Adding a 1 ohm series resistor (for current transduction/measurements) changes the test conditions.
Is there not a better way of deriving current measuremrnts...ie current transformer or hall effect current transducer like ACS712: Fully Integrated, Hall-Effect-Based Linear Current Sensor IC ?.
These are easily/cheaply available on Ebay pcb mounted.
Dan.
Not sure the sensitivity(66mv/A)/linearity is good enough on these, I would think a 50mOhm shunt and good instrumentation amp would be better.
Adding a 1 ohm series resistor (for current transduction/measurements) changes the test conditions.
Is there not a better way of deriving current measuremrnts...ie current transformer or hall effect current transducer like
ACS712: Fully Integrated, Hall-Effect-Based Linear Current Sensor IC ?.
Yes, we use these types quite often.
http://www.lem.com/docs/products/la 100-p e.pdf
For all devices, the key is to limit the insertion artifacts. The hall is pretty good, DCCT's are too low in BW. It's a tradeoff issue.Adding a 1 ohm series resistor (for current transduction/measurements) changes the test conditions.
Is there not a better way of deriving current measuremrnts...ie current transformer or hall effect current transducer like ACS712: Fully Integrated, Hall-Effect-Based Linear Current Sensor IC ?.
These are easily/cheaply available on Ebay pcb mounted.
Dan.
Or go even lower in resistance. A 10 milliohm shunt can be easily made using parallel resistors, and an interleave scheme can reduce the inductance down into the 50 picohenry range give or take. Shunt inductance becomes a troublesome parasitic once we start using low milliohm values of CVR. I had to modify a 250 micro-ohm shunt to bypass self inductance.Not sure the sensitivity(66mv/A)/linearity is good enough on these, I would think a 50mOhm shunt and good instrumentation amp would be better.
With a good low L and bdot resistor, then, the only issue would be how to make a low noise instrumentation amplifier. Know anybody that can do that??😉
jn
I would think a 50mOhm shunt and good instrumentation amp would be better.
We have now about 120dB dynamic range between fundamental frequency amplitude and noise bottom, for measurement with 1 ohm resistor. Balanced input of instrumentation topology used. Shall we get same dynamic range with 50 mOhm shunt and currents below 1A? In fact 1.4V/8R = 175 mA. 8.75mV at 50 milliohm and 120dB dynamic range?
I was measuring tweeters today with only 300mVrms amplifier output. 37 mA current. I do not assume that 50 mOhm shunt would work for it.
P.S.: values edited
Last edited:
... An analogy would be to drive a car with only springs as suspension. Somehow there must be some kind of 'damper' placed 'there' [either physical or mechanical ...] , with speakers it can be made by controlling the airflow/motion inside the cabinet.
FIRST WATT ARTICLES
... An analogy would be to drive a car with only springs as suspension. somehow there must be some kind of damper placed there, with speakers it can be made by controlling the airflow/motion inside the cabinet.
Qes and Qms are rarely infinite.
Actually I remember Thorsten recommending a low Qms woofer because once you go current drive it "nullifies" Qes and all that's left is the mechanical damping of the woofer.
Someone mention ported/sealed vs restrictive flow, and again I recall T saying that because drivers are designed for voltage drive I probably won't be able to find a woofer with really low Qms and I could use restrictive flow to increase the mechanical resistance and lower the Qms. He suggested many drill holes in the back of the cab with some "restriction" applied: cloth, fiberglass, etc ... The process was to add more restriction until it is critically damped (1.0 - 0.7 - 0.6).
Finally, again I recall T advising that I could use the freq resp aberrations of current drive to extend woofer response. Most big pro woofers have an fs=40 ish Hz.
If you add a bit of 'electrical' resistance in parallel, you can control the peaking (fr 'shaping') a la Nelson: ...
Last edited:
I was measuring tweeters today with only 300mVrms amplifier output. 37 mA current. I do not assume that 50 mOhm shunt would work for it.
P.S.: values edited
For a 64k FFT a 1-2nv in-amp should be ~ -120dB at 20mA rms in .05Ohms
... An analogy would be to drive a car with only springs as suspension. somehow there must be some kind of damper placed there, with speakers it can be made by controlling the airflow/motion inside the cabinet.
