Tsardoz,Quick question here... I am about to finally try testing some panels of different materials. I have settled on 50x30 cm panel size due to some sheets I already have. The frame will be the same for each using foam on edges for support and the different materials will be swapped out using the same exciter.
The question is how do people mount the exciters so panels can be swapped? I am a bit loathe to use the supplied double sided tape as I dont think it is intended to be removed and reapplied. I will have some sort of wood mounting structure to support the exciter (to be determined) but wondering how to couple the exciter to the panel. I have an assortment of Dayton exciters to try out and have just ordered some of the Aiyamas from Aliexpress as well.
Panels will be
- 2mm Nomex honeycomb with wood veneer on each side
- 5mm end grain balsa
- 3mm bass wood plywood
I am thinking some sort of silicone or polyurethane sealer which has low strength. Of course once I decide on the best material I will use something stronger.
For now for me : the supplied double side tape (Dayton Audio) works fine. It allows to have the full band of the panel and you can remove the exciter using gently some blade. The panel may be damaged then. As I had some fear of a bad quality gluing, what I do is to apply watered PVA 10cmx10cm on the exciter area, sanding it, cleaning with alcohol. I let also 1 day the tape glue to operate before using the panel. Among all of that I don't know what is strictly necessary.
When removed, the original tape was not re-usable. So I removed it completely from the exciter with no damage.
To re-use the exciter I haven't found the right tape to do it. One pair was re-used with an epoxy glue. I am not sure I will be able to re-use it. A second pair was used for the quick tests described in the posts before. The double side tape I found is strong but created a limit in high frequency so not suitable for a complete panel tests. The more standard double side tape I tested was not strong enough. It seems Spedge has a better one. Refer to posts 2624 (p132), 4559 (p228) for information about the original 3M VHB and alternative. There are probably other posts.
Keep us informed
Christian
Thanks for the replies.
I am even thinking of hot melt glue... that stuff is generally pretty easy to remove but is more difficult to achieve a thin layer.
For testing purposes when comparing one panel type to another they should all share the same disadvantages.
I am even thinking of hot melt glue... that stuff is generally pretty easy to remove but is more difficult to achieve a thin layer.
For testing purposes when comparing one panel type to another they should all share the same disadvantages.
Tsardoz,Thanks for the replies.
I am even thinking of hot melt glue... that stuff is generally pretty easy to remove but is more difficult to achieve a thin layer.
For testing purposes when comparing one panel type to another they should all share the same disadvantages.
With the 3mm plywood, you should reach the 10k/20k with no problem (see the FR with plywood posted earlier). If it is not so it might be a question of glue.
Christian
#4657 About the SPL at 2m for different materials... part 2
@Veleric , @cheapvega , This post follows the posts #4201, 4203, 4256 about the role of the thickness.
So my tests about the SPL at distance for different materials, different thickness reach what was in previous posts : the "efficiency" is a characteristic of the material through the Young modulus E and the density rho.
In the plot below, I put the SPL measured in the test and E/rho³ estimated from the material data. It matches not too badly considering the uncertainty mainly about E.
In the plot
In the Piano Sound board thesis it is also written balsa is the wood with the highest E/rho³, not suitable for piano application because of the strength of the strings, but for DML why not, in addition considering the good results you have Eric (see #4270)
Christian
@Veleric , @cheapvega , This post follows the posts #4201, 4203, 4256 about the role of the thickness.
So my tests about the SPL at distance for different materials, different thickness reach what was in previous posts : the "efficiency" is a characteristic of the material through the Young modulus E and the density rho.
In the plot below, I put the SPL measured in the test and E/rho³ estimated from the material data. It matches not too badly considering the uncertainty mainly about E.
In the plot
- point on the left : acrylic
- central group : plywood 3, 4, 10mm
- right group : PS (EPS 20mm, XPS 20mm, XPS 9mm, XPS 5mm)
In the Piano Sound board thesis it is also written balsa is the wood with the highest E/rho³, not suitable for piano application because of the strength of the strings, but for DML why not, in addition considering the good results you have Eric (see #4270)
Christian
With the panel and exciter both hanging separately the only pressure on the tape should be the vibrating coil.
The conditions for all the panels would be the same.
There will probably be a slight hf roll off above 10k ,but the rest of the frequencies should be similar to when rigidly mounted.
