kevinkr,
Tungsten carbide is much harder ---- 9 to 9.5 on Mohs scale where quartz is a 7 on the same scale, diamond is 10 on the scale. I doubt there is much difference in drag between the two materials but the dimensional accuracy from the precision grinding of carbide far outweigh the possible benefits of common extruded quartz rod IMHO. I am sure off the shelf quartz rod is a lot cheaper than precision ground carbide.
Tungsten carbide is much harder ---- 9 to 9.5 on Mohs scale where quartz is a 7 on the same scale, diamond is 10 on the scale. I doubt there is much difference in drag between the two materials but the dimensional accuracy from the precision grinding of carbide far outweigh the possible benefits of common extruded quartz rod IMHO. I am sure off the shelf quartz rod is a lot cheaper than precision ground carbide.
It's not so much drag as rolling resistance. The bearings/wheels do not slide on the glass rods but roll on them. The coefficient of friction between the bearings and rods is not important, the hardness of them is. A good analogy is to imagine a push bike tyre. The coefficient of friction between the tyre and road is high. Let some air out of the tyre and go for a short ride, it's quite hard work. Now pump the tyre up really hard, it now takes a lot less effort to cycle the same route.
The smoothness of the surfaces can also make a big difference, like the difference between course road asphalt and the smoothness of pavement/sidewalk asphalt on your bike ride. The glass rods use by souther are, I believe, borosilicate glass (pyrex). The way these are manufactured, by molten drawing, gives an extremely smooth surface. Combining the super smooth surface with it's relatively high hardness makes this type of glass ideally for this application.
Niffy
The smoothness of the surfaces can also make a big difference, like the difference between course road asphalt and the smoothness of pavement/sidewalk asphalt on your bike ride. The glass rods use by souther are, I believe, borosilicate glass (pyrex). The way these are manufactured, by molten drawing, gives an extremely smooth surface. Combining the super smooth surface with it's relatively high hardness makes this type of glass ideally for this application.
Niffy
niffy,
It is true that glass (borosillicate or otherwise ) can be very smooth and fairly hard but as far as being accurate in all dimensions straight from the drawing process, the chances are slim to none. Precision centerless grinding is the only process I know that can give an accurate dimension to any extruded glass or metal rod, but can be expensive.
I invite you to call a few glass rod suppliers on your side of the pond and see what tolerances are offered for extruded glass rod. I checked a few companies in the USA and the best quality I found was + or - .003" per foot. You would be surprised to find that the rods are not truly round and not very straight plus these defects happen at random places along the rod. I would like to see how match a pair of these rods. The rods that the bearings ride on are just as important as the quality of the bearings used on the carriage. If you don't have the ability to measure the accuracy of the rods then you should buy rods that have a guaranteed spec. The rods used for linear bearings are common and very accurate, not too expensive.
I can tell you that if a pivot tonearm had .002" slop in the bearings the audiophile community would be howling and proclaim the arm as absolute junk--and they would be right !!!
It is true that glass (borosillicate or otherwise ) can be very smooth and fairly hard but as far as being accurate in all dimensions straight from the drawing process, the chances are slim to none. Precision centerless grinding is the only process I know that can give an accurate dimension to any extruded glass or metal rod, but can be expensive.
I invite you to call a few glass rod suppliers on your side of the pond and see what tolerances are offered for extruded glass rod. I checked a few companies in the USA and the best quality I found was + or - .003" per foot. You would be surprised to find that the rods are not truly round and not very straight plus these defects happen at random places along the rod. I would like to see how match a pair of these rods. The rods that the bearings ride on are just as important as the quality of the bearings used on the carriage. If you don't have the ability to measure the accuracy of the rods then you should buy rods that have a guaranteed spec. The rods used for linear bearings are common and very accurate, not too expensive.
I can tell you that if a pivot tonearm had .002" slop in the bearings the audiophile community would be howling and proclaim the arm as absolute junk--and they would be right !!!
Plenty of interesting thoughts here, I'm currently wrestling with some other issues. (The Windfeld is not a very good match to these arms and I am now looking for something more suitable.)
