Eric.
The designer of the podium panels ,in one of his interviews, mentioned designing the panel to ring like a bell !
Obviously he did not mean this literally, but to have a free edge.
The only drawback for me is the heavy honeycomb panel, which gives the sense of lacking HF, even though it probably measured very well.
I had the same problem with my 3mm ply panels even though they had a huge hump in the 10k and above area ,which you would have thought would make them sound bright.
We are obviously like chalk and cheese when it comes to the sound we like, but I would think we are not too far apart as dml panels tend to have a similar dml sound.
I have just put up the other ply panel ,made from a cheep crate , but without mounting it in a canvas frame.
This panel also has a high output it seems, I'll have to compare this to my other types of panels, very interesting.
The un-mounted panel has some nasty peaks in the response, which I believe to be exciter panel noises.
If I hold the panel between my hands the peaks disappear into the link noise, but they are obviously still there.
I notice these peaks on some of my panels that I have not treated.
The peaks are still on the canvas panel but are well suppressed by the glue and canvas.
Steve.
The designer of the podium panels ,in one of his interviews, mentioned designing the panel to ring like a bell !
Obviously he did not mean this literally, but to have a free edge.
The only drawback for me is the heavy honeycomb panel, which gives the sense of lacking HF, even though it probably measured very well.
I had the same problem with my 3mm ply panels even though they had a huge hump in the 10k and above area ,which you would have thought would make them sound bright.
We are obviously like chalk and cheese when it comes to the sound we like, but I would think we are not too far apart as dml panels tend to have a similar dml sound.
I have just put up the other ply panel ,made from a cheep crate , but without mounting it in a canvas frame.
This panel also has a high output it seems, I'll have to compare this to my other types of panels, very interesting.
The un-mounted panel has some nasty peaks in the response, which I believe to be exciter panel noises.
If I hold the panel between my hands the peaks disappear into the link noise, but they are obviously still there.
I notice these peaks on some of my panels that I have not treated.
The peaks are still on the canvas panel but are well suppressed by the glue and canvas.
Steve.
Because I'm lack of measure tools so really not sure how the FS change. And the main purpose of the method is for easy change exciters on test materials.@hkguy6
I would like to come back o the attachment method you described hkguy6 in the post #4750
Here is a quick test where I added a metallic washer between the exciter voice coil and the panel. As usual those days, it is a XPS 9mm 20x30cm not really special, only for tests purpose by comparison.
The washer is 27mm diameter with a 15mm hole, 2.7mm thick so about 8.4g (evaluation, no balance...) which is a lot compare to the voice coil mass 1.6g!
Looking at the FR, it is incredible. The bandwidth is not really affected by this additional weight. One could think the linearity is better.
- blue is the XPS panel as reference
- green is with the washer added
Looking at the spectrogram, the picture is not so good. Some frequencies remain a long time.
The technique seems promising. Here the idea was to push a bit far in weight to see if there is FR limitation... and this washer was just under my eyes close to the exciter diameter. The screw is also missing in this test.
So who will propose an easy to make light enough solution ?
Christian
About the weight, I don't think the weight is really matter as I said before. The washer weight is added to the whole system instead of on the voice coil only.
You may use different materials to make your own washer. And it's not necessary round or same size as the voice coil. For example the original washer comes with the Aiyima 50MM is aluminium. And I also use polywood to make washer. Different material with different density and rigidity have different transistion nature it may affect FS and efficiency.
Hi Steve
I have brought home a selection of large sheets of the Ribbed Impact Board today. along with a 800 x 800 Board of Birch Ply at about 3-4mm and a Few Green MDF 1000 x 1000 Boards at 6mm.
I have the panels to get underway.
If you would like to try the ribbed board send me your PM me your address, and I will see if I can get a courier to deliver it, a local shop offers courier pick ups as a service.
John
I have brought home a selection of large sheets of the Ribbed Impact Board today. along with a 800 x 800 Board of Birch Ply at about 3-4mm and a Few Green MDF 1000 x 1000 Boards at 6mm.
