I forgot theory is 1500 rpm at 50 Hz. 1800 rpm at 60 Hz for the theory of an induction motor. but no induction motor reaches the theoretical speed. reducing voltage reduces the torque and consequently the motor loses the laps.
simone lucchetti
simone lucchetti
I forgot theory is 1500 rpm at 50 Hz. 1800 rpm at 60 Hz for the theory of an induction motor. but no induction motor reaches the theoretical speed. reducing voltage reduces the torque and consequently the motor loses the laps.
simone lucchetti
Hello Simon, nice to hear from you. One of the problems that has led to the question of whether rebuilt motors are for some reason running too fast is that to compensate, some people have been forced to adjust the eddy current brake so that it applies more braking force. When this adjustment is made, it seems to cause the pulley to generate more noise. Have you been forced to make an eddy current brake adjustment like this? What do you find is the average clearance in millimeters between the brake and the pulley? - Jim
the thorens td 124 is designed with the use of the brake. and the alternative would be to reduce the diameter of the pulley to get closer to the correct speed. I build a turntable that has an engine and use asynchronous Bodine 2 brakes. and I honestly do not know this problem. the other way is to mount as I do on my turntable synchronous motor always American and then build a controller that speed by varying the frequency of the network varies the engine speed . we have built a controller for synchronous motor . in my opinion and I think I know " something about thorens 124 " the fault lies in the bushings that are too vary the engine speed . just a nothing and the engine rpm changes . I tried this for an engine that uses ball bearings. the engine bearings are more noisy but you have a variation of hot and cold 3 laps of più.i engine bearings such as the thorens td 124 have large variations in speed just because the bushings move . I have designed a new bushing for the 124 is very similar to that of the Garrard 301 but I have not had time to try it. simone sorry for my english :-(
Hi Simone.
Thanks for joining this discussion.
For me the questions began when I noticed different values being reported as a nominal rpm for the E50.
Bung: 1350
Yourself: ~1440
And those, are for 50 hz operation. 60 hz must be greater by approx 17%.
This caused me to wonder what rpm would be necessary for the platter to turn at 33-1/3rd. And I'm in NA where the mains are 60 hz.
In post #1035 I calculated that if platter rpm is 33-1/3rd rpm then the motor shaft must be turning ~1600 rpm. When using the 60 hz drive pulley. I think this makes sense and helps me to accept that Bung must be incorrect in his statement of 1350 rpm.
I'll send an email to Joachim to see if his research has turned up any more data on the E50.
-Steve
Thanks for joining this discussion.
For me the questions began when I noticed different values being reported as a nominal rpm for the E50.
Bung: 1350
Yourself: ~1440
And those, are for 50 hz operation. 60 hz must be greater by approx 17%.
This caused me to wonder what rpm would be necessary for the platter to turn at 33-1/3rd. And I'm in NA where the mains are 60 hz.
In post #1035 I calculated that if platter rpm is 33-1/3rd rpm then the motor shaft must be turning ~1600 rpm. When using the 60 hz drive pulley. I think this makes sense and helps me to accept that Bung must be incorrect in his statement of 1350 rpm.
I'll send an email to Joachim to see if his research has turned up any more data on the E50.
-Steve
I don't recollect the exact ratios, but the motor speed is primarily determined by line frequency, but load and line voltage also play a pretty significant role as well.
I would agree that an unloaded motor that runs faster will require more eddy current braking. I am starting to think that a custom pulley with a running diameter a couple of % smaller might be a good way to go.
Note that a motor that runs at 1440 on 50Hz is going run somewhere around 1728rpm at 60Hz. (A 4 pole synchronous motor would run at 1800rpm) Actual shaft speed in an induction motor is also load dependent, and torque output is line voltage dependent.
I did some speed measurements on the motor, revision incl. bearings, no belt !
