That's how I understood it as well. And, honestly, as this is not my mother language, it sometimes is not that easy to follow John's repetitive style, and I sometimes just don't have the time and energy to read all of it.
That said, I am thankful for all your effort for sure, which also includes Jamie of course and his engagement on the o ring front.
That said, I am thankful for all your effort for sure, which also includes Jamie of course and his engagement on the o ring front.
And, after our rave reviews of the Torlon bushes here they will be sold in a minute. There is also the German analogue forum with several owners of this table who could be interested.
As I already confirmed by email, I'm still in with 2 pairs. And as far as I followed this thread noone left the GB?!
Yes there is a misunderstanding.
I could have requested a confirmation to agree with the list I produced, but missed this as a request.
I do not desire to personally purchase more than 5 Sets of the Torlon Bushes.
I see this as being quite fair to initiate the GB.
Audio Musica - 2 Sets
Dubai 2000 - 1 Set
Jamie 123 - 1 Set
Jogi - 1 Set
JohnnoG - 2 Sets + 3 Sets that are Surplus.
As Dubai2000 has already made their intention clear.
If the other Three Contributors are able to confirm that they intend to continue with the GB, this will be my reassurance to limit the quantity I will be paying for.
I will hold off until Friday, before a I contact the Engineer.
In relation to the Silicone Oil.
There is a vast range of viscosities, I have seen these Oils on offer from 100cSt to 50000cSt.
It also appears through investigation that the 'cSt' and 'wt' share the same values as the 1000wt is passed, this can be further investigated and confirmed.
I could have requested a confirmation to agree with the list I produced, but missed this as a request.
I do not desire to personally purchase more than 5 Sets of the Torlon Bushes.
I see this as being quite fair to initiate the GB.
Audio Musica - 2 Sets
Dubai 2000 - 1 Set
Jamie 123 - 1 Set
Jogi - 1 Set
JohnnoG - 2 Sets + 3 Sets that are Surplus.
As Dubai2000 has already made their intention clear.
If the other Three Contributors are able to confirm that they intend to continue with the GB, this will be my reassurance to limit the quantity I will be paying for.
I will hold off until Friday, before a I contact the Engineer.
In relation to the Silicone Oil.
There is a vast range of viscosities, I have seen these Oils on offer from 100cSt to 50000cSt.
It also appears through investigation that the 'cSt' and 'wt' share the same values as the 1000wt is passed, this can be further investigated and confirmed.
John, I read audiomusica's post (183) as a clear indication that he is still in and I know from Jogi personally that he is still ready to go as well....
Hi All, apologies for my causing of the turbulence.
I will continue with the proposed GB as I am confident Jamie is remaining interested as well.
I will continue with the proposed GB as I am confident Jamie is remaining interested as well.
Don't sweat it - happens to the best of us - and thx again for your effort.
BTW: Does anybody know the diameter of the ball at the bottom og the spindle? Methinks it would be interesting to use/try a different material....
BTW: Does anybody know the diameter of the ball at the bottom og the spindle? Methinks it would be interesting to use/try a different material....
it needs careful drilling out,preferably on a lathe,if yours is not marked i wouldn't worry about it.Don't sweat it - happens to the best of us - and thx again for your effort.
BTW: Does anybody know the diameter of the ball at the bottom og the spindle? Methinks it would be interesting to use/try a different material....
In Post 45 there is the image of the New Part Sump Plug that has a two part construction.
The Thrust Pad incorporated into the design is a separate part and can be exchanged.
This design leaves options for other Thrust Pad Materials to be used.
These alternative options should be just as good as looking to exchange a interference for ball on the spindle.
Again a search on the Lenco Heaven forum will uncover a variety of materials used as a thrust pad with a steel ball.
The important consideration for the New Thrust Pad design is that it is a exchange part with the White Plastic Thrust Pad/ Sump Plug.
With this method being used, to return the TT back to its original condition is relatively easy to achieve.
The ease of returning the TT as an original spec, is something I have been working carefully with.
In each of the progressive ideas for the designs I have on paper.
The removed Phosphor Bronze Bushes are the only parts that would not be reinstated if the TT was returned to original spec, only because they are not in a condition I feel is of any value.
The Thrust Pad incorporated into the design is a separate part and can be exchanged.
