Raw bamboo splits and cracks very easily with changes in humidity. This is a huge problem for antique (or new) Japanese shakuhachi flutes. People wrap them with wire to minimize but they all resort to storing them in humidity controlled bags/cases or humidor like a cigar. The bamboo I think you are talking about is the resin impregnated and baked stuff also called carburized bamboo - an engineered wood they use for floors, chopping boards, bowls, etc.
Wesayso,
Maybe you should torque the bolts on the intact tower to be tighter than before to provide the compression needed to prevent it from splitting? It is important that the rods are not bonded to the wood along their length. Are they bonded? If so this won't work.
Maybe you should torque the bolts on the intact tower to be tighter than before to provide the compression needed to prevent it from splitting? It is important that the rods are not bonded to the wood along their length. Are they bonded? If so this won't work.
Ok a little more on my findings from a few years ago with these monsters I did.
I will back up a bit first and this will take some time so follow threw 🙂
I recieved all my pieces for both the array and the subs from another person who started the large project but could not finish them.
With the first day we placed all the stacked pieces in my shop plus the large side panels and sub woofer cabinets.The next day I walked out to the shop and I had to pick my jaw off the floor.The cabinets split all over.Some so bad I took pictures to send to my customer showing the daylight threw the other side.Some split 1/4" over night.
With this I told my customer we are going to let them rest for 2 months no touching any part.Well I can say over a few months more and more cracks showed up on every piece that was assembled.With this I got a moisture gauge and checked several pieces all over and the content was 15% and that was after 4 months of climate control dry summer months.
With the splitting continuing we talked about looking off the long ready rods in each piece.At this point the large panels had already twisted out of shape
And several attempts at bondo to fill cracks more were showing up all over
As this was taken on as a back project I let it sit with the customer being on side for several months.
After getting the moisture level down a lot better sorry can not remember what % but I did remember the worst it was, we set out to finish the sub cabinets first.
We had to re clad them with 1/4" after covering the cabinets with 2 gallons of bondo to get them straight and smooth plus fill in all the cracks.Pictures for those were in my previous post and if you would like you can see the build on my Flickr for thtose large subsLarge Sub - a set on Flickr
Both the large sub cabinets and the other pieces less the baffle with the Accuton drivers, were all bolted together and the wood was under tension while the moisture changed.
I loosened all the bolts leaving the nuts off and just the bolts in place were I could to that and then attached the top pieces.Those small stacking blocks shown on the side were sealed when I received them plus every piece was filled with sand.(yes once the large curved piece was finished it was filled with sand as well then sealed top)
This photo shows the tops open but not yet sealed up.
Once the veneer was at this point I filled them with sand added the top piece and finished the veneer.
Here is showing the large baffles book matched veneer
If you notice the wing that once was positioned for a tweeter cut had to be cut off all due to cabinet twisting and splitting.Was a good move in the overall design.
This last photo shows the one speaker complete less finish and the lower sub cabinet with 4 tc 12" woofer that this all sat on.
Best advice for you to correct and or limit the splitting you have going on.
Get the tension on those bolts off.With this be prepared they are going to split all over.Sorry but they will!!! With this let them sit in your house, place your baffle listen to them for a few months.Believe me the tension on the wood needs to release number 1 and number 2 the moisture in the wood needs to acclimate plus become even.Time to correct this now over all going to be 4 months plus all depending on your climate and moisture in your house.But with this large amount of layered and compressed wood it will take time.
Sand your cabinet outsides down to bare wood.
After a few months apply a good wood filler and or clear epoxy with wood shavings to match your finish you are going toward.Let them set for another month ya I know not want you want, but having been in your steps I can say time will only be your friend.
After a month or so check for cracking. If you are good no more cracking , at this point seal the cabinets up with a sealer 3-4 coats on the inside and the same outside.1-2 coats on wood is not enough on raw unsanded material like the inside of your cabinet.
After all the sealing is done several coats. Let them sit again for another few weeks.Again all threw this enjoy them listen to them.This also makes the process more enjoyable you can listen to them.
If no evidence of cracking or splitting after a few weeks the do your finishing at this time.
After that try and keep them in the same environment.
Not a simple and quick fix for this.Cal can confirm along with Dave that these monsters were in my garage for a few years start to finish.
