Having the bearings loose on the spacing shaft allows some self centering of the bearings to allow for imperfections in the glass tube and bearing edges contacting the glass as it rolls along. Otherwise it may be only contacting 3 points at various points along the rail with potential rocking to the non contacting fourth bearing.
Regards
Wayne
Regards
Wayne
Hmmm... wiggly, wobbly then?
If this is the case then the whole assembly will try to rotate about an axis perpendicular to the record (the same axis as does the center pin that goes through the record, in addition to trying to slide horizontally across the glass tube. It will do first whichever requires the lower force.
As far as the bearings binding when the inner race is held solid, I'm surprised that this can or does happen, especially with precision bearings.
WRT the ability of the bearings to slide on their shaft, albeit a small amount, it's entirely unclear how that will permit them to correct for imperfections in the flatness of the glass surface. Under the weight of the carriage they will be pushed to the maximum outer position, with no way for a single bearing to move back to the center on its own. They'll stay at the max regardless of the "terrain" they follow. Maybe if they were spring loaded that would be a different case, but they are not spring loaded along the shaft.
So it seems to me...
If this is the case then the whole assembly will try to rotate about an axis perpendicular to the record (the same axis as does the center pin that goes through the record, in addition to trying to slide horizontally across the glass tube. It will do first whichever requires the lower force.
As far as the bearings binding when the inner race is held solid, I'm surprised that this can or does happen, especially with precision bearings.
WRT the ability of the bearings to slide on their shaft, albeit a small amount, it's entirely unclear how that will permit them to correct for imperfections in the flatness of the glass surface. Under the weight of the carriage they will be pushed to the maximum outer position, with no way for a single bearing to move back to the center on its own. They'll stay at the max regardless of the "terrain" they follow. Maybe if they were spring loaded that would be a different case, but they are not spring loaded along the shaft.
So it seems to me...
SGregory and BillG,
Very nice work. Congratulations. Enjoy the music.
Bear,
Spring loaded. Interesting idea.
Very nice work. Congratulations. Enjoy the music.
Bear,
Spring loaded. Interesting idea.
Bear,
You bring up valid points, but I must admit here that the glass tube size vs bearing spacing is more important on this design than whether the bearing is loose. Precision bearings probably don't need this, but it does work without any stick slip behavior which was the goal.
Colin
You bring up valid points, but I must admit here that the glass tube size vs bearing spacing is more important on this design than whether the bearing is loose. Precision bearings probably don't need this, but it does work without any stick slip behavior which was the goal.
Colin
May i ask why everybody is running the cart ON the glass-tube rather than cut it open and run like the Cantus-arm inside the tube? Is it purly because it's much simpler to build or because you have tried both and thought it was better ON the tube? (i haven't been reading the whole thread from the start)
I would think that the open tube would be better, because you would only need two bearings, and hence less contact/friction. Well i'm just thinking out loud.
I would think that the open tube would be better, because you would only need two bearings, and hence less contact/friction. Well i'm just thinking out loud.
Rolle2k,
Yes you can run it in the tube, but, that's been done before. I didn't want to copy a design, I dont know that its simpler really but heck it works well and sounds good!. We have the Cantus, the Clearaudios, nothing wrong with thinking outside the box, or in this case, tube, lol. In reality in or out of the tube contact area is the same, with possibly more in the tube in reality.
Colin
Yes you can run it in the tube, but, that's been done before. I didn't want to copy a design, I dont know that its simpler really but heck it works well and sounds good!. We have the Cantus, the Clearaudios, nothing wrong with thinking outside the box, or in this case, tube, lol. In reality in or out of the tube contact area is the same, with possibly more in the tube in reality.
Colin
Rolle2k,
Yes you can run it in the tube, but, that's been done before. I didn't want to copy a design,Colin
In no way is this an attack. Just friendly fodder. May 2010 Post 213 is a good view.
http://www.diyaudio.com/forums/analogue-source/34126-opus-3-cantus-parallel-tracking-arm-22.html
For one thing, cutting a glass tube lengthwise is a PIA... best done with a diamond saw imho... maybe under coolant, almost certainly. I think you could manage it with a consumer type "tile saw" (uses diamond blades). In the USA they can be had inexpensively from Harbor Freight.
I think they did the cutout because it doubles as a dust cover for the inner part, otherwise you could simply use a half cut tube, which at least in theory might be easier to make...
I think they did the cutout because it doubles as a dust cover for the inner part, otherwise you could simply use a half cut tube, which at least in theory might be easier to make...
Golana,
No attack, I've seen that one, but having the assembly on the front of the tube leaves the arm at a weight distribution disadvantage. Thanks for the pic is.
Colin
No attack, I've seen that one, but having the assembly on the front of the tube leaves the arm at a weight distribution disadvantage. Thanks for the pic is.
Colin
Sorry correction, looked at wrong thread, similar idea, different concept with my free floating bearings, I wonder if he too discovered the importance of the spacing, one pic looks really close, it's a balance between low friction and stability .
