6l6, thanks. Looking at them more closely cutting the underside of the board between last cap and output pads to add a resistor and using the filter resistor location for the chokes looks doable.
Diode bridge heatsink
I'm in the phase of laying out parts in a chassis to see how things will fit and keeping interference noise the lowest.
Using the Fairchild GBPC3502 rectifier bridge: I read the spec sheet and looked at the temperature / amperage derating curve - which was done using a 200mm x 200mm x 50mm heatsink. I have never seen a build with a giant heatsink for these. nor do I remember the interior of an Adcom using similar diode bridges having a memorable heatsink.
I'm probably going to find a small section of thick wall 1.25" aluminum square tube to mount these and make them into a pair of chimney's of sorts. Plan is to keep all AC near the bottom where I can shield it, then put the PSU high in the back of the chassis. Maybe split the PSU board and "fold" it back to back on a riser plate to save a little room. A large PEM with switch, fuse and filter is taking up more space than I had originally imagined.
I'm in the phase of laying out parts in a chassis to see how things will fit and keeping interference noise the lowest.
Using the Fairchild GBPC3502 rectifier bridge: I read the spec sheet and looked at the temperature / amperage derating curve - which was done using a 200mm x 200mm x 50mm heatsink. I have never seen a build with a giant heatsink for these. nor do I remember the interior of an Adcom using similar diode bridges having a memorable heatsink.
I'm probably going to find a small section of thick wall 1.25" aluminum square tube to mount these and make them into a pair of chimney's of sorts. Plan is to keep all AC near the bottom where I can shield it, then put the PSU high in the back of the chassis. Maybe split the PSU board and "fold" it back to back on a riser plate to save a little room. A large PEM with switch, fuse and filter is taking up more space than I had originally imagined.
Bridge rectifiers get hot if they have to pass a high current continuously.
They also get hot if they have to pass a very pulsating current that has a high rms value that is a significant proportion of it's maximum rating.
Most amplifiers do not draw a continuous current. Typical amps we use are ClassAB. Some will use ClassG & H and some will be switching types. All of these draw average currents that are MUCH lower than the transient current that can be demanded during short periods of near maximum output.
Bridge rectifiers never get hot in that type of operation. They may get warm, but rarely require a heatsink. Simply bolting the rectifier to the floor or side of the chassis is sufficient if a bit of extra cooling is deemed necessary.
ClassA is the exception.
This does draw a continuous load that does heat up the bridge rectifier.
This is exagerated due to impulsive nature of the charging current flowing through the rectifier.
I have found that ClassA amplifier rectifiers need a heatsink.
They also get hot if they have to pass a very pulsating current that has a high rms value that is a significant proportion of it's maximum rating.
Most amplifiers do not draw a continuous current. Typical amps we use are ClassAB. Some will use ClassG & H and some will be switching types. All of these draw average currents that are MUCH lower than the transient current that can be demanded during short periods of near maximum output.
Bridge rectifiers never get hot in that type of operation. They may get warm, but rarely require a heatsink. Simply bolting the rectifier to the floor or side of the chassis is sufficient if a bit of extra cooling is deemed necessary.
ClassA is the exception.
This does draw a continuous load that does heat up the bridge rectifier.
This is exagerated due to impulsive nature of the charging current flowing through the rectifier.
I have found that ClassA amplifier rectifiers need a heatsink.
The 3 legged rectifier diodes can be installed in either direction, correct? Connecting to the chassis. Not using small heat sinks.
If pin 2 is cathode, then yes.
BUT remember that the case is also cathode, so use insulators if they are not insulated package.
BUT remember that the case is also cathode, so use insulators if they are not insulated package.
Quick (and possibly dumb) question. What is the point of the ST_V-/+ and ST_G1/2 blades, are they just alternatives to the euroblocks?
Cheers.
Cheers.
It depends on how well matched your transistors are... the 1R value was to utilize loosely matched outputs.
Ok I see.I am going to order transistors from h_a (If he still sells them..?)
I don´t know how well he matches them?
I don´t know how well he matches them?
If I wanna use air wound coils instead,can I use this one 2,0mH or 2,5mH?:
Spole Luftlindad Ø1.2 mm tråd - HIFI KIT
Spole Luftlindad Ø1.2 mm tråd - HIFI KIT
So perhaps someone can help me. I have 22mf caps 4 each rail. 22k bleeder resistors. Why do my leds stay on way after the power is off. I can read the volts dropping down after I remove the AC but it takes 5 minutes. Is this normal??? I have a 800KVA 25 volts and +35 and -35vdc then it will drop slowly (3 minutes or more) to 0VDC. My hundred watt light comes on and then fades to nothing. but will "light up" for a moment if I give the caps time to discharge. So I think I have it right.