Here is a smaller project again same customer for Accuton driver and a G1 sitting on the top. Aluminum baffles were cut after this photo.These were more test cabinets for him.
http://www.flickr.com/photos/28279019@N05/sets/72157625054168290/
Take your time like I said it will work out but you need the time for the wood to acclimate.
Feel free to PM if you would like
Al
I will back up a bit first and this will take some time so follow threw 🙂
I recieved all my pieces for both the array and the subs from another person who started the large project but could not finish them.
With the first day we placed all the stacked pieces in my shop plus the large side panels and sub woofer cabinets.The next day I walked out to the shop and I had to pick my jaw off the floor.The cabinets split all over.Some so bad I took pictures to send to my customer showing the daylight threw the other side.Some split 1/4" over night.
With this I told my customer we are going to let them rest for 2 months no touching any part.Well I can say over a few months more and more cracks showed up on every piece that was assembled.With this I got a moisture gauge and checked several pieces all over and the content was 15% and that was after 4 months of climate control dry summer months.
With the splitting continuing we talked about looking off the long ready rods in each piece.At this point the large panels had already twisted out of shape

And several attempts at bondo to fill cracks more were showing up all over

As this was taken on as a back project I let it sit with the customer being on side for several months.
After getting the moisture level down a lot better sorry can not remember what % but I did remember the worst it was, we set out to finish the sub cabinets first.
We had to re clad them with 1/4" after covering the cabinets with 2 gallons of bondo to get them straight and smooth plus fill in all the cracks.Pictures for those were in my previous post and if you would like you can see the build on my Flickr for thtose large subsLarge Sub - a set on Flickr
Both the large sub cabinets and the other pieces less the baffle with the Accuton drivers, were all bolted together and the wood was under tension while the moisture changed.
I loosened all the bolts leaving the nuts off and just the bolts in place were I could to that and then attached the top pieces.Those small stacking blocks shown on the side were sealed when I received them plus every piece was filled with sand.(yes once the large curved piece was finished it was filled with sand as well then sealed top)
This photo shows the tops open but not yet sealed up.

Once the veneer was at this point I filled them with sand added the top piece and finished the veneer.
Here is showing the large baffles book matched veneer
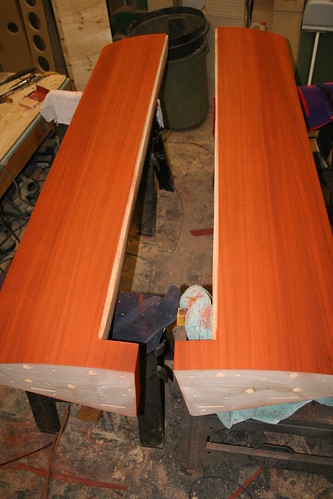
If you notice the wing that once was positioned for a tweeter cut had to be cut off all due to cabinet twisting and splitting.Was a good move in the overall design.
This last photo shows the one speaker complete less finish and the lower sub cabinet with 4 tc 12" woofer that this all sat on.

Best advice for you to correct and or limit the splitting you have going on.
Get the tension on those bolts off.With this be prepared they are going to split all over.Sorry but they will!!! With this let them sit in your house, place your baffle listen to them for a few months.Believe me the tension on the wood needs to release number 1 and number 2 the moisture in the wood needs to acclimate plus become even.Time to correct this now over all going to be 4 months plus all depending on your climate and moisture in your house.But with this large amount of layered and compressed wood it will take time.
Sand your cabinet outsides down to bare wood.
After a few months apply a good wood filler and or clear epoxy with wood shavings to match your finish you are going toward.Let them set for another month ya I know not want you want, but having been in your steps I can say time will only be your friend.
After a month or so check for cracking. If you are good no more cracking , at this point seal the cabinets up with a sealer 3-4 coats on the inside and the same outside.1-2 coats on wood is not enough on raw unsanded material like the inside of your cabinet.
After all the sealing is done several coats. Let them sit again for another few weeks.Again all threw this enjoy them listen to them.This also makes the process more enjoyable you can listen to them.
If no evidence of cracking or splitting after a few weeks the do your finishing at this time.
After that try and keep them in the same environment.
