Hello David,
You may not be familiar with published figures for stiction/friction in tonearms. To give you a few examples:
Technics EPA 500: <7mg in either plane
Fidelity Research FR64S: 20mg in the lateral plane(actual measurement by HIFI EXCLUSIV magazine around 1980)
Dual ULM arms: <15mN, lateral
should be in Newton all the time, but....
The first and the last arm were supposed to be used with high compliance carts...
The FR arm has (supposedly) very high quality bearings...
So no more than 3,5mg for the LT arm isn't exactly "considerable friction" when the (typically non-linear) force(generated by the cartridge, - causing lateral cantilever displacement) required to bend the wiring in air bearing tonearms far exceeds this value.
The 3,5mg figure is for the lateral and forward movement combined....
The vertical bearings are essentially frictionless. Only the force that is needed to bend the wiring can be measured.
Cheers,
Frank
You may not be familiar with published figures for stiction/friction in tonearms. To give you a few examples:
Technics EPA 500: <7mg in either plane
Fidelity Research FR64S: 20mg in the lateral plane(actual measurement by HIFI EXCLUSIV magazine around 1980)
Dual ULM arms: <15mN, lateral
should be in Newton all the time, but....
The first and the last arm were supposed to be used with high compliance carts...
The FR arm has (supposedly) very high quality bearings...
So no more than 3,5mg for the LT arm isn't exactly "considerable friction" when the (typically non-linear) force(generated by the cartridge, - causing lateral cantilever displacement) required to bend the wiring in air bearing tonearms far exceeds this value.
The 3,5mg figure is for the lateral and forward movement combined....
The vertical bearings are essentially frictionless. Only the force that is needed to bend the wiring can be measured.
Cheers,
Frank
I'm trying to wrap my head around how, say, an air bearing doesn't have this feature even though you place the 30mm vs 100mm in the same camp. They're in different camps. One has no friction (air) across the record and yours needs considerable friction (bearings and forward arc) to accomplish the same thing in its 30mm requirement.
All air-bearing tonearms use a form of horizontal LINEAR bearing, regardless of friction or not, air or no air, the stylus has to carry the entire mass of the carriage horizontally so the horizontal mass is enormous compare to typical pivot tonearms. Even if there's no carriage the mass of the cartridge body still has to be accounted for which is around, say, 10 grams. So, now compare that to the figure given by Frank, that is, 3.5mg! Hope you get the picture.
Thanks for chiming in.
That's an apples and oranges comparison. The 3.5 mg is a poor way of expressing a force of 35μN (micronewton)*. This is the amount of force that is required before the arm starts to move, and as Frank says, this is exceptionally low.
The same force applied to a mass of 10 g would accelerate it at about 2.9 x 10^-3 m.s^-2 if no friction were present.That's line ball with the peak acceleration when tracking a 2mm eccentricity.
* Frank said himself the forces should be in Newtons but he used the units given in the specs to avoid confusing people. Unfortunately this confused some people.
The same force applied to a mass of 10 g would accelerate it at about 2.9 x 10^-3 m.s^-2 if no friction were present.That's line ball with the peak acceleration when tracking a 2mm eccentricity.
* Frank said himself the forces should be in Newtons but he used the units given in the specs to avoid confusing people. Unfortunately this confused some people.
Last edited:
micronewton
Thanks for the correction, Mark!
Just curious... what would be the typical "micronewton" or the "amount of force that is required before the arm starts to move" in some of the popular air bearing tonearms, say, the ET2, Kuzma Airline, and Transfi Terminator?
Thanks for the correction, Mark!
Just curious... what would be the typical "micronewton" or the "amount of force that is required before the arm starts to move" in some of the popular air bearing tonearms, say, the ET2, Kuzma Airline, and Transfi Terminator?
2 mm eccentricity is, maybe, to extreme. But it seems, that even with more common 0.5mm eccentricity, lateral forces applied to stylus (for pure mechanical linear arms) should be worse, than inside (skating) force with average pivot arms, canceling imaginary advantages. Am I right?
Last edited:
Thanks for the correction, Mark!
Just curious... what would be the typical "micronewton" or the "amount of force that is required before the arm starts to move" in some of the popular air bearing tonearms, say, the ET2, Kuzma Airline, and Transfi Terminator?
That's the orange in the apples and oranges comparison. Air bearings are to all intents and purposes frictionless.
