Here's a new speaker using the Aurasound NS3. I'm impressed with the very useable high excursion and nice off-axis sound.
The quasi-anechoic response is derived from the merging of a 3" measurement with a 14" gated measurement at 5.5kHz. I used an EMM-6 mic calibrated by Cross-Spectrum. Mic and DAC responses are compensated for in the unfiltered response graph. The filter was made using DRC with my custom psychoacoustic configuration, as well as REW for some subsequent low-end tuning. Final response is critically damped with an Fs of 65Hz. I did some listening with the addition of baffle step compensation and it sounds very good.
Construction: 1/4" MDF bonded with super glue, inside joints sealed with wood glue, inside/outside surface sealed with oil, 3 coats of acrylic latex paint rolled on. I made gaskets for the drivers from a vinyl damping sheet, and there is a small piece of recycled packing material inside to damp the (fairly benign) high pitched structural resonance.
The stand bases have adjustable set screws for balance/leveling. I was having trouble with threaded inserts splitting the wood since the screws are near the corners, so I just tapped the (1/2") MDF itself (which allows for a tighter grip of the screw anyway). The speakers are resting on polyurethane "pucks" made from pairs of low profile flat-top (cylindrical) bumpers joined together by the adhesive sides. The grip is good enough that if the speakers are pushed from behind, the stand will tilt forward as if attached to the speakers.
The quasi-anechoic response is derived from the merging of a 3" measurement with a 14" gated measurement at 5.5kHz. I used an EMM-6 mic calibrated by Cross-Spectrum. Mic and DAC responses are compensated for in the unfiltered response graph. The filter was made using DRC with my custom psychoacoustic configuration, as well as REW for some subsequent low-end tuning. Final response is critically damped with an Fs of 65Hz. I did some listening with the addition of baffle step compensation and it sounds very good.
Construction: 1/4" MDF bonded with super glue, inside joints sealed with wood glue, inside/outside surface sealed with oil, 3 coats of acrylic latex paint rolled on. I made gaskets for the drivers from a vinyl damping sheet, and there is a small piece of recycled packing material inside to damp the (fairly benign) high pitched structural resonance.
The stand bases have adjustable set screws for balance/leveling. I was having trouble with threaded inserts splitting the wood since the screws are near the corners, so I just tapped the (1/2") MDF itself (which allows for a tighter grip of the screw anyway). The speakers are resting on polyurethane "pucks" made from pairs of low profile flat-top (cylindrical) bumpers joined together by the adhesive sides. The grip is good enough that if the speakers are pushed from behind, the stand will tilt forward as if attached to the speakers.
Attachments
g post #541
Hi there g: Impressive FR graph, what is the Vb for this build? Hope you will post more listening impressions. Looks like you have a great start on a FAST, by adding a bass unit. ...regards, Michael
Hi there g: Impressive FR graph, what is the Vb for this build? Hope you will post more listening impressions. Looks like you have a great start on a FAST, by adding a bass unit. ...regards, Michael

Hi, j. Enclosure volume is 0.1 cu. ft. (2.8 l). SPL is adequate for my needs, and I think these could work well for a FAST if a low-order, low freq x-over is desired.
BYRTT, Thanks again for the kind words. I figured I owed you a pretty graph by now 😉.
BYRTT, Thanks again for the kind words. I figured I owed you a pretty graph by now 😉.
Hi, I have been reading this post page by page, I haven't reached the very last one. But I have a big question since the beginning, that I haven't seen answered anywhere, not here and not in other places.
First of all, I might know a lot about other stuff, but I am next to illiterate in this particular field, so please bear with me.
So this is my existential doubt: is there a reason why the original design of this speaker asks for a face of it to be truncated? I have seen the two options, either on a 4 side pyramid, or a 3 side one, ending up with a square or triangle for the "flat" face where the speaker would be installed.
BUT, why not install it on a regular rhombus face? I don't see the reason for this, I just made a model in cardboard of the 12-sided figure, and my drive will fit in any of those.
And, a bonus question, is there a reason why I should not try to use 4 drivers on the same assemby? Because I was planning on doing two versions, one with a single driver in one of the rhombus, and one with 4 smaller ones on 4 adjacent rhombi.
Thank you for the feedback. I would love to hear the opinion of Tesserac and Gmad in particular, since they are the strongest supporters of this kind of design.
First of all, I might know a lot about other stuff, but I am next to illiterate in this particular field, so please bear with me.
So this is my existential doubt: is there a reason why the original design of this speaker asks for a face of it to be truncated? I have seen the two options, either on a 4 side pyramid, or a 3 side one, ending up with a square or triangle for the "flat" face where the speaker would be installed.