Not a simple and quick fix for this.Cal can confirm along with Dave that these monsters were in my garage for a few years start to finish.
Here is a smaller project again same customer for Accuton driver and a G1 sitting on the top. Aluminum baffles were cut after this photo.These were more test cabinets for him.

http://www.flickr.com/photos/28279019@N05/sets/72157625054168290/
Take your time like I said it will work out but you need the time for the wood to acclimate.
Feel free to PM if you would like
Al
carbonized is a colouring process.
dave
A colorizing process that bakes it under steam pressure after being boiled in boric acid. Not exactly coloring like simple dye.
Raw bamboo splits and cracks very easily with changes in humidity. ... The bamboo I think you are talking about is the resin impregnated and baked stuff
All unfinished wood shrinks and swells. This is one of the reason we oil or wax furniture (both top and bottom. Paint, varnish or even better epoxy (like the West system) provides a seal which minimises the rate of moisture level change.
All unfinished wood shrinks and swells. This is one of the reason we oil or wax furniture (both top and bottom. Paint, varnish or even better epoxy (like the West system) provides a seal which minimises the rate of moisture level change.
I agree that is what I ended up using.
Regarding using Epoxy and or various fibres. Unfortunatly, I would have to say its best to take of the clear coat finish first if you want to epoxy impregnate it, as it will bond to and reinforce the wood better. Soaking the inside of the cabinet will also do a lot. But since you finish is so nice it would be a real same to take it off. If it was me…, I’d leave the current finish on, I think.
As for using additional fibre laminate. If you want the same “clear finish”, even glass mat will possibly show and it’s hard getting an even lay-up without bubbles etc.., unless you start using a vacuum bag, (google it) and even then it’s diffecult. As with Kevlar and Carbon, you’ll lose the clear finish obviously, vacuum baging would be recommended as well.
As for pre heating the wood prior to applying the epoxy. You could rent some infrared heaters at Bo-rent or maybe the Gamma. Getting the wood up to 20-25C would make a big difference in the viscosity of the epoxy. I would highly recommend doing this. Gradually pre heat the speakers overnight, so they are nice and warm and cure with the heating as well. Also the epoxy will work best if it’s 20-25C when applying and make sure to take the slow curing type.
If you decide to take the current finish off, if you use a water based stain this would work very well with epoxy.
As for using additional fibre laminate. If you want the same “clear finish”, even glass mat will possibly show and it’s hard getting an even lay-up without bubbles etc.., unless you start using a vacuum bag, (google it) and even then it’s diffecult. As with Kevlar and Carbon, you’ll lose the clear finish obviously, vacuum baging would be recommended as well.
As for pre heating the wood prior to applying the epoxy. You could rent some infrared heaters at Bo-rent or maybe the Gamma. Getting the wood up to 20-25C would make a big difference in the viscosity of the epoxy. I would highly recommend doing this. Gradually pre heat the speakers overnight, so they are nice and warm and cure with the heating as well. Also the epoxy will work best if it’s 20-25C when applying and make sure to take the slow curing type.
If you decide to take the current finish off, if you use a water based stain this would work very well with epoxy.
Thanks all for the experiences and ideas.
It makes it easier for me to make the decision on what to do. Right now, as said both columns are in one piece. Right now I have the tension of the rods on and I'll keep it that way as long as they are in one piece. If they don't split again and if the steel rods don't break I'll sand back the finish when the warm days return and use epoxy to recoat them. Either in an all black finish or using water based stain.
If they do split I'll release the tension on the rods and in the spring grind trough the rods from the outside in several places to minimize the tension of the rods even further. I'll recover the enclosures using again epoxy as a main ingredient. Due to the sheer size of the enclosures I don't think I'd ever want to go without any long stabilizing factor when using wood. Free running rods, but that also had disadvantages etc...
Maybe thinking out loud for a next attempt, be it mine or someone else: bigger threaded rods, like 4x M10 with a damping area below and above the wood column for this kind of stack? Free from the enclosure so the wood can do its thing.
I like what Magico did with their Mini. They held the baffle on with trough bolts from back to front to apply some pressure on the enclosure. But than again, they went all aluminum after that.
I'll be crossing my fingers and adjusting/correcting the pre torque with a torque wrench for now and hope to have some audio playing to enjoy in the mean time 😀.