2 mm eccentricity is, maybe, to extreme. But it seems, that even with more common 0.5mm eccentricity, lateral forces applied to stylus (for pure mechanical linear arms) should be worse, than inside (skating) force with average pivot arms, canceling imaginary advantages. Am I right?
I'm not sure I understand your question.
The lateral force required to accelerate a frictionless linear bearing of a given mass through a given amplitude at a known frequency is easily calculated, it's simply m x A x ω. A is single ended amplitude eg centre to peak, obviously if you have peak to peak divide by two. ω is of course in radians per second, for a record at 33 rpm take it as 3.5.
For a pivoted bearing of any type, substitute the effective mass in the plane of relevance, then add the static friction to the output of the equation.
Now we are comparing like with like.
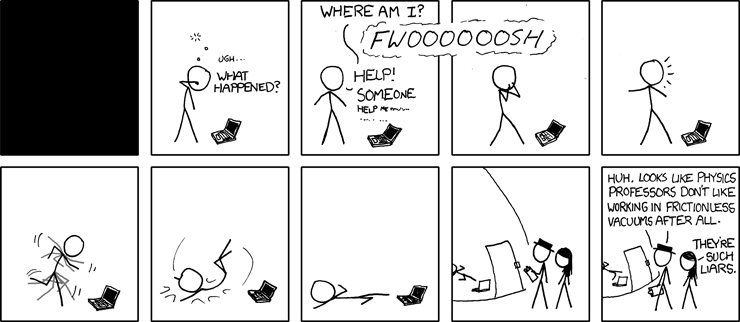
Last edited:
Hi,
Not sure I should reply, but to clear things up(hopefully):
There is stiction, which is(can be) a function of the bearings and, more often than not, the wiring.
Imagine a braided or twisted wiring. When you bend it, it will not "follow" the applied force smoothly, but the "rubbing" conductors will break loose from each other, than bend until stiction(static friction) has been over come - and so on...
Same for wiring that is guided through the arm-bearing shaft. Most of the time, it "rubs".
To overcome this stiction, or simply to bend the wiring, the displacement of the cantilever can reach values quite a bit higher(!) than what is caused by a skating compensation mechanism(skating force varies between 4 and 18% of the VTF).
Such a displacement obviously causes a suspension asymmetry in the lateral plane, reducing dynamic range(bass in particular) and a loss of resolution. Imaging is affected, but much more a function of crosstalk symmetry.
Air bearings, as Mark said, are stiction-free, but the wiring issues are (nearly) unavoidable. A servo, moving the attachment point of the wiring along with an air-bearing arm, would solve this issue(for the lateral plane mostly).
Then there is cantilever displacement due to eccentric records. Unavoidable with linear arms that have a high eff. mass laterally. A pivoted arm wins in this department. Well, maybe with the exception of the Dynavector arms....
In my view, it is not the tracing error that potentially yields the greatest benefit in linear tracking arms, but the reduction of the lateral preload on the cantilever that could be achieved through proper execution.
Anyway, no arm sounds better than another just because it features frictionless bearings. A tonearm cartridge combination is WAAAYY to complex a system to define quality based on that(or any other, single) parameter alone.
Cheers,
Frank
Not sure I should reply, but to clear things up(hopefully):
There is stiction, which is(can be) a function of the bearings and, more often than not, the wiring.
Imagine a braided or twisted wiring. When you bend it, it will not "follow" the applied force smoothly, but the "rubbing" conductors will break loose from each other, than bend until stiction(static friction) has been over come - and so on...
Same for wiring that is guided through the arm-bearing shaft. Most of the time, it "rubs".
To overcome this stiction, or simply to bend the wiring, the displacement of the cantilever can reach values quite a bit higher(!) than what is caused by a skating compensation mechanism(skating force varies between 4 and 18% of the VTF).
Such a displacement obviously causes a suspension asymmetry in the lateral plane, reducing dynamic range(bass in particular) and a loss of resolution. Imaging is affected, but much more a function of crosstalk symmetry.
Air bearings, as Mark said, are stiction-free, but the wiring issues are (nearly) unavoidable. A servo, moving the attachment point of the wiring along with an air-bearing arm, would solve this issue(for the lateral plane mostly).
Then there is cantilever displacement due to eccentric records. Unavoidable with linear arms that have a high eff. mass laterally. A pivoted arm wins in this department. Well, maybe with the exception of the Dynavector arms....
