So the V-groove bearings will be touching hard surfaces and not on the carbon fiber parts.
Exactly as designed: and steel weights less than tungsten. Titanium or ruby rods even better, but I can't find them in my scrap bin.
But to mill and glue with tight tolerances remains the real problem
difficult to imagine the best way to share the weight on the wheels (me)
I try to use the least number of parts if possible. Dd
my reasoning was this: the upper bearing rotates, while the lower one prevents just swinging, so it is sufficient that it's loaded at minimum. Carriage A is wrong, B is excessive: are we sure that a normal carriage C (with a third wheel) has more friction?
Since the design requires a swiveling base, why use vertical pivot at all? I'm thinking of a hanging structure with springs for vertical movement. Hmm....
Step after step are we together slowly reinventing the Lil Casey? Hmm....
carlo
Exactly as designed: and steel weights less than tungsten. Titanium or ruby rods even better, but I can't find them in my scrap bin.
But to mill and glue with tight tolerances remains the real problem
difficult to imagine the best way to share the weight on the wheels (me)
I try to use the least number of parts if possible. Dd
my reasoning was this: the upper bearing rotates, while the lower one prevents just swinging, so it is sufficient that it's loaded at minimum. Carriage A is wrong, B is excessive: are we sure that a normal carriage C (with a third wheel) has more friction?
Since the design requires a swiveling base, why use vertical pivot at all? I'm thinking of a hanging structure with springs for vertical movement. Hmm....
Step after step are we together slowly reinventing the Lil Casey? Hmm....
carlo
Last edited:
Really impressive. But this could be even better...in the right hands, of course.
carlo
https://www.historicgames.com/lathes/bowlathes.html
YouTube
YouTube
Lorch Watchmaker's Lathes
carlo
https://www.historicgames.com/lathes/bowlathes.html
YouTube
YouTube
Lorch Watchmaker's Lathes
Attachments
They do say better late than never, and I have been thinking about a linear tonearm for a while but my RP8 was not a good rig. Now I have the SP10 up and running and I have been listening for a couple of months I thought I'd jump in and make a linear arm.
Not finished but close. I broke my only M2.5 tap and there are none available in the town I live so waiting for one to arrive. I ordered a couple of ABEC9 bearings waiting for them too.
The aluminium tube will be the cue mechanism.
Not finished but close. I broke my only M2.5 tap and there are none available in the town I live so waiting for one to arrive. I ordered a couple of ABEC9 bearings waiting for them too.
The aluminium tube will be the cue mechanism.
Attachments
What a fascinating and educational thread! Must rate as one of the best I've read on any forum, about any subject, ever! 
I've spent the last three days reading in between testing at work (EMC) and have reached page 271, and it has inspired me to build one of these beasts, starting over the Christmas break.
I'm no stranger to building, having built probably half a dozen tables, and at least twice as many arms, including a couple of Dynavector DV505 inspired devices. I've often considered a linear tracker but got sidetracked, but this thread has been the kick in the pants to get going.
It's been fantastic to see the many different approaches and some really clever and imaginitive new ways to 'skin the cat'
Keep up the good work!
I've spent the last three days reading in between testing at work (EMC) and have reached page 271, and it has inspired me to build one of these beasts, starting over the Christmas break.
I'm no stranger to building, having built probably half a dozen tables, and at least twice as many arms, including a couple of Dynavector DV505 inspired devices. I've often considered a linear tracker but got sidetracked, but this thread has been the kick in the pants to get going.
It's been fantastic to see the many different approaches and some really clever and imaginitive new ways to 'skin the cat'
Keep up the good work!
I was going to build a Ladegaard style arm until I stumbled across this thread. What I liked is the simplicity and no pump.
There are some very innovative ideas. I like Niffy's pin bearings and plan implementing these in my next iteration using 1mm ZR02 balls in a stainless cup as the pivot.
There are some very innovative ideas. I like Niffy's pin bearings and plan implementing these in my next iteration using 1mm ZR02 balls in a stainless cup as the pivot.