BUT, why not install it on a regular rhombus face? I don't see the reason for this, I just made a model in cardboard of the 12-sided figure, and my drive will fit in any of those.
And, a bonus question, is there a reason why I should not try to use 4 drivers on the same assemby? Because I was planning on doing two versions, one with a single driver in one of the rhombus, and one with 4 smaller ones on 4 adjacent rhombi.
Thank you for the feedback. I would love to hear the opinion of Tesserac and Gmad in particular, since they are the strongest supporters of this kind of design.
That will be a mess as the wood glue will smear and drip all over the place as you fumble to hold it together. I think you tack with dots of hot melt and then use a hypo needle to inject wood glue into crevice between panels at the edges.
Maybe it's my 'early music' background, but how about using the stuff that has been used for centuries on violins, i. e., hide glue? You can re open any of the panels for repairs if need be.
smell for one, and extremely hot steam which can easily burn you and if you use mdf as your construction material your knackered even plywood would delaminate.
Last edited:
smell for one, and extremely hot steam which can easily burn you and if you use mdf as your construction material your knackered even plywood would delaminate.
True, but, and I hadn't read the posts around page 23, if you think of the speaker enclosure as a sort of musical instrument, and use tonewood, it might be feasible. At any rate I would give it a try, and if you use softer hide glue from rabbit skin, you don't need it to be that extremely hot, I know of a luthier that has some kind of natural glue that works at room temperature (he uses for repairs, such as small cracks).
By the way, regarding construction, I think it is fairly straightforward, I am thinking in aproximating the rhombi to final size on a table saw, and then cut them with a mold and a 30 degree tracing bit.
Regarding wood, I know of a source of the highest possible tonewood, which is not that expensive, if anyone in Europe is interested, I can give that away. It's about 100 euros for a square meter, of the highest straight and close grain, quarter-sawn spruce. I would not use that myself to begin with, but it would be nice to experiment with such wood, if, as many here do, you think that the cabinet walls contribute to the sound.
So this is my existential doubt: is there a reason why the original design of this speaker asks for a face of it to be truncated? I have seen the two options, either on a 4 side pyramid, or a 3 side one, ending up with a square or triangle for the "flat" face where the speaker would be installed.
Without the truncation, you would not have a large flat square to mount the driver against. All the faces are parallelgrams in shape and smaller.
Hide glue would work fine if you have it and are used to it. Hot melt is just easier for me as it has a trigger gun dispenser and hardens in 40 seconds. I am impatient. 🙂
Hi, White Fang.
My experience is limited to the sqare truncated enclosure. I believe this is Matthew Kennedy's (Tesserax) preferred design for two reasons (the second of which is theoretical):
-It allows the use of the largest diameter driver for a given internal volume
-It positions the driver on the face of the internal cube where its motion cooperates with the reflected backwave over a wider frequency range
My experience is limited to the sqare truncated enclosure. I believe this is Matthew Kennedy's (Tesserax) preferred design for two reasons (the second of which is theoretical):
-It allows the use of the largest diameter driver for a given internal volume
-It positions the driver on the face of the internal cube where its motion cooperates with the reflected backwave over a wider frequency range
Without the truncation, you would not have a large flat square to mount the driver against. All the faces are parallelgrams in shape and smaller.
Thank you a lot for the replies, it is more than I expected in a thread that had no activity in a long time, and sorry for my impatience and eagerness.
Well, I do have a relatively large rhombus where I could mount the driver against, to be precise, 12 of them. I grant you you might lose a bit of space putting the driver within them, but it is not that critical, or is it?.
I just made a 25 cm by side model in cardboard (which represents the "inner dimensions", I am attaching a picture so you can see it with the driver siting on top of it. I grant you if I were to chop off a vertex to create the square face I would be able to install an even bigger driver, but again I don't see why it is so critical.
I read carefully the explanation in which M. Kennedy explains the failure by using a lot of drivers together, so that there was not enough air-springiness, but would I be experiencing this issue if I were to use a driver that fits just inside one rhombus? As it is my 25 cm (roughly 10 inches) by side dodecaedron seems quite reasonable. By the way, it is a VISATON BG 20, quite a cheapo, and easy to get here in the old world.
VISATON BG 20 - 8 Ohm | Loudspeaker Database
I am planning on building two with one driver, and one with 4 of these, even cheaper ones:
VISATON BG 17 - 8 Ohm | Loudspeaker Database
Hide glue would work fine if you have it and are used to it. Hot melt is just easier for me as it has a trigger gun dispenser and hardens in 40 seconds. I am impatient. 🙂
sorry, it might be my "back to the time there was no WC and toilet paper" (as some musician who hated early music used to say) background... I like the way hide glue creates a musical bond, there is a reason it is still being used to this day for serious musical instrument building... although I might build the first ones without it and leave the hide glue for a "special one" made of instrument grade quarter-sawn spruce (maybe with a better driver also)...