In my view, it is not the tracing error that potentially yields the greatest benefit in linear tracking arms, but the reduction of the lateral preload on the cantilever that could be achieved through proper execution.
Anyway, no arm sounds better than another just because it features frictionless bearings. A tonearm cartridge combination is WAAAYY to complex a system to define quality based on that(or any other, single) parameter alone.
Cheers,
Frank
Is it possible to avoid rigid wires, like here, still using well sounding ones? Back to 70-th and 80-th tone arm wires usually were thin and extremely flexible, and nowadays it looks opposite. Missing the point of high quality arm bearings and rest of hassle, if wire resistance measures in grams. Strangely it looks like nobody cares, except Mr. Shroder recent post...Sorry for naїve post.
Attachments
I don't see a reduction in lateral preload In your design but an increase. The foundation that is fixed in other designs and split with its tradeoffs involved, is a moving requirement placed on the cantilever in your design.
The cartoon friend in the illustration is placed in a frictionless vacuum chamber, but with your design the entire chamber must move at all times to accomplish what an air bearing or fixed foundation For example, splits.
Vertical and horizontal impedances are seperate in air bearimgs here, but your design requirement must include global mass to make it funtion to the same plane.
I see more stress on the cantilever system because your foundation must move to perform its duty. There is no rest period at all but a constant competing with stlylus movement at all times.
Whether this additional constant "arc" movement requirement floating along side the cantilever movement is totally seperate and transparent is something I would like to hear.
Are you displaying this arm at the upcoming CES in Vegas as this is most interesting and unique
Regards
David
The cartoon friend in the illustration is placed in a frictionless vacuum chamber, but with your design the entire chamber must move at all times to accomplish what an air bearing or fixed foundation For example, splits.
Vertical and horizontal impedances are seperate in air bearimgs here, but your design requirement must include global mass to make it funtion to the same plane.
I see more stress on the cantilever system because your foundation must move to perform its duty. There is no rest period at all but a constant competing with stlylus movement at all times.
Whether this additional constant "arc" movement requirement floating along side the cantilever movement is totally seperate and transparent is something I would like to hear.
Are you displaying this arm at the upcoming CES in Vegas as this is most interesting and unique
Regards
David
Hi David,
I did travel extensively this year and will likely skip CES(sorry).
I'm afraid you didn't grasp the function of this arm to its full extent.
There is essentially NO sidethrust on the cantilever at any time.
When set on a blank(not just zero modulation groove) record, the slightest blow(too strong a word) will move the arm in either direction, depending on the direction of the oncoming "whiff". An air bearing arm will typically move just as or more easily, but then return to a position on the blank disc that is defined by the wiring exhibiting zero force.
An Orsonic side thrust checker and a straingauge cartridge(which comes in handy for such experiments, since its a displacement sensor) show no side thrust(non-or modulated groove) higher than that caused by bearing friction, which as mentioned above, is lower than practically all other arm utilizing captive bearings.
And there is no antiskating mechanism acting on the arm.....
I realize it's hard to believe, but enough people that were doubtful have heard and seen it 🙂
All the best,
Frank
I did travel extensively this year and will likely skip CES(sorry).
I'm afraid you didn't grasp the function of this arm to its full extent.
There is essentially NO sidethrust on the cantilever at any time.
When set on a blank(not just zero modulation groove) record, the slightest blow(too strong a word) will move the arm in either direction, depending on the direction of the oncoming "whiff". An air bearing arm will typically move just as or more easily, but then return to a position on the blank disc that is defined by the wiring exhibiting zero force.
An Orsonic side thrust checker and a straingauge cartridge(which comes in handy for such experiments, since its a displacement sensor) show no side thrust(non-or modulated groove) higher than that caused by bearing friction, which as mentioned above, is lower than practically all other arm utilizing captive bearings.
And there is no antiskating mechanism acting on the arm.....
I realize it's hard to believe, but enough people that were doubtful have heard and seen it 🙂
All the best,
Frank
Oh I get it, just projecting out.
I am very impressed and of course there will be those that will want to clone like me eventually🙂
Regards
David
I am very impressed and of course there will be those that will want to clone like me eventually🙂
Regards
David
Burne-Jones tonearm
.
Here's another curiosity and one of the earliest designs of this genre, the Burne-Jones tonearm.
.
.
Here's another curiosity and one of the earliest designs of this genre, the Burne-Jones tonearm.
