Is tapped horn a must for you then?
You have a lot of other solution that will get you 40-150 Hz at 104-105 db.
Front loaded subs, ported horns ....
You have a lot of other solution that will get you 40-150 Hz at 104-105 db.
Front loaded subs, ported horns ....
Does your measurements go along with the hornresp simulations?
If yes than something else is wrong. TH115 is not far from that internally. So no hidden tricks inside the box that will get you better higher frequency response.
Please post a screen shot with the parameters you are using so i can compare them with mine.
If yes than something else is wrong. TH115 is not far from that internally. So no hidden tricks inside the box that will get you better higher frequency response.
Please post a screen shot with the parameters you are using so i can compare them with mine.
I have just noticed one strange thing. If you simulate a driver in a scoop box with a back chamber of just 5 liters and with a horn of around 280cm you are getting almost the same results as when you try to simulate as a tapped horn.
I somehow doubt that hornresp can realistically simulate a TH.
TH115 has 4 bents and in the hornresp you are entering a data for just 3. If you take bent 2 and 3 as one section and enter the data for the length and mouth area for the end of the bent 3, results are why out.
I somehow doubt that hornresp can realistically simulate a TH.
TH115 has 4 bents and in the hornresp you are entering a data for just 3. If you take bent 2 and 3 as one section and enter the data for the length and mouth area for the end of the bent 3, results are why out.
MarjanM said:Is tapped horn a must for you then?
You have a lot of other solution that will get you 40-150 Hz at 104-105 db.
Front loaded subs, ported horns ....
They may be.
The problem is really this. Sorry it's long but clear.
Keep in mind I'm somewhere between a weekend warrior and a Pro, Not quite either but I was getting high profile work before I switched to BFM tops.
If you run 4 double 18 boxes you are running two ohms on your amp. To be safe you simply use a second amp. The problem with that is in the types of work I get. I often can only run one amp rack with the power available so I get stuck with only two double driver subs. Since I repair amps I know how far I can push 2.6 ohms or 3 drivers on one 1/2 of an amp so I used to carry a set of single 18's as well. At 2.6 ohms properly running I have never had an amp failure vs other small and large companies running 2 ohms all the time with constant amp failures.
Unfortunately when I helped sell the Apogee 3x3's there were no subs to go with them so I had to let mine go at below driver value. To make matters worse some moron blew up one of the single 18's when I was not around. so No subs.
I figured I'd try the Titan, wasn't crazy about it. I realized I was pushing 40 on my double 18's and the titan wasn't even close so I tried a quick tapped horn from here and got hooked.
Since then I've been at it constantly trying to get one to work as close as possible to a double 18 in a truly portable size.
Theoretically a pair of them should exceed a double 18 by a mile.
The model is to run primary mains off one amp rack with 4 subs (Six if it looks like a loud show) off a switchmode amp, 6 horn loaded tops (line array) off 2 conventional crests.
A second rack gets used outdoors to run 4 more horn loaded tops
adding to the line array.
The monitor rack consists of Stewart switchmode amps so it sips power to run up to 4 mixes.
This is the way I was getting work because many people did not want big boys tearing up thier breaker boxes to get power.
It also got me a lot of sub contract gigs as the bigger companies didn't want to deal with the hassles. Of course now those of us down here are competing with them directly as they are taking gigs at a loss if necessary.
I built a rig with almost no money available, despite high child support and low income , out of junk, made a name for myself.
had it paying for it's own upgrades, then screwed up by trying to improve it. Fortunately the support ended last year but I still am trying to do this with under 16k salary.
I tried renting Yorkies for my upcoming show but no one in town has them. Apparently even the big companies here don't know who Tom Danley is and never heard of a tapped horn. I have a reputation for trying innovative stuff so they'll be watching to see what I end up using. The tappeds would give me the edge to keep working gigs despite the overwhelming competition.
Sigh... if I only had credit...... I'd simply buy em instead of practically putting myself in the morgue trying to build em.
I have not posted designs other than pics simply because none of them have come close enough to what is needed for others as well.
I didn't mean for this to be so long.....Long?..... There's a guy I met way too late to learn from. I really wish I'd met him sooner.
One other thing I have not revealed to anyone untill now.
The ultimate goal is to take on the Jagermiester truck with a smaller all horn loaded system when I can afford to.