I have the panels to get underway.
If you would like to try the ribbed board send me your PM me your address, and I will see if I can get a courier to deliver it, a local shop offers courier pick ups as a service.
John
EricChristian,
Nope. Just about right. Per my spreadsheet, they should have a B (or D if you prefer) of about 10 Pa m3, which is probably close to 3 mm plywood. BUT with a B/mu^3 of around 100, so rivaling PS foams in that regard. In theory, at least. This construction has literally been on my list of things to try (#5 actually), since I developed my spreadsheet. But I was afraid the fiberglass (or carbon) would suck into the cavities of the nomex honeycomb, unless I used a prepreg. But apparently it can be done just fine with plain old fiberglass and epoxy. The process he followed is actually simpler than my process for carbon/balsa panels.
Eric
I have in my notes a bending stiffness of even 20Pa.m³ for the 3mm plywood. Long time without having a look to that so perhaps I would have to reevaluate it... Yes a B/mu³ of 100 is impressive. Even for me who has no experience in composite, the process seems not too complicated. The key point is the tooling with the teflon board. Is there alternative to that? Or is it something available from stores dedicated to composites?
Christian
NaRenaudYou are vacuum bagging? It can be done even without vacuum bagging by doing one side at a time and letting it fully cure. You wet one layer on your release surface then lay the honeycomb on it and then weights and let it cure (I've seen a layer of closed cell and a piece of plywood laid carefully on the honeycomb to give even pressure). As long as you don't overwet the honeycomb won't wick up too much. Then when it's cured repeat for the over side. I think that same guy did this with aluminum honeycomb.
If I sum up the process : the fiber glass mat is impregnated with the epoxy resin while being in close between 2 sheets of plastic film. The fiber glass is put on a tooling surface (teflon), the nomex on top then some board (plywood) and weight to press until the resin cures. When done do the same for the second side. Is it correct? What are the indication for the resin, Sorry for the basic question, I am completly ignorant about those techniques for now! Do other material work instead of teflon? Glass?
Christian
hkguy6,Because I'm lack of measure tools so really not sure how the FS change. And the main purpose of the method is for easy change exciters on test materials.
About the weight, I don't think the weight is really matter as I said before. The washer weight is added to the whole system instead of on the voice coil only.
You may use different materials to make your own washer. And it's not necessary round or same size as the voice coil. For example the original washer comes with the Aiyima 50MM is aluminium. And I also use polywood to make washer. Different material with different density and rigidity have different transistion nature it may affect FS and efficiency.
For now I don't have the same understanding. The washer is a local weight directly on the voice coil. The washer I tested was really heavy with not so big impact on the efficiency or the bandwidth. It is a good idea. The academic papers showing a simple model of the DML modeled the voice coil by an inductance and a high pass filter is expected somewhere but not found... I have difficulty in following your idea of assimilating the washer to panel. No matter for now. We'll see what will be the next learnig.
Christian
Eric,I'm not sure I would go as far as Christian to say clamped is loudest, but I do agree that constraining the edges can have a positive effect on both FR and overall output. One of the NXT patents demonstrated this but I'd have to look to find it.
For me, so far the best constraint seems to be attaching the panel to a rigid frame around most or all of the perimeter using a double sided foam tape. This approaches what engineers refer to as "simple supports" which implies that the edges of the panels can't move (not much, anyway), but can rotate. So the perimeter is mainly like a hinge. I think this is effectively what the Tectonic supports do, although their combination of rigid and compliant supports may be more nuanced.
Here are two examples comparing panels with frames and foam, compared to the same panels hanging from strings (free edges). In both cases the biggest difference is at the low frequency end, where the framed panels provide much greater output than the free panels. At higher frequencies, the responses tend to converge. The first is for a 16"x23" CF/balsa panel, and the second is for a 14"x48" plywood panel. In both cases, the same exciter was used for both test, and the amp was set to the same volume, and the mic was placed at 1 meter. I have done this many times and see pretty much the same thing every time.