This design leaves options for other Thrust Pad Materials to be used.
These alternative options should be just as good as looking to exchange a interference for ball on the spindle.
Again a search on the Lenco Heaven forum will uncover a variety of materials used as a thrust pad with a steel ball.
The important consideration for the New Thrust Pad design is that it is a exchange part with the White Plastic Thrust Pad/ Sump Plug.
With this method being used, to return the TT back to its original condition is relatively easy to achieve.
The ease of returning the TT as an original spec, is something I have been working carefully with.
In each of the progressive ideas for the designs I have on paper.
The removed Phosphor Bronze Bushes are the only parts that would not be reinstated if the TT was returned to original spec, only because they are not in a condition I feel is of any value.
On the SP10 Thread, there is an interesting information about the impact of metal on controlling transferred energies through them.
With this in mind, I am wondering if Jamie's Brass Donut for the Pressed Bowl, will be further benefited if a Lead Spacer was clamped between the Base of the Bowl and the Brass.
The thoughts behind this is that there is a possibility that energy that is transferred to this point will be better dissipated and not travel back through the Bearing Assembly.
When the Donut is braced as well, the energy soak away effect may even be better improved.
This is in keeping with methods utilised to reduce energy getting transferred to and detected by the Stylus /Cantilever.
With this in mind, I am wondering if Jamie's Brass Donut for the Pressed Bowl, will be further benefited if a Lead Spacer was clamped between the Base of the Bowl and the Brass.
The thoughts behind this is that there is a possibility that energy that is transferred to this point will be better dissipated and not travel back through the Bearing Assembly.
When the Donut is braced as well, the energy soak away effect may even be better improved.
This is in keeping with methods utilised to reduce energy getting transferred to and detected by the Stylus /Cantilever.
the ring is now in place,i had to raise the pcb up about 5mm as a couple of transistors hit the ring. i have held off this week from doing anything to the new sealing thrust pad,i have had a change of mind regarding using o rings,i will try 2 flat viton rings of 1.5 mm thickess ,1 on each side of the brass washer,think car oil filter type rubber seal and you'll get the picture. i think this is a better first approach.

The Brass Donut is looking quite Bling.
The attachment is an update to a Rough Sketch Drawing I put on paper in the earliest days of my investigations into the TTS 8000 Bearing.
It is not perfect in any ways but shows the general ideas I had on Paper.
The Update is that I am trying to look at the design today to keep as close to the Original as possible and not need to exchange the original parts.
With Jamie's work now being carried out on the preparations to produce a design for making the Bearing Assembly a more rigid assembly and create a method that can reduce flexion of the assembly, as well as actively looking into a method to replace the Square Walled Washer.
I thought I would add the additional design considerations that I had on paper for the internal the bearing housing, that was to be used with the the Torlon Bushes.
The attached image shows two methods the bottom partial detail is showing a recent idea I considered where an added felt pad to cap of the top of the Bearing Housing is incorporated to create a Barrier to Oil.
To prepare for the use of a felt cap, it is to be assumed the Original White Plastic Bush will need a reduction in length, to accommodate creating the recess to seat the felt pad in.
In general the main detail is showing the Top Bush which has 5mm Thick wall has a 2mm Diameter Hole that can receive a Grub Screw to seal it.
There are Two Holes produced on the opposite sides of the Bush.
One is to inject a Lubrication and the other as suggested by the Engineer is to enable air to escape as the Lubrication Levels are worked with.
The Outer wall of the Original White Sleeve and the Lowest set Torlon Sleeve will have a small rebate produced on the entire length of the Wall.
When assembling the Bushes within the bearing housing the Rebates on each bush and the Top Bush Hole will need to be aligned to create a unobstructed channel to enable the Lubricant to travel to the base of the Spindle and collect within the Pressed Metal Bowls base.
I would say a 10Ml Syringe with a 1mm Hyperdermic Needle can be used to add or extract the Oil.
The incremental Ml's of Oil being added can be recorded to see where the maximum impact is to be discovered.
Keeping in mind a Hydrodynamic Lubrication is the goal to be maintained at the Spindle /Bush Interface.
