Dave,Right now I'm doing only the horizontal plane at 1m, from -45deg to 45 deg. There's no vertical plane in there. Could always be added in, of course.
Thanks for the clarification, but you mean you are doing -90 to plus 90, right (not -45 to + 45)? Or do I misunderstand your meaning?
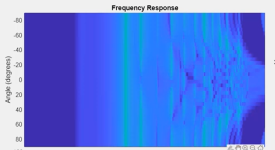
Regarding the vertical plane, one could do that simply by swapping the panel length and width values, and "repositioning" the exciter accordingly, and re-running the model, right?
You certainly don't have to add every feature we request, just the ones I do, haha. We do really appreciate what you are doing.As much as I like working on these advanced topics, I'm worried that I'm getting too far afield from the original intention of why I was developing PETTaLS (it was originally just for my grad students to make graphs and pictures easily!).
Thanks,
Eric
@EarthTonesElectronics
Dave,
Again, concerning the lobes: Below is an an image from one of Ben Zenker's papers. It seems to be showing the number of lobes due to the (1,7) mode as being frequency dependent. Does this make sense to you?
Thanks,
Eric
https://www.researchgate.net/public...zing_the_Off-Axis_Radiation_below_Coincidence
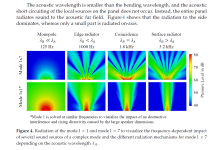
Dave,
Again, concerning the lobes: Below is an an image from one of Ben Zenker's papers. It seems to be showing the number of lobes due to the (1,7) mode as being frequency dependent. Does this make sense to you?
Thanks,
Eric
https://www.researchgate.net/public...zing_the_Off-Axis_Radiation_below_Coincidence
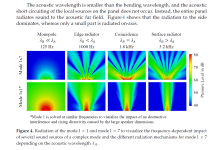
+ @Mark'51Both of these are worth trying.
Yes. I would go to the one which seem the softer or the more flexible if possible in the same way in both direction (which is not a property of plywood!). Maybe sanding a bit the external layers would help (not tested!).
I had a look to what is masonite. It is known under other names as hardboard or isorel (FR). Wood fibers are pressed together at high temperature. No need of additional glue to obtain the material. I think the density dependent on the wood used. Seems quite dense. The panels have a smooth surface on one side and a structured surface on the other. In addition to the doubts for a DML application, the structured surface won't help. I don't have in mind somebody already tested it.
Eric, do you include here the standard speakers you built (TL?)?And I think possibly my favorite speaker that I have made so far is made from Lowes (or HD?) birch plywood.
Eric
Christian
+ @EarthTonesElectronics@EarthTonesElectronics
Dave,
Again, concerning the lobes: Below is an an image from one of Ben Zenker's papers. It seems to be showing the number of lobes due to the (1,7) mode as being frequency dependent. Does this make sense to you?
Thanks,
Eric
https://www.researchgate.net/public...zing_the_Off-Axis_Radiation_below_Coincidence
Hello Eric, hello Dave,
Good to focus on that. After the investigation about the "cavity noise", it is what come next for me.
The directivity measurements I did show clearly that in the midrang/upper midrange a DML can have higher SPL at high angle compare to on axis... or not!. As explained in the paper, the angle increases with the frequency.
The interesting point is all the materials don't behave the same so as for the coincidence frequency, there is a possibility of choice.
One expectation I have from the simulation tool is to understand which property of the material change that. Of course, in front, it supposes the simulation shows this behavior.
This is an example from B Zenker's paper. In A we can see the coincidence frequency pattern. The point now is the pattern in B
From my directivity measurements paper :
Here are 2 examples of panels with medium to high off axis SPL. It is visible on the directivity index too (lower plot, blue arrow B). The second point of negative DI in A being the "cavity resonance" (or what ever cause). If the EPS sample is not so bad too listen, the XPS is not good
The patterns differe a bit from the one of the linked paper because they are from an open back DML with the cancellation of the front and rear waves at 90° . In B Zenker's paper, there is no effect of the rear wave.
And here are 2 materials with low SPL at high angles. Note here the negative DI is due to the "cavity resonance" or what ever other rear side undisered emission
So to me it is clearly one of the key points to increase the quality of the DML.
Please do not make conclusion about materials from those plots. Consider more each as test panels made from one material, some coating or not, dimensions, edge conditions
Christian
Hello Steve,Mark51.
My local wickes store used to have 3mm MDF which worked very well as a dml panel.