This is just a method for quick and easy testing and works fine for short periods.
PVA glues exciters directly onto wood with no problems , I glued my exciters directly on to my rigid ply panels years ago and they are still ok.
If gluing onto metal or epoxy you must use some heat from a hair dryer or radiator or near a heat source.
not too much heat as this will make the pva bubble.
and give the glue plenty of time to dry, the hf will take a few more days after all this , before it starts to increase with drying.
Steve.
The conditions for all the panels would be the same.
There will probably be a slight hf roll off above 10k ,but the rest of the frequencies should be similar to when rigidly mounted.
This is just a method for quick and easy testing and works fine for short periods.
PVA glues exciters directly onto wood with no problems , I glued my exciters directly on to my rigid ply panels years ago and they are still ok.
If gluing onto metal or epoxy you must use some heat from a hair dryer or radiator or near a heat source.
not too much heat as this will make the pva bubble.
and give the glue plenty of time to dry, the hf will take a few more days after all this , before it starts to increase with drying.
Steve.
@homeswinghome very interesting data. Is that estimated SPL across a musical spectrum or at a specific frequency? I'd be curious to see the estimated spectral response for 3-4 thicknesses if possible. I'm certain my acrylic panels are prob a good 15-20dB less efficient at peak frequencies vs EPS....... but with the EQ necessary for a musical response, it's probably a wash overall.
Cheapvega,@homeswinghome very interesting data. Is that estimated SPL across a musical spectrum or at a specific frequency? I'd be curious to see the estimated spectral response for 3-4 thicknesses if possible. I'm certain my acrylic panels are prob a good 15-20dB less efficient at peak frequencies vs EPS....... but with the EQ necessary for a musical response, it's probably a wash overall.
It is the level in dBA (SPL meter) for a band limited pink noise (200 to 5kHz) as proposed by REW. So a kind of mean value across this band with the dBA filter shape (probably low action on this band).
My microphone is not calibrated. So don't read the values as absolute but only relative. To get an idea of the real value add perhaps something like 20dB.
I am not sure to have all the spectrums. I will check tomorrow what I have.
For the plywood, the 3mm is the largest one with 0,45x1.2m so its bandwidth is quiet large (for sure it is a panel I use). The 4mm or the 10mm are pieces of plywood I have, not as large as the 3mm one so because of their thickness, because of their area, their band was more limited but where they can play, they play almost at the same level. Same when the surface is divided (see post 4657). Some curves will help for sure.
"it's probably a wash overall " ??? Deepl or wordreference didn't help me... new vocabulary for me, what means?
Christian
@homeswinghome I didn't realize this was real data! That's great. Yes the curves would definitely help. Even if the mic isn't calibrated, as long as the same mic is used across all measurements we can see relative differences.
And "it's a wash" means the differences will probably be negligible, at least in the context of DSP correction. Though I may be wrong. For me the difference between ~6mm acrylic and ~3mm acrylic was a panel that was usable vs one that wasn't.
In any case I'm very interested in the response curves of your measurements, even over limited bandwidths.
And "it's a wash" means the differences will probably be negligible, at least in the context of DSP correction. Though I may be wrong. For me the difference between ~6mm acrylic and ~3mm acrylic was a panel that was usable vs one that wasn't.
In any case I'm very interested in the response curves of your measurements, even over limited bandwidths.
Christian,I tried to see a logic in that with the density and the Young modulus to have characteristics not linked to the geometry. This allows to sort the material in almost the order coming from the test but it doesn't completely fits as figure.
All of that is perhaps already known... it was not my case...
So if somebody as the knowledge or even an idea to link that to some physics, I'll appreciate.
Our favorite factor, D/mu^3, is independent of thickness for homogeneous materials. So that's why different thicknesses of the same material have similar efficiency. D is a function of thickness^3, and mu^3 is also a function of thickness^3, so D/mu^3 is independent of thickness.
I think I included the "homogeneous" worksheet in the file I sent you. You can see this effect there.
It's not exactly the same for composites. If you make two composite panels using the same skin thickness but different core thickness, D/mu^3 will be different for the two panels. But if you change the skin and core thicknesses in the same proportions (double them both for example), D/mu^3 will be the same for both.
Of course, even if the efficiency factor (D/mu^3) is the same, the Fc and F0 (fundamental for a particular size) will change as a factor of thickness. So changing thickness has an effect, just not on efficiency.