The speed from a 4 pole shaded motor is 1500 rpm minus slip at 50Hz and 1800 rpm 60 Hz minus slip.
tap 200-250 V 230 V- 50 Hz -1455 RPM slip 3%
tap 100-120 V 110 V-60hz 1755 RPM slip 3%
tap 125-150 V 110 V-60hz 1748 RPM slip 2,8 %
Volken
Hi Simone.
Thanks for joining this discussion.
For me the questions began when I noticed different values being reported as a nominal rpm for the E50.
Bung: 1350
Yourself: ~1440
And those, are for 50 hz operation. 60 hz must be greater by approx 17%.
The speed Bung mentioned is probably from a old motor without revision cold start !
I have measured this speed in this condition sometimes after an hour its closer to 1400 rpm.but still too low !
Hi Simone.
Thanks for joining this discussion.
For me the questions began when I noticed different values being reported as a nominal rpm for the E50.
Bung: 1350
Yourself: ~1440
And those, are for 50 hz operation. 60 hz must be greater by approx 17%.
The speed Bung mentioned is probably from a old motor without revision cold start !
I have measured this speed in this condition sometimes after an hour its closer to 1400 rpm.but still too low !
Can you confirm that these readings are from a motor completely unloaded, or if under full load while driving the platter?
there is the rpm loss due to normal slippage, even under no load.
Then the rpm loss due to eddy brake drag
and the rpm loss due to all drive train loads.
-Steve
Can you confirm that these readings are from a motor completely unloaded, or if under full load while driving the platter?
there is the rpm loss due to normal slippage, even under no load.
Then the rpm loss due to eddy brake drag
and the rpm loss due to all drive train loads.
-Steve
Steve I think we must use as reference the motor speed unloaded as I did !
The loaded speed depents from the state motor, voltage, frequence, and load as always with this kind off motor.
Volken
with a smaller pulley does not change the speed, the relationships are between the motor and the stepped pulley . the only way to reduce this speed and if you do not want to use a brake. building turntable pulley are sure of what I write. simone
with a smaller pulley does not change the speed, the relationships are between the motor and the stepped pulley . the only way to reduce this speed and if you do not want to use a brake. building turntable pulley are sure of what I write. simone
If when calculating motor speed by means of the rotating platter speed, by the method outlined back a few posts, the motor speed will not change with regard to the drive pulley diameters. But driven pulley speeds will change. I think that is what you are saying. I just want to clarify.
And for further clarification. motor rpm does change with mains frequency.
If 1455 rpm unloaded at 50hz it will be 1702 rpm at 60 hz. Unloaded.
For instance the 50 hz drive pulley is 1.428 inches dia. (36.27mm)
and the 60 hz drive pulley is 1.177 inches dia (29.9mm)
the motor speed works out the same so long as the formulas are worked correctly.
But we should also consider beyond the motor to the other drive train elements. The drive train load imposed on the motor is apparently very, very significant.
-Steve
your discussion is correct but if you change the size of the stepped pulley you change the speed. changing the step of 33 45 and 78 you'll change the speed. simone sorry for my english
your discussion is correct but if you change the size of the stepped pulley you change the speed. changing the step of 33 45 and 78 you'll change the speed. simone sorry for my english
understood and taken as a given.
But within the context of the formulas used to calculate pulley rpms.
Here's a copy / paste of my earlier post with the simple formulas for calculating pulley rpm.
Machinery's handbook offers some short formulas for determining pulley diameters and speeds (rpm).
Here's what we know for diameters.
item 1: 60 hz drive pulley diameter is 1.177 inches dia.
item 2: driven step idler dia at the belt interface is 2.755 inches dia.
item 3: the 33-1/3 rpm ring on the step pulley is .470 inches dia.
item 4: the idler driven platter at the inside rim is 9.682 inches dia.
known rpms: platter rpm is set to 33-1/3 rpm.
The rest needs to be calculated:
(a) to know the step pulley rpm:
9.682dia x 33.333/.470dia = 686.66rpm.