I made two 6ft x 2ft panels ,one MDF and the other 3.4 mm ply.
They sounded similar but the MDF had a more damped sound with less coloration than the ply.
The rigidly of the panel is not a problem as long as you make it large enough.
I would show a picture but this site is having problems with my phone again.
Steve.
I didn't remember you tested MDF and the result was similar to ply... Terrible this thread and more probably our memory or what we really read!
Anyway, I add the MDF 3mm which is easy to source to my next set of directivity measurements (with the cardboard) and why not the lid of a camembert Le Rustique box (I just went through your video on Youtube)
Christian
https://www.diyaudio.com/community/attachments/20250210_193838-jpg.1420320/
The MDF panels were when I was on AudioCircle.
Hopefully this link will show the picture as I am still having trouble uploading pictures.
Steve.
The MDF panels were when I was on AudioCircle.
Hopefully this link will show the picture as I am still having trouble uploading pictures.
Steve.
this is the recording.
Christian.this is the recording.
This is the recording of the finger positions.
The post before that shows the positions on the panel.
Steve.
Yep, sorry, I'm working on too many research projects at once.Thanks for the clarification, but you mean you are doing -90 to plus 90, right (not -45 to + 45)? Or do I misunderstand your meaning?
Yes!Regarding the vertical plane, one could do that simply by swapping the panel length and width values, and "repositioning" the exciter accordingly, and re-running the model, right?
Yeah, there is a frequency dependence, and it's pretty complicated. All of the lobes are generally not seen at low frequencies.Again, concerning the lobes: Below is an an image from one of Ben Zenker's papers. It seems to be showing the number of lobes due to the (1,7) mode as being frequency dependent. Does this make sense to you?
Here's a simulation graph of just the (1,1) clamped mode with a point force excitation (in my simulation it's actually called the (2,2) mode for the number of nodes).
Here's just the (7,1) mode...
So when I say that there's a "number of lobes," there's also a frequency dependence to that lobing effect.
Dave,Here's just the (7,1) mode...
![]()
So when I say that there's a "number of lobes," there's also a frequency dependence to that lobing effect.
Oh that's so cool to see plotted. I had no idea the lobes acted like that. And if I'm understanding correctly, at the resonance frequency of the 1,7 mode, you really only "see" three lobes, and it's not until well above it's resonance that all 7 lobes appear. Is that correct? And also, though, I suspect it's only the lobes at resonance that are really loud enough to matter.
Thanks,
Eric
Eric,And if I'm understanding correctly, at the resonance frequency of the 1,7 mode, you really only "see" three lobes, and it's not until well above it's resonance that all 7 lobes appear. Is that correct? And also, though, I suspect it's only the lobes at resonance that are really loud enough to matter.
In this example, the mode shape 1,7 is a reality in the way if you look at the nodal lines at its frequency, you will see it. While the behavior of this mode (alone) over the frequency range is convenient for calculation or analysis but as no reality; it is not visible by itself. The polar plot of a panel at a given frequency is the result of all those elementary modes that can contribute to it.
Correct?
Christian
Yeah, that type of radiation pattern is interesting, and I'm not totally sure what causes it. Seems to occur in the "pebble in a pond" region, but below coincidence.This is an example from B Zenker's paper. In A we can see the coincidence frequency pattern. The point now is the pattern in B
![]()
Here's a picture of experimental results from a glass panel from my PhD thesis, along with my best attempt to recreate that in my software (don't remember what the dimensions were and where/what the exciter was). This type of behavior is definitely apparent in both.
Yes, the relationship between the resonance frequency, wavelength on the panel, and wavelength in air determines what the lobing effect is. So with the right panel dimensions and resonant frequency you should be able to see 7 lobes at the resonance, where here there would only really be 3.Oh that's so cool to see plotted. I had no idea the lobes acted like that. And if I'm understanding correctly, at the resonance frequency of the 1,7 mode, you really only "see" three lobes, and it's not until well above it's resonance that all 7 lobes appear. Is that correct? And also, though, I suspect it's only the lobes at resonance that are really loud enough to matter.
DML Directivity measurements, edition 4
The edition 4 of this paper is available in github (too heavy to be attached here).
The content :
The conclusion:
The edition 4 of this paper is available in github (too heavy to be attached here).