I will investigate precision ground carbide at some point in the not too distant future.
Currently gearing up to experiment with making arm wands and counter weights. This will also serve as a training exercise for the machine tools I have. (Mini lathe, mini mill and a variety of supporting tools)
I will investigate precision ground carbide at some point in the not too distant future.
Currently gearing up to experiment with making arm wands and counter weights. This will also serve as a training exercise for the machine tools I have. (Mini lathe, mini mill and a variety of supporting tools)
I agree that precision ground tungsten carbide would theoretically be better than glass but the only sources that I've found that supply nonindustrial quantities are in the States and won't ship to England. I'm stuck with glass for now but as I seem to be getting very good results using it I'm in no big rush to find tungsten replacements.
Niffy.
Niffy.
One of the reasons that this thread is so interesting to me is that I have been doing a lot of work investigating bearing friction in an attempt to improve my passive linear tracking arm. To this end I have built a test rig to accurately measure the static friction of various bearings. Static friction is more important than dynamic friction as it is higher than dynamic and the arm is constantly stop starting due to record eccentricity.
My arm is different to the souther as it uses two bearings running between two rods but the effects of bearing friction will be the same.
I have two sets of high quality bearings and have to date only fully tested one set, full ceramic zirconium oxide, as the others are fitted to my arm and I still want to listen to music, though a quick test indicated they are similar in performance. The test rig has the bearings spaced the same as my arm with the side force applied where the stylus would be to give a real world image of what's going on.
I took literally hundreds of separate readings with different carriage masses. I plotted the distribution of side force required to move the carriage for each carriage mass (30, 40, 50 and 60 grams). As my computer had gone down I had to do this old school with a pencil and paper. I had expected/hoped to see a nice Gaussian (bell curve) distribution spread over a narrow range. What I actually found was quite surprising. The distribution showed two overlapping bell curves, each with a nice Gaussian distribution, of similar magnitude and much more spread out than expected. By dividing the measured lateral force, in grams, by the carriage mass the coefficient of friction of the bearing system can be determined. The coefficients of friction calculated for each peak and the overall average were consistent between the four different carriage masses tested. The overall average coefficient of friction was 0.01. The lower mode/peek was 0.008 and the higher at 0.011. The highest level of the coefficient of friction measured was 0.015.
The bearings used in the souther are not fully ceramic and probably have a coefficient of friction even higher than those I measured. I do not know the exact mass of the souther carriage. If I assume that it is 40g including cartridge then a 0.011 c.o.f. ,the higher mode, would result in a lateral force of 0.44g. Using a cartridge of 9um/mN compliance with a 5mm long cantilever would result in a lateral tracking error of 0.45°. Still better than a pivoted arm but not perfect. The maximum lateral tracking error would be higher still.
With extra testing I determined that the peeks in the distribution curve were connected to the rotational angle of the bearing. If the bearings were positioned with a single ball at the bottom this resulted in the higher mode and if positioned with two balls at the bottom in the lower mode. As the carriage moves across the record the lateral force varies up and down by a small amount in absolute terms but a large amount in relative terms, about 40%.
The bearings used for this arm are designed for high speed applications where only their dynamic friction is of concern and small variations within a single revolution do not matter. Our application is the opposite of this, very low speed.
We have mentioned the importance of having a very accurate smooth surface of the rails. The same is also true for the outside of the bearings. Unfortunately for the intended use of these bearings only the dimensional accuracy of the outside is important and not the surface finish. Polishing the outside of the bearings can help to reduce friction and lower noise. This is definitely worth doing but extreme care must be taken to avoid contamination of the bearing with polishing compound.