It makes it easier for me to make the decision on what to do. Right now, as said both columns are in one piece. Right now I have the tension of the rods on and I'll keep it that way as long as they are in one piece. If they don't split again and if the steel rods don't break I'll sand back the finish when the warm days return and use epoxy to recoat them. Either in an all black finish or using water based stain.
If they do split I'll release the tension on the rods and in the spring grind trough the rods from the outside in several places to minimize the tension of the rods even further. I'll recover the enclosures using again epoxy as a main ingredient. Due to the sheer size of the enclosures I don't think I'd ever want to go without any long stabilizing factor when using wood. Free running rods, but that also had disadvantages etc...
Maybe thinking out loud for a next attempt, be it mine or someone else: bigger threaded rods, like 4x M10 with a damping area below and above the wood column for this kind of stack? Free from the enclosure so the wood can do its thing.
I like what Magico did with their Mini. They held the baffle on with trough bolts from back to front to apply some pressure on the enclosure. But than again, they went all aluminum after that.
I'll be crossing my fingers and adjusting/correcting the pre torque with a torque wrench for now and hope to have some audio playing to enjoy in the mean time 😀.
oh, now to think....my build is also multi layer birch ply....crap, now you got me worried that it can crack....
Oh well, have to think about some addition to the build to "keep it together" 🙂
Danny
I wouldn't be surprised if your ply layers will show after the finish but wouldn't worry about cracking in your case. That being said, in hindsight, I'd opt for epoxy below the bondo to get the smoothest possible finish.
Maybe the surfboard way to construct something like that isn't a bad option. As well as the big towers I have. I have thought about that before going with wood. I wouldn't dare use mdf as a base material in constructions like this. And I am not yet sold on Bamboo ply.
My stack is 130 separate pieces of ply glued together, let's not forget about that!
You have a good spirit.
Thanks Cal,
If we don't have that, what's the use? So I learned something. That's never bad is it? I had asked before I started using the rods or not. Never got much replies if any (don't remember if it was on this site or DIYMA). I had my doubts and still went for it... No one to blame but me. Learn from it and move on 😀.
If in the end I have great playing speakers it will all have been worth it and I would gladly do it again. Just in a slightly different way. Or maybe even a totally different way.
I'm a mechanical engineer, know way more about metals than wood. But I do enjoy learning the do's and don'ts. Even if at first it gives you a big scare.
If I had more space available (eh make that: allowed to use by girlfriend) I'd been all over the synergy horns. Love the big outdoors setup you showed. I had a neighbor that had Altec Barcelona's in his house. Lovely mids!
I let my carpenter friend look at this threads pictures, first thing he said upon seeing the 'split' picture was "The rods still inside it."
And:
"The wood has dried and contracted while the rod has expanded."
He said lots of nice things as well.
I wouldn't put bondo over epoxy, the former will react with the latter and your bondo will fall off at some point.
You would have to finish the wood then prime it with 'watered down' Polyester resin that has a slight wax content (wax is a levelling agent and also makes in effect a 'thermal blanket' to cook / cure the resin).
Then you would have to sand it almost back to bare wood.
Then you would use a 'Hot Mix' - this is resin with say 3% wax and 5% cat, it does exactly as its name suggests, it gets HOT, the cured resin is very hard and very hard to sand even.
Then you Gloss - Taupo Gloss resin is best for this, though you can make gloss resin from lam resin (5% wax, 3 1/2% cat and 'stale' resin).
This is the layer that gives you the 'solid water' gloss and is an utter cow bag to sand and polish because the resin is so hard, heat build up is massive and can leave yellow > brown scorch marks IN the finish.
Finishing like this is a very fast process as you have to work fast before the resin fully cures out - if the previous layer is too hard and lost its 'tack', even though it has a 'key', there is a chance that the next layer will lift or 'soft' as you sand.
Finishing can be by hand or machine, the way things go wrong are the same in either instance.
Epoxy is amazing stuff, but even harder to work with than Poly, with the added bonus that one can become sensitised not just by the liquid getting on your skin, but also by the dust when sanding leaching into sweaty pores.
And:
"The wood has dried and contracted while the rod has expanded."
He said lots of nice things as well.
