Love it! My Mom is German. I grew up around it. I just have not used it for 37 years. And technical German was not really used around the house. I included a couple more articles on calibration.Wow, thanks! That's pretty impressive, especially in light of your signature line ;-)
Yes nothing is idiot proof, they always invent better idiots.
Same for AI human nature is not exactly predictable is it 🙂
Mark
I see a couple of options to control the 3 steppers:
Does anyone have any good advise? A list of pros and cons? A well contemplated solution?
- tic, easy but gets expensive for 3 axis
- arduino + cnc shield
- 3d printer board + marlin
- 3d pritner board + raspberry pi + klipper
- ?
Does anyone have any good advise? A list of pros and cons? A well contemplated solution?
For all of us that are CNC babies, ease of control software is probably the real problem. Running wiring and connecting up belts and pulleys is not going to be a issue with most of us I think.
depending on how much interest there is, I am more than happy to make a proper PCB.Does anyone have any good advise? A list of pros and cons? A well contemplated solution?
All that being said, for first prototype, just get a ready board first.
If memory serves well, those Arduino CNC boards are easy to use/hack/abuse.
Has anyone found tic-based silent stepper drivers? That would be my preference but so far I haven’t found one. If we instead disable the motors while measuring we’ll need a counterweight for the vertical component. It would be nice to avoid that.
Few
Few
Actually the “shield “ portion has other options as well.arduino + cnc shield
Why: Octave has Arduino support; it also doesn’t hurt that Arduino is cheap. 🙂
Steppers with brakes? Quiet at least.Has anyone found tic-based silent stepper drivers? That would be my preference but so far I haven’t found one. If we instead disable the motors while measuring we’ll need a counterweight for the vertical component. It would be nice to avoid that.
That POM rack that was shown by Scott has me interested in at least part of mine being T-Slot extrusions.
That could also MATAA/Octave, would make a nicely integrated system.raspberry pi
Has anyone found tic-based silent stepper drivers? That would be my preference but so far I haven’t found one. If we instead disable the motors while measuring we’ll need a counterweight for the vertical component. It would be nice to avoid that.
Few
Microstepping and some other tweaks have limited noise considerably. However, there is a position dependent high pitched noise when they are stationary. For now I also disabled the motors during the measurements.
They are quite a bit more expensive, but they solve a problem...Steppers with brakes? Quiet at least.
https://www.aliexpress.com/item/1005002107565356.html?spm=a2g0o.detail.pcDetailBottomMoreOtherSeller.13.6a45iNW6iNW6hv&gps-id=pcDetailBottomMoreOtherSeller&scm=1007.40000.326746.0&scm_id=1007.40000.326746.0&scm-url=1007.40000.326746.0&pvid=588df23a-cc36-4e54-9e94-96e92562d274&_t=gps-id😛cDetailBottomMoreOtherSeller,scm-url:1007.40000.326746.0,pvid:588df23a-cc36-4e54-9e94-96e92562d274,tpp_buckets:668#2846#8107#66&pdp_npi=4@dis!CAD!42.88!42.88!!!30.88!30.88!@2103205217109651831928111ecc7e!12000018763258558!rec!CA!122373966!&utparam-url=scene😛cDetailBottomMoreOtherSeller|query_from:
A method to be able to know our angular position. If we use a motor with an encoder we are very far from the actual mic position. If we want a few mm positional accuracy it might be smart to have some reasonably priced rotary encoder for rotational position.
Asking for comments. Shoot it down? I'm thinking out loud here having worked on many different types of machines. There are losses due to flexture in the solid moving arm, loose fittings, gear meshing clearances that are required. They all add up quickly to a system where you really do not have the real world resolution that you think you have.
Mark
A method to be able to know our angular position. If we use a motor with an encoder we are very far from the actual mic position. If we want a few mm positional accuracy it might be smart to have some reasonably priced rotary encoder for rotational position.
Asking for comments. Shoot it down? I'm thinking out loud here having worked on many different types of machines. There are losses due to flexture in the solid moving arm, loose fittings, gear meshing clearances that are required. They all add up quickly to a system where you really do not have the real world resolution that you think you have.
And they are quiet. Steppers holding position are not quiet. They whine. A brake will buzz a bit to.They are quite a bit more expensive, but they solve a problem...
Mark
That could also MATAA/Octave, would make a nicely integrated system.
Would solve some issues with people on different platforms that have to install and setup stuff manually. We could just provide an image for the raspberry.
But on the other hand, sound a bit like gold plating while we're still wrestling in the mud.