Colin
Colin
Let me repost that link on here from the Cantus thread, in post #213. That blog post from a Thai audiophile was posted in 2008. Originally in Thai language translated via Google Translate.
http://aboyhome.blogspot.com --- "Linear arm on glass tube" Google Translated from Thai
http://aboyhome.blogspot.com/2008/07/blog-post_31.html --- Linear arm on metal tube
http://aboyhome.blogspot.com --- "Linear arm on glass tube" Google Translated from Thai
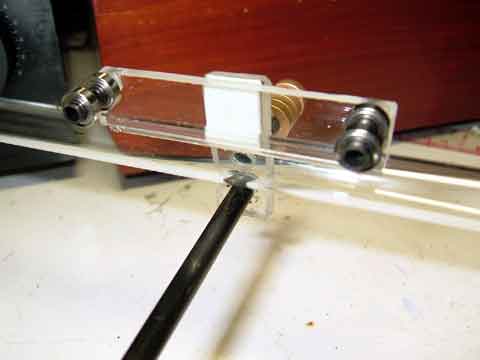
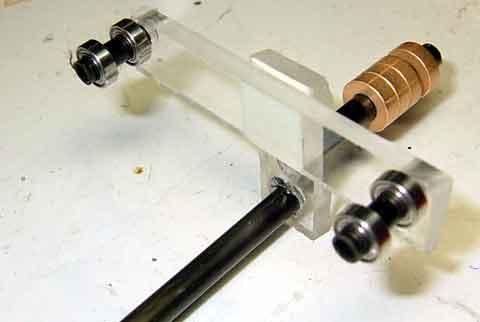
http://aboyhome.blogspot.com/2008/07/blog-post_31.html --- Linear arm on metal tube
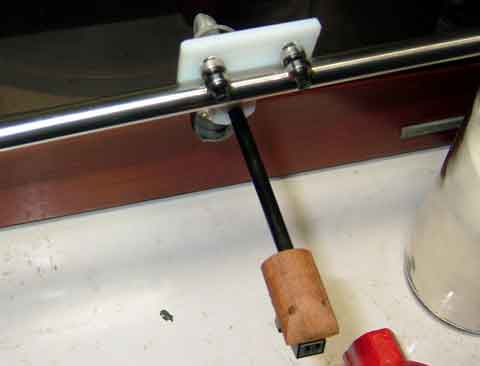
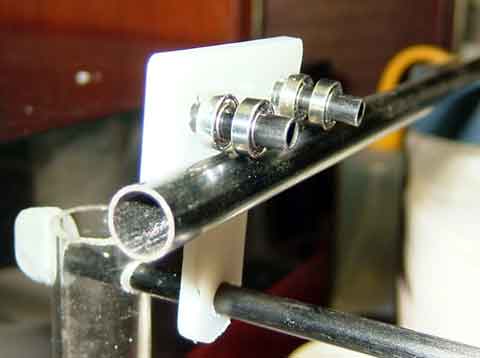
Bear has got me paranoid about the stylus picking up hum from incorrect mounting. So I have cut part of my top chassis away so I can attach a lump of granite as a base for the arm. This granite is attached using the original tone arm mountings so hopefully I now have a safe stable base for the arm.
Electricians who connect cables running under ground use a potting compound where they make joins. It seals out the elements. While the turntable is apart. Would it improve the table if I pour some of this dense potting compound into the bottom tray. Obviously keeping it away from the stator, the ventilation holes for the transformer and the suspension columns.
Sorry the question is sort of off topic, but I would not of done this unless I was fitting the arm
Electricians who connect cables running under ground use a potting compound where they make joins. It seals out the elements. While the turntable is apart. Would it improve the table if I pour some of this dense potting compound into the bottom tray. Obviously keeping it away from the stator, the ventilation holes for the transformer and the suspension columns.
Sorry the question is sort of off topic, but I would not of done this unless I was fitting the arm
Attachments
Oh, ur going to definitely *hate me*... but you could just take that motor assembly and CHUCK the rest of that "turntable" and build up ur own "plinth" (that's what you Brits call it?) and get a much better result.
I'd say anything that you can to to damp the path between that motor assembly (mounted to the sheet metal base now) and the rest of the world, the quieter the TT will be.
Having said all that, one of the things that folks who are going nuts over the old Garrard 301 seems to be the opposite, which is a strong coupling (or so it seems) in the upper midrange making it sound "alive".
My guess is that the potting compound would help... others may wish to comment too?
Fwiw, I was not talking about "hum" I was referring to acoustic coupling, which is related to acoustic feedback as well as effecting the tonal qualities of the playback. Much like the effects of the arm materials and what Colin referred to when he (and others) discussed the sonic effects of the bearings.
What I mentioned is that IF the original arm was mounted on a movable sub-chassis that this would be a problem for this arm type, which relies upon having a very solid mounting to maintain the geometry and tracking. The solid mounting, however MAY be decoupled or coupled from/to the rest of the turntable. So, that granite chunk could be put on epoxy to the base, or mounted via a large surface area of appropriately high density rubber (for example), etc...