(b) to know motor shaft rpm:
2.755dia x 686.66rpm/1.177dia = 1607.26 rpm
And calc (b) does not consider the pitch diameters with regard to the belt that runs over both drive and driven pulley surfaces. So that final rpm figure is lesser than it would be.
The above was calculated using the 60hz motor pulley and the 33-1/3rd rpm step pulley dia to drive the platter. If you wanted to use the same formula to calculate motor rpm at 45 rpm platter speed you should still get the same motor speed so long as you insert the correct 45 rpm ring diameter on the step pulley and all other diameters are unchanged.
-Steve
Add to this the fact that the motors run a bit fast to start with and need to be loaded heavily by the eddy current brake in order to run on speed - usually resulting in much less than -3% below nominal due to maxing out the brake. Changing the pulley diameter slightly would require much less eddy current braking and might allow some of us to get the speed range centered with an adjustment range approaching +/-3%.
Currently I run my TD-124/II on 110V mains from a nominal of 117V. (It fluctuates slightly but is never far from this value.)
My TD-124/I runs off of 117V, needs motor mount upgrade and has the magnet pretty well maxed out.
By the way the cork damping I applied to the inside of the intermediate (stepped) pulley seems to be a keeper on both tables. Much less noise overall.
Should someone (hint, hint) decide to machine up a bunch of really good quality 60Hz pulleys just a few % smaller than the originals count me in for two.
Currently I run my TD-124/II on 110V mains from a nominal of 117V. (It fluctuates slightly but is never far from this value.)
My TD-124/I runs off of 117V, needs motor mount upgrade and has the magnet pretty well maxed out.
By the way the cork damping I applied to the inside of the intermediate (stepped) pulley seems to be a keeper on both tables. Much less noise overall.
Should someone (hint, hint) decide to machine up a bunch of really good quality 60Hz pulleys just a few % smaller than the originals count me in for two.
I just cleaned out my step pulley bushing, and noticed a lot of fibres stuck inside the bushing. Eventually I managed to pull out a small piece of green cloth! Someone at some stage tried to clean the bushing and this piece of cloth got stuck!
There are some markings on the inside of the bushing, Is it possible to polish the inside of the bushing without destroying its oil retaining properties?
Would autosol work, or are there any other better alternatives?
// Nils
There are some markings on the inside of the bushing, Is it possible to polish the inside of the bushing without destroying its oil retaining properties?
Would autosol work, or are there any other better alternatives?
// Nils
I just cleaned out my step pulley bushing, and noticed a lot of fibres stuck inside the bushing. Eventually I managed to pull out a small piece of green cloth! Someone at some stage tried to clean the bushing and this piece of cloth got stuck!
There are some markings on the inside of the bushing, Is it possible to polish the inside of the bushing without destroying its oil retaining properties?
Would autosol work, or are there any other better alternatives?
// Nils
That explains the noise you've been experiencing. And I had expected something along those lines.
With the "healthy step pulleys I've experienced the noise I've observed from the step pulley is more of a soft whirring when I have the un-assisted ear next to the operating TD124.
If it were over here, the first thing I'd do with this particular step idler pulley is to do what you've been doing; clean it of all loose and all stuck-on debris. Perhaps a soak in some grease dissolving solvent. Like lacquer thinner.
2nd thing: and having made certain that there is no more contaminating materials within that bearing, I would make a close visual examination of the upright shaft that the step pulley spins on. and I'd mic it to determine that the diameter in the unworn areas are the same as those areas of the shaft that takes the sleeve bushing. the materials are high quality.
3rd thing: step pulley bushing. The thing to do before any polishing, or the use of any type of abrasives inside the bushing is to measure it for wear. As with the shaft, the worn areas should not show a significant increase in size compared to the areas of the bushing ID that do not run against the shaft. A bore gage is needed for the bushing ID.
