Hi Hans,
That really is excellent work you have done there; I think we are pretty much there with both 2 and 3 phase solutions to the issue of powering our turntables to the best of their capabilities.
I think the only thing that needs to be done is to find the optimum signal generator, and there appear to be a few choices, both analog and digital, all at low cost.
I know the commercial suppliers have to make a profit, but with a few people brainstorming on this forum the solution looks like the whole thing shouldn't cost more than around $100~$150 to make.
Once again, many thanks.
Ralph
That really is excellent work you have done there; I think we are pretty much there with both 2 and 3 phase solutions to the issue of powering our turntables to the best of their capabilities.
I think the only thing that needs to be done is to find the optimum signal generator, and there appear to be a few choices, both analog and digital, all at low cost.
I know the commercial suppliers have to make a profit, but with a few people brainstorming on this forum the solution looks like the whole thing shouldn't cost more than around $100~$150 to make.
Once again, many thanks.
Ralph
Hi Hans
Great work!!! Been getting my electronic books out to get a better understanding of sand components. It is fun to build and learn.
I have that 5mhz dds gen on the way found one in US for 30.00 should have this week. Maybe have to build trying both of the new generators on the way.
Have a question on the 1 splitter on post 151 vs the lasts ones. The first one requires a + 15 - power supply for the op amps and latest does not. Was there others reasons for the difference between the circuits. There was talk about easier speed change and phase angle adjustment but I am not sure what the latter circuits do.
I am not concerned about 45 rpm or having to buy a 13.00 + - 15 volt power supply so do you like the first or last versions for my needs???
Thanks again this is a thread that getting things built that work. OK the 3 phrase gen thing is to course for rpm adjustment but they said .1 and in reality about .4. Well it looks like the dds one is .01 that should put us on track.
Tom
Great work!!! Been getting my electronic books out to get a better understanding of sand components. It is fun to build and learn.
I have that 5mhz dds gen on the way found one in US for 30.00 should have this week. Maybe have to build trying both of the new generators on the way.
Have a question on the 1 splitter on post 151 vs the lasts ones. The first one requires a + 15 - power supply for the op amps and latest does not. Was there others reasons for the difference between the circuits. There was talk about easier speed change and phase angle adjustment but I am not sure what the latter circuits do.
I am not concerned about 45 rpm or having to buy a 13.00 + - 15 volt power supply so do you like the first or last versions for my needs???
Thanks again this is a thread that getting things built that work. OK the 3 phrase gen thing is to course for rpm adjustment but they said .1 and in reality about .4. Well it looks like the dds one is .01 that should put us on track.
Tom
I seems I missed a lot of conversations.. Please let me know in one sentence what's wrong with that one. Thank you.
Sent from my iPhone using Tapatalk
Sent from my iPhone using Tapatalk
Tom, looks like we have the back end together (amps transformers, and motor), and thanks to the good work of Hans, Ralph, Pyramid, and others, looks like we might have the signal generating end down as well. This isn't just a DIY alternative to expensive commercial equipment. In the case of the Papst motor, I don't know of any motor drive, commercial or not, capable of 3 phase VFD, that can handle a 30 watt motor.
In my case, I'm just interested in the 3 phase version. If I understand this correctly, I can build 2 splitters, one for 60hz, and another for 81hz, switch them to the power amp stages, with one generator feeding the splitters. Preferably, I'm thinking that I can build one splitter for 60hz, and switch in 2 parallel resistors for the 81hz frequency.
Like Tom, I don't care if I have to buy more than 1 dual op amp, or other power supplies. I'm just looking for the best solution. What ever it takes, I'll do it. I have a few details to work out, that will probably require a little clarification from those that are more knowledgeable, and will build, test, and report back.
When I have a little more time, (and a few less beers 🙂), I'll probably require a little more assistance. I have slightly different amps and transformers than Ralph, so when it comes to power supplies, and DC offset, I have a few questions.
