I think it pretty unlikely, the cork disk inserts weigh between 0.84gms and 0.91gms depending on the size, and the intermediate (stepped) pulley weighs over 49gms so the effect of a slightly off center placement should be negligible given the % of mass the cork contributes to the overall assembly. (2%) Something to note is that while the motor pulleys at least on later tables are dynamically balanced the intermediate pulleys either aren't at all or had a small quantity of thick enamel paint applied on the inside of lighter side of the pulley.
It worked extremely well on the MKII, and I will evaluate the MKI with another (later version) modified pulley this evening.
I have spare bearings in any event, and likely need to replace them in the MKI (wondering if the odd flutter I can now hear since the other noises are gone is in fact an indication that those bearings might be worn..)
I can't guarantee that this will work on all tables or that it won't potentially increase the wear on the upper bearing, so as always it is a matter of personal judgment, and the change is very easily fully reversible if you remove the cork within a few hours, and may be a bit more work if the adhesive bonds well to the metal. (It does over time)
I would recommend cleaning the inside of the pulley with alcohol before installing cork. Also make sure that you allow for the eddy brake components and bearing boss when you cut out the cork disk. Incidentally I used an old prescription pill bottle as the template for mine.
It worked extremely well on the MKII, and I will evaluate the MKI with another (later version) modified pulley this evening.
I have spare bearings in any event, and likely need to replace them in the MKI (wondering if the odd flutter I can now hear since the other noises are gone is in fact an indication that those bearings might be worn..)
I can't guarantee that this will work on all tables or that it won't potentially increase the wear on the upper bearing, so as always it is a matter of personal judgment, and the change is very easily fully reversible if you remove the cork within a few hours, and may be a bit more work if the adhesive bonds well to the metal. (It does over time)
I would recommend cleaning the inside of the pulley with alcohol before installing cork. Also make sure that you allow for the eddy brake components and bearing boss when you cut out the cork disk. Incidentally I used an old prescription pill bottle as the template for mine.
Great to hear that cork works well.🙂
I was actually thinking about making an mdf or delrin ring which would press fit on the inside on the step pulley. Cork is much easier to do, and also with the right addhesive also easy to remove. If Cork gives the desired effect, I will try it aswell!
In the meantime I have checked my step pulley. I had a grinding noise comming from it. I discovered that I had some small metal flakes sitting on the magnet (probably from my screwdriver). Since I had the magnet so close to the step pulley the metal flakes touched the pulley. After cleaning the magnet, the grinding has gone away.
Also I have adjusted the magnet according to Steve's advice, I bought a new belt, but that was very tight, so I put back the old belt. The turbulence noise has clearly been reduced, altough it is still present.
I made a closer examination of my pulley shaft, and I discovered that the bearing ball has made a small dent on the top of the shaft. I will try and pollish that away.
Since the step pulley is fairly light, I was thinking perhaps the bearing ball is not the best sollution? Is it possible that the bearing ball adds chatter into the pulley? Would a thrust pad made out of delrin be a better solution?
What are your thoughts?
//
Nils
I was actually thinking about making an mdf or delrin ring which would press fit on the inside on the step pulley. Cork is much easier to do, and also with the right addhesive also easy to remove. If Cork gives the desired effect, I will try it aswell!
In the meantime I have checked my step pulley. I had a grinding noise comming from it. I discovered that I had some small metal flakes sitting on the magnet (probably from my screwdriver). Since I had the magnet so close to the step pulley the metal flakes touched the pulley. After cleaning the magnet, the grinding has gone away.
Also I have adjusted the magnet according to Steve's advice, I bought a new belt, but that was very tight, so I put back the old belt. The turbulence noise has clearly been reduced, altough it is still present.
I made a closer examination of my pulley shaft, and I discovered that the bearing ball has made a small dent on the top of the shaft. I will try and pollish that away.
