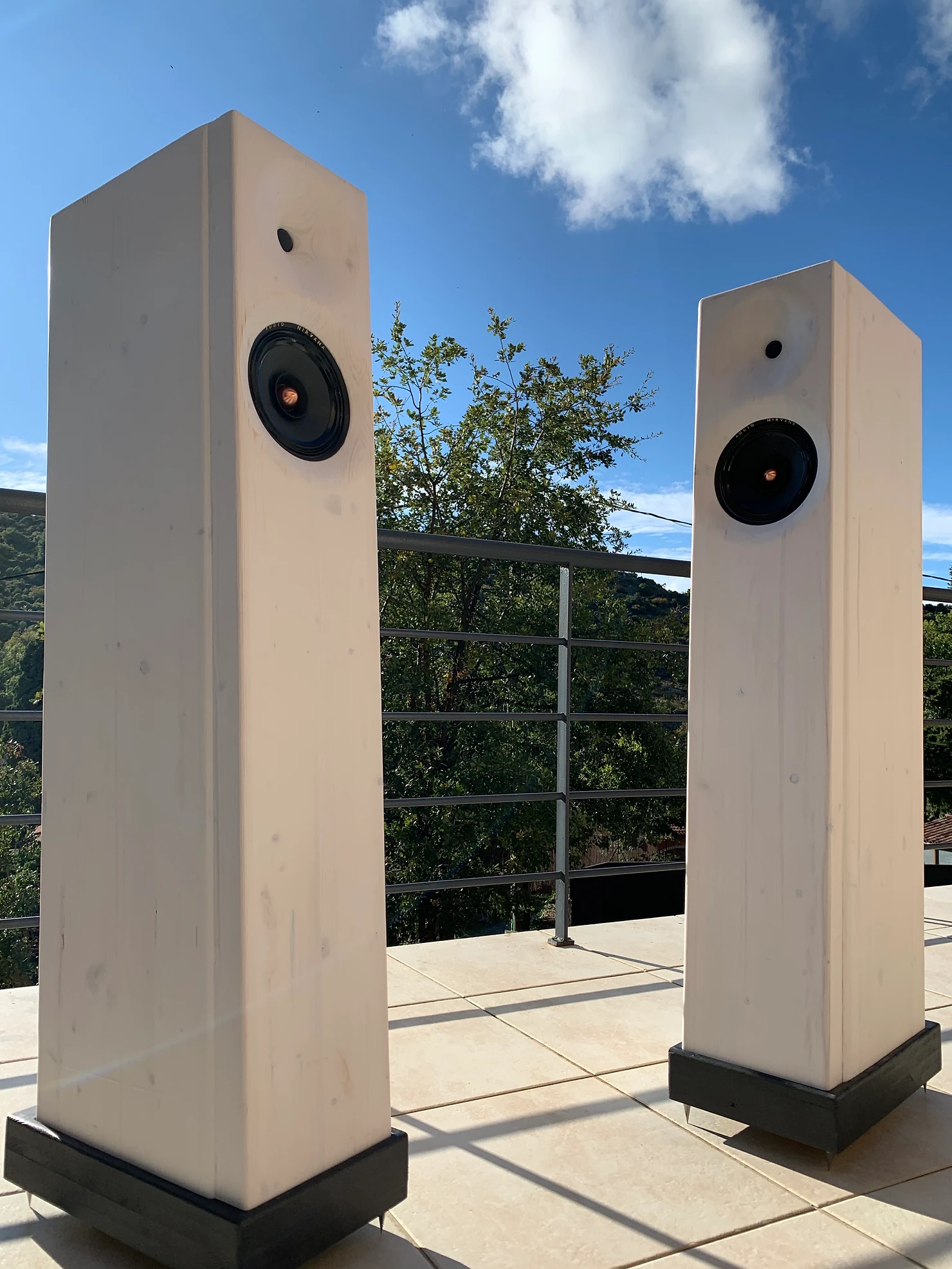
New TQWT speaker by inception
Hello again,
I have finally printed two TinyRs for my Linn Unik speakers, actually I have taken the file generated in the demo exported to Fusion, divided into two halves and printed in a 240mm diameter delta. The first half was made in ABS, with this material I had warping problems, I made the other halves with PETG. The result is quite correct, I have glued the parts with cyanoacrylate with activator and the joint is very good, it has resisted some fall to the ground. The first unit I taped together and put it in the unit to test, the second unit is a bit more elaborate, I have applied a coat of polyurethane primer and now wait for the finish color coat.
At the level of results I have to say that these small speakers are in my workshop of about 60 m2, the effect of the horn is a curious improvement in reproduction, from here I hope to make other prototypes with a little more previous analysis and looking for results , It has been a good test to evaluate the use of the 3d printer for the manufacture of horns.
Thanks Mabat for this awesome app
I have finally printed two TinyRs for my Linn Unik speakers, actually I have taken the file generated in the demo exported to Fusion, divided into two halves and printed in a 240mm diameter delta. The first half was made in ABS, with this material I had warping problems, I made the other halves with PETG. The result is quite correct, I have glued the parts with cyanoacrylate with activator and the joint is very good, it has resisted some fall to the ground. The first unit I taped together and put it in the unit to test, the second unit is a bit more elaborate, I have applied a coat of polyurethane primer and now wait for the finish color coat.
At the level of results I have to say that these small speakers are in my workshop of about 60 m2, the effect of the horn is a curious improvement in reproduction, from here I hope to make other prototypes with a little more previous analysis and looking for results , It has been a good test to evaluate the use of the 3d printer for the manufacture of horns.
Thanks Mabat for this awesome app
Attachments
- Home
- Loudspeakers
- Multi-Way
- Acoustic Horn Design - The Practical Way