My experiments are on going with the aim of producing lower friction, better sounding bearings. Currently I have just made some pin bearings, similar to those used in watches and clocks and designed for low speed. So far this is looking very promising. The distribution for these bearings show a normal Gaussian distribution, with no double peeks, a narrower distribution and most importantly less than half the friction. I am midway through building a new rail to test these bearings on my arm so I do not know how they effect sound quality as yet. On the hardness of materials used. I initially used aluminium for the wheels, to keep mass down, and got a coefficient of friction of 0.005. Pretty good. I then tried 316 stainless steel and the coefficient of friction dropped to 0.0039, over 20% improvement. Hardness really is important. I would love to try tungsten carbide rails at some point to see if any further improvements can be made. Also, currently the cups of my pin bearings are just stainless steel. If the new bearing design shows an improvement in sound quality over the ball bearings then I will replace the cups with sapphire vee jewels, much harder than steel and should lower friction even further. As the vee jewels are expensive l want to be sure that they work before splashing out on them. Pin bearings should also have several advantages other than lower more consistent friction. With ball race bearings only the balls at the bottom are under load, the rest are loose and free to move about. This is a possible source of chatter. Although any chatter would be at a very low level, and not directly heard, it could still smear microdynamics. With pin bearings there are no unloaded components so the possibility of chatter is greatly reduced. Also the carriage is supported on what are essentially spikes. This should give very effective mechanical grounding, the same principle as spiked equipment supports or speaker stands. Finally, compared to ball races the pin bearings are much quieter. Rolling my test carriage backwards and forwards on my test rigs rail with ball races fitted results in a clearly audible noise, with the pin bearings it is almost silent.
The last section is probably a bit off topic as it is probably very difficult to upgrade a souther to use this type of bearing but might be worth trying.
Niffy
My arm is different to the souther as it uses two bearings running between two rods but the effects of bearing friction will be the same.
I have two sets of high quality bearings and have to date only fully tested one set, full ceramic zirconium oxide, as the others are fitted to my arm and I still want to listen to music, though a quick test indicated they are similar in performance. The test rig has the bearings spaced the same as my arm with the side force applied where the stylus would be to give a real world image of what's going on.
I took literally hundreds of separate readings with different carriage masses. I plotted the distribution of side force required to move the carriage for each carriage mass (30, 40, 50 and 60 grams). As my computer had gone down I had to do this old school with a pencil and paper. I had expected/hoped to see a nice Gaussian (bell curve) distribution spread over a narrow range. What I actually found was quite surprising. The distribution showed two overlapping bell curves, each with a nice Gaussian distribution, of similar magnitude and much more spread out than expected. By dividing the measured lateral force, in grams, by the carriage mass the coefficient of friction of the bearing system can be determined. The coefficients of friction calculated for each peak and the overall average were consistent between the four different carriage masses tested. The overall average coefficient of friction was 0.01. The lower mode/peek was 0.008 and the higher at 0.011. The highest level of the coefficient of friction measured was 0.015.
The bearings used in the souther are not fully ceramic and probably have a coefficient of friction even higher than those I measured. I do not know the exact mass of the souther carriage. If I assume that it is 40g including cartridge then a 0.011 c.o.f. ,the higher mode, would result in a lateral force of 0.44g. Using a cartridge of 9um/mN compliance with a 5mm long cantilever would result in a lateral tracking error of 0.45°. Still better than a pivoted arm but not perfect. The maximum lateral tracking error would be higher still.
With extra testing I determined that the peeks in the distribution curve were connected to the rotational angle of the bearing. If the bearings were positioned with a single ball at the bottom this resulted in the higher mode and if positioned with two balls at the bottom in the lower mode. As the carriage moves across the record the lateral force varies up and down by a small amount in absolute terms but a large amount in relative terms, about 40%.
The bearings used for this arm are designed for high speed applications where only their dynamic friction is of concern and small variations within a single revolution do not matter. Our application is the opposite of this, very low speed.
We have mentioned the importance of having a very accurate smooth surface of the rails. The same is also true for the outside of the bearings. Unfortunately for the intended use of these bearings only the dimensional accuracy of the outside is important and not the surface finish. Polishing the outside of the bearings can help to reduce friction and lower noise. This is definitely worth doing but extreme care must be taken to avoid contamination of the bearing with polishing compound.