Since the step pulley is fairly light, I was thinking perhaps the bearing ball is not the best sollution? Is it possible that the bearing ball adds chatter into the pulley? Would a thrust pad made out of delrin be a better solution?
What are your thoughts?
//
Nils
Great to hear that cork works well.🙂
I was actually thinking about making an mdf or delrin ring which would press fit on the inside on the step pulley. Cork is much easier to do, and also with the right addhesive also easy to remove. If Cork gives the desired effect, I will try it aswell!
In the meantime I have checked my step pulley. I had a grinding noise comming from it. I discovered that I had some small metal flakes sitting on the magnet (probably from my screwdriver). Since I had the magnet so close to the step pulley the metal flakes touched the pulley. After cleaning the magnet, the grinding has gone away.
Also I have adjusted the magnet according to Steve's advice, I bought a new belt, but that was very tight, so I put back the old belt. The turbulence noise has clearly been reduced, altough it is still present.
I made a closer examination of my pulley shaft, and I discovered that the bearing ball has made a small dent on the top of the shaft. I will try and pollish that away.
Since the step pulley is fairly light, I was thinking perhaps the bearing ball is not the best sollution? Is it possible that the bearing ball adds chatter into the pulley? Would a thrust pad made out of delrin be a better solution?
What are your thoughts?
//
Nils
re: bearing ball and the "indention".
There should be a spherical shaped thrust point -- within and at the top of the stepped pulley bushing. It is there specifically to receive the bearing ball and provide a seat for the ball.
--When-- the indentation from the ball is showing at the top end of the hardened shaft. This would, I think, present evidence of abnormal wear. Perhaps lack of lube over an extended period of use. However, its presence should not, by itself, prevent the shaft from being used in the future. I'd be more concerned about indications of wear on both the bushing areas of the shaft and within the bushing itself.
-Steve
Last edited:
The indention is at the top end of the hardened shaft. I have no plans (yet) to pollish away the thrust point inside the bushing! 🙂
//
Nils
//
Nils
The indention is at the top end of the hardened shaft. I have no plans (yet) to pollish away the thrust point inside the bushing! 🙂
//
Nils
Right. And a more careful (this time) read indicated as much.😛
I'd think it is time to use an OD mic to measure the shaft for indications of wear. And nice small bore gage to do same with the bushing. Given the dimple at the top of the shaft, and noisy operation of the stepped pulley, Id definitely be suspicious of bushing wear on that item. That is until I had measured evidence to the contrary.
But the dimple at the top of the shaft is evidence of wear. And where there is some evidence of wear, it seems likely there will be more evidence to be found.
-Steve
Removed and replaced the intermediate (stepped) pulley on my older MKI table both with and without the cork, both pulleys were identical, and sans cork significantly noisier. The strange ticking noise was still there, pulled off the magnet - cleaned the magnet and the area where it is mounted in the chassis and lo and behold much quieter. While I was about it I also polished the pulley as I had it out of the machine.
No longer audible from a few feet away..
No longer audible from a few feet away..
Removed and replaced the intermediate (stepped) pulley on my older MKI table both with and without the cork, both pulleys were identical, and sans cork significantly noisier. The strange ticking noise was still there, pulled off the magnet - cleaned the magnet and the area where it is mounted in the chassis and lo and behold much quieter. While I was about it I also polished the pulley as I had it out of the machine.
No longer audible from a few feet away..
The old steppulley bearing gave a lot off noise so Schopper made a new one for it . You need a another special tool to replace it no hammer this time !
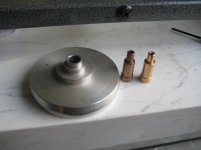
Looks like a significant improvement over the OEM part. My tables are all later and use two bearings in the chassis.
The older single bearing version in good running order seemed a bit quieter than the later design, but again no means of direct measurement available here.