Always realize that when you polish a bearing surface you are removing material from that surface you polish. If you do this without first measuring the surface to be polished, you do so blindly. Without adequate knowledge. There is no putting material back in😱
No polishing of the step pulley bushing ID. If no gages there is a way to check the operating clearance between shaft and bushing Id. For the mechanic who doesn't own the gages. A clean dry assembly followed by a check for play at the interface between bushing Id and the shaft it runs on. Once fully assembled complete with thrust ball at the top.

But minus the grease.
Then pushing downward on the rim of the large diameter that engages the drive belt. If you can feel no evidence of play, that is good. If you can, that's not so good.
Next step is to remove the step pulley from the shaft, add lube to the interior of the bushing and to the thrust ball. Then check it for free spin. Does it seem to spin freely or is there something creating friction? never mind that the eddy brake, even when adjusted for least effect, will prevent the step pulley from long spin-down times.
-Steve
I just cleaned out my step pulley bushing, and noticed a lot of fibres stuck inside the bushing. Eventually I managed to pull out a small piece of green cloth! Someone at some stage tried to clean the bushing and this piece of cloth got stuck!
There are some markings on the inside of the bushing, Is it possible to polish the inside of the bushing without destroying its oil retaining properties?
Would autosol work, or are there any other better alternatives?
// Nils
There is felt inside as oil reservoir , if you clean the inside it is often broken !
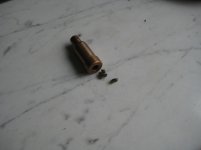
There is felt inside as oil reservoir , if you clean the inside it is often broken !
View attachment 411684
Right.
I just took the step pulley off of sn 7388. It has a groove in the bushing ID. About midway up. And with just the right light I can see a felt ring within that groove. It looks intact. Best to let sleeping dogs sleep. To remove it would destroy it.
I had forgotten about this. But now I recall seeing this before. With #2729 I chose to leave the felt ring in the groove because I had no way install another. Nor was there a known source of replacement felt rings for this part.
(sheepish grin😱)
-Steve
It may be that
Well, I got an original piece of felt for sale! 🙂
Attached photos of it. It looks to be in good shape, Although I am not sure I want to put it back, since I do not know how it was put there in the first Place.
[/url][/IMG]
[/url][/IMG]
I have cleaned the pulley bushing and also tried to flush the bushing with hot oil, but I do not think it worked out too well. I did not want to sink the whole pulley in hot oil, because it seems to be some lacquer on the pulley surface, which I do not want to ruin.
I then dried the bushing with lint free cloth, and tested it in a dry run. I took the magnet away to make it spin freely. Very good spin in the dry run, but there was clearly some grinding /ticking noice when putting my ear next to the pulley.
I then lubricated and tested, and with oil the pulley is quiet.
I am curently not sure what to do. Should I try to put the felt pad back? or should I just leave it alone, making sure the bushing gets a regular zip of oil? or should I go for a replacement bushing?
For the time being I think I will just put it together to check how it sounds and that the speed is alright.
//
Nils
Attached photos of it. It looks to be in good shape, Although I am not sure I want to put it back, since I do not know how it was put there in the first Place.
I have cleaned the pulley bushing and also tried to flush the bushing with hot oil, but I do not think it worked out too well. I did not want to sink the whole pulley in hot oil, because it seems to be some lacquer on the pulley surface, which I do not want to ruin.
I then dried the bushing with lint free cloth, and tested it in a dry run. I took the magnet away to make it spin freely. Very good spin in the dry run, but there was clearly some grinding /ticking noice when putting my ear next to the pulley.
I then lubricated and tested, and with oil the pulley is quiet.
I am curently not sure what to do. Should I try to put the felt pad back? or should I just leave it alone, making sure the bushing gets a regular zip of oil? or should I go for a replacement bushing?
For the time being I think I will just put it together to check how it sounds and that the speed is alright.
//
Nils
- Home
- Source & Line
- Analogue Source
- Restoring and Improving A Thorens TD-124 MKII