An externally hosted image should be here but it was not working when we last tested it.
An externally hosted image should be here but it was not working when we last tested it.
An externally hosted image should be here but it was not working when we last tested it.
An externally hosted image should be here but it was not working when we last tested it.
An externally hosted image should be here but it was not working when we last tested it.
An externally hosted image should be here but it was not working when we last tested it.
An externally hosted image should be here but it was not working when we last tested it.
An externally hosted image should be here but it was not working when we last tested it.
An externally hosted image should be here but it was not working when we last tested it.
.
Hi,
This is the "father" of the VanEps and the Thales Simplicity arm(but not the Zero 100). Already the more "refined" Super 90 version. The simpler model can be picked up for a song and "pimped" to perform surprisingly well. In its stock form it makes for a nice display item.
Have a great weekend,
Frank
This is the "father" of the VanEps and the Thales Simplicity arm(but not the Zero 100). Already the more "refined" Super 90 version. The simpler model can be picked up for a song and "pimped" to perform surprisingly well. In its stock form it makes for a nice display item.
Have a great weekend,
Frank
nicely done Frank.
As a fledgeling tonearm "designer", I love the simplicity of the design.
Which suggests the drag is very minor. Consider the lateral forces that act on a stylus tip and how those lateral forces can effect tracking and tracking error.
Not me😉. All should look at the non-offset headshell closely and go back to first principles. I've recently read a review of a "zero offset" tonearm. If you do a little calculus of derivatives of the known equations and the answer should sort of "pop out" at you.
As Einstein stated " Make everything as simple as possible, but not simpler." I think that about says it all. Nicely done Frank.
As a fledgeling tonearm "designer", I love the simplicity of the design.
Hi,
I can demo(did that many a time by now) that the arm(when set up properly) will remain stationary once set down on a blank disc(irrespective of VTF!!!)... a mild blow will move it across the disc though(either way).
Which suggests the drag is very minor. Consider the lateral forces that act on a stylus tip and how those lateral forces can effect tracking and tracking error.
(@alighiszem):Your analysis is semi-correct, but there is more to the design than what is visible in the pics. Even if what you describe would be all there is, the resulting skating force would maximally be less than 1/3rd of an arm of comparable eff. length(offset angle accordingly).
Is no-one building a clone yet? 🙂
Not me😉. All should look at the non-offset headshell closely and go back to first principles. I've recently read a review of a "zero offset" tonearm. If you do a little calculus of derivatives of the known equations and the answer should sort of "pop out" at you.
The patents cited are mostly based on the Thales circle(one arm features an offset angle). My design doesn't depend on it.
The guide/control mechanisms are all friction laden (or too massive), require an electrical circuit or/and are complicated as hell.
All the best,
Frank
As Einstein stated " Make everything as simple as possible, but not simpler." I think that about says it all. Nicely done Frank.
Schröder LT YouTube video
.
Video from the RMAF 2013 explaining the arm's mechanism and movement.
<RMAF 2013: check video from 1:50 to 2:43>
Something from the previous year.
<RMAF 2012: Schröder LT tonearm in action>
I think after seeing the video clips, you will get a better understanding. Ingenious, indeed!
.
.
Video from the RMAF 2013 explaining the arm's mechanism and movement.
<RMAF 2013: check video from 1:50 to 2:43>
Something from the previous year.
<RMAF 2012: Schröder LT tonearm in action>
I think after seeing the video clips, you will get a better understanding. Ingenious, indeed!
.
Schröder LT YouTube video
.
Video from the RMAF 2013 explaining the arm's mechanism and movement.
<RMAF 2013: check video from 1:50 to 2:43>
Something from the previous year. (I included the wrong link on the previous post. Here's the correct one.)
<RMAF 2012: Schröder LT tonearm in action>
I think after seeing the video clips, you will get a better understanding. Ingenious, indeed!
.
.
Video from the RMAF 2013 explaining the arm's mechanism and movement.
<RMAF 2013: check video from 1:50 to 2:43>
Something from the previous year. (I included the wrong link on the previous post. Here's the correct one.)
<RMAF 2012: Schröder LT tonearm in action>
I think after seeing the video clips, you will get a better understanding. Ingenious, indeed!
.
Schröder LT hi-rez pictures
The good people at another forum posted some high resolution images of an Schröder LT tonearm that is in current production. Check out particularly the first picture below that shows the magnetic guiding mechanism. Slightly modified from the earlier version but still the same concept. Just brilliant!