Qes and Qms are rarely infinite.
Actually I remember Thorsten recommending a low Qms woofer because once you go current drive it "nullifies" Qes and all that's left is the mechanical damping of the woofer.
Someone mention ported/sealed vs restrictive flow, and again I recall T saying that because drivers are designed for voltage drive I probably won't be able to find a woofer with really low Qms and I could use restrictive flow to increase the mechanical resistance and lower the Qms. He suggested many drill holes in the back of the cab with some "restriction" applied: cloth, fiberglass, etc ... The process was to add more restriction until it is critically damped (1.0 - 0.7 - 0.6).
Finally, again I recall T advising that I could use the freq resp aberrations of current drive to extend woofer response. Most big pro woofers have an fs=40 ish Hz.
If you add a bit of 'electrical' resistance in parallel, you can control the peaking (fr 'shaping') a la Nelson: ...
I find this subject fascinating, because it shows what we often ignore in loudspeaker-amp interface. It makes sense that with a poor magnetic assembly the loudspeaker will force a different 'impedance' at different positions of the cone position. When we measure the impedance curve of a loudspeaker these changes are averaged into a specific quantity.
As far as current drive is concerned, it is certainly possible to do so, and has been done with servo motors, at least when I designed amp drivers for them, but for a different reason. However, how are we going to adequately compensate for the varying frequency response of the loudspeaker system, with real speakers? Do we have to equalize each driver separately? What a headache, but an interesting concept.
As far as current drive is concerned, it is certainly possible to do so, and has been done with servo motors, at least when I designed amp drivers for them, but for a different reason. However, how are we going to adequately compensate for the varying frequency response of the loudspeaker system, with real speakers? Do we have to equalize each driver separately? What a headache, but an interesting concept.
Now these dynamic speaker mechanisms may not be fully understood, but ----- which is then summed to the driving current creating the measured distortion.
Current drive is just as bad (actually a lot worse) as it will be like constant force but there's still the varying load, this will create a lot of acoustical distortion as that will be the only physical possibility.
Drivers which are planar types and ribbons, also Heil, etc are low Z and very low L and magnetic structure which is very different. And, there is the electro-static.... all seem to minimize the problems of conventional drivers and amplifier interaction.
Wouldn't they have lowered amp interaction (back emf etc). What do we get for current distortion with those types of drivers?
THx-RNMarsh
Last edited:
Actually I remember Thorsten recommending a low Qms woofer because once you go current drive it "nullifies" Qes and all that's left is the mechanical damping of the woofer.
This was originally Mills/Hawksford's point. Nelson first made me aware of their work. The current drive thing keeps getting rediscovered, then disappears- to John's point, it would be best used with drivers designed for it rather than trying to force the square peg of voltage drive speakers into the round hole of current drive.
Actually I remember Thorsten recommending a low Qms woofer because once you go current drive it "nullifies" Qes and all that's left is the mechanical damping of the woofer.
Someone mention ported/sealed vs restrictive flow, and again I recall T saying that because drivers are designed for voltage drive I probably won't be able to find a woofer with really low Qms and I could use restrictive flow to increase the mechanical resistance and lower the Qms. He suggested many drill holes in the back of the cab with some "restriction" applied: cloth, fiberglass, etc ... The process was to add more restriction until it is critically damped (1.0 - 0.7 - 0.6).
Finally, again I recall T advising that I could use the freq resp aberrations of current drive to extend woofer response. Most big pro woofers have an fs=40 ish Hz.
If you add a bit of 'electrical' resistance in parallel, you can control the peaking (fr 'shaping') a la Nelson: ...
Sorry, bad internet connection through my base-level smart phone ..., I wasn't done ..
.. so, a la Nelson:
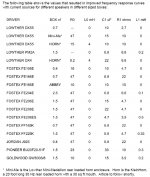
You can control the amount of peaking to suit your application ... but it's ususally a lot larger a res than you would expect (25-75 ohms)
... or you could go full-active-control and create Linkwitz style circuits that manipulate these exact, high-level-math features ...