My experiments are on going with the aim of producing lower friction, better sounding bearings. Currently I have just made some pin bearings, similar to those used in watches and clocks and designed for low speed. So far this is looking very promising. The distribution for these bearings show a normal Gaussian distribution, with no double peeks, a narrower distribution and most importantly less than half the friction. I am midway through building a new rail to test these bearings on my arm so I do not know how they effect sound quality as yet. On the hardness of materials used. I initially used aluminium for the wheels, to keep mass down, and got a coefficient of friction of 0.005. Pretty good. I then tried 316 stainless steel and the coefficient of friction dropped to 0.0039, over 20% improvement. Hardness really is important. I would love to try tungsten carbide rails at some point to see if any further improvements can be made. Also, currently the cups of my pin bearings are just stainless steel. If the new bearing design shows an improvement in sound quality over the ball bearings then I will replace the cups with sapphire vee jewels, much harder than steel and should lower friction even further. As the vee jewels are expensive l want to be sure that they work before splashing out on them. Pin bearings should also have several advantages other than lower more consistent friction. With ball race bearings only the balls at the bottom are under load, the rest are loose and free to move about. This is a possible source of chatter. Although any chatter would be at a very low level, and not directly heard, it could still smear microdynamics. With pin bearings there are no unloaded components so the possibility of chatter is greatly reduced. Also the carriage is supported on what are essentially spikes. This should give very effective mechanical grounding, the same principle as spiked equipment supports or speaker stands. Finally, compared to ball races the pin bearings are much quieter. Rolling my test carriage backwards and forwards on my test rigs rail with ball races fitted results in a clearly audible noise, with the pin bearings it is almost silent.
The last section is probably a bit off topic as it is probably very difficult to upgrade a souther to use this type of bearing but might be worth trying.
Niffy
The only part of the equation I don't know is the carriage mass, and I have a spare and representative bearings and can therefore measure them. I'll try to do that tonight.
The mass of several different arm wands and counter weights are given earlier in the thread. I doubt the carriage weighs more than a couple of grams..
Horizontal moving mass could be significantly lower than 15gms including a 5gm cartridge with some plausible combinations of wand, counter weight and the carriage.
The Tri-Quartz set up with the Royal is going to be slightly under 30gms in the horizontal plane.
The mass of several different arm wands and counter weights are given earlier in the thread. I doubt the carriage weighs more than a couple of grams..
Horizontal moving mass could be significantly lower than 15gms including a 5gm cartridge with some plausible combinations of wand, counter weight and the carriage.
The Tri-Quartz set up with the Royal is going to be slightly under 30gms in the horizontal plane.
On the second set of comments since I might eventually attempt to build an arm from scratch the information is useful and might help me to design and build something that might be an improvement in some aspects of performance over the Souther. (This all is predicated on me acquiring some bona-fide skills to go along with the machine tools I already own.. lol)
niffy,
WOW, I am officially impressed in your efforts to make the best mechanical linear tonearm possible !!! What diameter rods do you use for the rails ? What length rod ? My reason for asking is if you are flexible about your rod dimensions I might be able to get you some tungsten carbide rods but they may be in inch dimension rather then mm. I will send them to you for free as my contribution to the cause. Also, small diameter carbide pins would be no problem. I think full ceramic bearings would be good enough but sapphire may be better--but very brittle. Send me an email at joesnipe767@yahoo.com if I can help. This is how you move the performance envelop of this type of arm forward.
WOW, I am officially impressed in your efforts to make the best mechanical linear tonearm possible !!! What diameter rods do you use for the rails ? What length rod ? My reason for asking is if you are flexible about your rod dimensions I might be able to get you some tungsten carbide rods but they may be in inch dimension rather then mm. I will send them to you for free as my contribution to the cause. Also, small diameter carbide pins would be no problem. I think full ceramic bearings would be good enough but sapphire may be better--but very brittle. Send me an email at joesnipe767@yahoo.com if I can help. This is how you move the performance envelop of this type of arm forward.
Hi Kevinkr
The mass of the carriage I am working from is the entire piece that moves horizontally including bearings. Even with a 5g cartridge I would be surprised if the total mass was as low as 15g but then Lou was aiming at minimum mass and low energy storage so maybe.
