I have 1-1/2" of material on the sides and angled the screws.I sunk metal threads into the wood for repeat abuse, but
neglected to angle them away from the sides enough to
get a power tool in there.
Thanks; that way you can try different speakers too with differant throats."...speaker baffle removable..." Nice touch, that'll allow you to play around with the throat configuration. Great to see you making progress.
Last edited:
I was thinking about that and may be I will sand by hand, but with the PL glue I am not to worried about it. That stuff is crazy!!!!!!!!!!be carefull with the beltsander.
it eets away a few millimetrs in no time.
Painting is not up to me the carpenter that is suppose to be helpping me is doing the painting. Thanks anyway. AndyYou could paint the inside with something like this:
We call them "T" nuts, these are six point, and the proper way to apply them;Are you SS15 (and similar) builders using hurricane nuts to secure your drivers?
Attachments
Is this the dat code? I did not see anything else.BTW -- Just check the date code.
Attachments
Mids tomorrow. Burn in starts Friday. tests Monday !!!! YES!!!! I never made speakers before thanks for all your help!!!!!!!!!!!!!!
Andy
Andy
Is this the dat code? I did not see anything else.
That's the part number for the cone. Look for a gray sticker on one of the basket arms, it's probably on the inside.
Mids tomorrow. Burn in starts Friday. tests Monday !!!! YES!!!! I never made speakers before thanks for all your help!!!!!!!!!!!!!!
Andy
Sweeeet! result numbers in the thread monday night for us all to digest! 😀
We call them "T" nuts, these are six point, and the proper way to apply them;
Hurricane nuts are just a different type, the barbs are on the barrel:
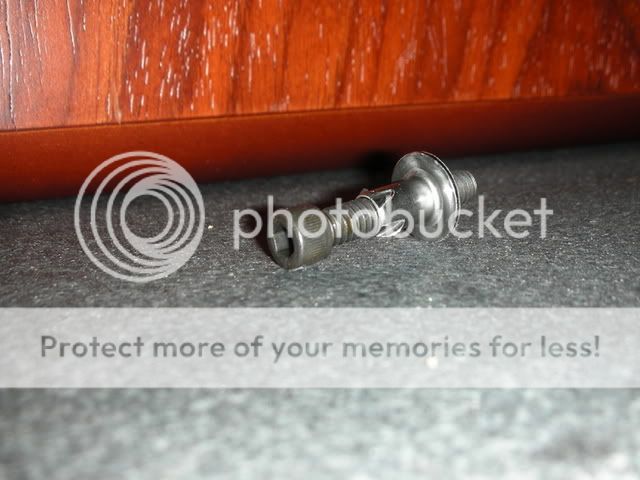
Dan; How well do thay hold? Looks like thay could strip easy. AndyHurricane nuts are just a different type, the barbs are on the barrel:
Dan; How well do thay hold? Looks like thay could strip easy. Andy
The holding power may be greater than T nuts because the barrel is longer, however they have the same limitations when it comes to installation. Generally for best results the hole should be tight to the barrel and I always put some adhesive on them to help keep them from getting knocked loose. And just like T nuts if you cross-thread and get stuck - your screwed 😱
I did use hurricanes for the loudspeaker, but not for attachment of the baffle.
Used brass inserts, cause I had a blind hole situation, no access to backside.
Also can't use T or Hurricane styles when hole purposely drilled at an angle.
Tool access is very difficult if you bolt the baffle to its cleats with no angle.
T-Nuts can't be driven into some hardwood, points break or bend every time.
Hurricanes and inserts can. And my cleats were impossibly hard oak 1x1 strip.
Don't think I would elect for oak cleats again. Oak required too much effort.
Used brass inserts, cause I had a blind hole situation, no access to backside.
Also can't use T or Hurricane styles when hole purposely drilled at an angle.
Tool access is very difficult if you bolt the baffle to its cleats with no angle.
T-Nuts can't be driven into some hardwood, points break or bend every time.
Hurricanes and inserts can. And my cleats were impossibly hard oak 1x1 strip.
Don't think I would elect for oak cleats again. Oak required too much effort.
Last edited:
Two suggestions:
These work much better than T or Hurricane Nuts: McMaster-Carr
Rotating the inserts 1/8 turn gives you knuckle room
These work much better than T or Hurricane Nuts: McMaster-Carr
Rotating the inserts 1/8 turn gives you knuckle room
Attachments
You missing the knuckle room problem, not the speaker.
Bolting a removable baffle into the enclosure is always
going to involve a few locations at inside 2 way corners.
Flange on that insert would make it very hard to use at
the required angle. And would it be pull out proof in blind
hole that can only be inserted from the front? Lose the
flange, and maybe you have something...
Bolting a removable baffle into the enclosure is always
going to involve a few locations at inside 2 way corners.
Flange on that insert would make it very hard to use at
the required angle. And would it be pull out proof in blind
hole that can only be inserted from the front? Lose the
flange, and maybe you have something...
The flange "crushes" into the ply ... no problem. My post was to address speaker mounting, not as a reply to your post, sorry.
Last edited:
KenPeter: You can buy hex wrenches with a "ball" end. They allow you to turn a hex screw when you can't get straight on.
I couldn't use a ball end for the first turn to break one loose.
Not talking small amount of force. Possibly shellac adheres with the
lacquer on my brass furniture bolts? Getting them in is much easier
than getting them back out later. If I had used steel, I would not
fear so much to damage the bolts.
You can't really see the ones up inside where I am having difficulty,
but they are the same style as those visible on the front. The old
DeltaPro12 baffle is now SigmaPro18A2, just barely fits with much
internal rasping required to clear. No logo to display on the 18, so
bolt pattern for that larger loudspeaker was rotated more sensibly.
Its the baffle to cleat bolts that are the clearance problem.
Not talking small amount of force. Possibly shellac adheres with the
lacquer on my brass furniture bolts? Getting them in is much easier
than getting them back out later. If I had used steel, I would not
fear so much to damage the bolts.
You can't really see the ones up inside where I am having difficulty,
but they are the same style as those visible on the front. The old
DeltaPro12 baffle is now SigmaPro18A2, just barely fits with much
internal rasping required to clear. No logo to display on the 18, so
bolt pattern for that larger loudspeaker was rotated more sensibly.
Its the baffle to cleat bolts that are the clearance problem.
Attachments
Last edited:
- Home
- Loudspeakers
- Subwoofers
- Single sheet TH challenge