Seems there is a lot of work for a loaded mobile stage truck but it's got to be a good system. It also makes a great showcase rig for equipment.
The ultimate goal is to take on the Jagermiester truck with a smaller all horn loaded system when I can afford to.
Seems there is a lot of work for a loaded mobile stage truck but it's got to be a good system. It also makes a great showcase rig for equipment.
As i understand you will be using them in a not smaller number than 4 in a block right?
Will something like this be ok for your need?
Will something like this be ok for your need?
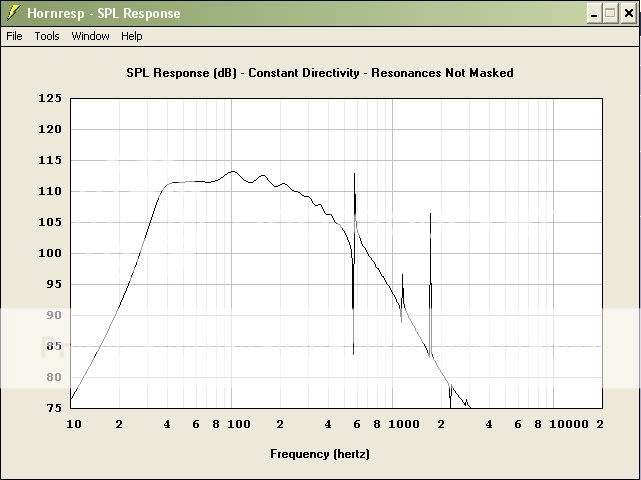
Most shows a block of two per side for a total of 4,
outdoors 3 per side for a total of 6, center clustered whenever possible. Half the time the client won't let you center them because the big boys dont around here. Religious type gigs are another matter.
That looks like a folded horn or maybe 4 of them?
I have 4015's 3015's and JBL 2225H's and some gauss, all 15" and all in sets of 4. Buying 18's is not possible and I'm tired of them.
outdoors 3 per side for a total of 6, center clustered whenever possible. Half the time the client won't let you center them because the big boys dont around here. Religious type gigs are another matter.
That looks like a folded horn or maybe 4 of them?
I have 4015's 3015's and JBL 2225H's and some gauss, all 15" and all in sets of 4. Buying 18's is not possible and I'm tired of them.
Not too big .
Around 450 lit.
Try to simulate your driver.
S1 500
S2 4200
L12 250
VRC 60
VTC 30000
Around 450 lit.
Try to simulate your driver.
S1 500
S2 4200
L12 250
VRC 60
VTC 30000
MarjanM
That is the exact same thing I asked and posted with using the 1850 Horn specs. A BPH seems like the way to go but I can't get it right in HR.
screamersusa
It seems we will have to learn AkAbak. In the DTS 20 there is a helmholtz resonator. Seemingly tuned to the upper freq. The portion that is in the driver cavity is capped while the other end ports into the horn before the mouth. Makes me wonder if the other's have this is some form.
That is the exact same thing I asked and posted with using the 1850 Horn specs. A BPH seems like the way to go but I can't get it right in HR.
screamersusa
It seems we will have to learn AkAbak. In the DTS 20 there is a helmholtz resonator. Seemingly tuned to the upper freq. The portion that is in the driver cavity is capped while the other end ports into the horn before the mouth. Makes me wonder if the other's have this is some form.
Somewhere in the main TH thread are some posts about the resonators in the DTS20. Someone also made akabak scripts to simulate them. But it will need trial and error to implement these in a real TH, because the correlation between the damping in the real tube and the damping variable in the script isnt clear. There seem to be four resonators in the DTS20, two of different length pointing upwards from the driver and two pointing downwards. The open end of all of them is next to the front side of the membrane at the beginning of the horn.
screamersusa, since it seems you need high spl in little package, the best thing i have found (only in theory, never tried it) for this requirement, is to keep the horn mouth small in comparison to driver membrane area. If you have a mouth size of 1x-2x the membrane area, you seem to get the most spl out of the same box volume. You still need a certain amount of mouth size to get a flat response, so you need multiple horns. Toms designs seem to favour a mouth size of around 2x membrane area.
next best thing is to use drivers with a strong motor and sturdy membrane, which can handle a high compression factor. this leads to the use of small drivers, like 12inch, because their membrane is usually more compact, having a higher mass per area and thickness per diameter ratio than membranes of bigger drivers.
