FRENCH GUARD: "No. Now, go away, or I shall taunt you a second time-a!" It may also involve mothers being hamsters, as well as elderberries.Not at all.
But gibberish calls for a taunting.
Please look up Dunning-Kruger.
At lower frequencies its pistonic and higher frequencies its modal. Its common knowledge.
The rocking motion is solved by adding a spine to the back of the exciters magnet. Problem solved hence the BMR driver was developed.
The rocking motion is solved by adding a spine to the back of the exciters magnet. Problem solved hence the BMR driver was developed.
The Brits are pretty good at mudding the waters...
View attachment 1138330 View attachment 1138327
patents are...
Thank you for all those patent links, will read them.The thing is, the voice coil shouldn't move the panel, the exciter must only transfer the vibrations. This is the tricky part. Have a look at all those patents, I posted in the post #9,094. Might help.
Oh yes!
You should contact him personally. Ask him. 🙂
That was my first project, full range dml. Flexible wind insulation board, high damping, exciter in the middle, viscoelastic foam around perimeter, with auto eq calibration.
Last edited:
So the panel doesn't move - it's immobile and yet vibrating at the same time .... magic stuff indeed!!The thing is, the voice coil shouldn't move the panel, the exciter must only transfer the vibrations.
So , without referring to any more patents - in your OWN words, please clearly explain how to achieve the 'tricky part' so we can all breathe a sigh of profound relief and move on... ie- how a dumb exciter, the coil of which only knows how to move in and out and is firmly fixed to the panel, can manage to pass on vibrations caused by said moving in and out without the panel following the movement of the exciter coil at the point of fixing. And pray tell how does one construct a bending wave panel without displacing areas of the panel relative to surrounding areas.
I anxiously await my Eureka! epiphany moment
By all means read them with a clear mind but don't be 'Trumped'Thank you for all those patent links, will read them.
Audiofrenzy said:This is the reason Spedge and I also like smaller DML panels because smaller panels will focus the high frequencies.
Can you give an example of that size for 1" insulation foamboard?
In slow motion you can see that the whole frame moves, attention has to be made to make it rock solid and damped at the same time.
Best to make the spider(red) as stiff as possible, so that the coil former (blue) won't jump out, restricting the piston motion, if possible completely, so the coil former/bobbin won't be able to push the panel like a piston. If you look at the post #9,059, you'd notice that both AER bbx and Aiyima exciters have the spider fixed tight. They don't push the panel. The excitations/vibrations comes from the centre. The spider does not move. In Aiyima, for example, you screw the plate in the centre, or change the plate to a conical-headed screw. The whole idea of the DM exciter is not to let the coil former/bobbin move. The exciter ideas are here, #8,772 and here, #8,780 from one of those links I posted. For you too, @pixel1
Last edited:
Now I now what you mean, looked at your links and it reminds me of Tectonic Elements TEAX32C20-8. Have you tried it?View attachment 1138448
Best to make the spider(red) as stiff as possible, so that the coil former (blue) won't jump out, restricting the piston motion, if possible completely, so the coil former/bobbin won't be able to push the panel like a piston. If you look at the post #9,059, you'd notice that both AER bbx and Aiyima exciters have the spider fixed tight. They don't push the panel. The excitations/vibrations comes from the centre. The spider does not move. In Aiyima, for example, you screw the plate in the centre, or change the plate to a conical-headed screw. The whole idea of the DM exciter is not to let the coil former/bobbin move. The exciter ideas are here, #8,772 and here, #8,780 from one of those links I posted. For you too, @pixel1
I used scan+speak motor for my fourth full range dml project specifically because of long linear stroke and short, lightweight coil. Longer stroke gives more flexibility to eq low frequencies.
Carbon fibre/Aramid Honeycomb-Sandwich sheet ended up being too stiff for given panel size of 550 x 700 x 3.5 mm. With 60w and after eq there was no visible excursion and motor was overheating. To increase pistonic motion I started to trim the foam surround around perimeter. Before cutting the 1100 x 700 mm plate in half I tested it with Dayton exciter and it sounded better even without eq.
RTA measurements I made for myself with Iphone to test and compare and guide me in right direction. As soon as I get usb measurement microphone I will start to learn and can publish the data.
Attachments
Hi, Eucy.Man there's some complicated stuff going on in this and previous posts of yours ---chopped up scanspeak driver, tortuous cutouts, chambers, etc etc. I also note in the above photos that the rear of the panel has been totally covered by polyfoam to damp it.
Some explanation of the project/s design, aims and results would be welcomed
Eucy
My second panels were 300x200x1.5mm carbon fiber plates, too stiff for the size. Yes, self adhesive 3m Acoustic Thinsulate is glued to the rear, 21mm thick, 7kg/m3, very good broadband damping.
To give scientific results I have to collect enough measurement data, but I can comment on pictures. For a moment Im moving away from full range dml to small flexible panels with active bass with woofers.
