Why would chipboard be better than two layers of ply? Is chipboard better than mdf?Or easier, a chipboard back to a birch ply baffle bonded with elastic glue
This thread gave me an idea! I'm already planning to front mount pro-audio drivers, with a polished aluminum ring to hide the flange and gasket....and securing the driver to the cabinet by bolting through ring, "sandwiching" the driver.
It would be easy for me to add a viscous rubber material to both sides of the driver's flange. (Probably remove the stock gasket.) Then the driver should be completely de-coupled from the cabinet?
It should be easy to do, and it shouldn't require any modifications to my design. So thanks guys! I don't know if it makes any difference practically, but doing it would take so little extra effort that I don't have an excuse not to!
It would be easy for me to add a viscous rubber material to both sides of the driver's flange. (Probably remove the stock gasket.) Then the driver should be completely de-coupled from the cabinet?
It should be easy to do, and it shouldn't require any modifications to my design. So thanks guys! I don't know if it makes any difference practically, but doing it would take so little extra effort that I don't have an excuse not to!
Between the drivers and cabinet just use something like a soft buna 50a cord it's cheap and easy to work with buy matching washers for the screws.
Any material would work is used the right Way. But if you use 21 mm Birch play and 2 mm lead, I bet that is waste.Has anybody thought about a 2mm layer of lead in between two sheets of birch ply? The plyboard isn’t very dense so this may be a way of adding mass to the baffle. Anybody tried it?
However, from my experience, glueing two sheets of material together makes for at better panel. Ie: 2x9 mm Birch glued together is better than 18 mm Birch ply.
I would strongly advise against the use of lead. There is a good reason it is banned in many circumstances.
Corkboard, if it is as i imagine, will add mass without stiffness moving potential resonances into territory they are more likely to get excited.
dave
It depends. I Got inspired from this speaker:
https://www.dagogo.com/lindemann-bl-10-bookshelf-speaker-review/
I suppose the lead would lower and even amplify the resonances. As far as i know the reason to use (strong) plywood in the first place is to get a light but stiff material to push resonances above enclosure/driver bandwidth.2mm layer of lead in between two sheets of birch ply?
Edit: the above is probably most valid for bass enclosures. Mid enclosures may be different, as the panel resonances are below useful bandwith. In this case lowering resonance frequencies and adding weigth may be useful.
Last edited:
I don't believe that more mass = better. There are lighter weight methods for making non-resonant panels. For example, tensioning the cabinet, or constrained mass damping.Any material would work is used the right Way. But if you use 21 mm Birch play and 2 mm lead, I bet that is waste.
However, from my experience, glueing two sheets of material together makes for at better panel. Ie: 2x9 mm Birch glued together is better than 18 mm Birch ply.
I would strongly advise against the use of lead. There is a good reason it is banned in many circumstances.
I've been dreaming about endgrain balsa core composite panels, so endgrain balsa in the middle of the panel, with thin plywood on either side. And then carbon fiber on both sides. I really want to do it, but I estimate it would be approx $600 in material to build, before the carbon fiber! I did some tests that indicate it should perform roughly the same or better than plywood. But I decided to just go ahead with MDF, since that is cheaper and simplifies construction. I mean, I kind of want to finish the speakers!
(notwithstanding the three ~stalled projects I have in my garage because somehow I have less time now than when I was going to work every day ???)Before going full out on such a project, it would be interesting to take apart an existing speaker and replacing the baffle with the one suggested and measuring the effects. Unfortunately I don't have a set of speakers lying around waiting to be hacked.
If you are measuring differences and considering using a different configuration/geometry, wouldn't knocking together a simple sealed box suffice?
I'm curious and interested in this speaker's unique cabinet build:It depends. I Got inspired from this speaker:
https://www.dagogo.com/lindemann-bl-10-bookshelf-speaker-review/
9mm ply + 4mm corkboard + 9mm ply constrained mass damping.
I wonder how effective it is?
lindemann-bl-10-bookshelf-speaker
Not lined with cork. Cork sandwiched by 2 layers of ply. Very different. A version of constarined layer.
Relatively light cabinets but with very stiff walls
Sounds like one of mine.
dave
Edit: the above is probably most valid for bass enclosures. Mid enclosures may be different, as the panel resonances are below useful bandwith
Given that the amount of energy to excite a (potential) resonance decreases quite dramatically with frequency. So the technique has been shown to work with single FR speakers. I would not do a mid enclosure any different.