The content :
Comment : the directivity plot of the XPS 20mm panel shows in my opinion why it was not pleasant and the one of the Depron 9mm that I probably discarded this material because of other problems...Additional sources about directivity (videos), a FR of the rear side is added when possible and also a FR of the lateral emission, 2 new materials: XPS 20mm and XPS/depron 9mm. New values and elements in the conclusion.
The conclusion:
And the table of the coincidence frequency :
- The directivity measurements are feasible for a DIYer in a standard environment with a tool like REW. An additional tool to plot the data in the form of a directivity plot is welcome!
- It allows to detect the coincidence frequency (or at least an interval of frequencies). See an example in figure 6
- The measurements of this document confirm that decreasing the thickness of a given material increases the coincidence frequency (see the plywoods). The coincidence frequency of a soft, heavy and thin material is also high.
- Those measurements show also that a panel having the same stiffness in its both direction may show different coincidence frequency according to these directions.
- If no coincidence frequency is detected, the panel doesn't suffer from the strong associated lobes. A test with the same material thicker might confirm the coincidence frequency of the thinner is out of the audio range.
- It is confirmed that the ring diameter of the exciter voice coil makes a low pass filter. The cut off frequency can hide the coincidence frequency which can be an advantage for the panel use or a drawback in test. In test an interface with a smaller diameter (smaller exciter or concentrator) might help in the fc detection
- The measurements have also shown other directivity singularities for open back DML with an exciter in the standard positions. Some of those singularities are similar to the one of a small large range on an open baffle of same dimensions which will need more investigations. See figure 7 for a list of the singularities.
I used the example of the directivity plot from B Zenker's paper because we can see clearly the 2 patterns, below and above the fc. In the example of the XPS20 I provided also, the transition is not so clear. We can only assume the fc is somewhere in the area.Yeah, that type of radiation pattern is interesting, and I'm not totally sure what causes it. Seems to occur in the "pebble in a pond" region, but below coincidence.
Here's a picture of experimental results from a glass panel from my PhD thesis, along with my best attempt to recreate that in my software (don't remember what the dimensions were and where/what the exciter was). This type of behavior is definitely apparent in both.
The most interesting aspect appears when we compare the panels with the level out of axis and how they are pleasant to listen or not. I am in the opinion there is a good correlation.
The question is which kind of property of the material is at play here? My first attempt of answer would be a frequency dependent damping. The subsidiary question being is there some coating that could help?
Christian
Now that I have proven to myself that 1" thick XPS isn't going to work for me, I want to remove the exciter and re-use it. I'm not so concerned about preserving the panel, just the exciter.
So I have a few questions --
1. What has been shown to be the least-destructive method of removing an exciter from a panel? It currently is attached using the as-supplied double-sticky tape.
2. What is the best known way to remove the old double-sticky tape that remains on the exciter? I have a variety of solvents -- N-Hexane, Acetone, Toluene, Xylene, citrus oil (A.K.A. Limonene) and Ethyl Acetate. In my experience some solvents don't really remove PSA, they just make it sort of gummy/slimy. In my experience Limonene and Toluene seem to work the best for most PSA's but maybe there's something even better.
3. What is the best way to re-attach an exciter, particularly if the attach/remove cycle could be repeated several times? I'm leaning toward something like Gorilla brand double-sticky tape but, again, perhaps there's something better out there. The Gorilla stuff IS spendy.....
So I have a few questions --
1. What has been shown to be the least-destructive method of removing an exciter from a panel? It currently is attached using the as-supplied double-sticky tape.
2. What is the best known way to remove the old double-sticky tape that remains on the exciter? I have a variety of solvents -- N-Hexane, Acetone, Toluene, Xylene, citrus oil (A.K.A. Limonene) and Ethyl Acetate. In my experience some solvents don't really remove PSA, they just make it sort of gummy/slimy. In my experience Limonene and Toluene seem to work the best for most PSA's but maybe there's something even better.
3. What is the best way to re-attach an exciter, particularly if the attach/remove cycle could be repeated several times? I'm leaning toward something like Gorilla brand double-sticky tape but, again, perhaps there's something better out there. The Gorilla stuff IS spendy.....
@Mark'51
1) I just stick something like a spatula inbetween the exciter and plate in a few places and bend until it is loose.
2) Put exciter in freezer for a few minutes. The tape comes off easy when cold.
3) Double sided sticky tape is probably best if you want to reattach. I use 3M 9088, and it is also not cheap, but a roll will last you ages and is useful for a lot of things.