If there is any of the contributors thoughts that are leaning toward filling the entire depth of the bearing housing, I added the Felt Pad Cap as an additional option to act as a Barrier to help with containing the Level of Oil Selected.
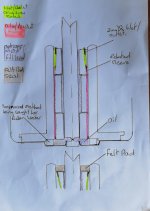
The attachment is an update to a Rough Sketch Drawing I put on paper in the earliest days of my investigations into the TTS 8000 Bearing.
It is not perfect in any ways but shows the general ideas I had on Paper.
The Update is that I am trying to look at the design today to keep as close to the Original as possible and not need to exchange the original parts.
With Jamie's work now being carried out on the preparations to produce a design for making the Bearing Assembly a more rigid assembly and create a method that can reduce flexion of the assembly, as well as actively looking into a method to replace the Square Walled Washer.
I thought I would add the additional design considerations that I had on paper for the internal the bearing housing, that was to be used with the the Torlon Bushes.
The attached image shows two methods the bottom partial detail is showing a recent idea I considered where an added felt pad to cap of the top of the Bearing Housing is incorporated to create a Barrier to Oil.
To prepare for the use of a felt cap, it is to be assumed the Original White Plastic Bush will need a reduction in length, to accommodate creating the recess to seat the felt pad in.
In general the main detail is showing the Top Bush which has 5mm Thick wall has a 2mm Diameter Hole that can receive a Grub Screw to seal it.
There are Two Holes produced on the opposite sides of the Bush.
One is to inject a Lubrication and the other as suggested by the Engineer is to enable air to escape as the Lubrication Levels are worked with.
The Outer wall of the Original White Sleeve and the Lowest set Torlon Sleeve will have a small rebate produced on the entire length of the Wall.
When assembling the Bushes within the bearing housing the Rebates on each bush and the Top Bush Hole will need to be aligned to create a unobstructed channel to enable the Lubricant to travel to the base of the Spindle and collect within the Pressed Metal Bowls base.
I would say a 10Ml Syringe with a 1mm Hyperdermic Needle can be used to add or extract the Oil.
The incremental Ml's of Oil being added can be recorded to see where the maximum impact is to be discovered.
Keeping in mind a Hydrodynamic Lubrication is the goal to be maintained at the Spindle /Bush Interface.
If there is any of the contributors thoughts that are leaning toward filling the entire depth of the bearing housing, I added the Felt Pad Cap as an additional option to act as a Barrier to help with containing the Level of Oil Selected.
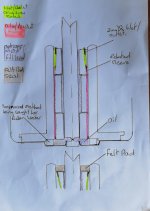
a small update from me, i've made a new sealing washer from brass,i turned 3 different thicknesses 1.2mm, 1.5mm and 2mm. i think the 2 mm might be too much so i started with the 1.5mm and then that has two viton rubber washers with i punched myself on top and bottom ,each are 1.5mm thick so all in we have 4,5mm. the recess for the washer measures 3.95mm approx.
early days but i think its oil tight,over filling the bearing housing and pushing down on the spindle sends the oil up and out of the bearing housing rather than out through the bottom which is a good sign.
i will leave it powered up and spinning for a few hours and take it apart and check.
original washer on the left,new on the right.
early days but i think its oil tight,over filling the bearing housing and pushing down on the spindle sends the oil up and out of the bearing housing rather than out through the bottom which is a good sign.
i will leave it powered up and spinning for a few hours and take it apart and check.
original washer on the left,new on the right.


Hats off to you Jamie, for the perseverance and for taking the time to produce parts and carry out trials. Good Luck with the Testing.
Wow Jamie, excellent work, hats off. For me this is the crucial part in the whole bearing assembly, everything else is just the icing on the cake. Btw one side effect of a leaking bearing is the unwanted "lubrication" of the circuit board, which can cause damage.
Would be interesting to check if there is a difference in sound with an oil filled bearing as a result of some damping.
I see another potential group buy at the horizon😛
For John: let us know when you need some payment from us...and also big thank you for your research and effort.
Would be interesting to check if there is a difference in sound with an oil filled bearing as a result of some damping.
I see another potential group buy at the horizon😛
For John: let us know when you need some payment from us...and also big thank you for your research and effort.

- Home
- Source & Line
- Analogue Source
- Sony TTS 8000 (All in Discussion)