Eric
Thank you for the confirmation and the extension to composite Eric. When I wrote the post 4657, I was probably still in the tests or it was too late... It is really strange to see the level of the frequencies in the bandwidth to keep their level when you divide the area by too and another time by 2, by 2 again... up to 5 times and also after a piece of 4mm plywood not so large in dimensions you put on the test frame a 10mm plywood piece much larger (of course, it looses in low frequencies). I realized after that we already exchanged on that with E/rho³ or D/mu³ which is almost the same and that it fits not too bad with the recorded SPL. This is post 4664.Christian,
Our favorite factor, D/mu^3, is independent of thickness for homogeneous materials. So that's why different thicknesses of the same material have similar efficiency. D is a function of thickness^3, and mu^3 is also a function of thickness^3, so D/mu^3 is independent of thickness.
I think I included the "homogeneous" worksheet in the file I sent you. You can see this effect there.
It's not exactly the same for composites. If you make two composite panels using the same skin thickness but different core thickness, D/mu^3 will be different for the two panels. But if you change the skin and core thicknesses in the same proportions (double them both for example), D/mu^3 will be the same for both.
Of course, even if the efficiency factor (D/mu^3) is the same, the Fc and F0 (fundamental for a particular size) will change as a factor of thickness. So changing thickness has an effect, just not on efficiency.
Eric
Christian
Christian,
You asked about the frequency response of my balsa plywood panel. I know I mentioned it before, but I don't think I posted the data, so here it is.
The panel is roughly 406 mm x 600 mm, supported by foam around the perimeter just like my "revply" speaker. Also, it's the same exciter(s), DAEX25FHE-4. The exciter was placed approximately in the 40/40 position. Shown are results for a single exciter and two exciters. As you can see, the response is quite similar in this case. In the two exciter case, the second exciters was placed in a "mirror image" position.
I made the panel by gluing together three layers of balsa, with each about 1.6 mm thick. The grain runs in the long direction of the panel on the outer layers, and in the perpendicular direction for the center layer. I used spray adhesive to attach the layers together.
It has pretty good efficiency, much better then plywood, but not as much as the carbon/balsa. Maybe halfway in between if I recall correctly. But the best thing about it is that it simply has a very pleasant sound quality. I don't know exactly why, but it just sounds very pleasant to my ear.
Obviously it lacks bass and has that nasty dip from 250 to 400 Hz, so that's not great. But I don't think those features are really the fault of the balsa material. Generally, I think for most panels (including this one) much of the frequency response below about 500 Hz is the result of the panel size, aspect ratio, perimeter treatment, and exciter placement. So probably the bass response and the nasty dip could both be improved lot optimizing those other factors for the panel. The challenge is that balsa is a lot more expensive than regular plywood, so I have not so far tried other panels sizes, etc as yet.
Eric
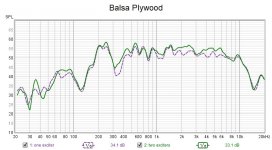
You asked about the frequency response of my balsa plywood panel. I know I mentioned it before, but I don't think I posted the data, so here it is.
The panel is roughly 406 mm x 600 mm, supported by foam around the perimeter just like my "revply" speaker. Also, it's the same exciter(s), DAEX25FHE-4. The exciter was placed approximately in the 40/40 position. Shown are results for a single exciter and two exciters. As you can see, the response is quite similar in this case. In the two exciter case, the second exciters was placed in a "mirror image" position.
I made the panel by gluing together three layers of balsa, with each about 1.6 mm thick. The grain runs in the long direction of the panel on the outer layers, and in the perpendicular direction for the center layer. I used spray adhesive to attach the layers together.
It has pretty good efficiency, much better then plywood, but not as much as the carbon/balsa. Maybe halfway in between if I recall correctly. But the best thing about it is that it simply has a very pleasant sound quality. I don't know exactly why, but it just sounds very pleasant to my ear.
Obviously it lacks bass and has that nasty dip from 250 to 400 Hz, so that's not great. But I don't think those features are really the fault of the balsa material. Generally, I think for most panels (including this one) much of the frequency response below about 500 Hz is the result of the panel size, aspect ratio, perimeter treatment, and exciter placement. So probably the bass response and the nasty dip could both be improved lot optimizing those other factors for the panel. The challenge is that balsa is a lot more expensive than regular plywood, so I have not so far tried other panels sizes, etc as yet.