The mechanical side is doing nothing if we don't have something worked out to move it.But on the other hand, sound a bit like gold plating while we're still wrestling in the mud.
https://www.aliexpress.com/item/1005002107565356.html?spm=a2g0o.detail.pcDetailBottomMoreOtherSeller.13.6a45iNW6iNW6hv&gps-id=pcDetailBottomMoreOtherSeller&scm=1007.40000.326746.0&scm_id=1007.40000.326746.0&scm-url=1007.40000.326746.0&pvid=588df23a-cc36-4e54-9e94-96e92562d274&_t=gps-id😛cDetailBottomMoreOtherSeller,scm-url:1007.40000.326746.0,pvid:588df23a-cc36-4e54-9e94-96e92562d274,tpp_buckets:668#2846#8107#66&pdp_npi=4@dis!CAD!42.88!42.88!!!30.88!30.88!@2103205217109651831928111ecc7e!12000018763258558!rec!CA!122373966!&utparam-url=scene😛cDetailBottomMoreOtherSeller|query_from:
A method to be able to know our angular position. If we use a motor with an encoder we are very far from the actual mic position. If we want a few mm positional accuracy it might be smart to have some reasonably priced rotary encoder for rotational position.
Asking for comments. Shoot it down? I'm thinking out loud here having worked on many different types of machines. There are losses due to flexture in the solid moving arm, loose fittings, gear meshing clearances that are required. They all add up quickly to a system where you really do not have the real world resolution that you think you have.
And they are quiet. Steppers holding position are not quiet. They whine. A brake will buzz a bit to.
Mark
Actual position is not that important. In the Klippel document attached a few posts back, they optimize the source location and orientation for each frequency.
I would say we don't need an encoder as long as the stepper is not skipping steps.
Then a hybrid stepper would cover that problem nicely.I would say we don't need an encoder as long as the stepper is not skipping steps.
Mark
As an aside, there is an enormous amount of making up for imprecise positioning in this "super precise" system. I am learning so much here. It is wonderful. I really appreciate everyone's comments and ideas.
The klippel rotates the whole measuring arm. Then is radially moves and finally is moves the microphone up and down.
In ordinary speaker impulse measurements I think I see the influence of the mic stand in the measurements. @fluid pointed me to this:
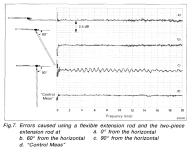
For SFS we need to measure at two distances from the speaker. If we change the 'order of motion' to rotation, up/down and finally radially, most of the reflections from measuring device will be the same for the 2 measurements at two (radial) distances. It feels like that would give SFS the best opportunity to even calculate out the reflections from the measuring device, whereas with the Klippel NFS it can't do that as the reflections of the vertical boom change. Makes sense?
For rigidity is has both pros and cons I think.
In ordinary speaker impulse measurements I think I see the influence of the mic stand in the measurements. @fluid pointed me to this:
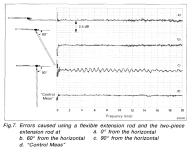
For SFS we need to measure at two distances from the speaker. If we change the 'order of motion' to rotation, up/down and finally radially, most of the reflections from measuring device will be the same for the 2 measurements at two (radial) distances. It feels like that would give SFS the best opportunity to even calculate out the reflections from the measuring device, whereas with the Klippel NFS it can't do that as the reflections of the vertical boom change. Makes sense?
For rigidity is has both pros and cons I think.
Yes exactly. The mic and the mic stand reflections are always present in a normal measurement.The klippel rotates the whole measuring arm. Then is radially moves and finally is moves the microphone up and down.
In ordinary speaker impulse measurements I think I see the influence of the mic stand in the measurements. @fluid pointed me to this:
What are we rotating? Mic Boom like Klippel or Loudspeaker?If we change the 'order of motion' to rotation, up/down and finally radially, most of the reflections from measuring device will be the same for the 2 measurements at two (radial) distances.
Mark
Yes exactly. The mic and the mic stand reflections are always present in a normal measurement.
And if they are not the same in both measurements, we can't calculate out the reflections.
Mic boom. Otherwise we can't calculate out the room reflections.What are we rotating?
That makes sense. The two stationary things are the loudspeaker and the room.Mic boom. Otherwise we can't calculate out the room reflections.
Mark
I find that picture rather strange.The klippel rotates the whole measuring arm. Then is radially moves and finally is moves the microphone up and down.
In ordinary speaker impulse measurements I think I see the influence of the mic stand in the measurements. @fluid pointed me to this:
View attachment 1288637
For SFS we need to measure at two distances from the speaker. If we change the 'order of motion' to rotation, up/down and finally radially, most of the reflections from measuring device will be the same for the 2 measurements at two (radial) distances. It feels like that would give SFS the best opportunity to even calculate out the reflections from the measuring device, whereas with the Klippel NFS it can't do that as the reflections of the vertical boom change. Makes sense?
For rigidity is has both pros and cons I think.
The mechanical momentum is the biggest by (a), followed by (b) and very little by (c), since the mass is basically at the mechanical reference point.
So unless this picture and experiment was taken on a different planet, but I find the results very strange to say the least?
Unless we are looking at reflections from the beam instead of vibrations, but it's a bit unclear at this point.
-referencing beam reflection’s (I think).
What I’m thinking of (mechanically) would have the rotating axis and the inward/outward axis at least 7 feet off of the floor/base.
What I’m thinking of (mechanically) would have the rotating axis and the inward/outward axis at least 7 feet off of the floor/base.
- Home
- Design & Build
- Software Tools
- Klippel Near Field Scanner on a Shoestring