The diodes on board are HER208.
I don't bother bypassing the electros, but no hard in it. MKP x2 safety caps work very well and they are cheap.
I don't bother bypassing the electros, but no hard in it. MKP x2 safety caps work very well and they are cheap.
Pardon for my ignorance, what's an MKP?The diodes on board are HER208.
I don't bother bypassing the electros, but no hard in it. MKP x2 safety caps work very well and they are cheap.
One of the capacitor codes. It means it's a polypropylene cap.
CBB is also polyproplyene as is MPX.
MKT is polyester
MKC is polycarbonate.
There's more info here:
https://en.wikipedia.org/wiki/Film_capacitor
Koda
CBB is also polyproplyene as is MPX.
MKT is polyester
MKC is polycarbonate.
There's more info here:
https://en.wikipedia.org/wiki/Film_capacitor
Koda
Thank you!One of the capacitor codes. It means it's a polypropylene cap.
CBB is also polyproplyene as is MPX.
MKT is polyester
MKC is polycarbonate.
There's more info here:
https://en.wikipedia.org/wiki/Film_capacitor
Koda
Jose
I bought one of these SMPS units a while back but have never used it. I've got a different project on the breadboard now so I'm not ready to start experimenting yet, but I'd like to clarify a few things.
I'd like to try using it to power a simple SE amp using 2 output tubes and no more than 2 input tubes. Outputs would likely be something like 6BQ5, 6V6, 6AQ5, 6N6G or similar.
An earlier post mentions that having a load on the 12.6v output is needed in order to maximize the level of HV output. In my current project I'm using a 6AX4GTB damper diode as a soft start device in a so-called "cockeyed bridge". The SS diodes take care of the rectification, the tube is fed DC and produces a slow start.
So I'm wondering if I could use the 12.6v output to heat a 12AX4GTB and use it as a soft start device? Would using a damper diode for soft start make it easier or harder for the HV supply to start up?
It wouldn't bother me if it resulted in an additional startup delay on top of the stock 30 seconds. But I'd like it to start up without having hiccups or re-starting repeatedly.
I'd like to try using it to power a simple SE amp using 2 output tubes and no more than 2 input tubes. Outputs would likely be something like 6BQ5, 6V6, 6AQ5, 6N6G or similar.
An earlier post mentions that having a load on the 12.6v output is needed in order to maximize the level of HV output. In my current project I'm using a 6AX4GTB damper diode as a soft start device in a so-called "cockeyed bridge". The SS diodes take care of the rectification, the tube is fed DC and produces a slow start.
So I'm wondering if I could use the 12.6v output to heat a 12AX4GTB and use it as a soft start device? Would using a damper diode for soft start make it easier or harder for the HV supply to start up?
It wouldn't bother me if it resulted in an additional startup delay on top of the stock 30 seconds. But I'd like it to start up without having hiccups or re-starting repeatedly.
Last edited:
Unless you modify it, the HV is delayed by 30 seconds or so so the damper will already be hot when it tries to start the HV section...
Perhaps I don't understand how the slow start aspect of the damper works. So you're saying that, once its heater is fully powered up and its cathode is fully heated, the damper won't slowly increase the DC from the HV tap? The load would see the full voltage immediately after the 30 second delay?Unless you modify it, the HV is delayed by 30 seconds or so so the damper will already be hot when it tries to start the HV section...
I guess it would make sense that the soft start characteristics of the damper (or indirectly heated rectifier) vary depending on the design of the cathode with some taking longer than others to reach full emission.
If that's the case a better way to load the 12.6v output would be to use a mix of 6.3v and 12.6v tubes.
If that's the case a better way to load the 12.6v output would be to use a mix of 6.3v and 12.6v tubes.
The 12AX4GTB warm up time is -~11s. When your HV is turned on after the 30s delay there will not be a soft start, the damper diode will be ready. You will have to remove or reduce the HV delay.
That mod was discussed earlier but I'm totally unfamiliar with SMPS circuitry so I don't really understand how to do it.The 12AX4GTB warm up time is -~11s. When your HV is turned on after the 30s delay there will not be a soft start, the damper diode will be ready. You will have to remove or reduce the HV delay.
@kodabmx said: "My trick was to tack a 33k resistor across the timing resistor for the 555 so the HV only delays 1/2 seconds instead of 30. There is no capacitor on the HV for output tubes, and RC of 10k/50uF per channel for the VA/PI stage."
I have no idea what a 555 is, what it looks like, where it's located, or which resistor is the timing resistor that he paralleled with a 33k. Anyone got a pic?