Eric
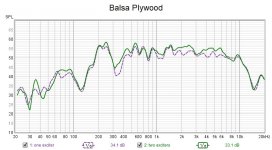
Thank you EricChristian,
You asked about the frequency response of my balsa plywood panel. I know I mentioned it before, but I don't think I posted the data, so here it is.
The panel is roughly 406 mm x 600 mm, supported by foam around the perimeter just like my "revply" speaker. Also, it's the same exciter(s), DAEX25FHE-4. The exciter was placed approximately in the 40/40 position. Shown are results for a single exciter and two exciters. As you can see, the response is quite similar in this case. In the two exciter case, the second exciters was placed in a "mirror image" position.
I made the panel by gluing together three layers of balsa, with each about 1.6 mm thick. The grain runs in the long direction of the panel on the outer layers, and in the perpendicular direction for the center layer. I used spray adhesive to attach the layers together.
It has pretty good efficiency, much better then plywood, but not as much as the carbon/balsa. Maybe halfway in between if I recall correctly. But the best thing about it is that it simply has a very pleasant sound quality. I don't know exactly why, but it just sounds very pleasant to my ear.
Obviously it lacks bass and has that nasty dip from 250 to 400 Hz, so that's not great. But I don't think those features are really the fault of the balsa material. Generally, I think for most panels (including this one) much of the frequency response below about 500 Hz is the result of the panel size, aspect ratio, perimeter treatment, and exciter placement. So probably the bass response and the nasty dip could both be improved lot optimizing those other factors for the panel. The challenge is that balsa is a lot more expensive than regular plywood, so I have not so far tried other panels sizes, etc as yet.
Eric
View attachment 1025446
Did you make this measurement in the same conditions as the CF/balsa or revplywood? I think about the distance from walls.
In the one exciter condition, is it really only one glued on the panel or the second one not connected but mechanically linked to the panel? what I notice is the low level above 10kHz.
Christian
Cheapvega,@homeswinghome I didn't realize this was real data! That's great. Yes the curves would definitely help. Even if the mic isn't calibrated, as long as the same mic is used across all measurements we can see relative differences.
And "it's a wash" means the differences will probably be negligible, at least in the context of DSP correction. Though I may be wrong. For me the difference between ~6mm acrylic and ~3mm acrylic was a panel that was usable vs one that wasn't.
In any case I'm very interested in the response curves of your measurements, even over limited bandwidths.
Here is what I have. There is more about the area reduction than about the thickness effect you would like to see
In the same test cession, I made 3 tests :
- the spectral contamination (see 4656). Here the signal with the 30 frequencies is played by Audacity to the DAC, the spectrum is displayed by the REW RTA
- the "efficiency". REW plays a band limited pink noise (200 to 5kHz); The mean level is given by the SPL meter of REW. It is just a value. No record
- for specific case, I didn't think to do it at the beginning of the test, I checked the spectrum with a full range pink noise. It is what is below.
The effect of the panel dimension (XPS 9mm)
- 1 orange 60x40cm. SPLmeter says 55.3dB (I see showing that here, the scales seem not the same. i don't know why...)
- 2 light blue 30x40cm. SPLmeter = 56.3dB
- 3 green 30x20cm. SPLmeter = 56.7dB
- 4 red 15x20cm. SPLmeter = 58dB
- 5 purple 15x10cm. SPLmeter = 56.8dB
Here is the 10mm plywood 50x86cm 2.35kg (blue) and the 1mm "acrylic" (if it is) sample 70x100cm 0.95kg (brown)
10mm plywood SPL = 47.3dB, 1mm acrylic = 42.7dB so about 5dB difference wich is the difference on the plot between the 2 flat portions. The bandwidth of the plywood is strongly limited because of its important thickness.
For none of those FR, the high frequency extension is really relevant of what the material can give, probably because of the tape I used. I have no explanation for the plywood that has a better high frequency extension.
Christian
Christian,Thank you Eric
Did you make this measurement in the same conditions as the CF/balsa or revplywood? I think about the distance from walls.
In the one exciter condition, is it really only one glued on the panel or the second one not connected but mechanically linked to the panel? what I notice is the low level above 10kHz.