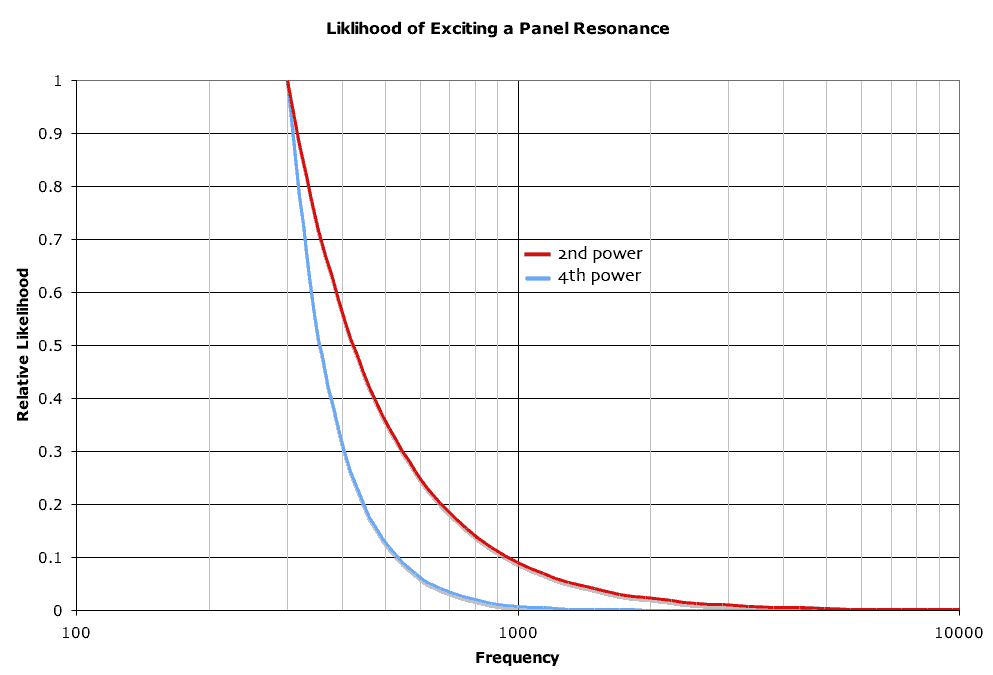
dave
Yes. Cabinet only Lined with cork would not Work 🙂Not lined with cork. Cork sandwiched by 2 layers of ply. Very different. A version of constarined layer.
Sounds like one of mine.
dave
Lining a cabinet with cork might help absorb internal sound and stop it being transfered through the walls.
On my latest project, I glued felt to the inside, then glued carpet tile to the felt, in an attempt to do the same - and to see if it would dampen the MDF sides. To be honest, after knocking on the sides it doesn't seem to have made a lick of difference in regard to damping, but it's restricted to a small area due to bracing.
On my latest project, I glued felt to the inside, then glued carpet tile to the felt, in an attempt to do the same - and to see if it would dampen the MDF sides. To be honest, after knocking on the sides it doesn't seem to have made a lick of difference in regard to damping, but it's restricted to a small area due to bracing.
Would it make a competent speaker? I think yes. Is it "the best" combination of materials? Hard to tell.I'm curious and interested in this speaker's unique cabinet build:
9mm ply + 4mm corkboard + 9mm ply constrained mass damping.
I wonder how effective it is?
I wanted to try the concept, but I decided against doing it because diminishing returns. It costs more and introduces a lot of complexity.
It will work. Hard to do right. I figure that one can get just as effectve a cabinet with less work.
dave
dave
Yeah it is complicated. And gets expensive with linoleum. But who dont want antistatic properties ;-)
I found that PVA Glue bonded just fine to cork - in perfect World I would have used a Glue that is a bit softer.
I have seen vintage drivers that have a gasket made of cork. At least 50 years Old. It looked brand spanking new.
Anyway i May shifted thread to OT. But my point is still that I think cork Work Great for gasket in some situations.
I found that PVA Glue bonded just fine to cork - in perfect World I would have used a Glue that is a bit softer.
I have seen vintage drivers that have a gasket made of cork. At least 50 years Old. It looked brand spanking new.
Anyway i May shifted thread to OT. But my point is still that I think cork Work Great for gasket in some situations.
I've always wondered about this, everyone is so engross in building a dead cabinets but I don't think I've read any thread on
preventing sound within the cabinet from reflecting onto the back of speaker cone. Isn't this far more important ?
preventing sound within the cabinet from reflecting onto the back of speaker cone. Isn't this far more important ?
3 inchs of melamine will handle that add in a lot very well fluffed wool and you should be fine.
augerpro did a great and extensive study on various ways to reduce resonances in box construction "A Monster Box Construction Methods Project" here https://www.somasonus.net/box-construction-methods. He used SPL measurements to show the difference between various approaches. His results were discussed in the diyaudio thread here: https://www.diyaudio.com/community/threads/a-monster-construction-methods-shootout-thread.356130/
- Home
- Loudspeakers
- Full Range
- Baltic Birch and rubber baffle