Thanks again folks, this thread is just what I was looking for.
twystd
In my case, I'm just interested in the 3 phase version. If I understand this correctly, I can build 2 splitters, one for 60hz, and another for 81hz, switch them to the power amp stages, with one generator feeding the splitters. Preferably, I'm thinking that I can build one splitter for 60hz, and switch in 2 parallel resistors for the 81hz frequency.
Like Tom, I don't care if I have to buy more than 1 dual op amp, or other power supplies. I'm just looking for the best solution. What ever it takes, I'll do it. I have a few details to work out, that will probably require a little clarification from those that are more knowledgeable, and will build, test, and report back.
When I have a little more time, (and a few less beers 🙂), I'll probably require a little more assistance. I have slightly different amps and transformers than Ralph, so when it comes to power supplies, and DC offset, I have a few questions.
Thanks again folks, this thread is just what I was looking for.
twystd
A Different Signal Generator
Rather than have an active device generate the sinewave signal to drive your power supply, why not create it in software and play it through the amplification scheme of choice. You can create a single channel sinewave of choice (frequency) in Audacity, copy it to a second channel (and a third for three phase). You then offset the channels to achieve the phase difference of choice and write the result out to a standard format like .wav. I've played with two channels this way (stereo), but have not created a file in a multichannel format that, for example, a device like an Oppo 103/105 could play out at line level for three phase. A smartphone or the simplest digital player with a headphone output could drive two phase.
This lengthens your iteration time as you seek the correct exact frequency for your motor, but once you have the file in the correct frequency, amplitude, and format, you just push play to start your table. I haven't built the amplification side for this purpose, so there may be a few issues, but I think it's a alternative worth considering.
Skip
Rather than have an active device generate the sinewave signal to drive your power supply, why not create it in software and play it through the amplification scheme of choice. You can create a single channel sinewave of choice (frequency) in Audacity, copy it to a second channel (and a third for three phase). You then offset the channels to achieve the phase difference of choice and write the result out to a standard format like .wav. I've played with two channels this way (stereo), but have not created a file in a multichannel format that, for example, a device like an Oppo 103/105 could play out at line level for three phase. A smartphone or the simplest digital player with a headphone output could drive two phase.
This lengthens your iteration time as you seek the correct exact frequency for your motor, but once you have the file in the correct frequency, amplitude, and format, you just push play to start your table. I haven't built the amplification side for this purpose, so there may be a few issues, but I think it's a alternative worth considering.
Skip
Skip. although I don't have a complete grasp of the active solid state solution for generating a signal, I have even less understanding on how to implement a software based signal. In other words, I'm totally clueless.
twystd
twystd
You guys need to start putting these things on metal boxes at some point... they're a pollutant of your audio system.
I also have some experience using class D amps to power a TT motor. Worked out beautifully but the system sounded horrible when the class D was up.
Doubt if a metal box will be much help - it's also polluting the mains. Had a serious rethink of this concept and even gave up on digitally synthesized waveforms, convenience be damned.
Do we really want to make our vinyl rigs sound worse than digital?
I've already successfully explored the idea of using a stereo signal to generate the 3 phases using the circuit in post #167.
I used Adobe Audition to automatically create a file with a 90° offset in the right channel.
Because of the low frequency involved I only used an 11025kHz bit rate; a file 16h long took only around 400Mb. I then copied the file to an old mp3 player I had lying around.
I fed the signal from the player back into my sound card in order to check for any errors, there were none, and the noise level was more than 72dB down, though this will vary with the mp3 player used.
By using the repeat facility of the mp3 player the signal can be made continuous, though there may be a small delay at the repeat point; this will vary with the player and is the reason I used such a long file.
Obviously you can generate several files at different frequencies and store them on the mp3 player, and simply switch between them in order to change speed.
If you use Wav files instead of mp3 it may be possible to create an automatically repeating file, if this works smoothly you need only small samples, maybe as little as a minute or so.