Christian
These measurements were made with the Balsa panel laying horizontally, about 1 meter from the floor, and the mic 1 m above the panel. There is a small bench about 0.3 meters directly below the panel, but with an area smaller than the panel. The exciters where not glued or otherwise attached to the panel, except by a weight of perhaps 100g resting directly on top of the exciter. That may indeed be why the usual hump at 16 kHz is so small on this panel. I honestly don't give that feature too much thought, I must admit, as I don't hear much about about 11 or 12 kHz anyway.
The "horizontal" panel method was my usual method (until very recently) to allow easily using the same exciter repeatedly without having to use new VHB adhesive each time. It also allows moving the exciter to new positions extremely quickly, as you only have to slide it across the panel. There is no need to pry it off and re-attach it. Perhaps the biggest negative of this method, however, is that the exciter may "bounce" a little at some frequencies, causing harmonic distortion. Adding more weight helps, but I was always worried about adding too much and damaging the exciter.
But since I found the double sided tape I shared earlier (3M 9589), I am more usually attaching the exciter with this tape, and orienting the panel in a vertical orientation. The tape allows me to drive the exciter to much higher volumes with no worry that the exciter will bounce. It takes a little more time to move the exciter to new positions, but not a lot more time.
I would have to test this tape on some scrap balsa before using it on my panel, however. Balsa is pretty fragile and I would not want to damage the panel. Probably it will be fine, however.
Eric
Clear EricChristian,
These measurements were made with the Balsa panel laying horizontally, about 1 meter from the floor, and the mic 1 m above the panel. There is a small bench about 0.3 meters directly below the panel, but with an area smaller than the panel. The exciters where not glued or otherwise attached to the panel, except by a weight of perhaps 100g resting directly on top of the exciter. That may indeed be why the usual hump at 16 kHz is so small on this panel. I honestly don't give that feature too much thought, I must admit, as I don't hear much about about 11 or 12 kHz anyway.
The "horizontal" panel method was my usual method (until very recently) to allow easily using the same exciter repeatedly without having to use new VHB adhesive each time. It also allows moving the exciter to new positions extremely quickly, as you only have to slide it across the panel. There is no need to pry it off and re-attach it. Perhaps the biggest negative of this method, however, is that the exciter may "bounce" a little at some frequencies, causing harmonic distortion. Adding more weight helps, but I was always worried about adding too much and damaging the exciter.
But since I found the double sided tape I shared earlier (3M 9589), I am more usually attaching the exciter with this tape, and orienting the panel in a vertical orientation. The tape allows me to drive the exciter to much higher volumes with no worry that the exciter will bounce. It takes a little more time to move the exciter to new positions, but not a lot more time.
I would have to test this tape on some scrap balsa before using it on my panel, however. Balsa is pretty fragile and I would not want to damage the panel. Probably it will be fine, however.
Eric
I member this set up or something close in posts when I have read this thread for a first time.
It explains the lack of high frequencies. When I measured the panels outdoor on different sides, it was visible too. The exciter by itself seems enough to stop those frequencies.
The set-up (exciter not glued, surface at 30cm...) might also explain the unusual dips at 150 and 300Hz.
The reason of my question is I am considering the option of a next panel with balsa. Your feedback on it is very good. From a theoretical point of view, the balsa seems a good candidate among the woods and I have already boards of balsa with no other destination than DML... In fact the question for me is the best use of them. I would like to make a new step with plain material; I feel not ready for sandwich or composite. In an other hand, a balsa board seems so fragile that I have difficulties to see it in a panel.
Christian
Christian.
Although I have always been a very critical of xps ,even with my 5mm pva coated panels ,which I managed to extract a fairly decent sound.
I now think that with the epoxy coating ,the 5mm xps has a very decent sound.
The sound is a lot brighter than the pva coated panel as is the hf extension.
I have notice that with the corrugated cardboard and epoxy panel , there is a bit of a problem with exciter and epoxy, I will check with the xps and epoxy to see if this is also affected ?
But presume it is.
Would fibreglass mesh make it too rigid ?
You mention the hf on ply , usually ply has a very good, even excessive hf response.
Depending on how you look at it , the hf on ply is more efficient than the lower frequencies or the lower frequencies are less efficient than the high frequencies ?
From memory the hf up to 20k travels all the way to the edges on the 3mm ply panels I used.
On less rigid panels the hf stops short , and on very flexible panels may only reach out a few cm from the coil .