Eric
View attachment 1040203
View attachment 1040205
I come to almost the same observations. I'd try to share some FR to show that. At the moment I am experimenting with XPS (for convenience). As it is a light and quite flexible material and my test panel is small (20x30cm), I think the foam leads to something more close to clamp conditions; By removing it in the corner, in the way of the Tectonic patent, the result is better.
Christian
Sure. The frame is a bit overdesigned, but maybe not as much as you might think. The exciter position that works best is about 5 inches above the center, and 1.5 inches to one side. Two exciters works well with the second one 1.5 inches to the opposite side. With two placed thus, the frequency response is almost identical. But (for reasons I don't understand), the impulse response is slightly cleaner. The opposite is true if the exciters are much farther apart.Do you have any photos of your 14"x48" plywood panels mounted in the foam?
Last picture shows the foam tape. In this case it's 3M Extreme double sided mounting tape, cut to about 1/2" wide. It turns out that the FR is pretty sensitive to the choice of foam tape. Even just the tape width. As you can see, this is pretty thin foam, only about 1.5 mm I imagine. I usually don't run the tape all the way to the corners, mainly so I have a chance at separating the panel from the frame for another trial. This is the highest damping foam tape I've used. It works well for this panel, but may not be the best for every panel.
https://www.scotchbrand.com/3M/en_U...ing-Tape/?N=4335+3289430068+3294529207&rt=rud
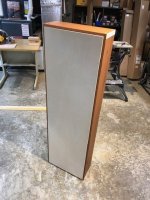
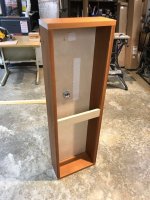
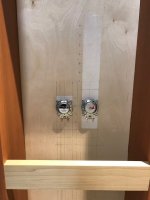
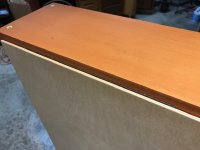
SteveLeob.
If trying to run a panel full range or for PA use ,manipulating a panel is a useful tool, but if for home use you are rolling off the response below 300hz or so , it becomes unnecessary.
when damping the edges with foam or rubber you are restraining the reflections, reducing dml modes and boosting others,
the panel is being pushed more into a bendingwave panel speaker.
the more damping the more into a bendingwave it becomes.
This alters the sound of the rest of the frequencies ,that you don't necessarily want to alter ?
there are many such speakers on the market today, with the exception of the podium of course.
I have found that clamping a dml panel ,tends to make it sound more like a conventional type of speaker.
which is not a problem ,if you like the sound of conventional speakers ?
Dml panels can be manipulated in so many ways, it depends on what you want from them.
Steve.
Here are 2 FR with a low smoothing. One is free edge - red (2 strings suspension), the second - green is frame and foam ( just 40% of each side to keep the corner free). I can't make a relation between what you say Steve and those graphs. I must admit it is panel for measurements, no listening test...
Christian
Yes it might come from this paper. Somewhere, they mention 3dB difference. Fully agree it is in the detrimental of the FR. All the current indications go to the simply supported conditions.Christian,
Now I recall at least one source of that information: it was this paper:
https://eprints.soton.ac.uk/369232/1/Eprints.pdf
where they say:
View attachment 1040288
But the caveat is (as Loeb pointed out), the the clamped plate has a higher fundamental frequency than other boundary conditions. So while it might be most efficient above its fundamental, its fundamental is higher. So there is a trade off. My experience so far is that a "simple" boundary (i.e. like a hinge which limits displacement but not rotation), rather than clamped is a pretty good compromise between high radiation efficiency without driving the fundamental needlessly higher.
Eric
I remember from this interview the ringing panel but also the time spent to find the right suspension and the quality of his relation with his supplier to find the right material. something to read again?The designer of the podium panels ,in one of his interviews, mentioned designing the panel to ring like a bell !