Attachments
Hi, White Fang.
My experience is limited to the sqare truncated enclosure. I believe this is Matthew Kennedy's (Tesserax) preferred design for two reasons (the second of which is theoretical):
-It allows the use of the largest diameter driver for a given internal volume
-It positions the driver on the face of the internal cube where its motion cooperates with the reflected backwave over a wider frequency range
Thank you a lot Gmad for taking the time to reply also. As for the reason #1, since the square we are talking about would have a side of the smaller diagonal of the rhombus, the maximum theoretical diameter allowed for the design taking 25 cm for the side, would be about 29 cm.
And the largest "theoretical" diameter for a driver inscribed within the rhombus is about 23.5 cm, so the difference is there, but it is not that insurmountable, is not even 25 percent.
The reason #2 I do not fully get: you mean instead of having at the back the summit of a pyramid, it has a surface that is paralell to the one where the driver is mounted? And thus the backwave acts in a less interesting way? It cannot contribute to as many frequencies, because of this?
Sorry, I don't have a background in physics at all.
Has anyone tried the fully dodecaedron vs truncated dodecaedron to establish the differences?
And sorry for going back like 30 pages in the posts, but I wonder if this shape would not be useful for percussive instruments, or the likes of the Cuban marimbula -used for early traditional Cuban music-, stompboxes, rumba box -like those used for roots Jamaican music-, cajon -Afro-Peruvian-, and the likes.
It is difficult to use a square drumhead, but for those instruments in which the preferred form is already squared, and in which the performer sits on top, this would be a nice shape to try. Particularly since it seems the structure seems to be very strong, which is a welcomed thing when there is 200 pounds sitting on top of it...
Marimbula - Wikipedia
It is difficult to use a square drumhead, but for those instruments in which the preferred form is already squared, and in which the performer sits on top, this would be a nice shape to try. Particularly since it seems the structure seems to be very strong, which is a welcomed thing when there is 200 pounds sitting on top of it...
Marimbula - Wikipedia
Hi White Fang (Pynchon?),
I built per Matthews original truncated dodecahedron with a Visaton B200, 5mm spruce plywood (no tonewood, though) and glued with Titebond hide glue.
Excellent result!
I have the pieces for the next iteration with 9mm plywood in preparation and will be able to tell if the thinner more resonating wood is worth it.
Best of luck,
Achim
I built per Matthews original truncated dodecahedron with a Visaton B200, 5mm spruce plywood (no tonewood, though) and glued with Titebond hide glue.
Excellent result!
I have the pieces for the next iteration with 9mm plywood in preparation and will be able to tell if the thinner more resonating wood is worth it.
Best of luck,
Achim
Hi White Fang (Pynchon?),
I built per Matthews original truncated dodecahedron with a Visaton B200, 5mm spruce plywood (no tonewood, though) and glued with Titebond hide glue.
Excellent result!
I have the pieces for the next iteration with 9mm plywood in preparation and will be able to tell if the thinner more resonating wood is worth it.
Best of luck,
Achim
Hi, thanks for your input. I bought the BG 20 because it was really inexpensive, and seemed reasonable for the frequencies I was interested in.
I am happy to see there has been a lot of experimenting with this enclosures, and so far, the people who builds them seemed quite happy with the results.
I might end up truncating it also, but I just wanted to know why you "have to" do it. Also, if it is for the sake of avoiding the backface being paralell with the one in which you install the driver, another solution would be to extrude that backface into another odd shaped pointed sort of pyramid...
White Fang was written by Jack London.
Will be interesting to know how the results differ, please let us know.
Intuitively, though, I feel that what gmad has pointed out - the movement of the driver being somehow analog to and in resonance with the other pyramids when sitting at the base of the truncated one - makes a lot of sense.
It certainly sounds like it. I run it completely without stuffing. A standard closed box with standard stuffing sounded muffled and coloured in comparison.
Intuitively, though, I feel that what gmad has pointed out - the movement of the driver being somehow analog to and in resonance with the other pyramids when sitting at the base of the truncated one - makes a lot of sense.
It certainly sounds like it. I run it completely without stuffing. A standard closed box with standard stuffing sounded muffled and coloured in comparison.
Will be interesting to know how the results differ, please let us know.