If reality is at least somewhat related to simulations, this should lead to a high spl system in a small package. Downside is, that you need alot of drivers, compared to other designs.
next best thing is to use drivers with a strong motor and sturdy membrane, which can handle a high compression factor. this leads to the use of small drivers, like 12inch, because their membrane is usually more compact, having a higher mass per area and thickness per diameter ratio than membranes of bigger drivers.
If reality is at least somewhat related to simulations, this should lead to a high spl system in a small package. Downside is, that you need alot of drivers, compared to other designs.
Smaller mouth size does seem to help low end in the sim, but it also cuts the upper end. Seems to hold true in my physical testing.
I tried those folded horn numbers and came up with a box too big to carry 4 in the trailer all the time. I also tweaked the babhorn a little to get the response I wanted, but it got too big as well.
I suspect that the resonators in a DTS20 are necessary given the boxes length and shape. The lining on the walls I saw in the pic make sense as well. Aside from dampening cabinet vibration, I suspect both of these treatments cut down on nasty resonances in the box. I did try lining one parallel side of a LSTH (live sound th), and it did make the box sound very pleasing for home hi-fi use but at a cost in level.
Back to making sawdust..
I tried those folded horn numbers and came up with a box too big to carry 4 in the trailer all the time. I also tweaked the babhorn a little to get the response I wanted, but it got too big as well.
I suspect that the resonators in a DTS20 are necessary given the boxes length and shape. The lining on the walls I saw in the pic make sense as well. Aside from dampening cabinet vibration, I suspect both of these treatments cut down on nasty resonances in the box. I did try lining one parallel side of a LSTH (live sound th), and it did make the box sound very pleasing for home hi-fi use but at a cost in level.


The mouth of the TH115 looks to be about 21"x21", the overall cabinet being 22.5" and constructed of 3/4" stock.
http://www.danleysoundlabs.com/pdf/TH 115 Spec Sheet.PDF
The woofer used has an Sd of about 850cm, the mouth roughly 2840cm, for a ratio of about 3.34x, not 1x or 2x.
http://www.danleysoundlabs.com/pdf/TH 115 Spec Sheet.PDF
The woofer used has an Sd of about 850cm, the mouth roughly 2840cm, for a ratio of about 3.34x, not 1x or 2x.
MaVo said:I didnt know this thread was about cloning the TH115. My apologies.
I didn't think so either -- but the TH-115 is a very good target for a live sound application, nobody seems to have been able to even equal its performance according to Hornresp (I've got within about 1dB) never mind exceed it.
And now Tom says he's got a new box (36"x36"x16") using 2 12" drivers coming soon which has even better performance... 🙂
Ian
It's not about cloning the TH115 because you can't.
I suspect that even with a specimen cabinet and a big saw, you'd have a hard time building one at home. That wouldn't be very respectable anyway.
It's about coming up with an acceptable DIY substitute for those of us who can't afford them or can't warrant the budget. Such as
someone who DJ's for friends or has a small bar band. It also serves as a means for small guys like me who only get to buy clothes and fix the car after a few sound gigs (despite a full time job) the ability to compete for work to eventually fund a true set of Danley Sound Labs built cabinets. In addition a bunch of well functioning DIY boxes running around in low budget land will spark interest and demand in the upper market where people can and will buy the real product.
A lesson learned.
Sony did something similar to Ampex when they gave Viacom (MTV) a ton of D2 Vtrs. Ampex had rejected the D2 because it was too problematic and the mechanics ate tape and were very hard to maintain. Sony bought the technology and it became SONY's equivalent to the 386 computer. They gave them away to Major networks to force all the small post-houses to buy them. This put Ampex at a disadvantage. When they released thier digital deck which was a typically AMAZING bulletproof Ampex product, we had all spent our money on the D2 and the networks made us use the D2.
After the small houses bought them, they gave away the Digital Betacam which was much better...before the loans were paid off.
So we had to refinance yet again.
The point bieng... getting the concept out there wowing people will help DSL and Yorkville sell boxes.
Case in point:
After a year with my first DIY system, the small companies around here cloned it using store bought boxes and some even
bought the EAW cabinets I based my tops on. Remember, I refused to build them for people.