Obviously he did not mean this literally, but to have a free edge.
Steve,Christian.
thank you for the recording.
I'm the recording you can hear a lot of the room.
have you tried to make a recording of moving closer to the speakers ,to see if you can find the sweet spot, hopefully where the room sound mostly disappears ?
But not so close as to make them sound like headphones.
In the description of recforge they say it still has a stereo setup, you can also have dual mono.
some phones will not allow stereo setup I'm afraid.
the hi-Q recorder does list some phones that will work with their app.
It looks like I will have to pay for the hi-Q app when I get my new phone, I only hope the phone will allow the other mic to be used ?
Steve.
For now, I haven't spent much time in trying it to work. It was just a quick test.
Eric,Sure. The frame is a bit overdesigned, but maybe not as much as you might think. The exciter position that works best is about 5 inches above the center, and 1.5 inches to one side. Two exciters works well with the second one 1.5 inches to the opposite side. With two placed thus, the frequency response is almost identical. But (for reasons I don't understand), the impulse response is slightly cleaner. The opposite is true if the exciters are much farther apart.
Last picture shows the foam tape. In this case it's 3M Extreme double sided mounting tape, cut to about 1/2" wide. It turns out that the FR is pretty sensitive to the choice of foam tape. Even just the tape width. As you can see, this is pretty thin foam, only about 1.5 mm I imagine. I usually don't run the tape all the way to the corners, mainly so I have a chance at separating the panel from the frame for another trial. This is the highest damping foam tape I've used. It works well for this panel, but may not be the best for every panel.
https://www.scotchbrand.com/3M/en_U...ing-Tape/?N=4335+3289430068+3294529207&rt=rud
View attachment 1040403 View attachment 1040405 View attachment 1040406 View attachment 1040408
Do you have made tests and calculation to estimate how close (or far) a design is from the targeted conditions? Or in other words where the suspension is between simply supported to clamped?
By the way, nice realization. The "oversized" frame seems a solution to keep the panel standing up by itself.
Christian
Mostly right...in the video he uses the two sheets of plastic to help keep the very thin fiberglass from distorting while wetting with resin and to help squeeze out excess resin. The plastic is removed before the nomex is applied. It's useful but not necessary. You can just lay your glass or CF on a smooth surface that won't bond too badly and roll epoxy onto it then apply the honeycomb as you said. The honeycomb soaks up resin so you want to squeegee out any excess resin before applying the honeycomb.NaRenaud
If I sum up the process : the fiber glass mat is impregnated with the epoxy resin while being in close between 2 sheets of plastic film. The fiber glass is put on a tooling surface (teflon), the nomex on top then some board (plywood) and weight to press until the resin cures. When done do the same for the second side. Is it correct? What are the indication for the resin, Sorry for the basic question, I am completly ignorant about those techniques for now! Do other material work instead of teflon? Glass?
Christian
A Teflon surface is very helpful if you do a lot of composites as it requires no preparation at all but most people don't have a Teflon surface. Most people use a mirror or other sheet of glass and spray it with some mold release film to make it easier to separate after curing. If you want an easy release you have to spray and let dry many times to build a layer...if you don't mind a little careful work to separate from the glass then you can use less, I've even seen people use car wax on the glass and it seems to work well enough.
There are other products to make the job easier and more consistent but at the very least you only need:
-Your glass or carbon fiber
-low viscosity resin
-a plastic squeegee
-a large mirror
-some release spray or wax for the mirror
-Your core material
-Weights that can be places evenly
-some patience.
-rubber gloves
Also the temperature should not be cold...I left my DML panels outside to cure last night after applying epoxy and it was too cold and I ruined my bond by pulling on it before it was fully cured. It was a sticky mess. Eventually it would have cured if I left it alone a day or two but I was not so smart.
Christian,Eric,
Do you have made tests and calculation to estimate how close (or far) a design is from the targeted conditions? Or in other words where the suspension is between simply supported to clamped?