_-_-bear
I'd say anything that you can to to damp the path between that motor assembly (mounted to the sheet metal base now) and the rest of the world, the quieter the TT will be.
Having said all that, one of the things that folks who are going nuts over the old Garrard 301 seems to be the opposite, which is a strong coupling (or so it seems) in the upper midrange making it sound "alive".
My guess is that the potting compound would help... others may wish to comment too?
Fwiw, I was not talking about "hum" I was referring to acoustic coupling, which is related to acoustic feedback as well as effecting the tonal qualities of the playback. Much like the effects of the arm materials and what Colin referred to when he (and others) discussed the sonic effects of the bearings.
What I mentioned is that IF the original arm was mounted on a movable sub-chassis that this would be a problem for this arm type, which relies upon having a very solid mounting to maintain the geometry and tracking. The solid mounting, however MAY be decoupled or coupled from/to the rest of the turntable. So, that granite chunk could be put on epoxy to the base, or mounted via a large surface area of appropriately high density rubber (for example), etc...
_-_-bear
Bear
Lol, no I don't hate, thanks for giving me your time and opinions.
I think your right about redesigning the turn table. Ever heard the phrase "one job makes two" ? It so happens I do have a fair amount of granite off cuts lying around. So it can be done.
I will for the time being though, just get an arm going on my original idea. As I am ultimately going to abandon this plinth , it would be a waste of my potting compound. I will remove the suspension legs and use your sand box idea
Thanks Alan
Lol, no I don't hate, thanks for giving me your time and opinions.
I think your right about redesigning the turn table. Ever heard the phrase "one job makes two" ? It so happens I do have a fair amount of granite off cuts lying around. So it can be done.
I will for the time being though, just get an arm going on my original idea. As I am ultimately going to abandon this plinth , it would be a waste of my potting compound. I will remove the suspension legs and use your sand box idea
Thanks Alan
Hi Alan...more OT, but what turntable is that?
Stuey (lurking on this thread and getting very interested in this arm design).
Stuey (lurking on this thread and getting very interested in this arm design).
Stuey
Its a technics SL 1800 which I got very cheap off ebay. Its kind of like an early 1200/1210. Did various tests and long of the short is : its tone arm is knackered. So thought I would give Colin's idea ago.
Its a technics SL 1800 which I got very cheap off ebay. Its kind of like an early 1200/1210. Did various tests and long of the short is : its tone arm is knackered. So thought I would give Colin's idea ago.
As long as I am making trouble...
... one could mount the motor and switch assembly on suitable chunk of material, call it chunk A. Then mount the arm assembly (suitably built to size and fit) on material (could be different material), call it chunk B.
Now place chunk A and chunk B on top of ur sand. 😀
Simple and effective.
_-_-
PS check the load carrying ability of the motor+platter by adding on some mass and seeing if it comes up to speed
and runs on speed ok... too much mass will make it not run properly or need the speed controls turned too far to keep
it on speed. But within reason you *may* wish to carefully fill/coat the bottom of the existing platter with some of that
damping compound - just be careful to keep the amounts in each section (presuming a casting with ribs) as close to equal
in weight/volume as you can.
even better... 😀
... one could mount the motor and switch assembly on suitable chunk of material, call it chunk A. Then mount the arm assembly (suitably built to size and fit) on material (could be different material), call it chunk B.
Now place chunk A and chunk B on top of ur sand. 😀
Simple and effective.
_-_-
PS check the load carrying ability of the motor+platter by adding on some mass and seeing if it comes up to speed
and runs on speed ok... too much mass will make it not run properly or need the speed controls turned too far to keep
it on speed. But within reason you *may* wish to carefully fill/coat the bottom of the existing platter with some of that
damping compound - just be careful to keep the amounts in each section (presuming a casting with ribs) as close to equal
in weight/volume as you can.
even better... 😀
Last edited:
Bear
I just been walking the dog thinking about the very same thing! I will hold fire for a minute and just get the arm up and running and have a little play around with it. It will all count as a practice run and some experience for doing your idea. Besides It won't cost any more money to change to the granite idea and its nice to do upgrades little by little because you can savour the changes and see the magnitude of change of your modification....I am really hoping this arm comes up with the goods.
I just been walking the dog thinking about the very same thing! I will hold fire for a minute and just get the arm up and running and have a little play around with it. It will all count as a practice run and some experience for doing your idea. Besides It won't cost any more money to change to the granite idea and its nice to do upgrades little by little because you can savour the changes and see the magnitude of change of your modification....I am really hoping this arm comes up with the goods.
Hi Chokesrule,
A good turntable is a great thing, however this arm seems to perform well even on a Sansui sr222 budget oldie 🙂. I think you will find built well that this arm will deliver the goods and then some, it will dig up surprising amounts of information from the grooves 🙂.
Colin
A good turntable is a great thing, however this arm seems to perform well even on a Sansui sr222 budget oldie 🙂. I think you will find built well that this arm will deliver the goods and then some, it will dig up surprising amounts of information from the grooves 🙂.
Colin
- Home
- Source & Line
- Analogue Source
- DIY linear tonearm