Oh that's not the half of it. There were half a dozen 5 ft lengths as well which I intend at some stage to make a new equipment rack from. The very nice 6' by 4' mirror I was not allowed to have by the boss as no where to put it.
@Ralf : You may be right, they seem to start at $300.
@Ralf : You may be right, they seem to start at $300.
Here's an upcoming player with a servo-controlled tangential arm (scroll down to the middle of the article):
Mono and Stereo High-End Audio Magazine: New Ballfinger M-063 reel-to-reel tape player exclusive report!
Mono and Stereo High-End Audio Magazine: New Ballfinger M-063 reel-to-reel tape player exclusive report!
The ballfinger arm is actually a linear tracking arm. I don’t know how they deal with eccentric records. It seems to me that there is no active tracking mechanism. If they just let the arm to swing left and right to deal with eccentric records, I think there will be a lot of tracking errors. It is really bad implement.
To me, a perfect active linear tracking arm should use active tracking system as laser record player, but the playing mechanism should be a cartridge.
To me, a perfect active linear tracking arm should use active tracking system as laser record player, but the playing mechanism should be a cartridge.
Last edited:
Ballfinger PS2 Turntable
The Ballfinger uses an active servo tonearm. Looks like a fancy modern Rabco.
The Ballfinger uses an active servo tonearm. Looks like a fancy modern Rabco.
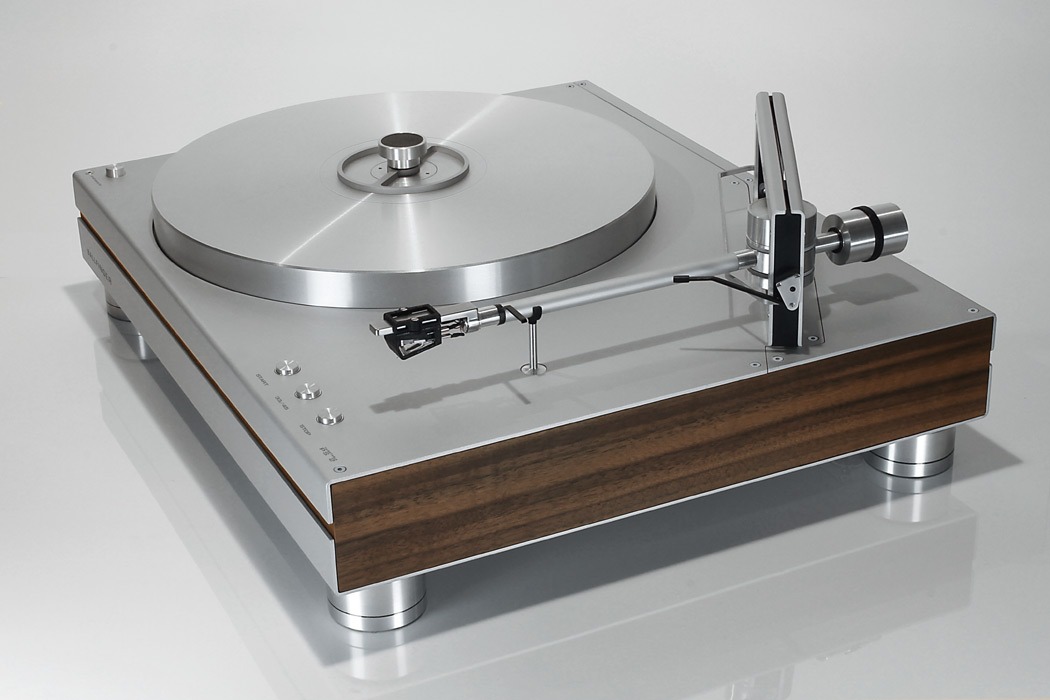
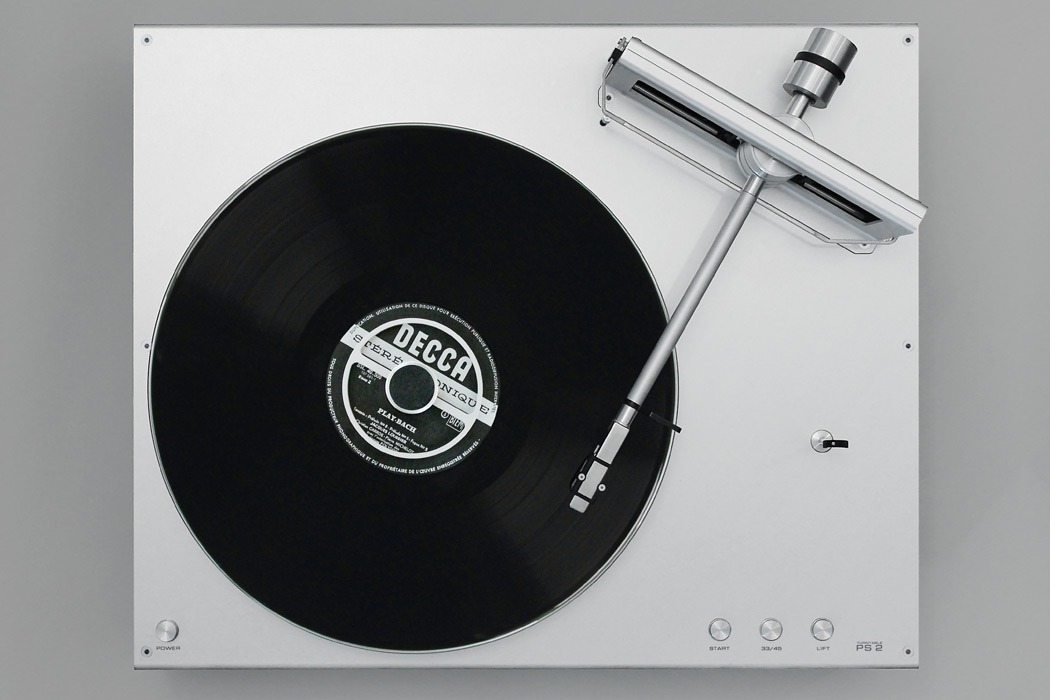
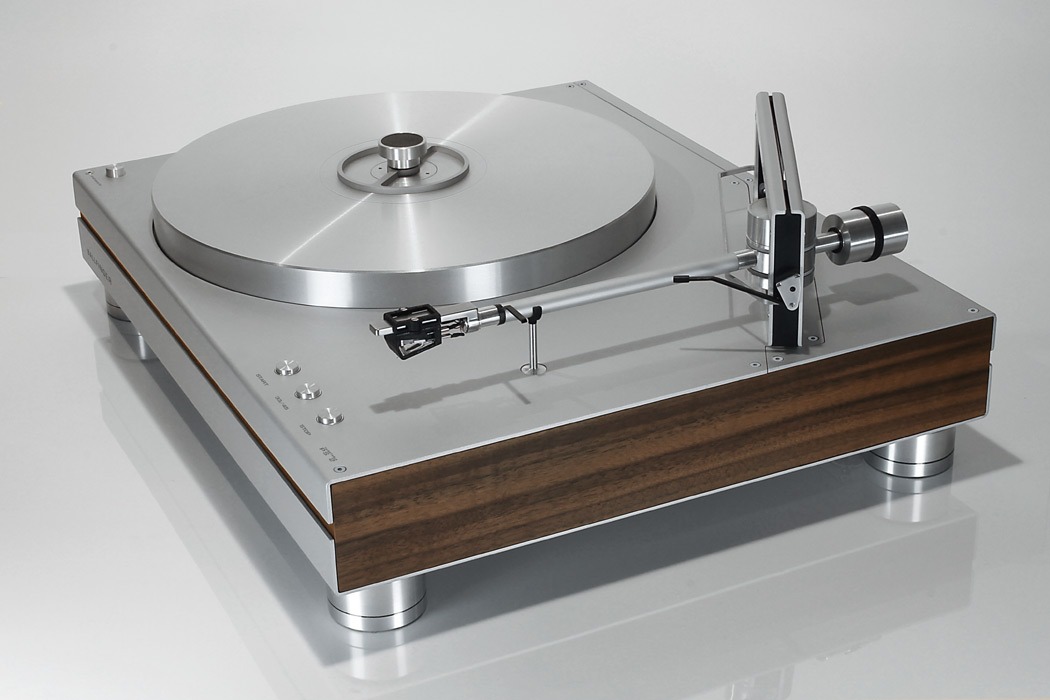
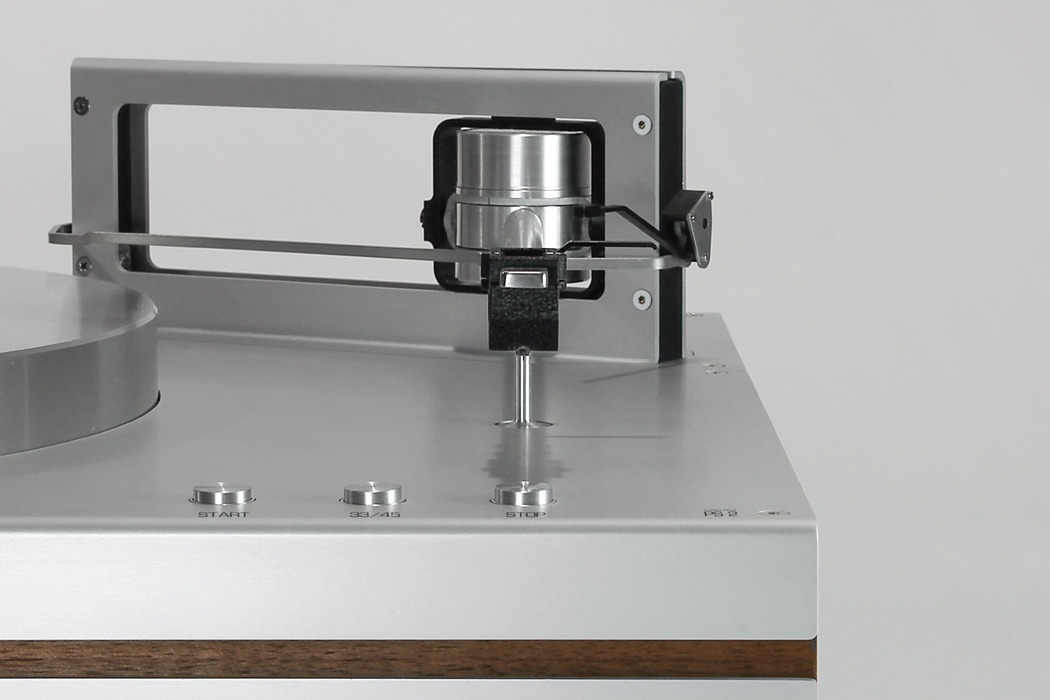
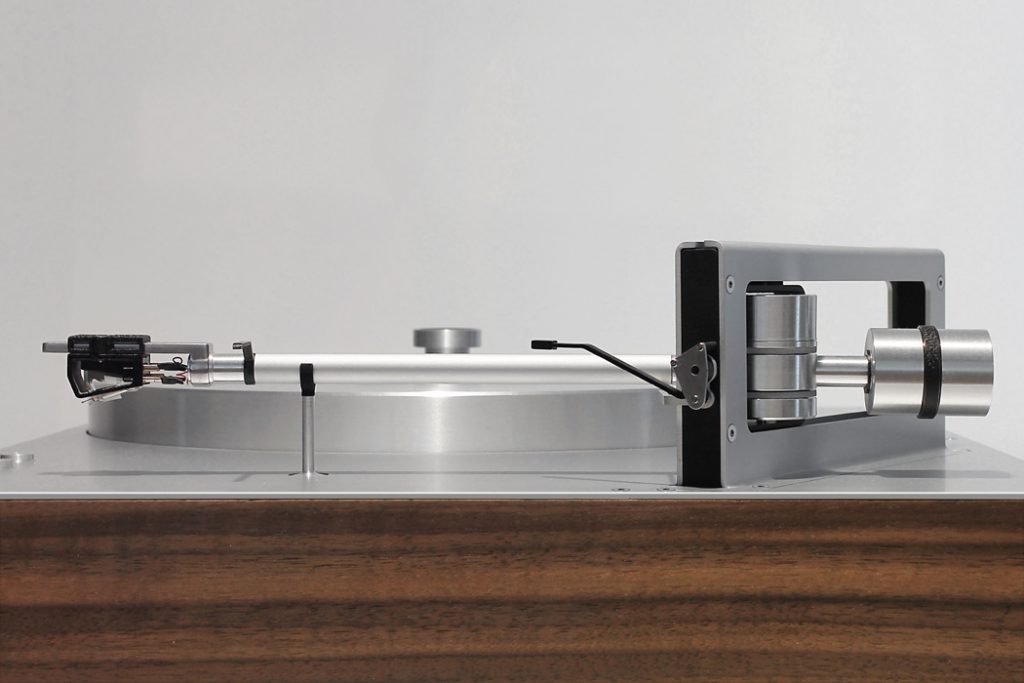
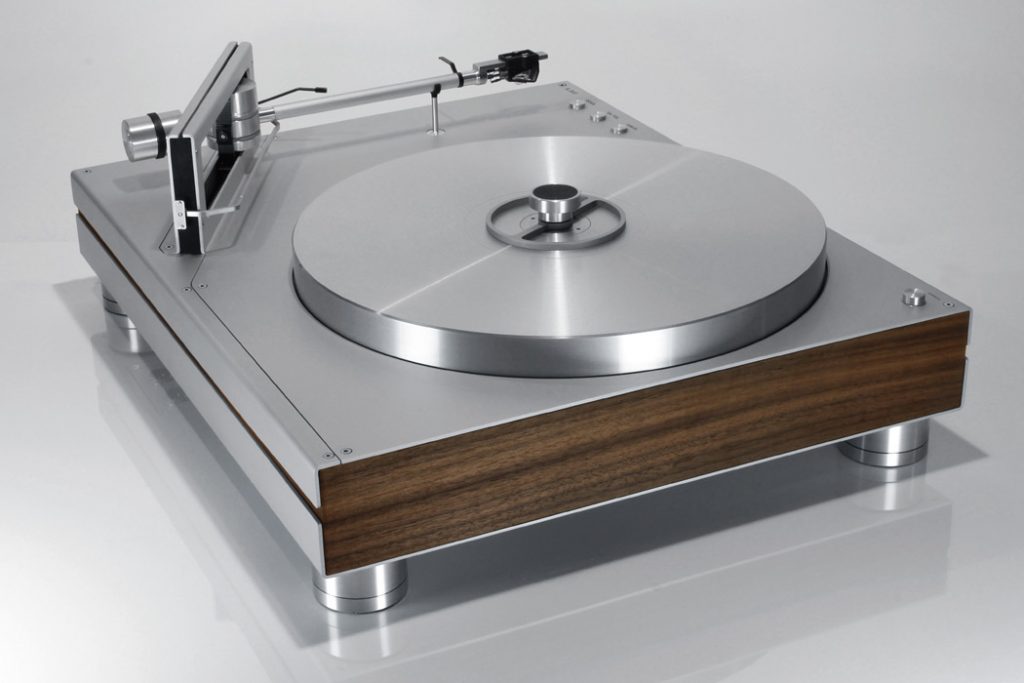
Well....I'm not recommending this, I wouldnt put it on my stuff on
the worst day......but it is linear tracking....
https://www.kickstarter.com/projects/493608538/love-the-worlds-first-intelligent-turntable
the worst day......but it is linear tracking....
https://www.kickstarter.com/projects/493608538/love-the-worlds-first-intelligent-turntable
but it is linear tracking....
https://www.kickstarter.com/projects/493608538/love-the-worlds-first-intelligent-turntable
The "turntable" is now a turn-tonearm! Not sure that's a good idea... looks like another item for hipsters.