By the way, nice realization. The "oversized" frame seems a solution to keep the panel standing up by itself.
Christian
It's much, much closer to the simply supported condition than clamped.
And yeah, they stand up themselves! That was just a happy accident, however.
Eric
My problem is , knowing how good cone bass drivers are , and the likes of the B139 , is it worth trying to build a sub dml panel (that isn't actually dml anyway ?) With all its problems ?
Do you have any thoughts on this ?
Steve.
Steve,
I was playing with it only for the novelty of having an "all-DML" system. I'm sure my simple DML sub wouldn't compete with any decent pistonic cone sub.
Eric
Steve,We are obviously like chalk and cheese when it comes to the sound we like, but I would think we are not too far apart as dml panels tend to have a similar dml sound.
Good thing I used to spend time in Newcastle. Otherwise I would not have known what "chalk and cheese" meant!
Eric
I'm with you. After my experience experimenting and getting my first fully functional panels going I have a strong urge to get rid of the remaining box in my media area. The sub won't go to waste, it can have a new home augmenting my bedroom system. I also have a bar area downstairs that needs a system....if I had a spare receiver/amp lying around I would probably already be building a second set of DMLs.Steve,
I was playing with it only for the novelty of having an "all-DML" system. I'm sure my simple DML sub wouldn't compete with any decent pistonic cone sub.
Eric
@Veleric &all
Eric,
I propose to adopt the following naming :
Assuming we can reach by the suspension simply supported condition and neglecting the effect of the exciter (not sure it is true for the low B value)...
* B/µ = [2.a².f0/pi/(1+1/k²)]²
My approach is to set 'a' as my target in width for the panel, f0 related to the targeted bandwidth, k as the panel ratio.
I made a spreadsheet of that to give the value of B according to µ
Here is a screenshot, attached is the zip file (xlsx format exported from OpenOffice... Linux computer!). Let me know if it works and if any mistake.
In yellow the parameter cells. 2 values of f0, 2 values of k (1.44 = 577/400, 3.4 you suggested
With that I understand why you propose a value of 10 for B where I am more thinking 3 or even less!
Christian
Eric,
I propose to adopt the following naming :
- B bending stiffness Nm or Pa/m³
- µ aerial mass km/m²
- a short side dimension m
- b long side dimension m
- k = b/a side ratio
- f0 = 1st resonance mode (1,1) Hz
Assuming we can reach by the suspension simply supported condition and neglecting the effect of the exciter (not sure it is true for the low B value)...
* B/µ = [2.a².f0/pi/(1+1/k²)]²
My approach is to set 'a' as my target in width for the panel, f0 related to the targeted bandwidth, k as the panel ratio.
I made a spreadsheet of that to give the value of B according to µ
Here is a screenshot, attached is the zip file (xlsx format exported from OpenOffice... Linux computer!). Let me know if it works and if any mistake.
In yellow the parameter cells. 2 values of f0, 2 values of k (1.44 = 577/400, 3.4 you suggested
With that I understand why you propose a value of 10 for B where I am more thinking 3 or even less!
Christian
Attachments
Last edited:
Sorry that I can't proof that. I just simply think... For example the art panel (canvas). We glue the voice coil to the polywood, the polywood glue to the canvas. The polywood here is exactly acts like a washer, a quite heavier washer. It also a local weight directly on the voice coil.hkguy6,
For now I don't have the same understanding. The washer is a local weight directly on the voice coil. The washer I tested was really heavy with not so big impact on the efficiency or the bandwidth. It is a good idea. The academic papers showing a simple model of the DML modeled the voice coil by an inductance and a high pass filter is expected somewhere but not found... I have difficulty in following your idea of assimilating the washer to panel. No matter for now. We'll see what will be the next learnig.
Christian
- Home
- Loudspeakers
- Full Range
- A Study of DMLs as a Full Range Speaker