And T recommended exactly this a decade to a decade and a half ago :0 ... way back to audioasylum.com days and the birth of this very forum ...
And he referenced it "against the old days" (pre 1950's) when they did all this ... on purpose ... to overcome acoustic hurdles, with tubes as current devices, seeing the driver-enclosure-room as a system that produces acoustic results, ...
And ended up with fantastic results in some cases ... but we seem to have forgotten ... anyway ...
Damn I miss that guy, too bad things didn't turn out ...
Cheers and thanks,
Jeff
Last edited:
Yeah, it's been around for a while. Mills and Hawksford wrote about it over 25 years ago and I bet they weren't the first.
I find this subject fascinating, because it shows what we often ignore in loudspeaker-amp interface. It makes sense that with a poor magnetic assembly the loudspeaker will force a different 'impedance' at different positions of the cone position. When we measure the impedance curve of a loudspeaker these changes are averaged into a specific quantity.
As far as current drive is concerned, it is certainly possible to do so, and has been done with servo motors, at least when I designed amp drivers for them, but for a different reason. However, how are we going to adequately compensate for the varying frequency response of the loudspeaker system, with real speakers? Do we have to equalize each driver separately? What a headache, but an interesting concept.
Me too John although I am more on the transducer side than amplifier side now days.
There is a paradox which no one caught in my earlier post. The linearity of the motor system is the primary distortion source for a woofer. The distorted waveform “shows up” because the motor’s force sensitivity changes with position instead of being a constant. This might be likened to the transfer function curve of many other real world devices.
My point was that in the back emf Voltage , on the other side of the Rdc, one has a measure of the driver velocity which includes the distortion and can be used as a negative feed back signal.
In he Servodrive subwoofers we used to make in the 80’s and 90’s I fiddled with PWM amps which were the norm for servomotors back then and found that they were neither a current or voltage amplifier but were a duty cycle controller. In making one from scratch, one needed to derive the output voltage and current, filter it from rail to rail hash into an analogue signal for feedback.
If one has lowered the output impedance below zero, the motion related distortion is reduced but the response is tipped as if Qe were VERY VERY small. If one has Current drive one has the response shape as if Qe were very large and usually increased distortion.
The reason as seen in the earlier rotary motor analogy, a motor driven by a current source has no speed regulation, it exerts a fixed amouth of torque from stopped to safe max speed. A motor driven by a Voltage source through a small resistor will slow down a little when loaded down but the amount of load is partially reflected in the increased current drawn under load. A motor driven with a perfect negative impedance equal to the motor Rdc when loaded will not slow at all and the load is entirely reflected in the increased current. With a loudspeaker, you have a simple DC motor, it's just driven with an AC signal. Where the motor oscillated proportionally back and forth, the voice coil moves proportionally in and out.
The best solution I think is to have the least non-linearity, fewest things to fix possible even in very large scale sound.
Best,
Tom Danley
Danley Sound Labs
Let's make a list of the mechanisms which cause distortion and whether they benefit from current drive. Then we can factor in the relative magnitudes of each contribution depending on speaker construction.
Nonlinear distortions:
Nonlinear Suspension - ?
Voice coil Eddy currents (Jneutron) - benefits from current drive
Voice coil resistance nonlinearity - benefits from current drive
Voice coil inductance nonlinearity - benefits from current drive
Nonlinear magnet - benefits from current drive?
Linear Distortions:
Response aberrations can always be EQ'd out. What linear distortions cannot be fixed by EQ and speaker design adjustments? Do we need to rely on electromagnetic braking to dampen the cone?
Shorting ring: This might throw away some of the potential benefits of current drive because it shunts any back-EMF rejection at the frequencies where it is active.
Nonlinear distortions:
Nonlinear Suspension - ?
Voice coil Eddy currents (Jneutron) - benefits from current drive
Voice coil resistance nonlinearity - benefits from current drive
Voice coil inductance nonlinearity - benefits from current drive
Nonlinear magnet - benefits from current drive?