The short arm of parallel tracking reminds me of the Revox arm and Rational Audio arm in the pictures below:
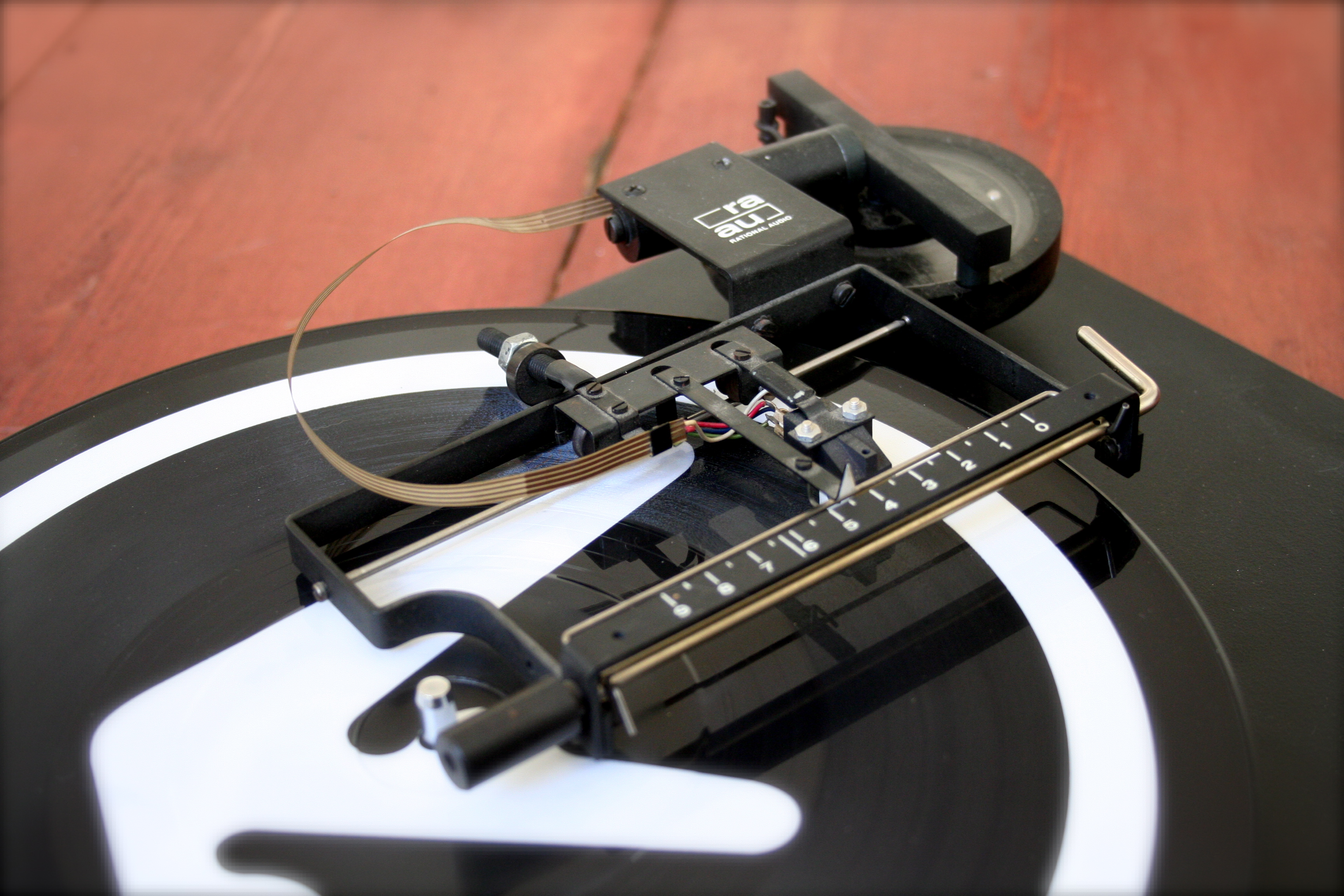
Ballfinger bad imlement?
A really bad implement in what way? Why does the servo mechanism have to follow eccentricity with laser precision? Let's say the servo mechanism is slow and eccentricity swings the arm left and right. The Ballfinger spec says that the effective length of the arm is 223mm, about par for a 9 inch conventional offset arm. If the record were eccentric by 1mm, then the angular error introduced would be 0.26 degrees. How is that worse than a conventional offset arm? The stiction in a purely mechanical tangential tracker would very likely cause as much, or more, tracking error by deflecting the stylus.