Intuitively, though, I feel that what gmad has pointed out - the movement of the driver being somehow analog to and in resonance with the other pyramids when sitting at the base of the truncated one - makes a lot of sense.
It certainly sounds like it. I run it completely without stuffing. A standard closed box with standard stuffing sounded muffled and coloured in comparison.
To carry that idea even further, you could put the driver "inside out", and then the driver would look even more as the missing pyramid...
Foam core works quite well - sort of like a modern "tonewood" in that it re-radiates a bit of sound and has built in dampening abilities. I added some internal panels with soft latex caulking to reduce the reverberation. This speaker actually sounded quite impressive.
HyperFAST - a Hypercube Based 2-Way
HyperFAST - a Hypercube Based 2-Way
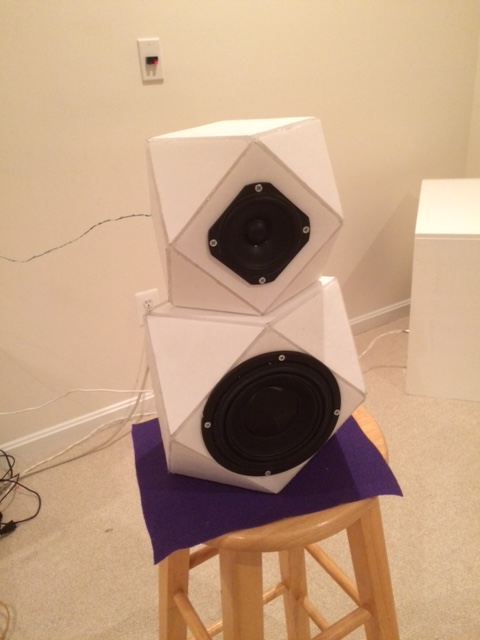
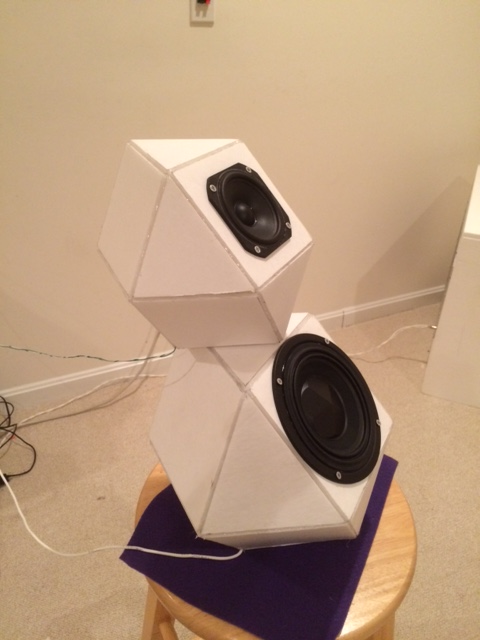
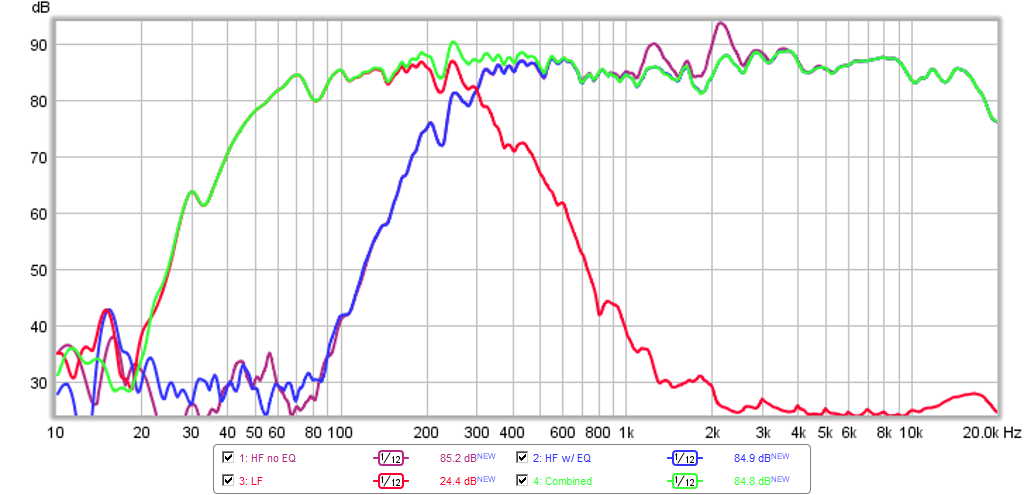
- Status
- Not open for further replies.
- Home
- Loudspeakers
- Full Range
- Hypercube Loudspeakers