Linear Distortions:
Response aberrations can always be EQ'd out. What linear distortions cannot be fixed by EQ and speaker design adjustments? Do we need to rely on electromagnetic braking to dampen the cone?
Shorting ring: This might throw away some of the potential benefits of current drive because it shunts any back-EMF rejection at the frequencies where it is active.
If you mean non-homogeneous field dependent on the coil position, no: current drive would make things worse: a pure, idealized voltage drive is what is needed.Nonlinear magnet - benefits from current drive?
Same remark for non-linearities in the compliance (or stiffness) of the suspension: a perfect voltage drive will impose constant velocity, whatever
Back emf is mostly caused by a motional mechanism: the shorting ring makes the magnetic field ~infinitely stiff regarding perturbations caused by the coil.Shorting ring: This might throw away some of the potential benefits of current drive because it shunts any back-EMF rejection at the frequencies where it is active.
I therefore doesn't shunt anything useful, quite the opposite in fact.
Back emf is nothing but mechanical impedance transformed to electrical side via gyrator. It acts like a resonant rlc circuit then. Same, no need for any mystery. Elements are nonlinear.
Oldies and goodies
Circa 1930 Voigt and Lowther were doing this.
Thornsten was also mentioning Eckmiller http://www.diyaudio.com/forums/lounge/200865-sound-quality-vs-measurements-482.html#post3002630
Addition of acoustic resistance and restricted back volume for speaker acoustical damping (Ted Jordan 1956):
http://www.ejjordan.co.uk/PDFs/A-Cabinet-of-Reduced-Size-with-Better-Low-Frequency-Performance.pdf
Amp-speaker interface related articles:
Zero-Impedance Output Stage:
by Raymond G. Anthes, Audio Engineering, January 1953:
https://www.aikenamps.com/images/Documents/zeroz.pdf
Variable Damping Factor Control
by Charles A. Wilkins, Audio, September 1954
https://www.aikenamps.com/images/Documents/vardamp.pdf
Speaker Damping
(source unknown), Journal of the Audio Engineering Society
https://www.aikenamps.com/images/Documents/dampfac.pdf
Control of Amplifier Source Resistance
by Charles A. Wilkins, Journal of the Audio Engineering Society, January 1956
https://www.aikenamps.com/images/Documents/sourcer.pdf
George
He (Thorsten) suggested many drill holes in the back of the cab with some "restriction" applied: cloth, fiberglass, etc ... The process was to add more restriction until it is critically damped (1.0 - 0.7 - 0.6).
Finally, again I recall T advising that I could use the freq resp aberrations of current drive to extend woofer response. Most big pro woofers have an fs=40 ish Hz.
Circa 1930 Voigt and Lowther were doing this.
Thornsten was also mentioning Eckmiller http://www.diyaudio.com/forums/lounge/200865-sound-quality-vs-measurements-482.html#post3002630
Addition of acoustic resistance and restricted back volume for speaker acoustical damping (Ted Jordan 1956):
http://www.ejjordan.co.uk/PDFs/A-Cabinet-of-Reduced-Size-with-Better-Low-Frequency-Performance.pdf
Amp-speaker interface related articles:
Zero-Impedance Output Stage:
by Raymond G. Anthes, Audio Engineering, January 1953:
https://www.aikenamps.com/images/Documents/zeroz.pdf
Variable Damping Factor Control
by Charles A. Wilkins, Audio, September 1954
https://www.aikenamps.com/images/Documents/vardamp.pdf
Speaker Damping
(source unknown), Journal of the Audio Engineering Society
https://www.aikenamps.com/images/Documents/dampfac.pdf
Control of Amplifier Source Resistance
by Charles A. Wilkins, Journal of the Audio Engineering Society, January 1956
https://www.aikenamps.com/images/Documents/sourcer.pdf
George
Last edited:
JAES Volume 3 Issue 3 pp. 132-142; July 1955Speaker Damping
(source unknown), Journal of the Audio Engineering Society
- Status
- Not open for further replies.
- Home
- Member Areas
- The Lounge
- John Curl's Blowtorch preamplifier part II