WOW hottattoo
That is an amazing offer, thank you very much. The rods I am using are 4mm diameter and 170mm long. I can be flexible with anything in this ballpark.Please please let me know if you can source tungsten carbide rods close to these dimensions, I would be extremely grateful.
In an earlier post you mentioned the difficulty in obtaining quality glass rods, I cannot remember who I got mine from, I did import them from the States and had to buy a batch of thirty at 30cm but at least that gave me lots to experiment with. The two I've just glued into my new rail were thoroughly checked. I measured them with a micrometer in dozens of places each. The measured diameter was to within 5um on all measurements. Also rolling them against each other on a mirror showed no deviation from absolutely straight. Looks like I got Lucky. I've attached a couple of pictures of my turntable/arm combo as it is at the moment. All hand built by myself with no fancy tools. (Having a bit of an issue uploading photos)
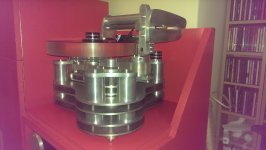
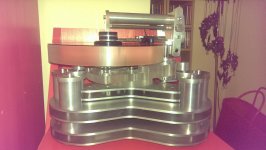
Niffy
The mass of the carriage I am working from is the entire piece that moves horizontally including bearings. Even with a 5g cartridge I would be surprised if the total mass was as low as 15g but then Lou was aiming at minimum mass and low energy storage so maybe.
WOW hottattoo
That is an amazing offer, thank you very much. The rods I am using are 4mm diameter and 170mm long. I can be flexible with anything in this ballpark.Please please let me know if you can source tungsten carbide rods close to these dimensions, I would be extremely grateful.
In an earlier post you mentioned the difficulty in obtaining quality glass rods, I cannot remember who I got mine from, I did import them from the States and had to buy a batch of thirty at 30cm but at least that gave me lots to experiment with. The two I've just glued into my new rail were thoroughly checked. I measured them with a micrometer in dozens of places each. The measured diameter was to within 5um on all measurements. Also rolling them against each other on a mirror showed no deviation from absolutely straight. Looks like I got Lucky. I've attached a couple of pictures of my turntable/arm combo as it is at the moment. All hand built by myself with no fancy tools. (Having a bit of an issue uploading photos)
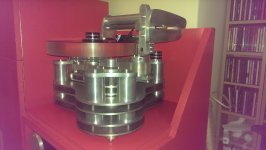
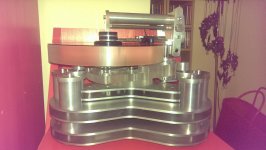
Niffy
Attachments
Wow, Niffy that looks completely amazing. Fine workmanship and a lot of thought obviously went into the design as well. 😀
Not sure if these guys would be of any use True Point (UK) Ltd - Precision engineers Found them a few days ago looking for jewelled bearings. As they do SME mods and some pink triangle work as well as a man+dog machine shop they can at least be enjoyable to talk to !
P.S. Nice rig. 🙂
P.S. Nice rig. 🙂
Hi niffy,
I figured this would happen. I can get 2 12" long carbide rods in either .1463" or .1875" diameter . I am waiting to hear from one person about 4mm carbide rod--should know in a day or two. Is that any help to you ? That is a beautiful turntable !!!
I figured this would happen. I can get 2 12" long carbide rods in either .1463" or .1875" diameter . I am waiting to hear from one person about 4mm carbide rod--should know in a day or two. Is that any help to you ? That is a beautiful turntable !!!
Arm wands
Tonight I pulled the hollow arm tube out of one of my two light weight arm wands and cut a replacement arm wand from some stainless steel stock that came this week-end, I made it about 3/8" inches longer than the arm tube it replaced. It press fit quite nicely onto the old Souther head shell. I've installed the Benz on the SLA-3 and reinstalled it on the MKII. So far it seems to be working pretty well.
The cartridge weighs in at 10.7gms, the sole counterweight is 6gms, the arm wand is 5.2gms, and carriage is about 6gms for a total mass in the horizontal plane of 27.9gms.