Ray K
The ballfinger arm is actually a linear tracking arm. I don’t know how they deal with eccentric records. It seems to me that there is no active tracking mechanism. If they just let the arm to swing left and right to deal with eccentric records, I think there will be a lot of tracking errors. It is really bad implement.
To me, a perfect active linear tracking arm should use active tracking system as laser record player, but the playing mechanism should be a cartridge.
A really bad implement in what way? Why does the servo mechanism have to follow eccentricity with laser precision? Let's say the servo mechanism is slow and eccentricity swings the arm left and right. The Ballfinger spec says that the effective length of the arm is 223mm, about par for a 9 inch conventional offset arm. If the record were eccentric by 1mm, then the angular error introduced would be 0.26 degrees. How is that worse than a conventional offset arm? The stiction in a purely mechanical tangential tracker would very likely cause as much, or more, tracking error by deflecting the stylus.
Ray K
A linear servo tonearm with allowance only for vertical movement would be good Right ? If we are ok with little compromise on angular error (While the servo is moving the tonearm) compared to conventional pivoted tonearms. We can make tonearm length as less as possible so as error is further reduced.
Why cant a servo with some platter rotation calculation to move tonearm be made ?
Regards.
Why cant a servo with some platter rotation calculation to move tonearm be made ?
Regards.
Hello Hiten
A linear tangential servo tone arm must be allowed to rotate slightly about the vertical axis in order to trigger the servo .
You can't use platter rotation to control the inward motion of a tone arm because the groove pitch varies continuously from .002" to .011".
Sincerely,
Ralf
A linear servo tonearm with allowance only for vertical movement would be good Right ? If we are ok with little compromise on angular error (While the servo is moving the tonearm) compared to conventional pivoted tonearms. We can make tonearm length as less as possible so as error is further reduced.
Why cant a servo with some platter rotation calculation to move tonearm be made ?
Regards.
A linear tangential servo tone arm must be allowed to rotate slightly about the vertical axis in order to trigger the servo .
You can't use platter rotation to control the inward motion of a tone arm because the groove pitch varies continuously from .002" to .011".
Sincerely,
Ralf
Ray,
First, I have to say that I don’t like any mechanical linear tracking arms on the market except niffy’s own diy creation. This is why I went for air bearing arms. I don’t use mechanical linear tracking arms to against Ballfinger’s.
If a linear tracking arm can’t reduce tracking errors, why do we need a linear tracking arm? If a linear tracking arm can only reduce some tracking errors, in my opinion, it is not good enough. 0.26 degrees is definitely too much for me.
For an active linear arms, it can only be driven towards the center of record. For a mechanical linear arm, it can move both directions. In my opinion, it will have less tracking errors under the condition of 1 mm eccentricity although I don’t have the experiment to support my view.
I highly admired your modification of Rabco arm. I bought a Rabco off eBay two years ago. But I looked the Rabco, I completely lost confidence. Mechanically, it was terribly designed. I just didn’t have the desire to improve it at all. I recently watched a video of David’s modified Rabco. Frankly speaking, I was not impressed. I hope it was because the electronics or poor quality of the video.
Jim
First, I have to say that I don’t like any mechanical linear tracking arms on the market except niffy’s own diy creation. This is why I went for air bearing arms. I don’t use mechanical linear tracking arms to against Ballfinger’s.
How is that worse than a conventional offset arm?
If a linear tracking arm can’t reduce tracking errors, why do we need a linear tracking arm? If a linear tracking arm can only reduce some tracking errors, in my opinion, it is not good enough. 0.26 degrees is definitely too much for me.
The stiction in a purely mechanical tangential tracker would very likely cause as much, or more, tracking error by deflecting the stylus.
For an active linear arms, it can only be driven towards the center of record. For a mechanical linear arm, it can move both directions. In my opinion, it will have less tracking errors under the condition of 1 mm eccentricity although I don’t have the experiment to support my view.
I highly admired your modification of Rabco arm. I bought a Rabco off eBay two years ago. But I looked the Rabco, I completely lost confidence. Mechanically, it was terribly designed. I just didn’t have the desire to improve it at all. I recently watched a video of David’s modified Rabco. Frankly speaking, I was not impressed. I hope it was because the electronics or poor quality of the video.