The older single bearing version in good running order seemed a bit quieter than the later design, but again no means of direct measurement available here.
e50 windings, rewindings and motor rpm
It was NilsW who indicates that his "rewound" E50 runs at a higher rpm than does the original item. This would likely cause a higher reliance upon the eddy brake to prevent the motor from running too fast. Beyond its range.
We know that the Eddy brake was said by its mfr to have a 3% adjustment over platter rpm. But what is the "nominal" motor rpm for the E50?
In Bung's book "Swiss Precision" the author tells us this from page 30:
"A gently suspended four pole induction motor running at 1350 rpm transmitted its energy to a step pulley running at the speed of 700 rpm via a short flat belt.
Bung does not mention whether this reading was taken at 50 hz or 60 hz. But he's in Europe so I'd guess it was 50hz.
Simone Lucchetti's rewound motors are said to operate at 1435 rpm. But he's in Rome and one might be excused for guessing that he was working off of 50 hz mains. But....suptract 3% of that motor rpm and you still have 1392 rpm. And then there is that paragraph where Bung tells us that 1350 rpm is nominal.
By what percent does mains frequency determine motor rpm on one of these 4 pole induction motors? I've been thinking that it was a rather high percentage. In other words, Mains frequency would have a significant effect on motor rpm.
So that begs the question, do Simone's rewound motors run too fast?
Just questions hoping for a definitive answer.
-Steve
It was NilsW who indicates that his "rewound" E50 runs at a higher rpm than does the original item. This would likely cause a higher reliance upon the eddy brake to prevent the motor from running too fast. Beyond its range.
We know that the Eddy brake was said by its mfr to have a 3% adjustment over platter rpm. But what is the "nominal" motor rpm for the E50?
In Bung's book "Swiss Precision" the author tells us this from page 30:
"A gently suspended four pole induction motor running at 1350 rpm transmitted its energy to a step pulley running at the speed of 700 rpm via a short flat belt.
Bung does not mention whether this reading was taken at 50 hz or 60 hz. But he's in Europe so I'd guess it was 50hz.
Simone Lucchetti's rewound motors are said to operate at 1435 rpm. But he's in Rome and one might be excused for guessing that he was working off of 50 hz mains. But....suptract 3% of that motor rpm and you still have 1392 rpm. And then there is that paragraph where Bung tells us that 1350 rpm is nominal.
By what percent does mains frequency determine motor rpm on one of these 4 pole induction motors? I've been thinking that it was a rather high percentage. In other words, Mains frequency would have a significant effect on motor rpm.
So that begs the question, do Simone's rewound motors run too fast?
Just questions hoping for a definitive answer.
-Steve
It was NilsW who indicates that his "rewound" E50 runs at a higher rpm than does the original item. This would likely cause a higher reliance upon the eddy brake to prevent the motor from running too fast. Beyond its range.
We know that the Eddy brake was said by its mfr to have a 3% adjustment over platter rpm. But what is the "nominal" motor rpm for the E50?
In Bung's book "Swiss Precision" the author tells us this from page 30:
"A gently suspended four pole induction motor running at 1350 rpm transmitted its energy to a step pulley running at the speed of 700 rpm via a short flat belt.
Bung does not mention whether this reading was taken at 50 hz or 60 hz. But he's in Europe so I'd guess it was 50hz.
Simone Lucchetti's rewound motors are said to operate at 1435 rpm. But he's in Rome and one might be excused for guessing that he was working off of 50 hz mains. But....suptract 3% of that motor rpm and you still have 1392 rpm. And then there is that paragraph where Bung tells us that 1350 rpm is nominal.
By what percent does mains frequency determine motor rpm on one of these 4 pole induction motors? I've been thinking that it was a rather high percentage. In other words, Mains frequency would have a significant effect on motor rpm.
So that begs the question, do Simone's rewound motors run too fast?
Just questions hoping for a definitive answer.
-Steve
Steve, below is a portion of a message I got from Simon some time back. I realize some of it is redundant.