Hi, niffy, super 10018, Straight tracker, and company
Thanks for posting the Steve Guttenberg Youtube videos. I just wanted to add my efforts to this fantastic thread. Happy to be one of the linear tracking "nuts". I couldn't just let you guys have all the fun !!! Merry Christmas, Happy Holidays etc. to all
Joe
Thanks for posting the Steve Guttenberg Youtube videos. I just wanted to add my efforts to this fantastic thread. Happy to be one of the linear tracking "nuts". I couldn't just let you guys have all the fun !!! Merry Christmas, Happy Holidays etc. to all
Joe
Hi, audiostar
Yes, I an the "Joe" in the videos.
I currently have an Oracle delphi Mk2, so I do have a turntable. Unfortunately, life gets in the way every now and then and I have to spend my time on other priorities. I will get things done. Lots of smaller machining tasks to perform. Thanks for your interest.
Joe
Yes, I an the "Joe" in the videos.
I currently have an Oracle delphi Mk2, so I do have a turntable. Unfortunately, life gets in the way every now and then and I have to spend my time on other priorities. I will get things done. Lots of smaller machining tasks to perform. Thanks for your interest.
Joe
First of all merry Christmas to you all, and happy new ideas to us all.
Congratulations EAlex for your double rail realization (and for the monster TT!) and thxs for your (too) kind words. Keep us informed of your results, details and impressions. I am still looking for a non-tilting, lightweight solution with just one, but the road is steep.
carlo
Xmas recipe: I recently discovered a simple system to improve the already excellent carbon fiber shafts: an inner coating with very diluted vinyl glue (white glue). Pour it inside in several layers until it reaches the desired sound (compare it with the one without). This glue remains a little viscous, and this creates a very effective compound with the carbon fiber. As usual, add your kind of damping for the stationary waves inside the tube.
Congratulations EAlex for your double rail realization (and for the monster TT!) and thxs for your (too) kind words. Keep us informed of your results, details and impressions. I am still looking for a non-tilting, lightweight solution with just one, but the road is steep.
carlo
Xmas recipe: I recently discovered a simple system to improve the already excellent carbon fiber shafts: an inner coating with very diluted vinyl glue (white glue). Pour it inside in several layers until it reaches the desired sound (compare it with the one without). This glue remains a little viscous, and this creates a very effective compound with the carbon fiber. As usual, add your kind of damping for the stationary waves inside the tube.
Last edited:
EAlex,
Do you know Serge Karmadon? Old Turntables Repair & Restoration – * New Life for Vintage Audio *
Many like his tonearms. How good is his bandage turntable on youtube? I like your latest project.
Do you know Serge Karmadon? Old Turntables Repair & Restoration – * New Life for Vintage Audio *
Many like his tonearms. How good is his bandage turntable on youtube? I like your latest project.
carlo
Xmas recipe: I recently discovered a simple system to improve the already excellent carbon fiber shafts: an inner coating with very diluted vinyl glue (white glue). Pour it inside in several layers until it reaches the desired sound (compare it with the one without). This glue remains a little viscous, and this creates a very effective compound with the carbon fiber. As usual, add your kind of damping for the stationary waves inside the tube.
That's interesting, have you tried laminating 2x 0.5mm rods this way.
I used 6x1mm carbon rod and glued balsa wood inside. I might give this a go.
Attachments
When I experimented with a lightweight carriage using carbon fibre tubes I also used balsa rods acting as damping cores. My use of a carbon fibre tube was quite different as it was used for the actual arm tube rather than the rail. The addition of the balsa really helped to smooth out the sound whilst adding virtually nothing to the overall mass.
The yoke is also made of thin carbon fibre skins with an end grain balsa core.
Niffy
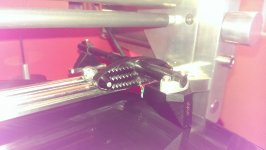
The yoke is also made of thin carbon fibre skins with an end grain balsa core.
Niffy
Sorry for misunderstandings: the recipe is just for the carbon tubes (poltruded, ex arrows, golf clubs or fishing rods) normally used for shafts, not for the Lil Casey rail, damped with a self-adhesive velvet strip at the top, otherwise the carriage does not slide.