.
The good people at another forum posted some high resolution images of an Schröder LT tonearm that is in current production. Check out particularly the first picture below that shows the magnetic guiding mechanism. Slightly modified from the earlier version but still the same concept. Just brilliant!
As quoted from Frank's own words in one post on 12-04-2013:
- - - - - - - - - - - - - - - - - - - - - - - - - - - - - - - - - - - - - - - - -
Hello gentlemen,
I think I may be able to shed some light on a few issues discussed in this thread.
First of all, a US patent for the mechanism that is the heart of this tonearm has been granted on Nov. 5th. In addition, it is protected under design copyright law in the EU.
The use of this arm on any softly suspended deck(like a Linn LP12, Oracle Delphi, Voyd....) is less than optimal. Just like any tonearm - and airbearing tonearms in particular - the arm needs to be leveled(a provision for which is "hidden" in the arm base) or else the advantage of no side thrust generation (lack of skating force) will be jeopardized as, similar the an air bearing "sled", the pivoted arm will find a gravitational "null" or resting position. It's not as pronounced an issue as with airbearing arms as the mass displacement is a lot smaller, but still...
Tangency is maintained through a vector addition. Lateral tonearm displacement (and frictional pull) will move the fixed outrigger underneath the main arm bearing to which a magnet is attached. That magnet always maintains minimum proximity to the ferromagnetic "guide-rail" above, yet never touches it. So for any given angle that the main tonearm assumes, the pivoting bar is forced to move so that the magnet stays as close to the bar as possible.
Yes, that mechanism needs excellent, in fact, the very best bearings one can buy. The total bearing friction in the lateral plane(<3,5mN) is lower than ANY other conventional tonearm with captive bearings. In the vertical bearings, friction is ZERO, as in unmeasurable/waaay below what the wiring is contributing.
The slightest whiff will move the arm across a blank record, and a hair, gently put on the headshell while the arm is in equilibrium, will displace it. Yet there is NO play in any of the bearings in operation.
No skating compensation is required, even if set up with a little less care than what one should apply, side thrust on the cantilever can be brought down to unprecedented low levels. This means that it now takes the same amount of force to displace the cantilever laterally in either direction from center(all bass below 80-100Hz is mono on LPs), increasing linearity/dynamics/extension.
The eff. length was not chosen arbitrarily, but yields the best combination of geometry and associated forces. Longer wouldn't result in less tracing error(so why do it?), shorter forces the displacement of the pivoting bar to increase, requiring more force.
Sorry if this reads like an advertising pamphlet, it isn't supposed to be one...
And I'm really happy that, so far, people who spent their hard earned money on this, really seem to "get" it! 🙂
Forgive me for stopping short of revealing everything that contributes to the fidelity of this arm, as I like to reduce the risk of plagiarism to a manageable level 🙂
Happy listening!
Frank Schröder
An externally hosted image should be here but it was not working when we last tested it.
An externally hosted image should be here but it was not working when we last tested it.
An externally hosted image should be here but it was not working when we last tested it.
An externally hosted image should be here but it was not working when we last tested it.
An externally hosted image should be here but it was not working when we last tested it.
An externally hosted image should be here but it was not working when we last tested it.
An externally hosted image should be here but it was not working when we last tested it.
.
DD,
Thanks as always. Your photo sleuthing is one of the highlights of this forum and the underneath shot is a gem.
But little things keep getting changed. How are would-be cloners supposed to keep up? (Little DIWhining, there.)
Thanks as always. Your photo sleuthing is one of the highlights of this forum and the underneath shot is a gem.
But little things keep getting changed. How are would-be cloners supposed to keep up? (Little DIWhining, there.)
Thanks as always. Your photo sleuthing is one of the highlights of this forum and the underneath shot is a gem.
It's my pleasure. A picture is worth a thousand words, indeed. Sometimes you can write till you are blue in the face and still cannot convey an idea better than a simple picture. The internet is so full of pictures that I'm surprised people don't post more in forums. If nothing else, I hope at least this thread provides some entertainment. 🙂
But little things keep getting changed. How are would-be cloners supposed to keep up? (Little DIWhining, there.)
DIYers are supposed to be able to deal with change! 😀
- Home
- Source & Line
- Analogue Source
- Angling for 90° - tangential pivot tonearms