I have the small 1mm veneer panel that I coated in epoxy on one side to test yet , I prefer thinner ply panels ,preferably two ply, they have to be the correct size though for ideal conditions.
Steve.
Although I have always been a very critical of xps ,even with my 5mm pva coated panels ,which I managed to extract a fairly decent sound.
I now think that with the epoxy coating ,the 5mm xps has a very decent sound.
The sound is a lot brighter than the pva coated panel as is the hf extension.
I have notice that with the corrugated cardboard and epoxy panel , there is a bit of a problem with exciter and epoxy, I will check with the xps and epoxy to see if this is also affected ?
But presume it is.
Would fibreglass mesh make it too rigid ?
You mention the hf on ply , usually ply has a very good, even excessive hf response.
Depending on how you look at it , the hf on ply is more efficient than the lower frequencies or the lower frequencies are less efficient than the high frequencies ?
From memory the hf up to 20k travels all the way to the edges on the 3mm ply panels I used.
On less rigid panels the hf stops short , and on very flexible panels may only reach out a few cm from the coil .
I have the small 1mm veneer panel that I coated in epoxy on one side to test yet , I prefer thinner ply panels ,preferably two ply, they have to be the correct size though for ideal conditions.
Steve.
A bit surprising results Christian. Makes me think that for making a large power system it could be worthwhile to take a bunch of ca 30x30 plates with a single powerful exciter each rather than trying to put more power on bigger plates. I'm still worried however that the benefit when it comes to how efficiently DML can cover a large area might be reduced with the size of the plate, but of course you have the same surface area by having more plates.
Also it might be the case that the smaller plates saturates at a lower level, so possibly one might as well use the larger plates driven with more power for a bit smoother FR.
I keep going back and forth on the printed 30x30 plates, but I now noticed that indeed it makes a big difference when the glue dried properly. Still sloping off a bit above 3k it sounds like, but not bad at all. If I just trim off some bass I can push it really hard without it breaking up
Getting some carbon fiber filament and a measuring mic and will see what I can get out of printed plates, and will post some pics and graphs.
Also it might be the case that the smaller plates saturates at a lower level, so possibly one might as well use the larger plates driven with more power for a bit smoother FR.
I keep going back and forth on the printed 30x30 plates, but I now noticed that indeed it makes a big difference when the glue dried properly. Still sloping off a bit above 3k it sounds like, but not bad at all. If I just trim off some bass I can push it really hard without it breaking up
Getting some carbon fiber filament and a measuring mic and will see what I can get out of printed plates, and will post some pics and graphs.
I am now listening to the small 7inch 1mm veneer panel with rather too much epoxy on.
The epoxy is only on the front side.
I started off by listening to pink noise on the panel.
I knew straight away that there was a problem, I could hear the panel.
when listening to loud group vocals harmonizing, it starts to sound like someone is blowing a whistle in the background.
The panel is ringing , and I think it is coming from the exciter panel problems I have described in the past.
The panel sounds good even without the weights to smooth the response.
I could even have reduced the peaks and troughs Even more if I had used the tectonic (and mine) technique .
Even with the weights the sound is still there.
I'm sure that using my technique of cutting a hole in the exciter area and replacing it with a fabric dome or phase plug will mostly sort out these problems ?
The pva does not suffer so much from this problem , I noticed this on the 1mm corrugated cardboard.
It is there in the pva, but at a much lower level.
I see I am going to have to start cutting holes in all these test panels to see if this cures the problem ,which could be even more of a plus for using epoxy ?
I believe this 1mm veneer panel would probably have been better if pva had been used instead, but I have nothing similar to setup and compare, so it is just a thought?
Anyway, here are a couple of pictures of the panel.
The first is the panel with some weights to smooth the response.
The second is the response at 90cm with no weights.
The third is at 90cm with weights.
If listening to these panels at 3m into the room I would raise the low frequency unit roll off point to about 400hz to help drive the room better.
Steve.
The epoxy is only on the front side.
I started off by listening to pink noise on the panel.
I knew straight away that there was a problem, I could hear the panel.
when listening to loud group vocals harmonizing, it starts to sound like someone is blowing a whistle in the background.
The panel is ringing , and I think it is coming from the exciter panel problems I have described in the past.
The panel sounds good even without the weights to smooth the response.