But its unclear whether or not the mod actually worked because he later added:
"Update: I turned up the volume and the POS protection tripped . . . 50 buck to who can tell me how to disable the protection. I'd rather it catch fire. It's a damned nuisance.
Update. RC 100R into 100uF on the HV solved the turn off problem, but now it hiccups 25 times to start."
So it sounds like the 33k resistor didn't really work but that tacking an RC on to the HV output might have. Was the 33k removed or left in place? And is the configuration that worked 100R into 100uf (to B+) followed by 10k into 50uf (to input tubes)?
All this is confusing because earlier in the thread there seemed to be a recommendation that the B+ should be taken directly off the HV output without any additional capacitance because that would cause the unit to shut down, although the cap size being discussed was much larger.
I'm not really too concerned about the 30 second delay but I'd like to configure it in such a way that eliminates an extended series of hiccups and the possibility of a "protection" shutdown. Was anyone able to either solve these issues or, at least, minimize them?
I'd recommend just using the smps as is. Connect the output tubes in series to the 12.6V output, and the input tubes to the 6.3V or 12.6 depending on the heater requirements.
Soft start is not reay needed for such low voltage, and you already have an HV delay.
Soft start is not reay needed for such low voltage, and you already have an HV delay.
Last edited:
Yeah, I wasn't all that concerned about the soft start aspect. I just thought that perhaps a damper diode would alleviate some of the startup issues while also loading the 12.6v output but I see that's not the case.
So is it best to run B+ right off the supply and add an RC for the inputs or will it work better if I add an RC prior to the B+ and follow it with another RC to the inputs?
Another question . . .
I've seen this advisory note about how to hook up the grounds "separately" but I'm confused about exactly what it means.
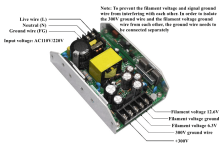
So is it best to run B+ right off the supply and add an RC for the inputs or will it work better if I add an RC prior to the B+ and follow it with another RC to the inputs?
Another question . . .
I've seen this advisory note about how to hook up the grounds "separately" but I'm confused about exactly what it means.
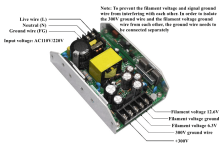
IMHO, the key to successful use of smps is to use these smps at a fraction of their power ratings...s if you have a unit quoted for 300 watts, try not to use it on loads of more than 100 watts total....
I understand the need to de-rate the current.
I'm mostly just trying to figure out how to hook it up so that it operates as smoothly as possible, which ideally means that it starts up after the 30 second delay without hiccups and re-starts.
Some posts say to just run the B+ directly from the 300v and then use an RC section to supply input tubes. Another post says it worked better running 100R into 100uf (to B+) followed by 10k into 50uf (to input tubes). And other posts warn against using too large of a cap to supply the B+, but I got the impression that this referred to putting a large value cap right after the 300v output with no R between them.
I assume the 300v ground connection would be to the negative of the cap?
So I'd like the hear about other's experiences and how they have the HV portion configured and if their startup is smooth.
Also, if I was heating the tubes with a normal filament winding I would run the heaters in parallel using a CT filament transformer with the CT providing a ground reference.
How would the heaters be wired in order to use a mix of 6.3v and 12.6v tubes when there is only one shared heater ground?
For example, if I was running two 6.3v tubes and two 12.6v. Would one heater pin of each 6.3v connect to the 6.3v, one heater pin of each 12.6v connect to the 12.6v connection and then the other four heater pins connect to the common heater ground? Is that ground connection then grounded to signal ground or is it left floating?
As I understand it, unless the tube is a rectifier, the heaters need a ground reference. Yet that seems to create a dilemma because the "note" in the diagram says that the HV ground and the heater ground need to be "isolated" from each other and connected "separately".
Would a ground buss with the HV ground connected to the cap negative at one end and the heater ground connected further away be considered "isolated" from each other and connected "separately"?
I'm mostly just trying to figure out how to hook it up so that it operates as smoothly as possible, which ideally means that it starts up after the 30 second delay without hiccups and re-starts.
Some posts say to just run the B+ directly from the 300v and then use an RC section to supply input tubes. Another post says it worked better running 100R into 100uf (to B+) followed by 10k into 50uf (to input tubes). And other posts warn against using too large of a cap to supply the B+, but I got the impression that this referred to putting a large value cap right after the 300v output with no R between them.