After I did a few shows with my BFMot12 modified quasi line array, some of the small guys with deep pockets around here scrambled to buy the Jbl and Qsc mini line arrays. In addition I sent a buch of weekend warriors over to the BFM site.
Now the TH. No one here appears to have heard of them.
I've already turned two church sound contractors on to the Danley stuff and my primary staduim capable ally is very interested in hearing some and encouraging me to come back into the circuit.
Personally If I am successfull, I will maintain the same additude I always have with regard to questions about my boxes at shows.
Q "Are those Meyers?" A "NO" (Passive meyer type boxes)
Q "Are those EAW's? A "No, the EAW's are better"
Q "Can you build some for me" ( $$$ in my face) "No I don't build boxes for sale, go buy the originals, you be happier with them."
My rule... You NEVER badge a DIY box, even a direct clone with another manufacturers name, and you NEVER say you have the genuine article when you don't ,nor try to sell yourself with the Genuinine article and show up with clones. That said, I have seen big companies with a mix of originals and clones all badged!!! When you look at the back of the cabinet, while you are setting up , you see the difference. Tapping the wood reveals them as well.
I personally dont want to "Clone the TH115" as that would hurt the species. Even with the plans in my hand, giftwrapped from Tom personally...I wouldn't build em or call them Danleys.
By the way.. has anybody noticed the USC-1 prices dropping?
I suspect that even with a specimen cabinet and a big saw, you'd have a hard time building one at home. That wouldn't be very respectable anyway.
It's about coming up with an acceptable DIY substitute for those of us who can't afford them or can't warrant the budget. Such as
someone who DJ's for friends or has a small bar band. It also serves as a means for small guys like me who only get to buy clothes and fix the car after a few sound gigs (despite a full time job) the ability to compete for work to eventually fund a true set of Danley Sound Labs built cabinets. In addition a bunch of well functioning DIY boxes running around in low budget land will spark interest and demand in the upper market where people can and will buy the real product.
A lesson learned.
Sony did something similar to Ampex when they gave Viacom (MTV) a ton of D2 Vtrs. Ampex had rejected the D2 because it was too problematic and the mechanics ate tape and were very hard to maintain. Sony bought the technology and it became SONY's equivalent to the 386 computer. They gave them away to Major networks to force all the small post-houses to buy them. This put Ampex at a disadvantage. When they released thier digital deck which was a typically AMAZING bulletproof Ampex product, we had all spent our money on the D2 and the networks made us use the D2.
After the small houses bought them, they gave away the Digital Betacam which was much better...before the loans were paid off.
So we had to refinance yet again.
The point bieng... getting the concept out there wowing people will help DSL and Yorkville sell boxes.
Case in point:
After a year with my first DIY system, the small companies around here cloned it using store bought boxes and some even
bought the EAW cabinets I based my tops on. Remember, I refused to build them for people.
After I did a few shows with my BFMot12 modified quasi line array, some of the small guys with deep pockets around here scrambled to buy the Jbl and Qsc mini line arrays. In addition I sent a buch of weekend warriors over to the BFM site.
Now the TH. No one here appears to have heard of them.
I've already turned two church sound contractors on to the Danley stuff and my primary staduim capable ally is very interested in hearing some and encouraging me to come back into the circuit.
Personally If I am successfull, I will maintain the same additude I always have with regard to questions about my boxes at shows.
Q "Are those Meyers?" A "NO" (Passive meyer type boxes)
Q "Are those EAW's? A "No, the EAW's are better"
Q "Can you build some for me" ( $$$ in my face) "No I don't build boxes for sale, go buy the originals, you be happier with them."
My rule... You NEVER badge a DIY box, even a direct clone with another manufacturers name, and you NEVER say you have the genuine article when you don't ,nor try to sell yourself with the Genuinine article and show up with clones. That said, I have seen big companies with a mix of originals and clones all badged!!! When you look at the back of the cabinet, while you are setting up , you see the difference. Tapping the wood reveals them as well.
I personally dont want to "Clone the TH115" as that would hurt the species. Even with the plans in my hand, giftwrapped from Tom personally...I wouldn't build em or call them Danleys.
By the way.. has anybody noticed the USC-1 prices dropping?
- Home
- Loudspeakers
- Subwoofers
- Live sound specific Tapped Horn thread...