Tonight I pulled the hollow arm tube out of one of my two light weight arm wands and cut a replacement arm wand from some stainless steel stock that came this week-end, I made it about 3/8" inches longer than the arm tube it replaced. It press fit quite nicely onto the old Souther head shell. I've installed the Benz on the SLA-3 and reinstalled it on the MKII. So far it seems to be working pretty well.
The cartridge weighs in at 10.7gms, the sole counterweight is 6gms, the arm wand is 5.2gms, and carriage is about 6gms for a total mass in the horizontal plane of 27.9gms.
Attachments
Niffy, the carriage weighs in at 5.93gms.. The only thing missing are the fasteners which are currently on the arms. As mentioned the current set up on the SLA-3 has a total mass in the horizontal plane of around 28gms.
Completely OEM with a 5gm cartridge it might be possible to get the total mass down close to 15 - 16gms, but I will continue to use MC cartridges in the 8 - 11gm range..
Completely OEM with a 5gm cartridge it might be possible to get the total mass down close to 15 - 16gms, but I will continue to use MC cartridges in the 8 - 11gm range..
Attachments
Hi all and thank you for your kind words.
I am planning on starting a new thread to describe my deck once it's completely finished. I'll probably focus more on the design and my philosophy behind it rather than the actual building, more the why than how.
Bill.
I have found true point. They are one of the two suppliers I have bookmarked for vee jewels.
Hottattoo
I could adapt to any of the sizes you've found. 4mm would be ideal though. I'm in no hurry as I would want to perfect the design using the glass rods then build the same in carbide and then compare. The rail is quite a complicated build which has the rods epoxied into a channel. Maximum rigidity and damping but a complete new rail would be needed to be built, I can't just swap the rods out. Thank you once again.
Kevinkr
That really is a low mass arm. At 28g the lateral tracking error, based on my previous example, would drop to only 0.31°. That's pretty close to completely inaudible. The lateral tracking error due to record eccentricity on the inner groove of an average record is higher than this. Nice.
Niffy
I am planning on starting a new thread to describe my deck once it's completely finished. I'll probably focus more on the design and my philosophy behind it rather than the actual building, more the why than how.
Bill.
I have found true point. They are one of the two suppliers I have bookmarked for vee jewels.
Hottattoo
I could adapt to any of the sizes you've found. 4mm would be ideal though. I'm in no hurry as I would want to perfect the design using the glass rods then build the same in carbide and then compare. The rail is quite a complicated build which has the rods epoxied into a channel. Maximum rigidity and damping but a complete new rail would be needed to be built, I can't just swap the rods out. Thank you once again.
Kevinkr
That really is a low mass arm. At 28g the lateral tracking error, based on my previous example, would drop to only 0.31°. That's pretty close to completely inaudible. The lateral tracking error due to record eccentricity on the inner groove of an average record is higher than this. Nice.
Niffy
I meant truepoint also do tungsten rods!
Thanks Bill.
I can't believe I didn't see these. I've browsed their site looking at pivots and jewels several times. Truepoint didn't come up at all in my search for tungsten rods. I've bookmarked them as a one stop shop for all things bearing. They seem to be able to produce almost anything. I wonder if they could make 15mm diameter solid ruby wheels to run on the tungsten rods or would that be overkill. Lol.
Niffy
NP. I found them mulling about ruby bearings. I have more turntable parts than arms so need to decide if I am brave enough to try and make an arm. Never had a true gimbal arm and on paper they look easy...
Hi Niffy,
Are you still using two rods and two bearings construction? I used two rods and two bearings when I started to build my very first linear arm. But I gave it up just one version because I think it is not safe for cartridge. The carriage can be easily dropped off the rail. Do you have any safety device to ensure the carriage staying on the rail?
Jim
Are you still using two rods and two bearings construction? I used two rods and two bearings when I started to build my very first linear arm. But I gave it up just one version because I think it is not safe for cartridge. The carriage can be easily dropped off the rail. Do you have any safety device to ensure the carriage staying on the rail?
Jim
- Status
- Not open for further replies.
- Home
- Source & Line
- Analogue Source
- Souther Linear Tonearm on A TD-124