"about temp. usually a good motor has a temp near 45 47 °. but is not importante the temp. important is a delta speed. a good motor start to 1435 rpm and in 5 10 minutes go to 1440 1442 rpm. a bad motor start to 1410. sorry for my english. regards simone lucchetti"
Steve, below is a portion of a message I got from Simon some time back. I realize some of it is redundant.
"about temp. usually a good motor has a temp near 45 47 °. but is not importante the temp. important is a delta speed. a good motor start to 1435 rpm and in 5 10 minutes go to 1440 1442 rpm. a bad motor start to 1410. sorry for my english. regards simone lucchetti"
Right....and we have another source that says rpm should be a nominal 1350 rpm. That is why I made the post. I see a discrepancy. So my question should be is there a way, based on the motor build specs, to calculate a nominal rpm. You know. I'm looking for proof.
-Steve
Right....and we have another source that says rpm should be a nominal 1350 rpm. That is why I made the post. I see a discrepancy. So my question should be is there a way, based on the motor build specs, to calculate a nominal rpm. You know. I'm looking for proof.
-Steve
I understand. Before I tear into my own motor, I'd like to know as well.
I don't recollect the exact ratios, but the motor speed is primarily determined by line frequency, but load and line voltage also play a pretty significant role as well.
I would agree that an unloaded motor that runs faster will require more eddy current braking. I am starting to think that a custom pulley with a running diameter a couple of % smaller might be a good way to go.
Note that a motor that runs at 1440 on 50Hz is going run somewhere around 1728rpm at 60Hz. (A 4 pole synchronous motor would run at 1800rpm) Actual shaft speed in an induction motor is also load dependent, and torque output is line voltage dependent.
I would agree that an unloaded motor that runs faster will require more eddy current braking. I am starting to think that a custom pulley with a running diameter a couple of % smaller might be a good way to go.
Note that a motor that runs at 1440 on 50Hz is going run somewhere around 1728rpm at 60Hz. (A 4 pole synchronous motor would run at 1800rpm) Actual shaft speed in an induction motor is also load dependent, and torque output is line voltage dependent.
if the goal is to calc motor rpm...
...when you know all of the drive and driven diameters.
Machinery's handbook offers some short formulas for determining pulley diameters and speeds (rpm).
Here's what we know for diameters.
item 1: 60 hz drive pulley diameter is 1.177 inches dia.
item 2: driven step idler dia at the belt interface is 2.755 inches dia.
item 3: the 33-1/3 rpm ring on the step pulley is .470 inches dia.
item 4: the idler driven platter at the inside rim is 9.682 inches dia.
known rpms: platter rpm is set to 33-1/3 rpm.
The rest needs to be calculated:
(a) to know the step pulley rpm:
9.682dia x 33.333/.470dia = 686.66rpm.
(b) to know motor shaft rpm:
2.755dia x 686.66rpm/1.177dia = 1607.26 rpm
And calc (b) does not consider the pitch diameters with regard to the belt that runs over both drive and driven pulley surfaces. So that final rpm figure is lesser than it would be.
The resulting rpm at the step pulley seems to agree with Bung's reference of 700 rpm. Or it is relatively close.
But the calculated rpm at the motor pulley doesn't jive with either figures quoted by Bung or Lucchetti.
I'm obviously missing something. But we haven't taken into account the behavior of this shaded pole induction motor. for instance load has a significant effect on final rpm. Higher load = lower rpm.
This type of motor does slip somewhat at each magnetic pole. This is probably why it was chosen in the first place. More slippage means lower cogging effect. And this is a 4-pole motor.
that's probably the part I won't know how to calc for. Unless we can come up with a cheat sheet from a motor mfr.
-Steve
...when you know all of the drive and driven diameters.
Machinery's handbook offers some short formulas for determining pulley diameters and speeds (rpm).