I assume the 300v ground connection would be to the negative of the cap?
So I'd like the hear about other's experiences and how they have the HV portion configured and if their startup is smooth.
Also, if I was heating the tubes with a normal filament winding I would run the heaters in parallel using a CT filament transformer with the CT providing a ground reference.
How would the heaters be wired in order to use a mix of 6.3v and 12.6v tubes when there is only one shared heater ground?
For example, if I was running two 6.3v tubes and two 12.6v. Would one heater pin of each 6.3v connect to the 6.3v, one heater pin of each 12.6v connect to the 12.6v connection and then the other four heater pins connect to the common heater ground? Is that ground connection then grounded to signal ground or is it left floating?
As I understand it, unless the tube is a rectifier, the heaters need a ground reference. Yet that seems to create a dilemma because the "note" in the diagram says that the HV ground and the heater ground need to be "isolated" from each other and connected "separately".
Would a ground buss with the HV ground connected to the cap negative at one end and the heater ground connected further away be considered "isolated" from each other and connected "separately"?
one thing to realize about SMPS, while the ripple voltage frequency of 60hz ac after rectification is 120 hz, with SMPS the ripple voltage frequency is in the neighborhood of 60khz or even more, so that the psu cap faltering that we have gotten used to in the 60hz case does not apply, what is needed is many many time smaller in ufd value and this is where films can be used to good, here the esr of the filter caps is what mattered more....
Not sure how practical it is to use film caps in that situation for high voltage dc filtering. For example a physically large 400Vdc rated film of say 3u3 likely has an impedance minima in the high hundreds of kHz, and its impedance back down at 60-100kHz may well be more than a 3u3 ecap. Film caps can get physically quite large, which then makes the charging current loop area quite large.
CBB60 caps are polypropylenes rated at 450vac and had become very small in size, to that it is now possible to make tube amps without electrolytics..
https://www.capacitorindustries.com...ilize,mechanical shock and vibration strength.
https://www.capacitorindustries.com...ilize,mechanical shock and vibration strength.
The recent discussion appears to be about two aspects. One is for an external cap (to the smps) that is used to further filter the 60-100kHz local to the smps before B+ is distributed to nearby amps. That external cap could also be used for local amp bypassing of B+, or the distribution could include additional RC where each amp has local C to keep large audio signal currents local to that amp.
If the aim is to further filter the 60-100kHz, then the impedance and loop area of that extra filter stage becomes important, otherwise parasitic couplings will tend to bypass the benefit of the filter parts. I note that the pcb already uses what looks like 33uF ecap filtering for B+. The best way to further filter 60-110kHz is on the smps pcb itself, but that isn't practical, so preferably the next filtering cap is directly on the pcb output terminals, and not a few inches away where any large motor start cap is bolted to the chassis.
If the aim is to further filter the 60-100kHz, then the impedance and loop area of that extra filter stage becomes important, otherwise parasitic couplings will tend to bypass the benefit of the filter parts. I note that the pcb already uses what looks like 33uF ecap filtering for B+. The best way to further filter 60-110kHz is on the smps pcb itself, but that isn't practical, so preferably the next filtering cap is directly on the pcb output terminals, and not a few inches away where any large motor start cap is bolted to the chassis.
Could anyone comment on the basic questions I posted about how to physically hook this up?
RC to B+ or B+ straight from the 300v output? How to wire a mix of 6.3v and 12.6v heaters when the two share a ground connection on the SMPS?
The technical issues involved in the question of whether a film cap or electrolytic would be best is something that I'm not so concerned about right now. Some info about the cap values that people have used with this would be informative, however.
RC to B+ or B+ straight from the 300v output? How to wire a mix of 6.3v and 12.6v heaters when the two share a ground connection on the SMPS?
The technical issues involved in the question of whether a film cap or electrolytic would be best is something that I'm not so concerned about right now. Some info about the cap values that people have used with this would be informative, however.
one thing to realize about SMPS, while the ripple voltage frequency of 60hz ac after rectification is 120 hz, with SMPS the ripple voltage frequency is in the neighborhood of 60khz or even more, so that the psu cap faltering that we have gotten used to in the 60hz case does not apply, what is needed is many many time smaller in ufd value and this is where films can be used to good, here the esr of the filter caps is what mattered more....
The same rule applies to chokes here. Their values are now measured in micro henries.
- Home
- Amplifiers
- Tubes / Valves
- HIFI 250W Switch Power Supply DC300V@0.6A +12.6V@4A +6.3V4A