I could even have reduced the peaks and troughs Even more if I had used the tectonic (and mine) technique .
Even with the weights the sound is still there.
I'm sure that using my technique of cutting a hole in the exciter area and replacing it with a fabric dome or phase plug will mostly sort out these problems ?
The pva does not suffer so much from this problem , I noticed this on the 1mm corrugated cardboard.
It is there in the pva, but at a much lower level.
I see I am going to have to start cutting holes in all these test panels to see if this cures the problem ,which could be even more of a plus for using epoxy ?
I believe this 1mm veneer panel would probably have been better if pva had been used instead, but I have nothing similar to setup and compare, so it is just a thought?
Anyway, here are a couple of pictures of the panel.
The first is the panel with some weights to smooth the response.
The second is the response at 90cm with no weights.
The third is at 90cm with weights.
If listening to these panels at 3m into the room I would raise the low frequency unit roll off point to about 400hz to help drive the room better.
Steve.
Attachments
My wife has been playing some church organ music on the front room surround sound , which I thought sounded rather good, so I decided to give it a play on these little panels.
I think at one point the organist must have had his hands on all of the keys and foot peddles at the same time, and it went on for some time.
The actual frequencies of the church organ did not go over 10k ,the blip above this I think was my knees cracking as I got up from the chair😁
the microphone was right behind my seat ,which was at 3m.
Recorded using peak hold.
The low frequency drivers were unaltered at 300hz and I was xo the little panels at 60hz.
I still felt they were contributing to the performance even though it was at a lower level combined with the LF drivers.
The recording was of Durham cathedral organ, which I was playing at very realistic sound levels in my room !
I think tectonic probably have got the panel size right for large halls , no point in making the panels any larger than they need to be.
I think I would like to make the corrugated cardboard panels a little bigger for more output down to 100hz or so.
If I can get small panels to perform this well at huge volume levels with a 10watt exciter ,I see no reason to think a reasonable size panel shouldn't fill a hall ?
Steve.
I think at one point the organist must have had his hands on all of the keys and foot peddles at the same time, and it went on for some time.
The actual frequencies of the church organ did not go over 10k ,the blip above this I think was my knees cracking as I got up from the chair😁
the microphone was right behind my seat ,which was at 3m.
Recorded using peak hold.
The low frequency drivers were unaltered at 300hz and I was xo the little panels at 60hz.
I still felt they were contributing to the performance even though it was at a lower level combined with the LF drivers.
The recording was of Durham cathedral organ, which I was playing at very realistic sound levels in my room !
I think tectonic probably have got the panel size right for large halls , no point in making the panels any larger than they need to be.
I think I would like to make the corrugated cardboard panels a little bigger for more output down to 100hz or so.
If I can get small panels to perform this well at huge volume levels with a 10watt exciter ,I see no reason to think a reasonable size panel shouldn't fill a hall ?
Steve.
Attachments
Hello Steve,Christian.
Although I have always been a very critical of xps ,even with my 5mm pva coated panels ,which I managed to extract a fairly decent sound.
I now think that with the epoxy coating ,the 5mm xps has a very decent sound.
The sound is a lot brighter than the pva coated panel as is the hf extension.
I have notice that with the corrugated cardboard and epoxy panel , there is a bit of a problem with exciter and epoxy, I will check with the xps and epoxy to see if this is also affected ?
But presume it is.
Would fibreglass mesh make it too rigid ?
You mention the hf on ply , usually ply has a very good, even excessive hf response.
Depending on how you look at it , the hf on ply is more efficient than the lower frequencies or the lower frequencies are less efficient than the high frequencies ?
From memory the hf up to 20k travels all the way to the edges on the 3mm ply panels I used.
On less rigid panels the hf stops short , and on very flexible panels may only reach out a few cm from the coil .
I have the small 1mm veneer panel that I coated in epoxy on one side to test yet , I prefer thinner ply panels ,preferably two ply, they have to be the correct size though for ideal conditions.
Steve.
Your remark about the traveling distance according the frequency meets questions I have. It is in my "test plan" to restart the close distance measurements in different location I shared here. It would be interesting to try to link this to the panel performance according your listening test. Is there a correlation like Long traveling distance = good listening performance?
It could help in understanding the role of the absorption in the material.
Christian
- Home
- Loudspeakers
- Full Range
- A Study of DMLs as a Full Range Speaker