The white glue seems a simple method to build a well damped compound with very different materials. A few tenths of mm layer is more than enough
As usual it remains to block the air resonances inside the tube. I use the two ends of a cotton swab which can be moved in two different points of the tube even after installing the cables.
carlo
maybe this method may be applied even to aluminum (till now for these i've used ovening at 200 C)
The white glue seems a simple method to build a well damped compound with very different materials. A few tenths of mm layer is more than enough
As usual it remains to block the air resonances inside the tube. I use the two ends of a cotton swab which can be moved in two different points of the tube even after installing the cables.
carlo
maybe this method may be applied even to aluminum (till now for these i've used ovening at 200 C)
Hi Warrjon,
The armtube is made from two tubes one inside the other. The outer has an od of 8mm, a 1mm wall, runs from the headshell to just behind the yoke and is about half the total length of the arm. The inner layer is 6mm in diameter, has a 0.5mm wall and runs the entire length of the arm and supports the counterweight. Therefore the front section of the arm has a 1.5mm wall thickness. There is also a 3mm diameter rod that acts as a cable guide and as something for the queuing lever to operate against. Here's another picture.
This design is different to that developed by Colin, the op, as the armtube is above the rail. I did this in order to bring the vertical pivot as close to the record as possible. This will help to reduce warp wow.
Another major difference is that I have the yoke in front of the rail rather than behind it. This was done for several reasons. Configuring the arm in this way made the arm much more rigid. This pushes the resonant frequency higher resulting in lower harmonic distortion. It also gave a much better mass distribution that again helped to increase the resonant frequency whilst allowing me to get the vertical effective mass spot on. With the yoke in this position the cable guide acts like a pin that solidly attaches the yoke to the armtube. I also think it looks better.
Although this arm worked and sounded fine it was no match for the heavier "batmobile" carriage that out performs it in every way.
Niffy
The armtube is made from two tubes one inside the other. The outer has an od of 8mm, a 1mm wall, runs from the headshell to just behind the yoke and is about half the total length of the arm. The inner layer is 6mm in diameter, has a 0.5mm wall and runs the entire length of the arm and supports the counterweight. Therefore the front section of the arm has a 1.5mm wall thickness. There is also a 3mm diameter rod that acts as a cable guide and as something for the queuing lever to operate against. Here's another picture.
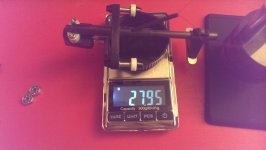
This design is different to that developed by Colin, the op, as the armtube is above the rail. I did this in order to bring the vertical pivot as close to the record as possible. This will help to reduce warp wow.
Another major difference is that I have the yoke in front of the rail rather than behind it. This was done for several reasons. Configuring the arm in this way made the arm much more rigid. This pushes the resonant frequency higher resulting in lower harmonic distortion. It also gave a much better mass distribution that again helped to increase the resonant frequency whilst allowing me to get the vertical effective mass spot on. With the yoke in this position the cable guide acts like a pin that solidly attaches the yoke to the armtube. I also think it looks better.
Although this arm worked and sounded fine it was no match for the heavier "batmobile" carriage that out performs it in every way.
Niffy
Thanks Niffy,
This arm is the first I've built and very close to what Colin built with the 2 rail 2 bearing arm. I bought a couple of Abu Garcia ABEC 9 dry lube bearings (haven't arrived yet).
I am using a Stanton 881s which is very high compliance and I think I may need to get the carriage weight lower, currently 49g with CW and cartridge. This is why I was interested in what you did. I have read almost all of this thread so I was interested in what you did with the carriage you just posted.
I am planning to build another rail system inspired by the Clearaudio TT1. This arm will have the rail very close to the platter and slide back to clear for record changes. Next years project.
As soon as the family go after Xmas I'll install this arm, can't wait to hear it.
Cheers Warren
This arm is the first I've built and very close to what Colin built with the 2 rail 2 bearing arm. I bought a couple of Abu Garcia ABEC 9 dry lube bearings (haven't arrived yet).
I am using a Stanton 881s which is very high compliance and I think I may need to get the carriage weight lower, currently 49g with CW and cartridge. This is why I was interested in what you did. I have read almost all of this thread so I was interested in what you did with the carriage you just posted.
I am planning to build another rail system inspired by the Clearaudio TT1. This arm will have the rail very close to the platter and slide back to clear for record changes. Next years project.
As soon as the family go after Xmas I'll install this arm, can't wait to hear it.
Cheers Warren
- Home
- Source & Line
- Analogue Source
- DIY linear tonearm