1) I just stick something like a spatula inbetween the exciter and plate in a few places and bend until it is loose.
2) Put exciter in freezer for a few minutes. The tape comes off easy when cold.
3) Double sided sticky tape is probably best if you want to reattach. I use 3M 9088, and it is also not cheap, but a roll will last you ages and is useful for a lot of things.
It's going to get down into the 20's tonight. Maybe that will be cold enough to get the tape off.....
If you're going to experiment often, then try what I do:3. What is the best way to re-attach an exciter, particularly if the attach/remove cycle could be repeated several times? I'm leaning toward something like Gorilla brand double-sticky tape but, again, perhaps there's something better out there. The Gorilla stuff IS spendy.....
Use masking (painters) tape - the green version -> 35-50mm wide about 75mm long (long enough to get to either end of when the exciter is mounted). Stick it firmly where you want fix the exciter, then use Gorilla wood glue or equal on the exciter ring. If done correctly, it will hold fast, and can be peeled off later without damaging the panel. Heavy exciters should be supported whichever method you use.
Commonly the tape stays on the exciter and you may even be able to relocate it for another trial before needing to re-do the tape.
Cleaning the tape and glue from the exciter is a trivial matter.
As for your other question about removing the original sticky tape - try the least damaging chemical first - if goo remains, just roll it off with your fingers.
Eucy
I like the tape idea! Sort of reminiscent of an early method of getting 3D printed parts to release from the bed.
One more question, regarding plywood (whatever the species). I'm thinking of a light coat of varnish, at least on the frontside, Mostly to make it less prone to pick up smudges. This thing has to keep the wife happy too (or at least mollified). But of course I'm wondering how it will affect the sonic properties of the panel. PVA on EPS panels appears to be a preferred treatment but I'm not so sure w/regard to the much heavier and stiffer plywood.
I suspect the properties of the plywood will dominate, at least with light coats of varnish or paint. But I'm curious if there has been any characterization regarding this. Just to be on the safe side I'm not going to treat the back of the panel.
I picked up a 2 x 2 piece of 1/4" birch ply at Lowes today. I flexed the panel along both axes to see if its rigidity is significantly different for one vs. the other. There is a slight difference but nowhere near as great as, say, Coroplast or Plaskolite.
Based on some experience with polycarbonate twin-wall (for our greenhouse) I'd say that the polycarbonate is somewhere between the plywood and Coroplast, in terms of the X-Y anisotropy. It is VERY rigid on one axis, noticeably less-so on the other: but both axes are a lot more rigid than corrugated polypropylene panels.
One more question, regarding plywood (whatever the species). I'm thinking of a light coat of varnish, at least on the frontside, Mostly to make it less prone to pick up smudges. This thing has to keep the wife happy too (or at least mollified). But of course I'm wondering how it will affect the sonic properties of the panel. PVA on EPS panels appears to be a preferred treatment but I'm not so sure w/regard to the much heavier and stiffer plywood.
I suspect the properties of the plywood will dominate, at least with light coats of varnish or paint. But I'm curious if there has been any characterization regarding this. Just to be on the safe side I'm not going to treat the back of the panel.
I picked up a 2 x 2 piece of 1/4" birch ply at Lowes today. I flexed the panel along both axes to see if its rigidity is significantly different for one vs. the other. There is a slight difference but nowhere near as great as, say, Coroplast or Plaskolite.
Based on some experience with polycarbonate twin-wall (for our greenhouse) I'd say that the polycarbonate is somewhere between the plywood and Coroplast, in terms of the X-Y anisotropy. It is VERY rigid on one axis, noticeably less-so on the other: but both axes are a lot more rigid than corrugated polypropylene panels.
Definitely NOT PVA on the plywood - light coats of Auto Acrylic clear coat OR shellac are by far the best finishes to use IMO. They can also be used together - Use shellac to add colour/tone, lightly sand and then coat with acrylic clear for a robust light finish. Shellac by itself is fine provided it doesn't get any moisture on it as it will leave white marks - shouldn't be a matter of concern with vertical surfaces.
Be aware that shellac takes some practice to achieve a good, streak free result.
If you want a solid colour, again Auto Acrylic is the go.
Eucy
Be aware that shellac takes some practice to achieve a good, streak free result.
If you want a solid colour, again Auto Acrylic is the go.
Eucy
- Home
- Loudspeakers
- Full Range
- A Study of DMLs as a Full Range Speaker