I used Adobe Audition to automatically create a file with a 90° offset in the right channel.
Because of the low frequency involved I only used an 11025kHz bit rate; a file 16h long took only around 400Mb. I then copied the file to an old mp3 player I had lying around.
I fed the signal from the player back into my sound card in order to check for any errors, there were none, and the noise level was more than 72dB down, though this will vary with the mp3 player used.
By using the repeat facility of the mp3 player the signal can be made continuous, though there may be a small delay at the repeat point; this will vary with the player and is the reason I used such a long file.
Obviously you can generate several files at different frequencies and store them on the mp3 player, and simply switch between them in order to change speed.
If you use Wav files instead of mp3 it may be possible to create an automatically repeating file, if this works smoothly you need only small samples, maybe as little as a minute or so.
Analog_sa, I hear you on that. I plan on double shielding this motor drive, and the power lines to the TT. I also plan on locating it as far away from the analog equipment as possible. I'm also planning on shielding the motor on the TT as well. I know how noisy this drive can get, if it is within 10' of my shop radio, I have to turn off the radio.
My analog equipment is on a dedicated line, feeding an isolation transformer, which is feeding a balanced power supply, and grounded by a technical ground. My analog equipment is all home made, and has Buddha yin-yang filters on the signal grounds. My DAC is isolated from my computer audio server, and battery powered. I guess I'm on the lunatic fringe when it comes to such things. Your point is well taken.
twystd
My analog equipment is on a dedicated line, feeding an isolation transformer, which is feeding a balanced power supply, and grounded by a technical ground. My analog equipment is all home made, and has Buddha yin-yang filters on the signal grounds. My DAC is isolated from my computer audio server, and battery powered. I guess I'm on the lunatic fringe when it comes to such things. Your point is well taken.
twystd
It didn't let me go why I couldn't get Ralphs circuit working with a single supply, and all the sudden the light went on and I knew what I did wrong.
So here it is, the version with one RC combination for switching between 33 1/3 and 45 RPM.
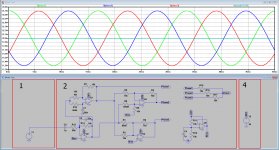
You see resp. 1) the Sinewave Generator, 2) the Phase Splitter and 3) the 24 Volt supply feeding both the Main Amps and the Phase splitter.
No additional external supplies needed!
What stroke me is the sensitivity for the accuracy of resistors R1 to R6 and R8. They should all be 0.1%.
Even going from 10k98 to 11k for R6 had a noticeable effect.
In the figure above I have magnified the "Check" signal a factor 10 to better show that all phases are correct.
Now you have two Phase Splitter versions to choose from:
One version with 3 Opamps and 2 RC combinations to select RPM. (posting #179)
A second version with 5 Opamps and 1 RC combination.
Both will work just as well, so it's up to you.
Hans
So here it is, the version with one RC combination for switching between 33 1/3 and 45 RPM.
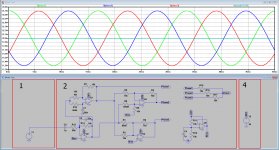
You see resp. 1) the Sinewave Generator, 2) the Phase Splitter and 3) the 24 Volt supply feeding both the Main Amps and the Phase splitter.
No additional external supplies needed!
What stroke me is the sensitivity for the accuracy of resistors R1 to R6 and R8. They should all be 0.1%.
Even going from 10k98 to 11k for R6 had a noticeable effect.
In the figure above I have magnified the "Check" signal a factor 10 to better show that all phases are correct.
Now you have two Phase Splitter versions to choose from:
One version with 3 Opamps and 2 RC combinations to select RPM. (posting #179)
A second version with 5 Opamps and 1 RC combination.
Both will work just as well, so it's up to you.
