I was once thinking of a spider inside the voicecoil former and fixed on the center pole. It wont allow for huge xmax and will be troublesome for small diameter voice coils. But there wont be any sound radiating spider on the back of the cone and mass will be light.
Didnt pursue it tho...
Didnt pursue it tho...
Hi RayCtech,
I did already make two models with magnetic centering like you mention (two directions winding) but... radial centering with ferrofluid. I found out this is not a good way, to much damping (was unable to apply the point of critical damping). Overdamped resulted in a not open stereofield, missed some "sparkle" in the music. Thinking of a solution for magnetic centering (axial and radial). But didn't found a (good) solution yet. The axial centering works very well so this is a good basis to go for (very lineair). Some help for the radial centering would be very much appreciated. If you have questions about my design please ask.
Cheers,
The minimalistic spider design are the only alternative to magnetic oil with my current mechanical design. And this will be evaluated as soon as I get time.
A redesign and building of new motor assemblies to incorporate a new non magnetic centering method are not anything I have time to do in the near future.
Some updates
I did try a cloth surrounding. It was one that I removed from a unit, it was softened by adding some de solvent to remove all glues and resin. After removing the access glue the weight was 2,6 g, but it was still to stiff resulting in a to high resonances frequency...The foam surroundings was way better.
When using cones that are as light a 1,6 g I need a surroundings with a very high compliance, and this lead me to try leather. I got a small piece to play with, it had to bee joint due to the small size but it turned out OK. As you can see it is totally durable, one thing tow It increases in size when it is socked in water....So it is actually big big now. 😱
Take care
I did try a cloth surrounding. It was one that I removed from a unit, it was softened by adding some de solvent to remove all glues and resin. After removing the access glue the weight was 2,6 g, but it was still to stiff resulting in a to high resonances frequency...The foam surroundings was way better.
When using cones that are as light a 1,6 g I need a surroundings with a very high compliance, and this lead me to try leather. I got a small piece to play with, it had to bee joint due to the small size but it turned out OK. As you can see it is totally durable, one thing tow It increases in size when it is socked in water....So it is actually big big now. 😱
Take care
Attachments
That's a very impressive looking job you've done there.
Indeed it sure is impressive.
Good to see.
Magura 🙂
After making a full circle from two sheets of leather, I let it sock in water for about 30 min. For moulding the shape I used some nice big 8” spiders (as you can see in the picture), I put the leather in between the two spiders and added pressure and let it sit for 3-4 hours.
The leather I used was from a lam, and is about 0,5 mm thick. Hope this is the info you are looking for, other vice please free to ask.
Take care
The leather I used was from a lam, and is about 0,5 mm thick. Hope this is the info you are looking for, other vice please free to ask.
Take care
Hi RayCtech,
I did already make two models with magnetic centering like you mention (two directions winding) but... radial centering with ferrofluid. I found out this is not a good way, to much damping (was unable to apply the point of critical damping). Overdamped resulted in a not open stereofield, missed some "sparkle" in the music. Thinking of a solution for magnetic centering (axial and radial). But didn't found a (good) solution yet. The axial centering works very well so this is a good basis to go for (very lineair). Some help for the radial centering would be very much appreciated. If you have questions about my design please ask.
Cheers,
Did you feed your centring coil from a constance current source, I think that is what you should do.
If you remember I thought if you use a voice coil former as a shorting ring, it would work. But in fact it turned out to have some funny effects.
If you feed your coils with a normal power supply, then the coil will see it's self as shorted. But if you use a constance current source, it will see it's self as a open loop.
Just some thoughts any way.
Did you feed your centring coil from a constance current source, I think that is what you should do.
If you remember I thought if you use a voice coil former as a shorting ring, it would work. But in fact it turned out to have some funny effects.
If you feed your coils with a normal power supply, then the coil will see it's self as shorted. But if you use a constance current source, it will see it's self as a open loop.