Hmm,His was not a DM operation, but a pistonic operation with flat panels, Those were the days Yamaha's ear, Hitachi's HS-5000, Sony's APM, Technics X700s, All were pistonic with flat panels. Sony and Technics had honeycomb, Hitachi filled the cone with foam to make it flat, Bertagni and Yamaha used carved polystyrene. Nothing to do with DM oscillations.
I’m not convinced after reading the patent and review of the BES SM300 That it is a pistonic speaker. There are some comments on the dispersion of the sound from the speaker ”The sound had the open, airy quality that we have always associated with a good “omni” system, and there was a near-total lack of localization of the sound source even when one was quite close to one of the speaker panels. They sounded just as good off to the sides as to the front or rear.”
This is clear indication that this is a bending wave speaker not a pistonic. There is also some descriptions in the patent that suggest likewise.
An intresting aspect of the patent is that he has adressed a lot of the challenges with a bendingwave speaker with quite innovative solutions.
Thomas
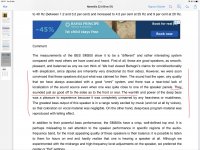
Attachments
Have a look at this video, you see for yourself. You can watch the video from the beginning, or from where I linked it.I’m not convinced after reading the patent and review of the BES SM300 That it is a pistonic speaker.
If the voice coil moves, then it is not a Distributed Mode exciter.I used scan+speak motor for my fourth full range dml project specifically because of long linear stroke and short, lightweight coil. Longer stroke gives more flexibility to eq low frequencies.
When you look at most full range CONE drivers they range from 2-8 inches. With DML's its double the size due to the flat surface, so around 4-16inches in the width while the height can be at most double so 8-32inches tall. This is my GENERAL rule.Can you give an example of that size for 1" insulation foamboard?
Most full range cone drivers are usually 4 inches when you look at famous brands like Fostex and Mark Audio. So IMO the standard width for DML's should be around 7or 8inches give or take a couple inches. The height can be equal to the width or at maximum double the width. I prefer 4-6inches more then the width.
So around 7-8inches for the width and 11-14inches for the height.
Again could you clearly write it is your understanding or assumptions? There is no demonstration, test or experiment here. I can agree on the fact that the relation between the panel stiffness and the exciter stiffness has not been highlighted enough but not on a spider as stiff as possible. A minimum of physics is needed with this kind of assertion. You even don't speak of the resulting bandwidth (here in LF).Best to make the spider(red) as stiff as possible, so that the coil former (blue) won't jump out, restricting the piston motion, if possible completely, so the coil former/bobbin won't be able to push the panel like a piston.
The voice coil is a force generator, force coming from the current in the magnetic field (M Lorentz or Laplace). This force acts against the voice coil mass, the spider stiffness, the panel stiffness.
If the spider is stiff, the force is simply wasted against it. The first mode will increase. The extreme being a fully blocked voice coil.
Is a glued voice coil a "stiff as possible" spider?
The voice coil doesn't jump by itself independently of the panel.
A too stiff panel leads to the same : no low frequency.
I won't use it : no bandwidth, no efficiencyI found this exciter, but there's no description in the patent. I suppose you will be able to understand how its made. Looks like it's supposed work on both skins, placed in a hole in the composite panel. It must be using very thin neodymium magnets, considering the panel should be around 3-5mm thick. It would be nice if someone can give any advice on this. Thanks.
View attachment 1133453
SIGH The spider does move. SMDH At high levels the voice coil will move the spider. You can easily test this by playing some heavy bass tracks at high levels and the voice coil will be moving like a piston along with the spider.View attachment 1138448
Best to make the spider(red) as stiff as possible, so that the coil former (blue) won't jump out, restricting the piston motion, if possible completely, so the coil former/bobbin won't be able to push the panel like a piston. If you look at the post #9,059, you'd notice that both AER bbx and Aiyima exciters have the spider fixed tight. They don't push the panel. The excitations/vibrations comes from the centre. The spider does not move. In Aiyima, for example, you screw the plate in the centre, or change the plate to a conical-headed screw. The whole idea of the DM exciter is not to let the coil former/bobbin move. The exciter ideas are here, #8,772 and here, #8,780 from one of those links I posted. For you too, @pixel1
What does that video prove????? 🙄 🤣Have a look at this video, you see for yourself. You can watch the video from the beginning, or from where I linked it.
Again you only think that DML's are modal and not pistonic when in FACT THEY ARE BOTH. To play low frequencies (around 150hz and under) the tranducer must be pistonic but to play mid to high frequencies the transducer must also be modal.
Last edited:
This is one of the problems some of you have. You think you have that minimum, while others don't. You've been here since December 2021, and you're still at it. You and few others still don't know what is this DM operation is.A minimum of physics is needed with this kind of assertion.
Does it matter to me? If you don't change your attitude, I won't be replying to you again. I won't be replying to DML..too. Good night!I won't use it : no bandwidth, no efficiency
- Home
- Loudspeakers
- Full Range
- A Study of DMLs as a Full Range Speaker