Hans
Check out also this thread:
http://www.diyaudio.com/forums/anal...ve-vs-sine-wave-oscillator-motor-control.html
http://www.diyaudio.com/forums/anal...ve-vs-sine-wave-oscillator-motor-control.html
Check out also this thread:
http://www.diyaudio.com/forums/anal...ve-vs-sine-wave-oscillator-motor-control.html
Nice to see that others are also "on the move" for quite some time.
Scanning quickly all postings, there where two things that I found interstingly, 1) that a rock stable frequency gives already a (significant) improvement over using the frequency of the mains supply.
2) that harmonic distortion of the sinewave seems to play a role also, unless it is below -60dB. This is of course a very subjective figure, but it could be a rationale behind VPI's ADS.
To reduce the HD from the generator, if necessary, is quite easy by using a low pass filter. But I have no idea what distortion is generated by the class D Main Amp that Ralph has suggested.
This will be somewhat harder to filter.
Ralph, do you have any means to measure the distortion of the sinewave before or even after the Trafo's and from the signal entering the Main Amp ?
Maybe some extra effort should still be invested in this part.
Hans
HI Hans, my breadboard version has been stripped for boxing, but I'll try to put a single phase back together to check out the distortion. It might take me a day or so but I'll see what I can do.
If you put a very small resistance between motor and amplifier you can measure the distortion of the load. With modern test gear it it could be a very small resistance. Whilst that's no reason not to try - 60 dB might be for the fun of it. I say this as if not someone will think - 80dB better. It is interesting to try squrewaves. They will not be a bad as thought as the load often is a filter.
Although I never tried it a friend said negative output impedance can get what this thread is hoping for. It was someones BSc project. Vibration control of motors using negative output impedance. Hope that says I don't discount the output impedance except to say ideally negative.
Although I never tried it a friend said negative output impedance can get what this thread is hoping for. It was someones BSc project. Vibration control of motors using negative output impedance. Hope that says I don't discount the output impedance except to say ideally negative.
- 60 db is fine. With many motors -40 dB would already be perfect. When feeding in a square-wave the 3 rd harmonic is at -9.54 dB ( - 19.08 triangle ). However the motor makes this look like - 22 dB at a good guess. Surprisingly an absoulutely pure sine wave is about the same, the motor corrupts it. If the voltage is set to have the same torque the difference is not large in vibration. However phase and voltage are a big difference. The problem with the very low output impedance of amplifiers is it stops you seeing the reality. However the low output impedance must help ( 3dB ? ). That's why I say use a very small resistance to measure the true working so as not to change the damping. With some motor types low vibration is not a question of doing a good job. Some have a limit of how low the vibration can be. The Linn Lingo made the mistake of going from an OK 90Vrms down to 66 Vrms. It sounded detailed yet thin. The torque is important.
It is possible to run the motor as a generator with a load similar to it's consumption. The more typical types show a crude sine wave. Also the ideal phase shift is shown. The current drawn when working is the same wave. I almost wonder if a triangle wave suits best. I had moments when it seemed so. I can't speak for all motor types. Just to say if time allows it is a worthwhile thing to try. I did find a pure sine wave useful and with no obvious reason not to use it. If running a triode valve at perhaps - 45 dB ( 1/3 rd ) with correctly ordered harmonics I could imagine the job is done ( a typical triode curve ). If the damping factor was >3 also job done.
On the Linn Valhalla I found the big problem was a beat frequency between mains frequency and crystal 50Hz ( 3.2768 MHz / 2^16 ). The mains ripple at - 41 dB. 220 uF ( 47 uF ) makes for - 54 dB and floating isolation transformer - 60 dB when together. Below that was impossible with that design. It is not subtle and worth doing. The actual Valhalla is about - 66 dB on various distortions. The power amp far better than it looks. The Linn motor shown is not the power supply which at - 66 dB is near perfect. It's what the motor uses.