I wouldn't put bondo over epoxy, the former will react with the latter and your bondo will fall off at some point.
You would have to finish the wood then prime it with 'watered down' Polyester resin that has a slight wax content (wax is a levelling agent and also makes in effect a 'thermal blanket' to cook / cure the resin).
Then you would have to sand it almost back to bare wood.
Then you would use a 'Hot Mix' - this is resin with say 3% wax and 5% cat, it does exactly as its name suggests, it gets HOT, the cured resin is very hard and very hard to sand even.
Then you Gloss - Taupo Gloss resin is best for this, though you can make gloss resin from lam resin (5% wax, 3 1/2% cat and 'stale' resin).
This is the layer that gives you the 'solid water' gloss and is an utter cow bag to sand and polish because the resin is so hard, heat build up is massive and can leave yellow > brown scorch marks IN the finish.
Finishing like this is a very fast process as you have to work fast before the resin fully cures out - if the previous layer is too hard and lost its 'tack', even though it has a 'key', there is a chance that the next layer will lift or 'soft' as you sand.
Finishing can be by hand or machine, the way things go wrong are the same in either instance.
Epoxy is amazing stuff, but even harder to work with than Poly, with the added bonus that one can become sensitised not just by the liquid getting on your skin, but also by the dust when sanding leaching into sweaty pores.
My projects made me look at how lamenated beams are made.. No bolts
Laminated in the length direction? Not exactly similar as this. You need the strength and stiffness for a high tower. That has got to come from somewhere.
A composite material is starting to make sense to me (again) for such a long enclosure. It was one of the things I discussed with a good friend (the one making me the Alu baffles). But I wanted a bit more weight and the rest is in this thread (lol).
Last edited:
Oh.......
Epoxy or Poly resin can blotch on the wood, bloom like cellulose and change colour depending on the season.
If your wood expands like in the picture with a resin finish, the repair will always be seen and the slightest 'ding' will result in a 'shattered glass' effect.
Epoxy or Poly resin can blotch on the wood, bloom like cellulose and change colour depending on the season.
If your wood expands like in the picture with a resin finish, the repair will always be seen and the slightest 'ding' will result in a 'shattered glass' effect.
So what would be the right thing to do to make the same shape and weight? And enough strength etc. I'd love to find the recipe for a slim tower like this standing 2m 22cm (base not included) but like to keep the round shape etc.
Make a 'plug', find veneer / thin ply (plywood is made down to 1/64th inch) and laminate the curved portion.
You could then add the internal bits and front sub baffle.
Speaking of which, Your baffle's a long strip of ally right...... That's going to expand and contract a lot.
I'd make them in 1m 22cm sections and bolt them together, do the joint right and you'll barely notice it 🙂
You could then add the internal bits and front sub baffle.
Speaking of which, Your baffle's a long strip of ally right...... That's going to expand and contract a lot.
I'd make them in 1m 22cm sections and bolt them together, do the joint right and you'll barely notice it 🙂
A colorizing process that bakes it under steam pressure after being boiled in boric acid. Not exactly coloring like simple dye.
Specifications do not differ from not-carbonized.
dave
Speaking of which, Your baffle's a long strip of ally right...... That's going to expand and contract a lot.
I'd make them in 1m 22cm sections and bolt them together, do the joint right and you'll barely notice it 🙂
Do you expect that much movement from the aluminum?
Coefficients of Linear Thermal Expansion
Wouldn't that translate to 0.022 mm per degree celsius per meter? Even epoxy moves more than double that. The steel rods do only half of that... In one of the previous replies to this thread someone mentioned the steel rods expanding too fast for the wood. I don't think that would be a great concern. Certainly not the cause of my 2 mm gap. It just doesn't get that cold/hot that fast in my living room.
I don't think I expect the temperature swings in my living room to cause a concern for the aluminum to expand/contract too much. The wood is another story. Not due to temperature but humidity changes. Both materials will expand/contract at different rates but temperature swings are not the main problem to focus on for the aluminum or the rods i.m.h.o.
edit: Polyester, glass fiber reinforced seems to match the aluminum well though, good to know for future plans.
Last edited:
- Home
- Loudspeakers
- Full Range
- The making of: The Two Towers (a 25 driver Full Range line array)