Jim
Last edited:
I don't see why an active linear arm cannot move both ways. Note this is different from whether commerical offerings have implemented this.
The eccentricity question is an interesting one. Reducing the 0.55Hz FM that this causes is one of the areas you can really clean up reproduction and this is way more significant that a bit of tracking error. But does any arm configuration mitigate this effect?
The eccentricity question is an interesting one. Reducing the 0.55Hz FM that this causes is one of the areas you can really clean up reproduction and this is way more significant that a bit of tracking error. But does any arm configuration mitigate this effect?
I don't see why an active linear arm cannot move both ways. Note this is different from whether commerical offerings have implemented this.
The eccentricity question is an interesting one. Reducing the 0.55Hz FM that this causes is one of the areas you can really clean up reproduction and this is way more significant that a bit of tracking error. But does any arm configuration mitigate this effect?
Active linear tracking arm can move both ways. But it requires a very accurate tracking and a fast and precise driving system. Please see the image to see how ELP laser turntable to track the groove. As I said before, a prefect active linear arm is with ELP laser turntable tracking system.
The Ballfinger’s linear arm looks like a one way driving active arm. I can be wrong since I only looked at the photos and don’t know the details.
Attachments
Not sure I buy your line of reasoning. The ELP needs pin point tracking because it has to shine a laser into the groove. Mechanical playback has a stylus that locks you into the groove. If you tracked a linear arm as accurately as the ELP system you would end up with no net movement of the diamond.
What you really want is to track the mean of the groove, straight down the middle so the stylus can accurately do its wiggling, or at least within the limits of something that's oscillating around at 8-10Hz ! A strain gauge cartridge would possibly be a better starting point as you get position data off that which you can use to steer.
Sorry I'm encouraging things going further off topic.
What you really want is to track the mean of the groove, straight down the middle so the stylus can accurately do its wiggling, or at least within the limits of something that's oscillating around at 8-10Hz ! A strain gauge cartridge would possibly be a better starting point as you get position data off that which you can use to steer.
Sorry I'm encouraging things going further off topic.
Please look at the diagram. There are two beams. One is tracking and another is data. If only the tracking beam can be used on an active linear arm and feeding the information from the tracking beam to the motor controller, the motor will drive the cartridge to follow the groove precisely. This is what I called a perfect active linear tracking arm. I am not sure how the tracking beam works. It may track the mean of the groove. Or it may track the bottom of groove. However, it is just a thought.
Last edited:
Sorry I'm encouraging things going further off topic.
Not at all! Have fun!
===================
The only turntable with servo tonearm I am aware of that allows for left and right movement of the carriage following the eccentric record is the popular Pioneer PL-L1000 (aka Phase Linear 8000) or the flagship PL-L1. The carriage rides on a linear motor to glide on metal rollers via magnetic field. I used to own couple L1000s. The servo could overshoot and prone to failure. The servo and carriage was just not fast enough to react to eccentricity. I personally don't think tracking eccentricity is necessary. If you want that, you are better off with a mechanical parallel arm. I much rather let the servo system advancing towards the inner groove just like the Rabco or Goldmund. It is best to address the eccentricity issue before trying to track it. And if that's not practical, then I rather just let the arm wriggle like a pivot arm. For me reducing skating force is as important as reducing geometric error, hence servo arm has its supporters.
An externally hosted image should be here but it was not working when we last tested it.
An externally hosted image should be here but it was not working when we last tested it.
Last edited:
Thanks Ralf.A linear tangential servo tone arm must be allowed to rotate slightly about the vertical axis in order to trigger the servo .
You can't use platter rotation to control the inward motion of a tone arm because the groove pitch varies continuously from .002" to .011".
Sincerely,
Ralf
A little abstract thought
Hello Hiten
That should be possible.
Sincerely,
Ralf
Thanks Ralf.
A little abstract thought. How about mounting a unipivot on a servo controlled linear tracking platform ?
That should be possible.
Sincerely,
Ralf
- Home
- Source & Line
- Analogue Source
- Angling for 90° - tangential pivot tonearms