If you are asking about the time to discharge 22mF with 22k bleeder, then you can model it using RC time constants.
RC = 22mF (0.022F) times 22k (22000ohms) = 484seconds =~8minutes
That is the time to reach 34% of the initial charge voltage.
RC = 22mF (0.022F) times 22k (22000ohms) = 484seconds =~8minutes
That is the time to reach 34% of the initial charge voltage.
6L6, I see little ceramic capacitors on your terminal blocks along with the CL-60 thermistors. Can you explain the theory behind them and how to size them?
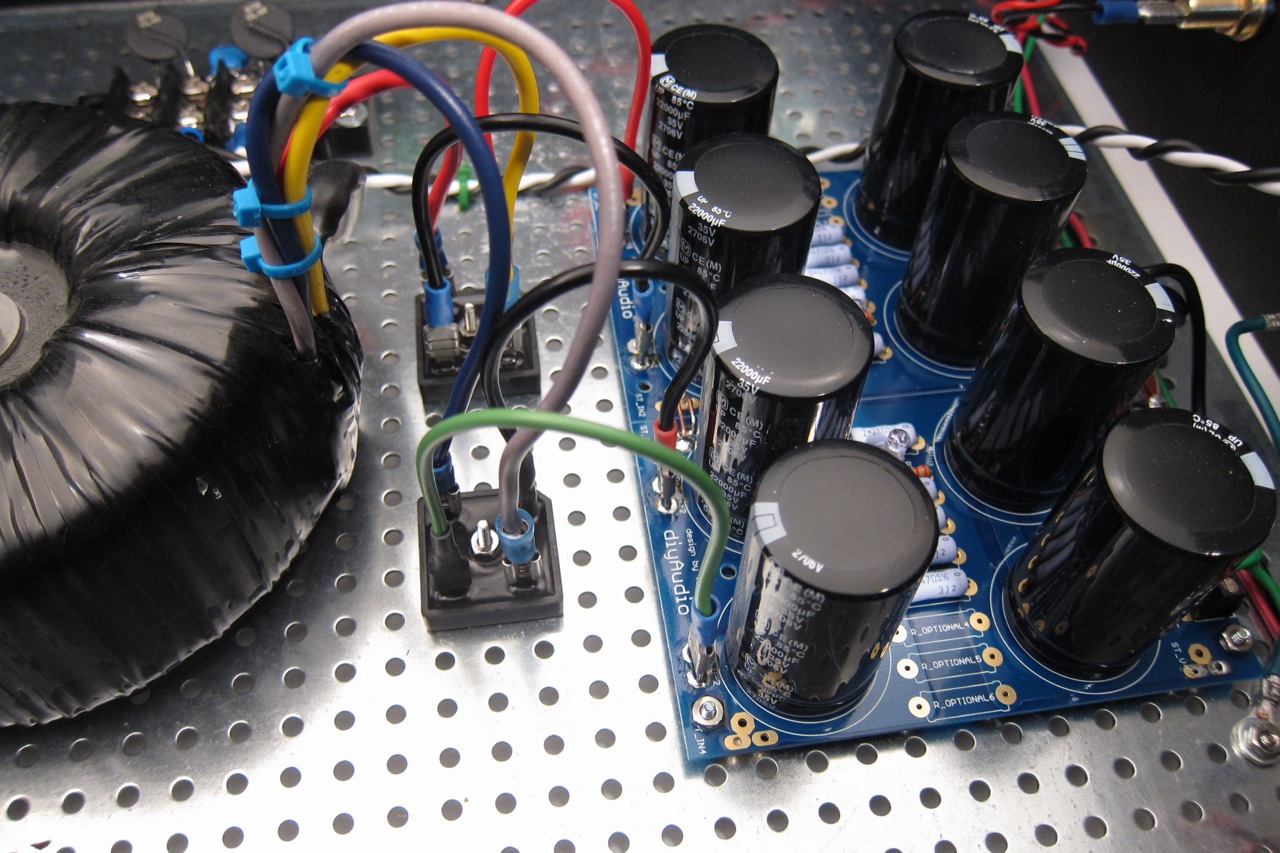
Last edited:
- Home
- Amplifiers
- Power Supplies
- diyAudio Power Supply Circuit Board v3 illustrated build guide