Just some thoughts any way.
Indeed I feed it with a stabilized current source till 20-22Khz with a LM317 chip. This wil stabilize the eddy currents in the former wich will neutralize the effects of it.
For the radial centering going to try this one (fixed distance but no counterforce when moving, except mass offcourse), don't know if this will work:
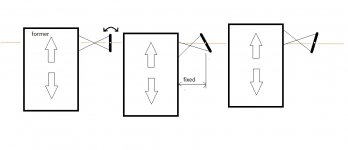
Tomorrow going to get my first lathe so this will hopefully speedup things 😉
cheers,
Last edited:
My idea of a spider has always been in the line of something like the below. Ofcourse each spoke can be made to provide a better flexibility and can be made with the desired progression.
Im planning to 3D print a couple of these (various spoke number and progressions) to see how it goes. Material used is PLA plastic.
Im planning to 3D print a couple of these (various spoke number and progressions) to see how it goes. Material used is PLA plastic.
Attachments
You may find that it is difficult to get the accuracy you want due to the support material that will be built into the design. Take care during the support addition stage and you should be OK.My idea of a spider has always been in the line of something like the below. Ofcourse each spoke can be made to provide a better flexibility and can be made with the desired progression.
Im planning to 3D print a couple of these (various spoke number and progressions) to see how it goes. Material used is PLA plastic.
EDIT: You should remove those sharp contours. They are stress risers.
Perhaps an ideal solution is to use a helical double-start or triple-start machined spring as a spider replacement. They can be designed for low spring rate in the axial direction, which is nice for getting your desired Fs. At the same time, they can also have high spring rate in the radial direction, which is great for centering. Finally, they have no stiction which is a problem in slide-type assemblies (e.g. Adire Audio Parthenon).You may find that it is difficult to get the accuracy you want due to the support material that will be built into the design. Take care during the support addition stage and you should be OK.
EDIT: You should remove those sharp contours. They are stress risers.
Nice spider.... but I'm sure it is hard to make, if you make it of plastic I think it will break over time.
I like the fact that the areal is small this will produce less sound and interfere less with the sound that the is cone making. I am still confused to what kind of spider I will be using, I need a very soft one due to the low cone mass.
Here is a picture of my new wizzer, the weight is a bit under 100 micro grams, in fact I can't measure it on my scale sense the resolution is 0,1 gram.
Take care
I like the fact that the areal is small this will produce less sound and interfere less with the sound that the is cone making. I am still confused to what kind of spider I will be using, I need a very soft one due to the low cone mass.
Here is a picture of my new wizzer, the weight is a bit under 100 micro grams, in fact I can't measure it on my scale sense the resolution is 0,1 gram.
Take care
Attachments
Interesting idea Jef, please let us know how it turns out.
Tried the solution but find out the fixed distance isn't fixed. It is the same as a normal needle just in the middle of it. In one direction it is possible to compensate a little as the rotating point is not in the middle, but shift upwards.
Back to ferrofluid with high viscosity 🙁
Spider
do not forget that one of the worst problem with small driver's spider may be ressonances
and especially when attached to such superlight assembly with close to no mass, and unable to absorb any
do not forget that one of the worst problem with small driver's spider may be ressonances
and especially when attached to such superlight assembly with close to no mass, and unable to absorb any
Last edited:
Spider
do not forget that one of the worst problem with small driver's spider may be ressonances
and especially when attached to such superlight assembly with close to no mass, and unable to absorb any
i'm now in the 'training process' where i want to learn to modify cheap Monacor SP-205/8 - adding a leather surround and making a new spider, based on this (i wanted to use bend guitar strings) http://i307.photobucket.com/albums/nn281/AudioVoice/IMGP0011.jpg
is this the case of possible resonances you mentioned ?
thanks
- Home
- Loudspeakers
- Multi-Way
- Project Ryu - DIY Field Coil Loudspeaker