Here's what we know for diameters.
item 1: 60 hz drive pulley diameter is 1.177 inches dia.
item 2: driven step idler dia at the belt interface is 2.755 inches dia.
item 3: the 33-1/3 rpm ring on the step pulley is .470 inches dia.
item 4: the idler driven platter at the inside rim is 9.682 inches dia.
known rpms: platter rpm is set to 33-1/3 rpm.
The rest needs to be calculated:
(a) to know the step pulley rpm:
9.682dia x 33.333/.470dia = 686.66rpm.
(b) to know motor shaft rpm:
2.755dia x 686.66rpm/1.177dia = 1607.26 rpm
And calc (b) does not consider the pitch diameters with regard to the belt that runs over both drive and driven pulley surfaces. So that final rpm figure is lesser than it would be.
The resulting rpm at the step pulley seems to agree with Bung's reference of 700 rpm. Or it is relatively close.
But the calculated rpm at the motor pulley doesn't jive with either figures quoted by Bung or Lucchetti.
I'm obviously missing something. But we haven't taken into account the behavior of this shaded pole induction motor. for instance load has a significant effect on final rpm. Higher load = lower rpm.
This type of motor does slip somewhat at each magnetic pole. This is probably why it was chosen in the first place. More slippage means lower cogging effect. And this is a 4-pole motor.
that's probably the part I won't know how to calc for. Unless we can come up with a cheat sheet from a motor mfr.
-Steve
Last edited:
......I don't recollect the exact ratios, but the motor speed is primarily determined by line frequency........
All induction motors have a rotational speed related to the power line frequency.
Considering that mains line frequency is not exactly 50 or 60 Hz , it's possible to make a simple sine wave power source with an accurate inbuilt 50 or 60 Hz source. This power would be cleaner and more accurate than the mains frequency . One could also lock it to a crystal, making the design more complicated. Most motors consume very little power. Maybe around 15 watts. Could use a small transformer and a chip power amp to implement the power stage !
I am still working on my step pulley. Hopefully I can put it together tonight and test how the new windings work when the eddy current is set up more correctly. I had the magnet too close to the pulley before.
Hopefully I can give you input on how it operates in European 50hz condition.
//Nils
Hopefully I can give you input on how it operates in European 50hz condition.
//Nils
I don't recollect the exact ratios, but the motor speed is primarily determined by line frequency, but load and line voltage also play a pretty significant role as well.
I would agree that an unloaded motor that runs faster will require more eddy current braking. I am starting to think that a custom pulley with a running diameter a couple of % smaller might be a good way to go.
Note that a motor that runs at 1440 on 50Hz is going run somewhere around 1728rpm at 60Hz. (A 4 pole synchronous motor would run at 1800rpm) Actual shaft speed in an induction motor is also load dependent, and torque output is line voltage dependent.
I will do some speed measurements with 60 Hz and 110 Volt with my CPS powersupply.
Volken
Unless we can come up with a cheat sheet from a motor mfr.
-Steve[/QUOTE]
Steve thats a problem there is very little information about this motor , Lately I have found some more info about the Papst motor but not the one that was used in the 124 !
-Steve[/QUOTE]
Steve thats a problem there is very little information about this motor , Lately I have found some more info about the Papst motor but not the one that was used in the 124 !
I realize that the motor windings are identical to the original. as the number of turns section. I disassembled my life over 1000 124 and the correct speed of an engine is perfect and clean in 1445. in theory could reach 1500 rpm. but being an induction motor does not reach the maximum speed. you can not change the number of engine revolutions, but only the torque. most section of the wire increases, and increases the torque increases more and more the engine reaches the correct speed. In fact, the structure of the 124 compared to mk1 mk2 is indentical. changes only the section of copper wire. 124 mk1 used in 2 sections of wire .. the mk2 model used a section of the same. 1350 rpm is a wrong speed. best regards simone lucchetti audiosilente
- Home
- Source & Line
- Analogue Source
- Restoring and Improving A Thorens TD-124 MKII