It is possible to run the motor as a generator with a load similar to it's consumption. The more typical types show a crude sine wave. Also the ideal phase shift is shown. The current drawn when working is the same wave. I almost wonder if a triangle wave suits best. I had moments when it seemed so. I can't speak for all motor types. Just to say if time allows it is a worthwhile thing to try. I did find a pure sine wave useful and with no obvious reason not to use it. If running a triode valve at perhaps - 45 dB ( 1/3 rd ) with correctly ordered harmonics I could imagine the job is done ( a typical triode curve ). If the damping factor was >3 also job done.
On the Linn Valhalla I found the big problem was a beat frequency between mains frequency and crystal 50Hz ( 3.2768 MHz / 2^16 ). The mains ripple at - 41 dB. 220 uF ( 47 uF ) makes for - 54 dB and floating isolation transformer - 60 dB when together. Below that was impossible with that design. It is not subtle and worth doing. The actual Valhalla is about - 66 dB on various distortions. The power amp far better than it looks. The Linn motor shown is not the power supply which at - 66 dB is near perfect. It's what the motor uses.

The Garrard motor is about - 54 dB. It is a different type as were the early TD124 and also Lenco. The Garrard trades a bit of absolute speed stability for lower vibration. If voltage and frequency fixed the stability is near perfect after 15 minutes warm up ( drag in motor bearings ). I suspect synchronous types are too good at dealing with drag. It is possible a timed starting phase would be best, mostly to get the motor hot. A green light to say ready. A NE555 could do that. My guess is 3 minutes full power would be fine. Drag is mostly a good thing if the drive train is happy with it. Mr Verdier thought so.
On my graphs above damping factor was > 200. Note also ideal capacitance given for that motor. At 45 it changes. Note the change is not 1/1.35 as the inductance has a considerable resistance in series ( DCR of motor ). Apart from that for two phase motors it is very OK to use a capacitor. As said before as a generator will give exact phase shift. It should be 90 degrees, it might not be ( 88, 92 ? ).
On my graphs above damping factor was > 200. Note also ideal capacitance given for that motor. At 45 it changes. Note the change is not 1/1.35 as the inductance has a considerable resistance in series ( DCR of motor ). Apart from that for two phase motors it is very OK to use a capacitor. As said before as a generator will give exact phase shift. It should be 90 degrees, it might not be ( 88, 92 ? ).
To slightly correct something implied. The connection to the capacitor phase is looser. One can infer that two ampifiers is good for tight coupling alone. The vibration we see is the harmonics dictated by the motor and the workings of the magnetic circuit. I was surprised to see a 7.5 degree stepper quite good on AC. I suspect early ones were just rewinds of synchronous types. What might be true is the a large motor run at half intended voltage might be ideal. The Linn Airpax wasn't really big enough. As I also said not speaking for all types, just what to look for. It is not the voltage waveform. I always take distortion of source needs to be - 20 dB better than device.
Another way of seeing the current waveform is to put in a resistance high enough to show different voltage waveforms either end of the resistor. I dislike that idea unless wanting that resistor to be used. If shown as the same as the current waveform that is sub critical damping.
A speculation I find hard to resist is the current waveform exactly matches some motor magnetic circuits. Here is the very nice 11 watt Crouzet motor as used by the Avid turntable. I use them for another purpose. Note the triangular magnetic windows. Two identical coils and a crude build ( all that is required really ).
Another way of seeing the current waveform is to put in a resistance high enough to show different voltage waveforms either end of the resistor. I dislike that idea unless wanting that resistor to be used. If shown as the same as the current waveform that is sub critical damping.
A speculation I find hard to resist is the current waveform exactly matches some motor magnetic circuits. Here is the very nice 11 watt Crouzet motor as used by the Avid turntable. I use them for another purpose. Note the triangular magnetic windows. Two identical coils and a crude build ( all that is required really ).

- Home
- Source & Line
- Analogue Source
- Optimally driving a (VPI) synchronous turntable motor